Page 298 of 652
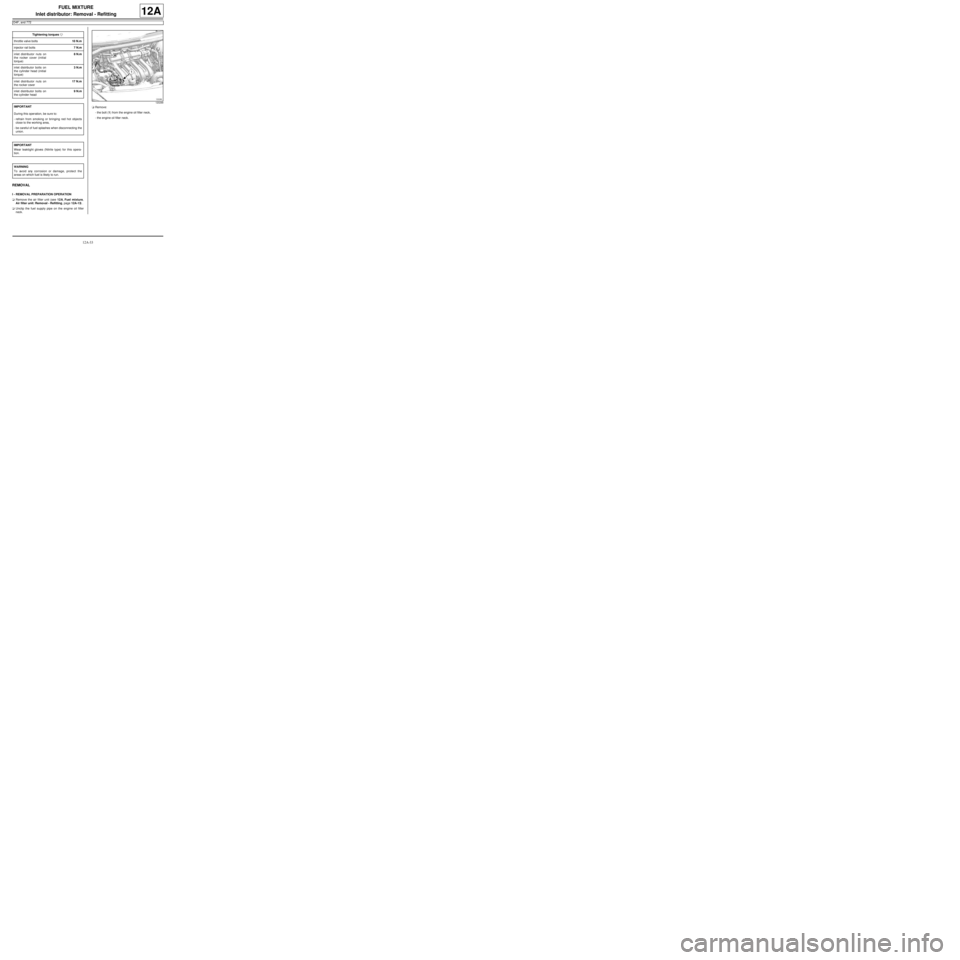
12A-33
FUEL MIXTURE
Inlet distributor: Removal - Refitting
D4F, and 772
12A
REMOVAL
I - REMOVAL PREPARATION OPERATION
aRemove the air filter unit (see 12A, Fuel mixture,
Air filter unit: Removal - Refitting, page 12A-13) .
aUnclip the fuel supply pipe on the engine oil filler
neck.aRemove:
-the bolt (1) from the engine oil filler neck,
-the engine oil filler neck. Tightening torquesm
throttle valve bolts10 N.m
injector rail bolts7 N.m
inlet distributor nuts on
the rocker cover (initial
torque)8 N.m
inlet distributor bolts on
the cylinder head (initial
torque)3 N.m
inlet distributor nuts on
the rocker cover17 N.m
inlet distributor bolts on
the cylinder head9 N.m
IMPORTANT
During this oper ation, be sure to:
-refrain from smoking or bringing red hot objects
close to the working area,
-be careful of fuel splashes when disconnecting the
union.
IMPORTANT
Wear leaktight gloves (Nitrile type) for this opera-
tion.
WARNING
To avoid any corrosion or damage, protect the
areas on which fuel is likely to run.
