Page 217 of 796
03-10
(3) DI Engine Fuel System Check Procedure
If several DTCs are output simultaneously, check the electric wiring for open or short circuit.
Check the low pressure fuel system and fuel filter and confirm that there are no abnormalities.
Carry out the high pressure fuel system check.
Page 219 of 796
03-12
(5) High Pressure System Pressure Test
Fuel rail pressure test ▶
Disconnect the pressure sensor connector
(A) and IMV connector (B) from the fuel rail. 1.
Connect the pressure tester to the fuel rail
pressure sensor connector. 2.
Crank the engine 2 times for 5 seconds.
3.
Read the highest pressure value displayed
on the tester display.
If the highest pressure value is 1,050 bar
or less, refer to the section "Fuel System
Check Process". -
-
Page 220 of 796
03-132210-01
How To Use Pressure Tester ▶
Press the "TEST" button on the tester to
check if the message "TEST?" is displayed.
If the button is pressed again at 4 seconds
after starting engine cranking, the highest
pressure is displayed on the tester. 1.
2.
The fuel rail pressure value can be checked using a diagnostic device.
Page 221 of 796
03-14
(6) Low Pressure System Pressure Test
Inspection procedure ▶
All wirings/connectors and fuel lines should
be connected and the engine should work
properly.
Prepare a special tool for low pressure test
and clean it thoroughly to prevent foreign
materials from entering. 1.
2.
Disconnect the key connector for fuel filter connection, and connect both connectors to the fuel filter
and hose. 3.
Start the engine and check visually for clogged low pressure fuel system, excessive air or air entry.
If the fuel flow is not sufficient or air is in the fuel, repair the leak area. 4.
5.
Page 222 of 796
03-152210-01
Static test for backleak of injector ▶
Disconnect the injector return hose and cover
the openings with caps shaped screw
(included in the special tool). 1.
Connect the hose of the container for
measuring backleak to the return nipple of the
injector.
(prevent air entry to the low pressure line) 2.
Disconnect the IMV connector of the high
pressure pump and then fuel pressure
sensor connector. 3.
The connector of the injector can be easily
contaminated. Always keep it clean.
Crank the engine 2 times for 5 seconds.
