Page 49 of 128
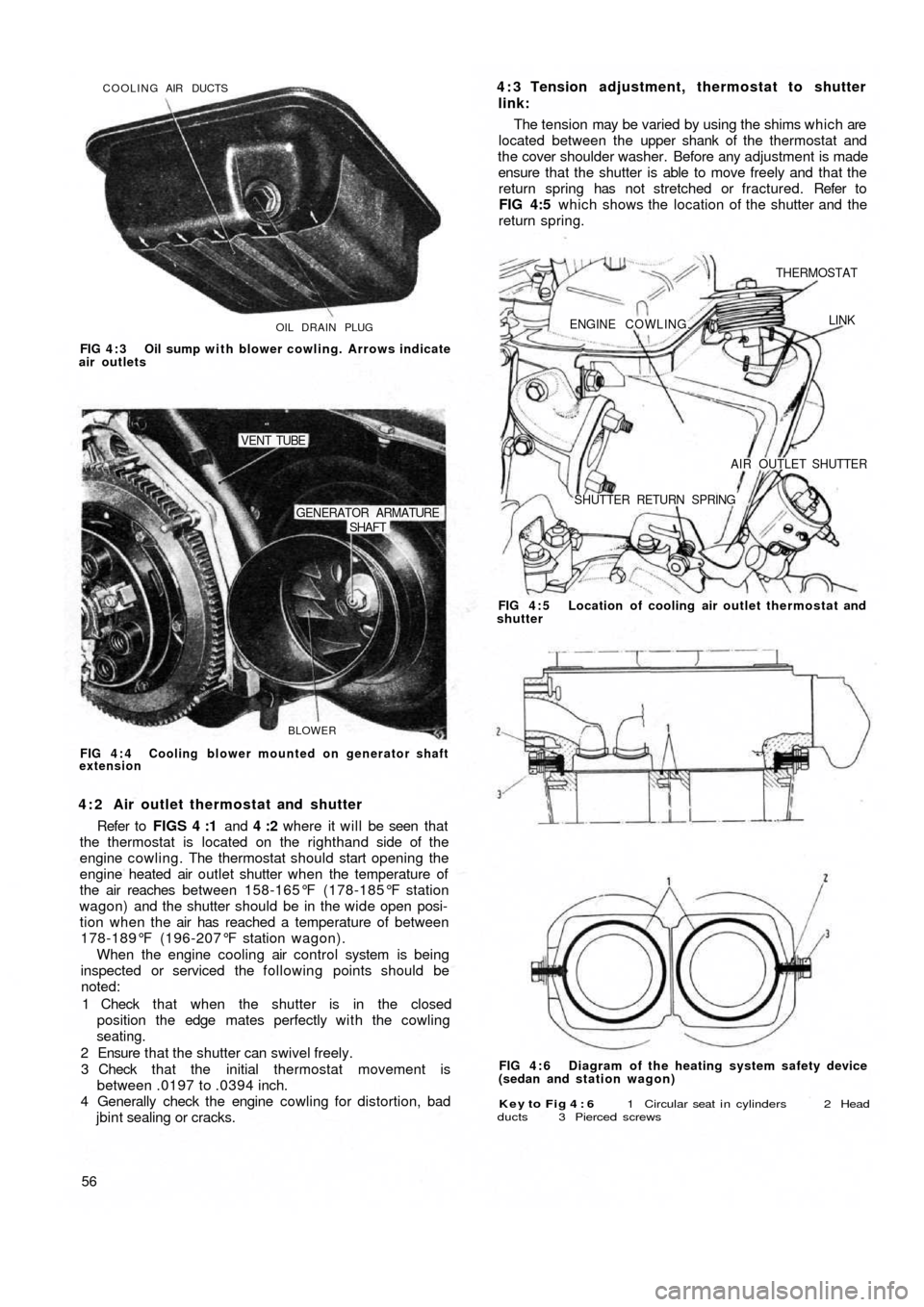
OIL DRAIN PLUG COOLING AIR DUCTS
FIG 4 : 3 Oil sump with blower cowling. Arrows indicate
air outlets
BLOWER
SHAFT GENERATOR ARMATURE
VENT TUBE
FIG 4 : 4 Cooling blower mounted on generator shaft
extension
4 : 2 Air outlet thermostat and shutter
Refer to FIGS 4 :1 and 4 :2 where it will be seen that
the thermostat is located on the righthand side of the
engine cowling. The thermostat should start opening the
engine heated air outlet shutter when the temperature of
the air reaches between 158-165°F (178-185°F station
wagon) and the shutter should be in the wide open posi-
tion when the air has reached a temperature of between
178-189°F (196-207°F station wagon).
When the engine cooling air control system is being
inspected or serviced the following points should be
noted:
1 Check that when the shutter is in the closed
position the edge mates perfectly with the cowling
seating.
2 Ensure that the shutter can swivel freely.
3 Check that the initial thermostat movement is
between .0197 to .0394 inch.
4 Generally check the engine cowling for distortion, bad
jbint sealing or cracks.
56
Key to Fig 4 : 6 1 Circular seat i n cylinders 2 Head
ducts 3 Pierced screws
FIG 4 : 6 Diagram of the heating system safety device
(sedan and station wagon) FIG 4 : 5 Location of cooling air outlet thermostat and
shutter
ENGINE COWLING.
