Page 1065 of 1336
2. TIGHTENING TORQUE
DescriptionTightening torque
Amount
Clutch housing boltUpper (17 mm) 85.0 to 100 Nm 2
Front (14 mm)
1
Rear (14 mm) 51.3 to 56.7 Nm 2
Lower (14 mm) 56.0 to 62.0 Nm 4
Pressure plate assembly bolt (Hexagon 6 mm) 21.0 to 27.0 Nm 6
Concentric slave cylinder bolt (Hexagon 5 mm) 10 to 16 Nm 3
Concentric slave cylinder oil pipe nut 24.5 to 28.4 Nm Remove the nut if it is
necessary. (Once
removed, apply the
Loctite on the thread
before installation.)
Master cylinder nut (12 mm) 7.8 to 17.6 Nm
Master cylinder oil pipe nut (10 mm) 14.7 to 17.6 Nm
Master cylinder push rod lock nut 8.8 to 13.7 Nm
Clutch oil chamber screw and bolt (10 mm) 3.9 to 7.8 Nm
Oil pipe nut (10 mm) 14.7 to 17.6 Nm
Clutch pedal mounting nut (12 mm) 7.8 to 17.6 Nm
Stopper bolt 16 to 22 Nm
Page 1070 of 1336
0000-00
3. DUAL MASS FLYWHEEL (DMF)
The dual mass flywheel (DMF) is of having a mass divided into two halves.
While one mass is connected to the engine crankshaft, which is affected by the mass moment of inertia
of the engine, the other mass is affected by one of the transmission.
The divided dual masses are connected to the coil spring and damping system internally.
The DMF has the following benefits:
Reducing fuel consumption by lowering engine speed
Reducing rattling noise and vehicle vibration in all driving ranges
Reducing synchronization wear
Facilitating gear change
Protecting power train parts by preventing excessive load from being delivered -
-
-
-
-
Primary flywheel
Secondary flywheel
Arc damper spring
Torque limiter
Ring gear 1.
2.
3.
4.
5.
Page 1071 of 1336
3310-02
1. SPECIFICATION
Description Specification
Structure 2-piece type with CV joint, spider, and rubber
coupling
Weight below 12.0 kg
Joint type CV joint, spider, rubber coupling
Spider Numbers one (installed on center bearing side)
External diameter
Overall size
Dimension
(Length x Dia.)No.1 shaft (TM to spider)
No. 2 shaft (spider to axle)
Runout of tube (after installation) 0.3 mm
Unbalance 80g.mm @ 3,000rpm
(second measurement: 120 g.mm)
U-joint Starting torque 0.3 to 0.7 Nm
Minimum starting angle
Amount of grease in CV joint 210+-10g
2. TIGHTENING TORQUE
Fastener Tightening torque
Bolt/nut for rubber coupling (rear axle side) 39.2 to 49.0 Nm
Bolt/nut for CV joint (transaxle side) 29.4 to 39.2 Nm
Mounting bolt for center bearing 58.8 to 68.6 Nm
Page 1072 of 1336
1. OVERVIEW
The propeller shaft is a thin steel pipe which transfers the power from the transmission to the E-coupling,
and has high resistance to torsion and bending.
The propeller shaft has the universal joint (cross axle) mounted on the center of the shaft and splines for
the slip joint on the E-coupling side to accommodate the height and length changes which occur as the
shaft rotates at high speed.
And the rubber bushing for center bearing in the center of the propeller shaft keeps the balance of the
shaft and absorbs its vibration.
Function of propeller shaft
Transmits driving torque.
Accommodates the angle change (universal joint / CV joint).