Check the time for flow if injector backleak
and confirm that it is within the specified
range. 4.
5.
If the value is out of the specified range,
replace the injector.
SpecificationBelow 20 sec.
Page 223 of 796
03-16
Dynamic test for backleak of injector ▶
Warm up the engine so that the engine
coolant tem
perature be over 80℃ and star
the engine again.
Disconnect the injector return hose and cover
the openings with caps shaped screw
(included in the special tool). 1.
2.
Connect the hose of the container for
measuring backleak to the return nipple of
the injector.
Start the engine again and let the engine idle
for 30 seconds.
Perform backleak test of fuel system with a
diagnostic device after 30 seconds. 3.
4.
5.
This test consists of 4 cycles, and the engine rpm
reaches 3,500 rpm for 18 seconds in each cycle.
Check the amount of backleak collected into
the container and confirm that it is within the
specified range. 6.
Specification38 ml or less
Page 225 of 796
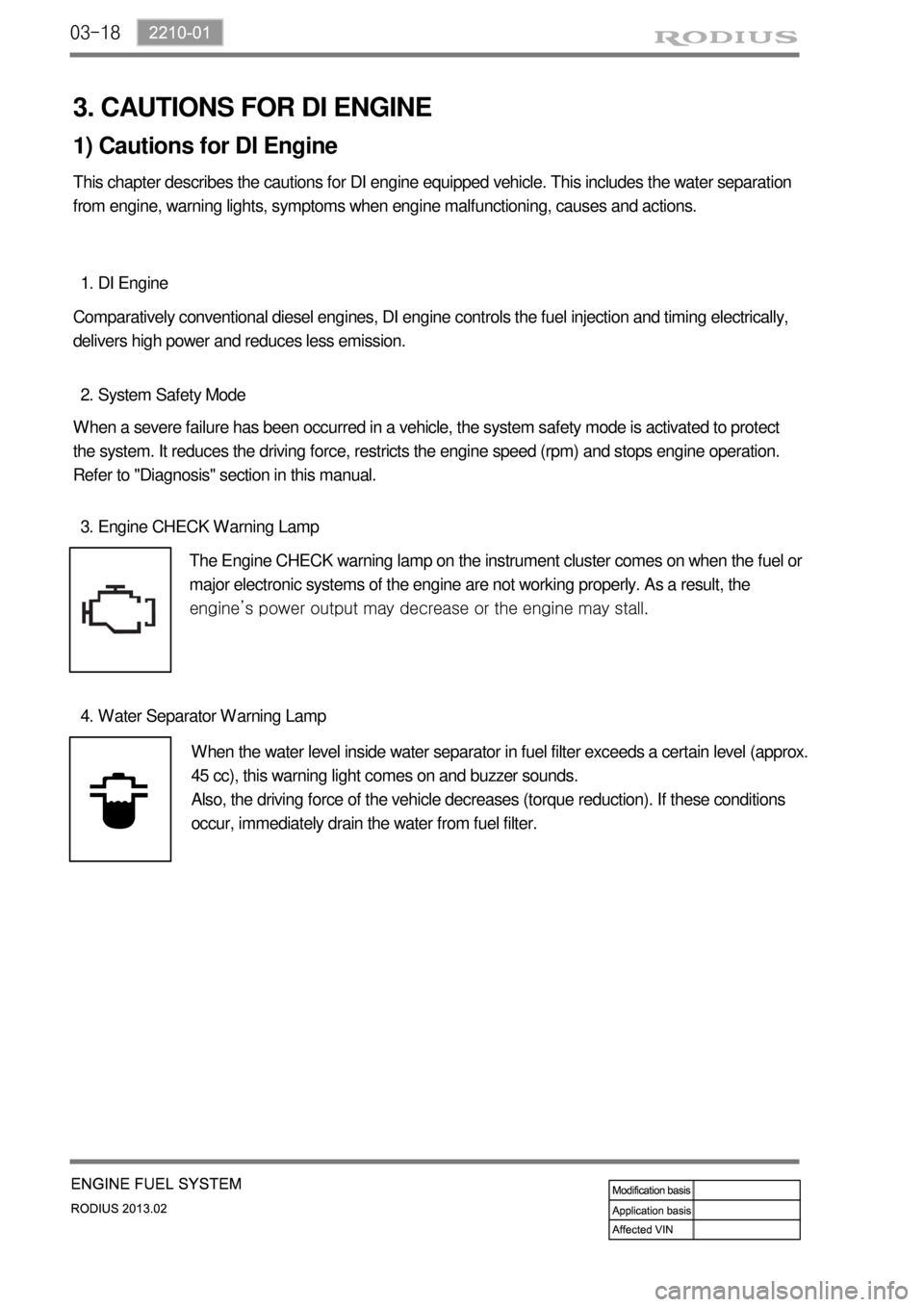
03-18
3. CAUTIONS FOR DI ENGINE
1) Cautions for DI Engine
This chapter describes the cautions for DI engine equipped vehicle. This includes the water separation
from engine, warning lights, symptoms when engine malfunctioning, causes and actions.
DI Engine 1.
Comparatively conventional diesel engines, DI engine controls the fuel injection and timing electrically,
delivers high power and reduces less emission.
System Safety Mode 2.
When a severe failure has been occurred in a vehicle, the system safety mode is activated to protect
the system. It reduces the driving force, restricts the engine speed (rpm) and stops engine operation.
Refer to "Diagnosis" section in this manual.
Engine CHECK Warning Lamp 3.
The Engine CHECK warning lamp on the instrument cluster comes on when the fuel or
major electronic systems of the engine are not working properly. As a result, the
engine’s power output may decrease or the engine may stall.
Water Separator Warning Lamp
4.
When the water level inside water separator in fuel filter exceeds a certain level (approx.
45 cc), this warning light comes on and buzzer sounds.
Also, the driving force of the vehicle decreases (torque reduction). If these conditions
occur, immediately drain the water from fuel filter.