THERMOSTAT
LINK
AIR OUTLET SHUTTER
SHUTTER RETURN SPRING
4 : 3 Tension adjustment, thermostat to shutter
link:
The tension may be varied by using the shims which are
located between the upper shank of the thermostat and
the cover shoulder washer. Before any adjustment is made
ensure that the shutter is able to move freely and that the
return spring has not stretched or fractured. Refer to
FIG 4:5 which shows the location of the shutter and the
return spring.
Page 50 of 128
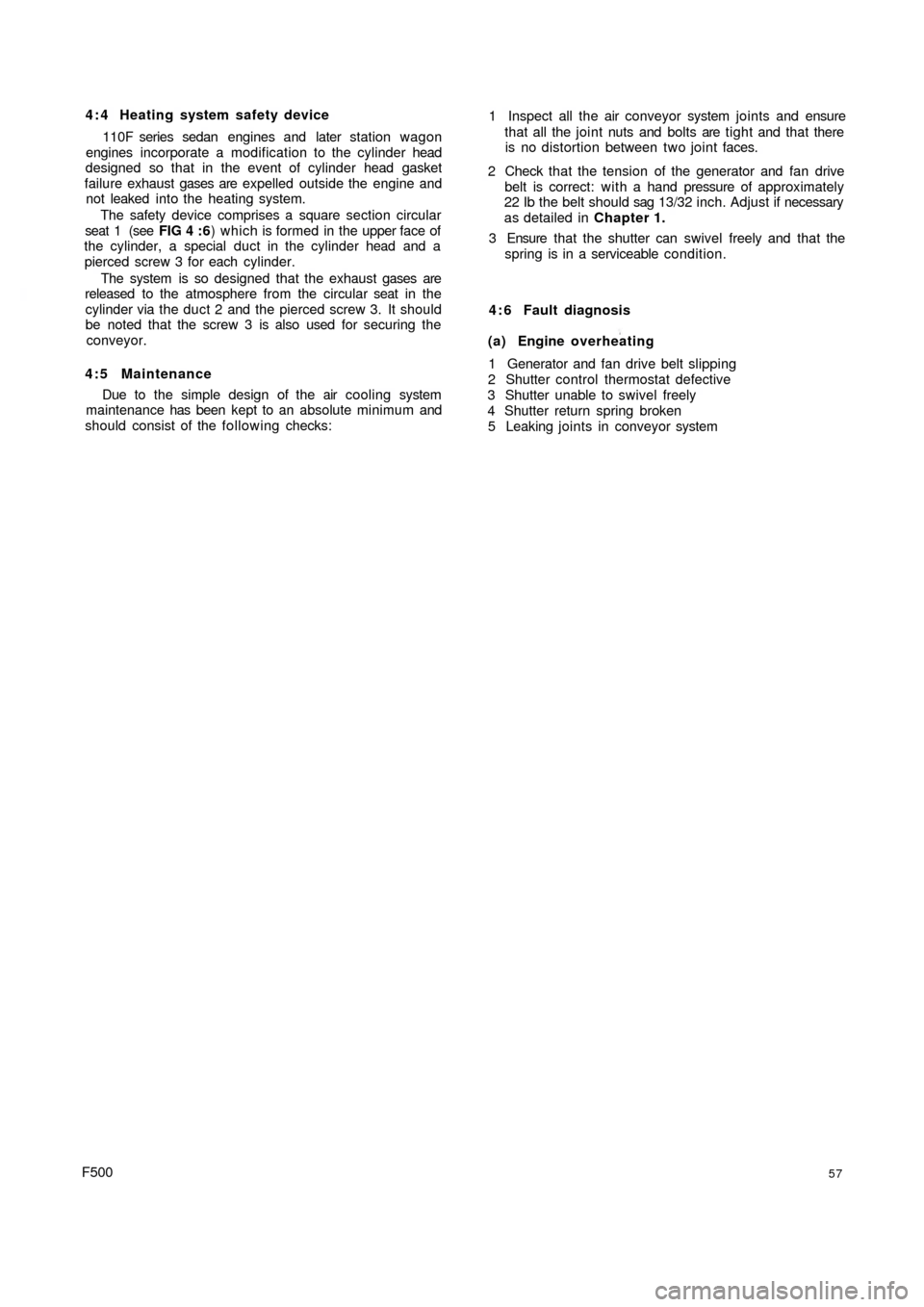
4 : 4 Heating system safety device
110F series sedan engines and later station wagon
engines incorporate a modification to the cylinder head
designed so that in the event of cylinder head gasket
failure exhaust gases are expelled outside the engine and
not leaked into the heating system.
The safety device comprises a square section circular
seat 1 (see FIG 4 :6) which is formed in the upper face of
the cylinder, a special duct in the cylinder head and a
pierced screw 3 for each cylinder.
The system is so designed that the exhaust gases are
released to the atmosphere from the circular seat in the
cylinder via the duct 2 and the pierced screw 3. It should
be noted that the screw 3 is also used for securing the
conveyor.
4 : 5 Maintenance
Due to the simple design of the air cooling system
maintenance has been kept to an absolute minimum and
should consist of the following checks:1 Inspect all the air conveyor system joints and ensure
that all the joint nuts and bolts are tight and that there
is no distortion between two joint faces.