Accommodates the axial length change (splines for the slip joint). -
-
-
CV joint
Universal yoke and
center bearingUniversal yoke and
rubber coupling
Page 1076 of 1336
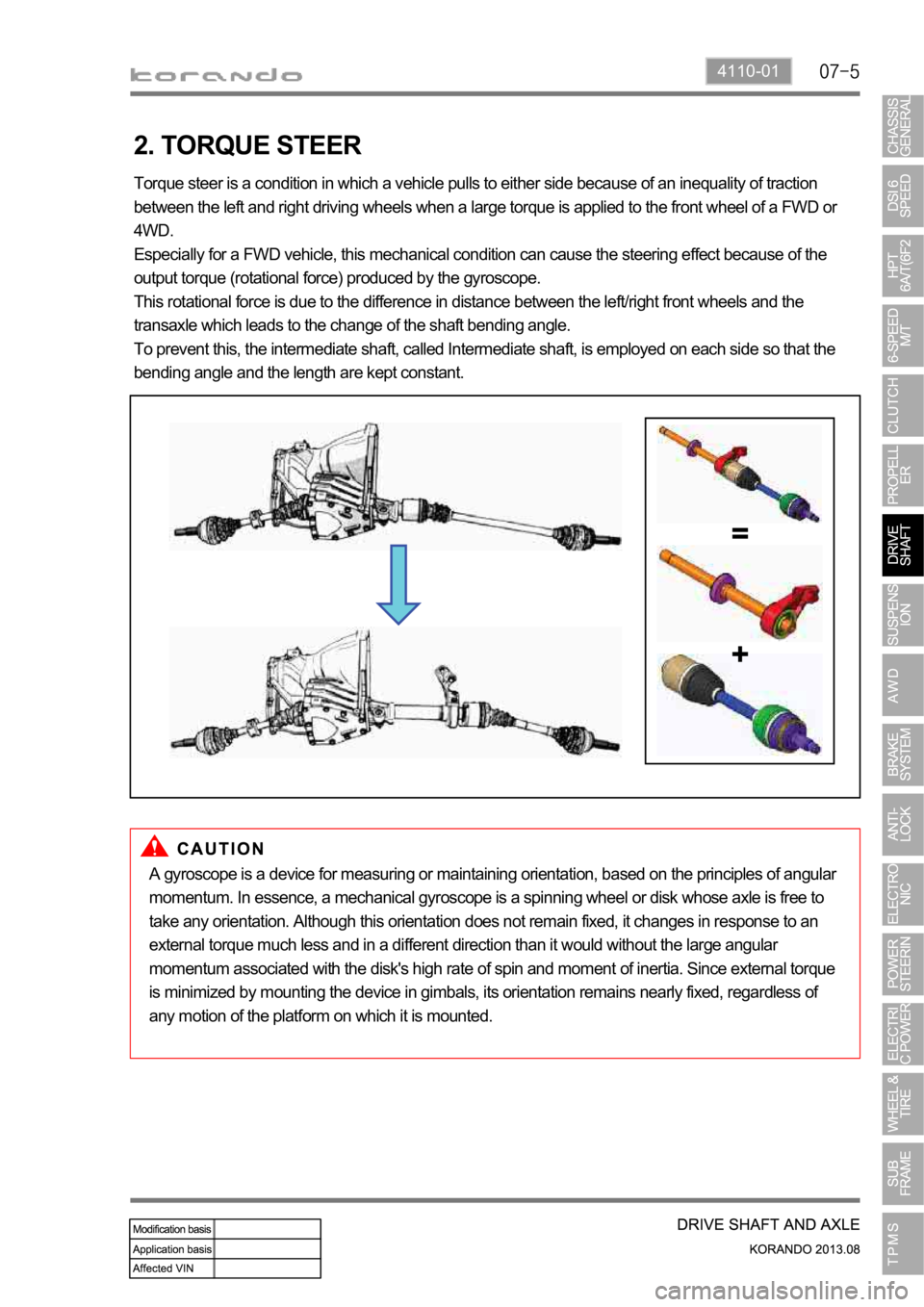
4110-01
2. TORQUE STEER
Torque steer is a condition in which a vehicle pulls to either side because of an inequality of traction
between the left and right driving wheels when a large torque is applied to the front wheel of a FWD or
4WD.
Especially for a FWD vehicle, this mechanical condition can cause the steering effect because of the
output torque (rotational force) produced by the gyroscope.
This rotational force is due to the difference in distance between the left/right front wheels and the
transaxle which leads to the change of the shaft bending angle.
To prevent this, the intermediate shaft, called Intermediate shaft, is employed on each side so that the
bending angle and the length are kept constant.
A gyroscope is a device for measuring or maintaining orientation, based on the principles of angular
momentum. In essence, a mechanical gyroscope is a spinning wheel or disk whose axle is free to
take any orientation. Although this orientation does not remain fixed, it changes in response to an
external torque much less and in a different direction than it would without the large angular
momentum associated with the disk's high rate of spin and moment of inertia. Since external torque
is minimized by mounting the device in gimbals, its orientation remains nearly fixed, regardless of
any motion of the platform on which it is mounted.
Page 1080 of 1336
0000-00
2. TIGHTENING TORQUE
Front suspension assembly
Page 1085 of 1336
0000-00
1. SPECIFICATION
Unit Description Specification
PTU
(Power Transfer Unit)Gear ratio 2.929
Numbers of helical gear 22/39
Numbers of hypoid gear 23/38
Oil IDEMITSU LW 80W/90
Oil capacity
Operating temperature
E-coupling Maximum torque 1,000 Nm
Operating temperature
Numbers of main clutch Outer: 11, Inner: 11
Numbers of pilot clutch Outer: 4, Inner: 3
Coil windings 240 turns
Weight 8 kg
Oil ECF107 (ATF based EMCD special oil)
Oil capacity 0.145 L (145 ml)
Page 1087 of 1336
0000-00
2. SYSTEM LAYOUT
1) Components
(1) PTU (Power Transfer Unit)
and transfer it to E-coupling to distribute the torque to rear wheels.
(2) E-Coupling (Electronic Coupling)
E-Coupling transfer the engine torque from PTU to rear axle and controls to distribute it between front
wheels and rear wheels.
(3) E-Coupling Control Unit (ECU)
E-Coupling controls the current (clutch engagement force) of EMCD in E-Coupling according to CAN
signals (wheel speed, engine torque, pedal position, ABS/ESP signals).
* EMCD: Electro-Magnetic Control Device PTU assemblyE-coupling control unit
(located on the floor under driver seat)E-coupling