120299
Page 302 of 652
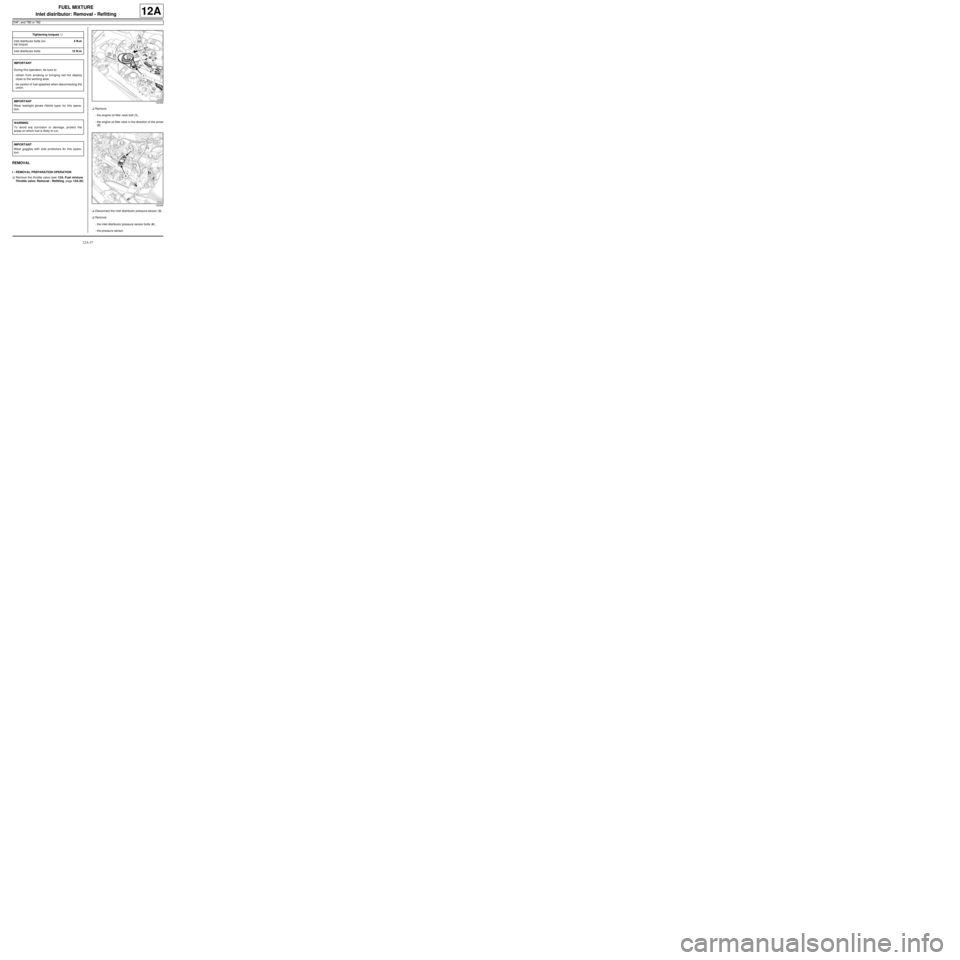
12A-37
FUEL MIXTURE
Inlet distributor: Removal - Refitting
D4F, and 780 or 782
12A
REMOVAL
I - REMOVAL PREPARATION OPERATION
aRemove the throttle valve (see 12A, Fuel mixture,
Throttle valve: Removal - Refitting, page 12A-20)
.aRemove:
-the engine oil filler neck bolt (1) ,
-the engine oil filler neck in the direction of the arrow
(2) .
aDisconnect the inlet distributor pressure sensor (3) .
aRemove:
-the inlet distributor pressure sensor bolts (4) ,
-the pressure sensor. Tightening torquesm
inlet distributor bolts (ini-
tial torque)4 N.m
inlet distributor bolts12 N.m
IMPORTANT
During this oper ation, be sure to:
-refrain from smoking or bringing red hot objects
close to the working area,
-be careful of fuel splashes when disconnecting the
union.
IMPORTANT
Wear leaktight gloves (Nitrile type) for this opera-
tion.
WARNING
To avoid any corrosion or damage, protect the
areas on which fuel is likely to run.
IMPORTANT
Wear goggles with side protectors for this opera-
tion.