2 Check that the tension of the generator and fan drive
belt is correct: with a hand pressure of approximately
22 Ib the belt should sag 13/32 inch. Adjust if necessary
as detailed in Chapter 1.
3 Ensure that the shutter can swivel freely and that the
spring is in a serviceable condition.
4 : 6 Fault diagnosis
(a) Engine overheating
1 Generator and fan drive belt slipping
2 Shutter control thermostat defective
3 Shutter unable to swivel freely
4 Shutter return spring broken
5 Leaking joints in conveyor system
F50057
Page 51 of 128
Page 52 of 128
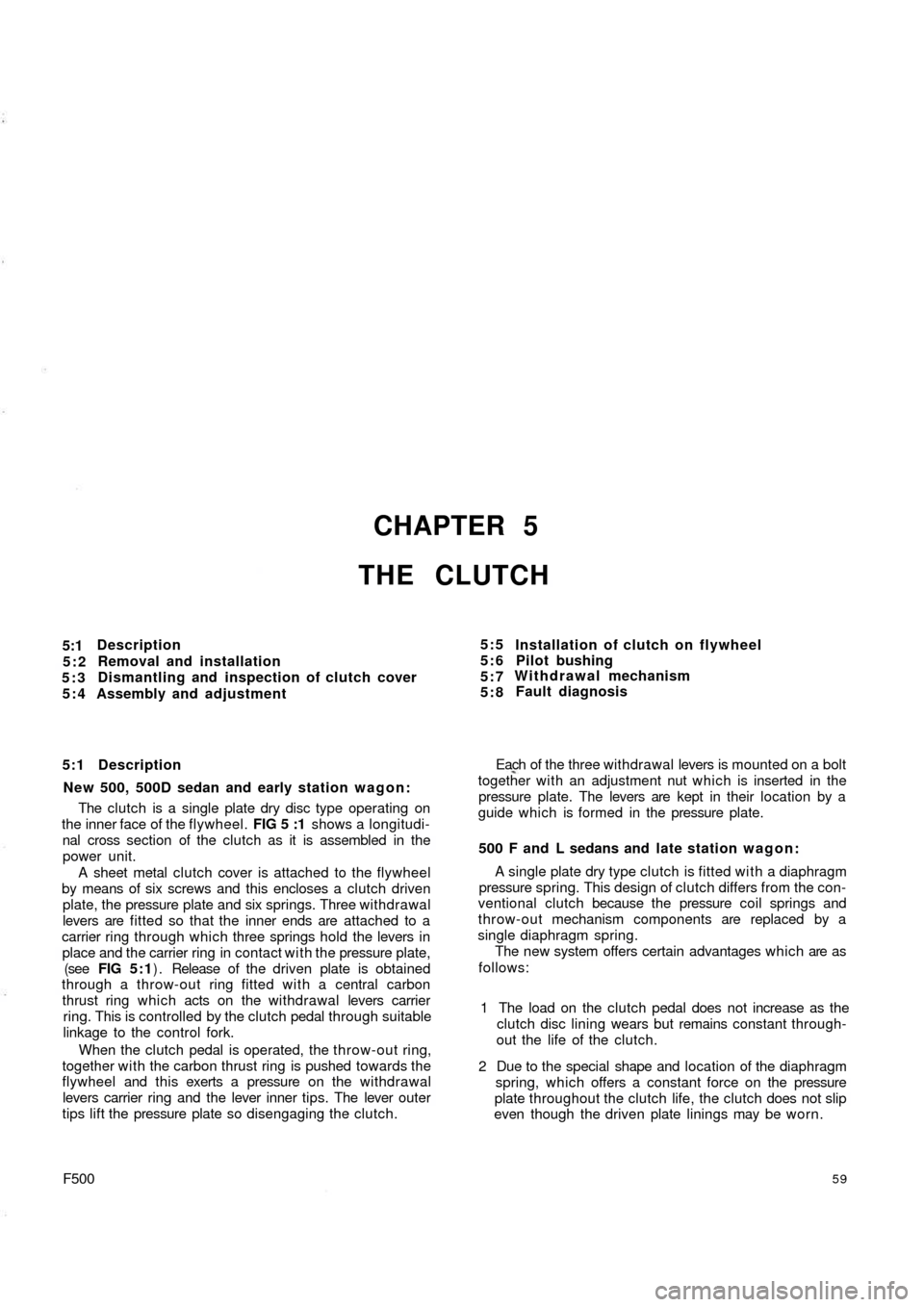
CHAPTER 5
THE CLUTCH
5:1
5:2
5:3
5:4Description
Removal and installation
Dismantling and inspection of clutch cover
Assembly and adjustment
5:1 Description
New 500, 500D sedan and early station wagon:
The clutch is a single plate dry disc type operating on
the inner face of the flywheel. FIG 5 :1 shows a longitudi-
nal cross section of the clutch as it is assembled in the
power unit.
A sheet metal clutch cover is attached to the flywheel
by means of six screws and this encloses a clutch driven
plate, the pressure plate and six springs. Three withdrawal
levers are fitted so that the inner ends are attached to a
carrier ring through which three springs hold the levers in
place and the carrier ring in contact with the pressure plate,
(see FIG 5 : 1) . Release of the driven plate is obtained
through a throw-out ring fitted with a central carbon
thrust ring which acts on the withdrawal levers carrier
ring. This is controlled by the clutch pedal through suitable
linkage to the control fork.