Page 227 of 796
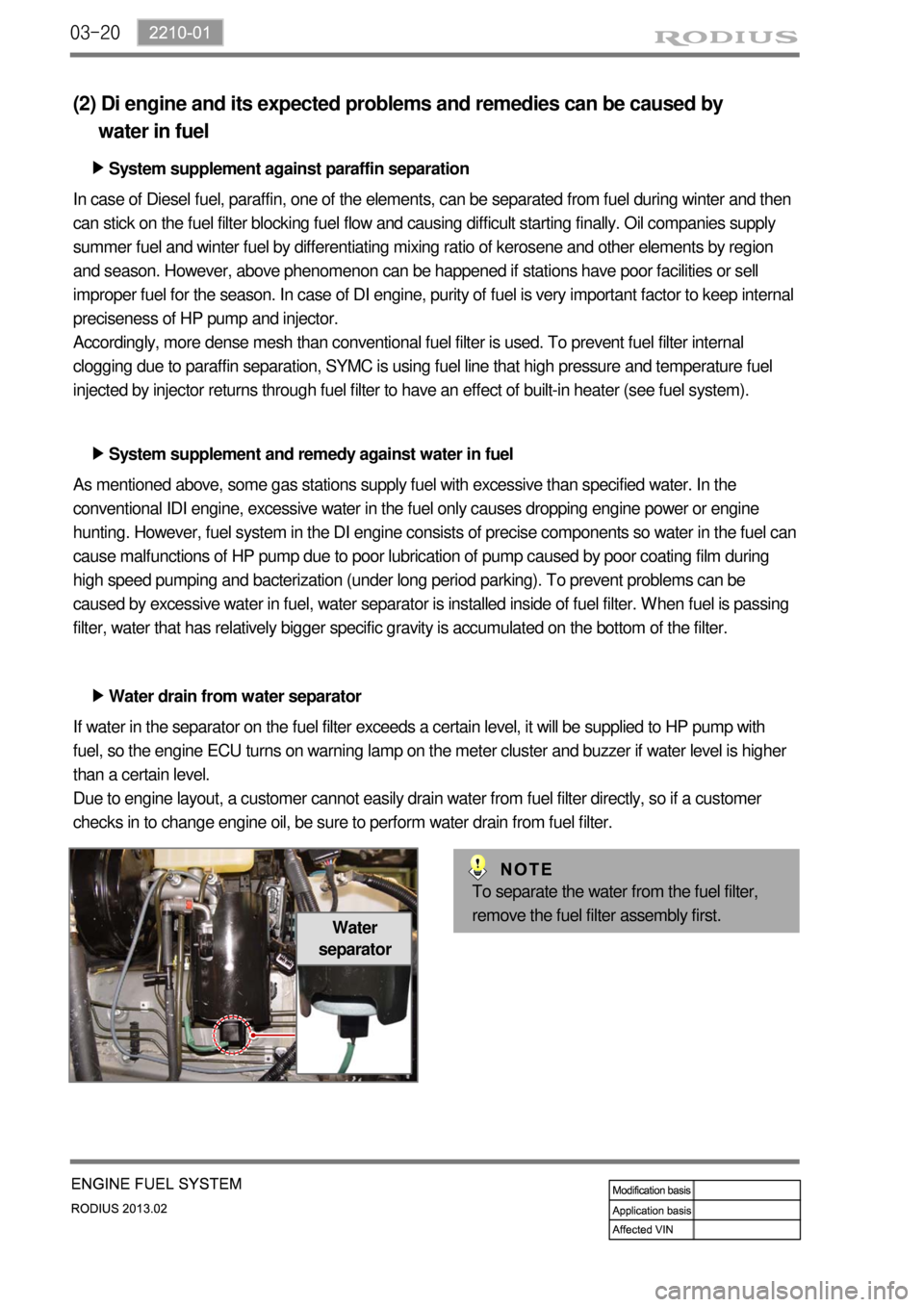
03-20
Water
separator
(2) Di engine and its expected problems and remedies can be caused by
water in fuel
System supplement against paraffin separation ▶
In case of Diesel fuel, paraffin, one of the elements, can be separated from fuel during winter and then
can stick on the fuel filter blocking fuel flow and causing difficult starting finally. Oil companies supply
summer fuel and winter fuel by differentiating mixing ratio of kerosene and other elements by region
and season. However, above phenomenon can be happened if stations have poor facilities or sell
improper fuel for the season. In case of DI engine, purity of fuel is very important factor to keep internal
preciseness of HP pump and injector.
Accordingly, more dense mesh than conventional fuel filter is used. To prevent fuel filter internal
clogging due to paraffin separation, SYMC is using fuel line that high pressure and temperature fuel
injected by injector returns through fuel filter to have an effect of built-in heater (see fuel system).
System supplement and remedy against water in fuel ▶
As mentioned above, some gas stations supply fuel with excessive than specified water. In the
conventional IDI engine, excessive water in the fuel only causes dropping engine power or engine
hunting. However, fuel system in the DI engine consists of precise components so water in the fuel can
cause malfunctions of HP pump due to poor lubrication of pump caused by poor coating film during
high speed pumping and bacterization (under long period parking). To prevent problems can be
caused by excessive water in fuel, water separator is installed inside of fuel filter. When fuel is passing
filter, water that has relatively bigger specific gravity is accumulated on the bottom of the filter.
Water drain from water separator ▶
If water in the separator on the fuel filter exceeds a certain level, it will be supplied to HP pump with
fuel, so the engine ECU turns on warning lamp on the meter cluster and buzzer if water level is higher
than a certain level.
Due to engine layout, a customer cannot easily drain water from fuel filter directly, so if a customer
checks in to change engine oil, be sure to perform water drain from fuel filter.
To separate the water from the fuel filter,
remove the fuel filter assembly first.