When the clutch pedal is operated, the throw-out ring,
together with the carbon thrust ring is pushed towards the
flywheel and this exerts a pressure on the w i t h d rawal
levers carrier ring and the lever inner tips. The lever outer
tips lift the pressure plate so disengaging the clutch.
F50059
Each of the three withdrawal levers is mounted on a bolt
together with an adjustment nut which is inserted in the
pressure plate. The levers are kept in their location by a
guide which is formed in the pressure plate.
500 F and L sedans and late station wagon:
A single plate dry type clutch is fitted with a diaphragm
pressure spring. This design of clutch differs from the con-
ventional clutch because the pressure coil springs and
throw-out mechanism components are replaced by a
single diaphragm spring.
The new system offers certain advantages which are as
follows:
1 The load on the clutch pedal does not increase as the
clutch disc lining wears but remains constant through-
out the life of the clutch.
2 Due to the special shape and location of the diaphragm
spring, which offers a constant force on the pressure
plate throughout the clutch life, the clutch does not slip
even though the driven plate linings may be worn. 5:5
5:6
5:7
5:8Installation of clutch on flywheel
Pilot bushing
Withdrawal mechanism
Fault diagnosis
Page 53 of 128
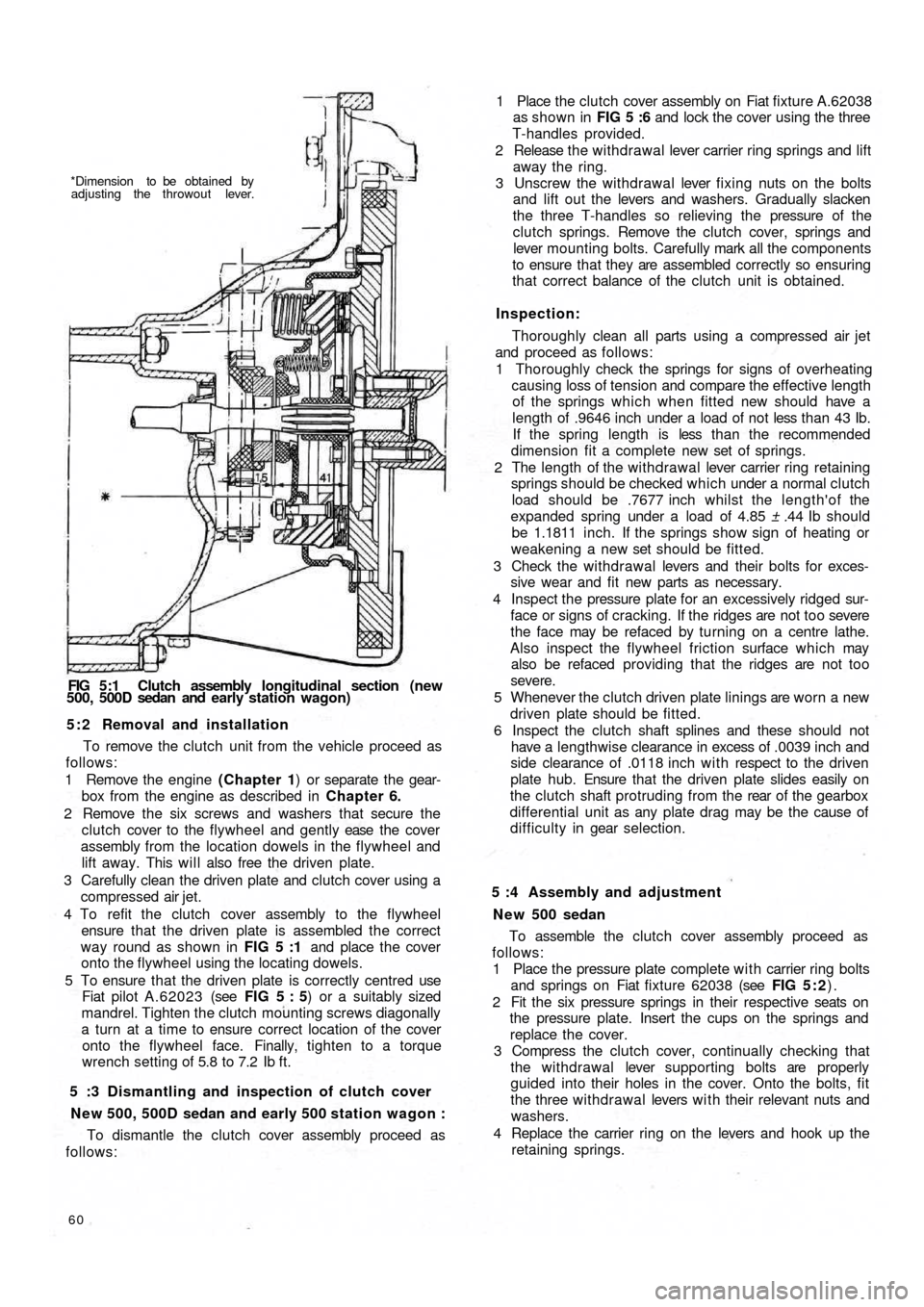
*Dimension to be obtained by
adjusting the throwout lever.
FIG 5:1 Clutch assembly longitudinal section (new
500, 500D sedan and early station wagon)
5 : 2 Removal and installation
To remove the clutch unit from the vehicle proceed as
follows:
1 Remove the engine (Chapter 1) or separate the gear-
box from the engine as described in Chapter 6.
2 Remove the six screws and washers that secure the
clutch cover to the flywheel and gently ease the cover
assembly from the location dowels in the flywheel and
lift away. This will also free the driven plate.
3 Carefully clean the driven plate and clutch cover using a
compressed air jet.
4 To refit the clutch cover assembly to the flywheel
ensure that the driven plate is assembled the correct
way round as shown in FIG 5 :1 and place the cover
onto the flywheel using the locating dowels.
5 To ensure that the driven plate is correctly centred use
Fiat pilot A.62023 (see FIG 5 : 5) or a suitably sized
mandrel. Tighten the clutch mounting screws diagonally
a turn at a time to ensure correct location of the cover
onto the flywheel face. Finally, tighten to a torque
wrench setting of 5.8 to 7.2 Ib ft.
5 :3 Dismantling and inspection of clutch cover
New 500, 500D sedan and early 500 station wagon :
To dismantle the clutch cover assembly proceed as
follows:
60
To assemble the clutch cover assembly proceed as
follows:
1 Place the pressure plate complete with carrier ring bolts
and springs on Fiat fixture 62038 (see FIG 5 : 2).
2 Fit the six pressure springs in their respective seats on
the pressure plate. Insert the cups on the springs and
replace the cover.
3 Compress the clutch cover, continually checking that
the withdrawal lever supporting bolts are properly
guided into their holes in the cover. Onto the bolts, fit
the three withdrawal levers w i t h their relevant nuts and
washers.
4 Replace the carrier ring on the levers and hook up the
retaining springs. 5 :4 Assembly and adjustment
N e w 500 sedan1 Place the clutch cover assembly on Fiat fixture A.62038
as shown in FIG 5 :6 and lock the cover using the three
T-handles provided.
2 Release the w i thdrawal lever carrier ring springs and lift
away the ring.
3 Unscrew the withdrawal lever fixing nuts on the bolts
and lift out the levers and washers. Gradually slacken
the three T-handles so relieving the pressure of the
clutch springs. Remove the clutch cover, springs and
lever mounting bolts. Carefully mark all the components
to ensure that they are assembled correctly so ensuring
that correct balance of the clutch unit is obtained.
Inspection:
Thoroughly clean all parts using a compressed air jet
and proceed as follows:
1 Thoroughly check the springs for signs of overheating
causing loss of tension and compare the effective length
of the springs which when fitted new should have a
length of .9646 inch under a load of not less than 43 Ib.
If the spring length is less t h a n t h e recommended
dimension fit a complete new set of springs.
2 The length of the withdrawal lever carrier ring retaining
springs should be checked which under a normal clutch
load should be .7677 inch whilst the length'of the
expanded spring under a load of 4.85 ± .44 Ib should
be 1.1811 inch. If the springs show sign of heating or
weakening a new set should be fitted.
3 Check the withdrawa l levers and their bolts for exces-
sive wear and fit new parts as necessary.
4 Inspect the pressure plate for an excessively ridged sur-
face or signs of cracking. If the ridges are not too severe
the face may be refaced by turning on a centre lathe.
Also inspect the flywheel friction surface which may
also be refaced providing that the ridges are not too
severe.
5 Whenever the clutch driven plate linings are worn a new
driven plate should be fitted.
6 Inspect the clutch shaft splines and these should not
have a lengthwise clearance in excess of .0039 inch and
side clearance of .0118 inch w i t h respect to the driven
plate hub. Ensure that the driven plate slides easily on
the clutch shaft protruding from the rear of the gearbox
differential unit as any plate drag may be the cause of
d i f f i c u l t y in gear selection.
Page 54 of 128
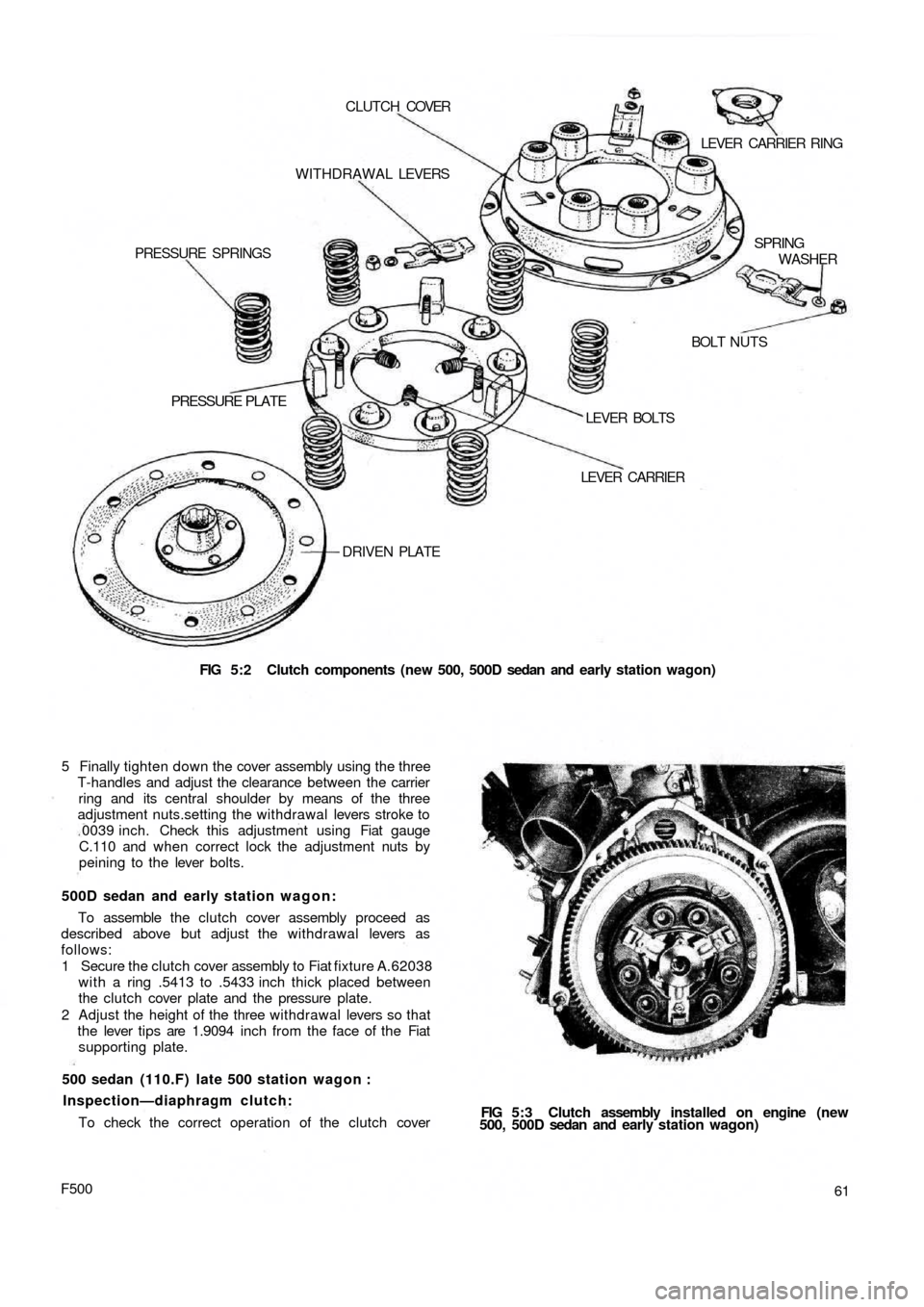
FIG 5:2 Clutch components (new 500, 500D sedan and early station wagon) DRIVEN PLATE
PRESSURE PLATE
LEVER CARRIER LEVER BOLTSBOLT NUTS PRESSURE SPRINGSWITHDRAWAL LEVERS CLUTCH COVER
LEVER CARRIER RING
SPRING
WASHER
FIG 5:3 Clutch assembly installed on engine (new
500, 500D sedan and early station wagon)
61
F500
To check the correct operation of the clutch cover 500 sedan (110.F) late 500 station wagon :
Inspection—diaphragm clutch: 5 Finally tighten down the cover assembly using the three
T-handles and adjust the clearance between the carrier
ring and its central shoulder by means of the three
adjustment nuts.setting the withdrawal levers stroke to
0039 inch. Check this adjustment using Fiat gauge
C.110 and when correct lock the adjustment nuts by
peining to the lever bolts.
500D sedan and early station wagon:
To assemble the clutch cover assembly proceed as
described above but adjust the withdrawal levers as
follows:
1 Secure the clutch cover assembly to Fiat fixture A.62038
with a ring .5413 to .5433 inch thick placed between
the clutch cover plate and the pressure plate.
2 Adjust the height of the three withdrawal levers so that
the lever tips are 1.9094 inch from the face of the Fiat
supporting plate.
Page 55 of 128
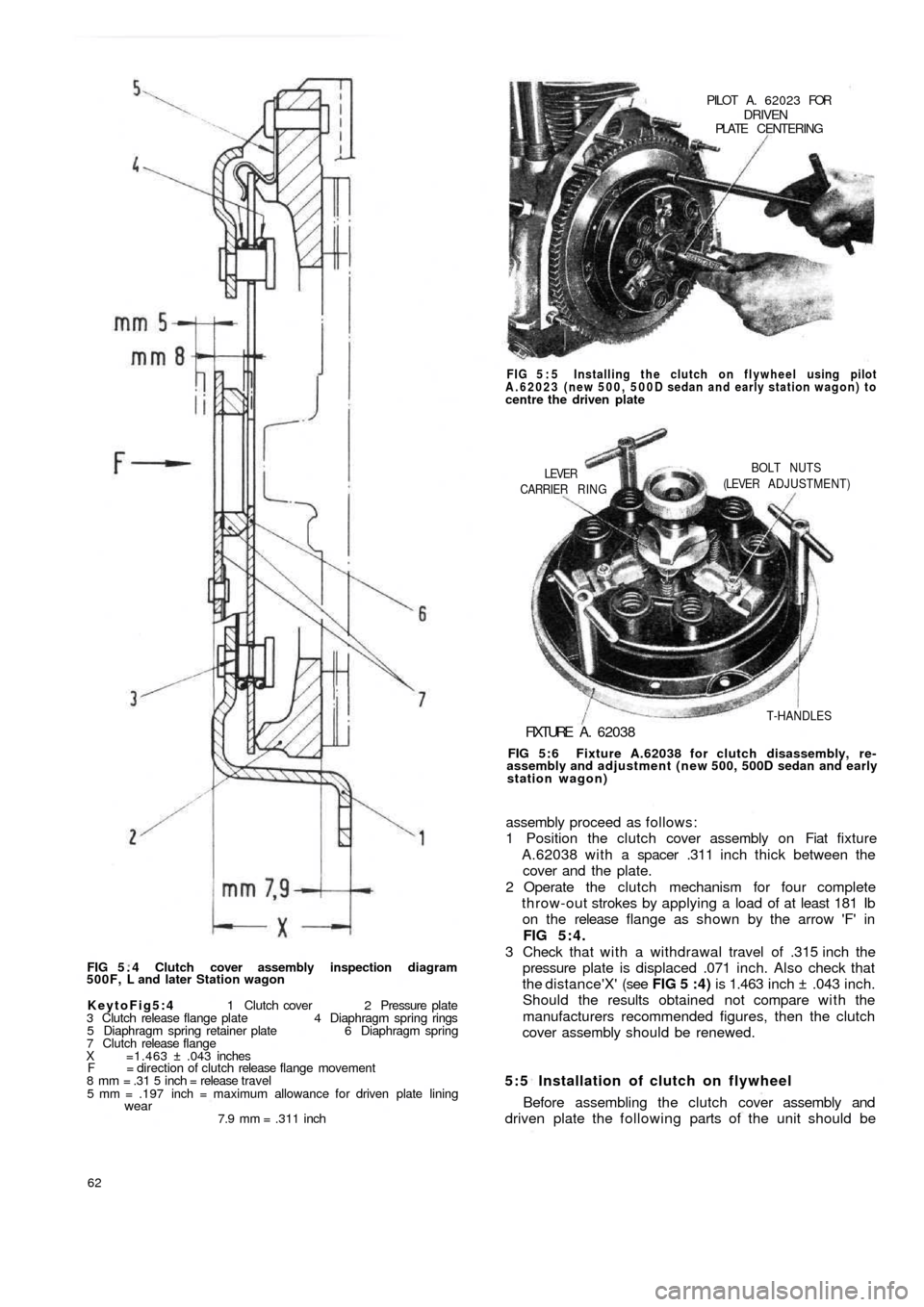
FIG 5 . 4 Clutch cover assembly inspection diagram
500F, L and later Station wagon
KeytoFig5:4 1 Clutch cover 2 Pressure plate
3 Clutch release flange plate 4 Diaphragm spring rings
5 Diaphragm spring retainer plate 6 Diaphragm spring
7 Clutch release flange
X =1.463 ± .043 inches
F = direction of clutch release flange movement
8 mm = .31 5 inch = release travel
5 mm = .197 inch = maximum allowance for driven plate lining
wear7.9 mm = .311 inch
62
5:5 Installation of clutch on flywheel
Before assembling the clutch cover assembly and
driven plate the following parts of the unit should be assembly proceed as follows:
1 Position the clutch cover assembly on Fiat fixture
A.62038 with a spacer .311 inch thick between the
cover and the plate.
2 Operate the clutch mechanism for four complete
throw-out strokes by applying a load of at least 181 Ib
on the release flange as shown by the arrow 'F' in
FIG 5:4.
3 Check that w i t h a withdrawal travel of .315 inch the
pressure plate is displaced .071 inch. Also check that
the distance'X' (see FIG 5 :4) is 1.463 inch ± .043 inch.
Should the results obtained not compare w i t h the
manufacturers recommended figures, then the clutch
cover assembly should be renewed.
FIG 5:6 Fixture A.62038 for clutch disassembly, re-
assembly and adjustment (new 500, 500D sedan and early
station wagon)
FIXTURE A . 62038
T-HANDLES CARRIER RING
LEVERBOLT NUTS
(LEVER ADJUSTMENT) FIG 5 : 5 Installing the clutch on flywheel using pilot
A.62023 (new 500, 500D sedan and early station wagon) to
centre the driven platePILOT A. 62023 FOR
DRIVENPLATE CENTERING
Page 56 of 128
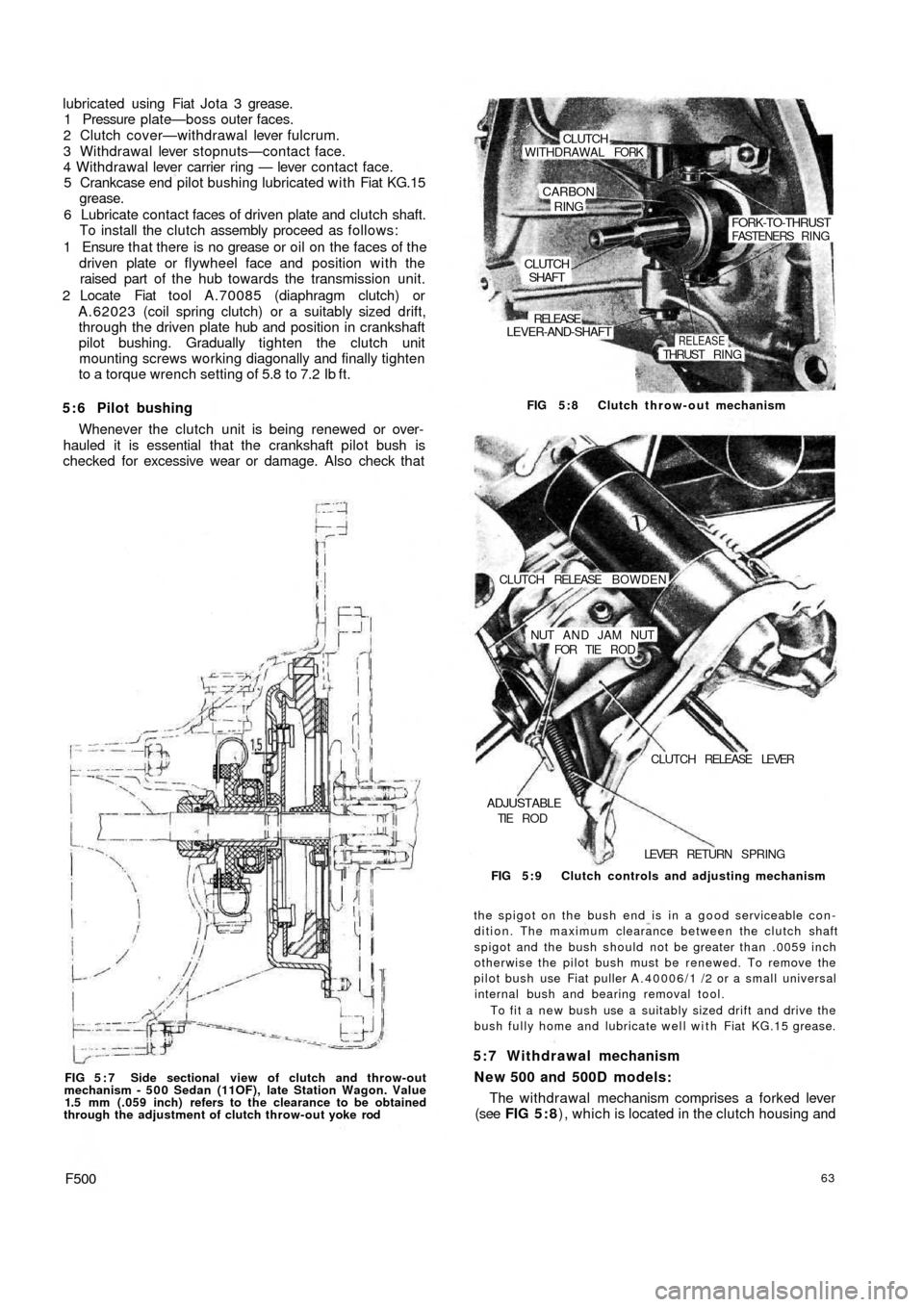
lubricated using Fiat Jota 3 grease.
1 Pressure plate—boss outer faces.
2 Clutch cover—withdrawal lever fulcrum.
3 Withdrawal lever stopnuts—contact face.
4 Withdrawal lever carrier ring — lever contact face.
5 Crankcase end pilot bushing lubricated with Fiat KG.15
grease.
6 Lubricate contact faces of driven plate and clutch shaft.
To install the clutch assembly proceed as follows:
1 Ensure t h a t there is no grease or oil on the faces of the
driven plate or flywheel face and position with the
raised part of the hub towards the transmission unit.
2 Locate Fiat tool A.70085 (diaphragm clutch) or
A . 6 2 0 2 3 (coil spring clutch) or a suitably sized drift,
through the driven plate hub and position in crankshaft
pilot bushing. Gradually tighten the clutch unit
mounting screws working diagonally and finally tighten
to a torque wrench setting of 5.8 to 7.2 Ib ft.
5 : 6 Pilot bushing
Whenever the clutch unit is being renewed or over-
hauled it is essential that the crankshaft pilot bush is
checked for excessive wear or damage. Also check that
FIG 5 : 7 Side sectional view of clutch and throw-out
mechanism - 5 0 0 Sedan (11OF), late Station Wagon. Value
1.5 mm (.059 inch) refers to the clearance to be obtained
through the adjustment of clutch throw-out yoke rod
F50063
The withdrawal mechanism comprises a forked lever
(see FIG 5 : 8), which is located in the clutch housing and 5:7 Withdrawal mechanism
New 500 and 500D models:
the spigot on the bush end is in a good serviceable con-
dition. The maximum clearance between the clutch shaft
spigot and the bush should not be greater than .0059 inch
otherwise the pilot bush must be renewed. To remove the
pilot bush use Fiat puller A.40006/1 /2 or a small universal
internal bush and bearing removal tool.
To fit a new bush use a suitably sized drift and drive the
bush fully home and lubricate well with Fiat KG.15 grease. FIG 5 : 9 Clutch controls and adjusting mechanism LEVER RETURN SPRING
ADJUSTABLETIE R O DCLUTCH RELEASE LEVER NUT A N D JAM NUT
FOR TIE R O D CLUTCH RELEASE BOWDEN FIG 5:8 Clutch throw-out mechanism
CLUTCHSHAFT
LEVER-AND-SHAFT
RELEASE
RELEASETHRUST RING
FORK-TO-THRUSTFASTENERS RING
CARBON
RING
WITHDRAWAL FORKCLUTCH