122392
122393
Page 305 of 652
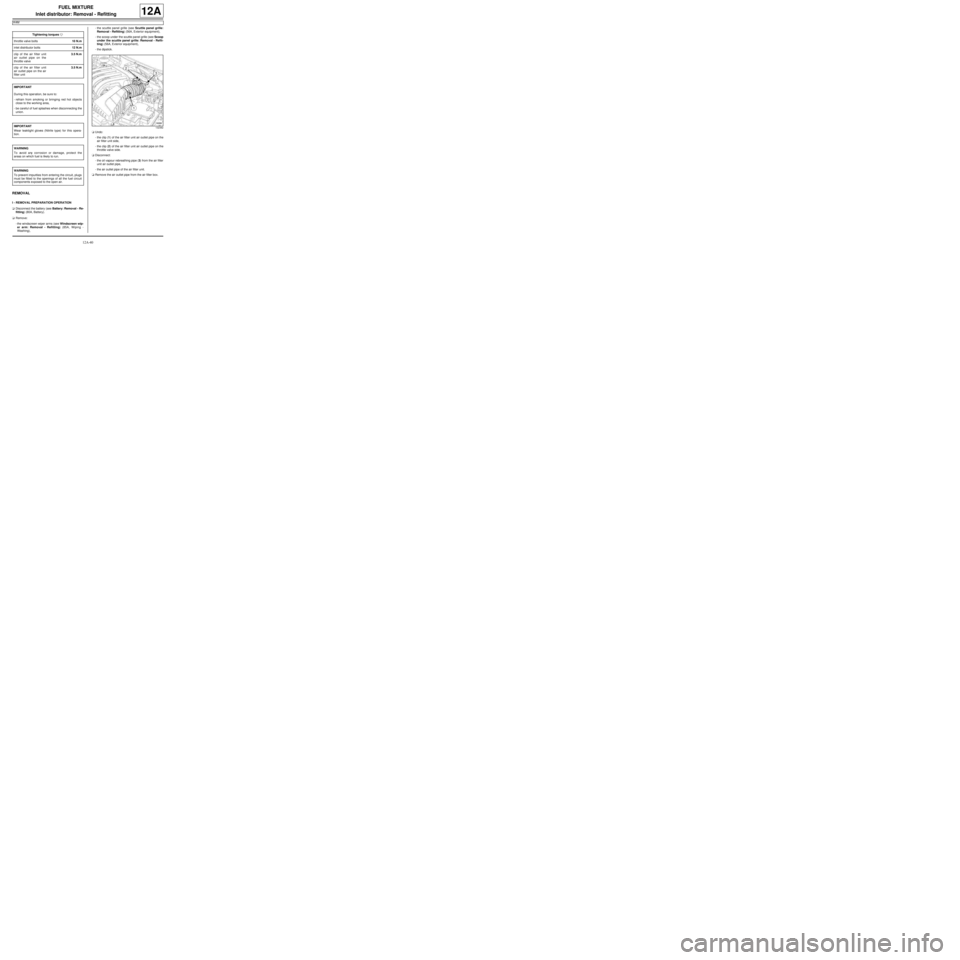
12A-40
FUEL MIXTURE
Inlet distributor: Removal - Refitting
K4M
12A
REMOVAL
I - REMOVAL PREPARATION OPERATION
aDisconnect the battery (see Battery: Removal - Re-
fitting) (80A, Battery).
aRemove:
-the windscreen wiper arms (see Windscreen wip-
er arm: Removal - Refitting) (85A, Wiping -
Washing),-the scuttle panel grille (see Scuttle panel grille:
Removal - Refitting) (56A, Exterior equipment),
-the scoop under the scuttle panel grille (see Scoop
under the scuttle panel grille: Removal - Refit-
ting) (56A, Exterior equipment),
-the dipstick.
aUndo:
-the clip (1) of the air filter unit air outlet pipe on the
air filter unit side,
-the clip (2) of the air filter unit air outlet pipe on the
throttle valve side.
aDisconnect:
-the oil vapour rebreathing pipe (3) from the air filter
unit air outlet pipe,
-the air outlet pipe of the air filter unit.
aRemove the air outlet pipe from the air filter box. Tightening torquesm
throttle valve bolts10 N.m
inlet distributor bolts12 N.m
clip of the air filter unit
air outlet pipe on the
throttle valve3.5 N.m
clip of the air filter unit
air outlet pipe on the air
filter unit3.5 N.m
IMPORTANT
During this oper ation, be sure to:
-refrain from smoking or bringing red hot objects
close to the working area,
-be careful of fuel splashes when disconnecting the
union.
IMPORTANT
Wear leaktight gloves (Nitrile type) for this opera-
tion.
WARNING
To avoid any corrosion or damage, protect the
areas on which fuel is likely to run.
WARNING
To prevent impurities from entering the circuit, plugs
must be fitted to the openings of all the fuel circuit
components exposed to the open air.
132382
Page 352 of 652
13A-9
FUEL SUPPLY
Fuel pressure: Check
D4F or D7F
13A
CHECK
aI - PREPARATION OPERATION FOR CHECK
aEnsure you have a checking tool (Mot. 1311-01) and
a “T” union (Mot. 1311-08).
aRemove the oil filler neck.
II - TEST OPERATION
aDisconnect the petrol inlet pipe from the injector rail. Special tooling required
Mot. 1311-01Pressure gauges and petrol
pressure measur ing unions.
Mot. 1311-08Union for taking fuel pres-
sure measurements .
IMPORTANT
During this operation, be sure to:
-refrain from smoking or bringing red hot objects
close to the working area,
-be careful of fuel splashes when disconnecting
the union.
IMPORTANT
Wear goggles with side protectors for this opera-
tion.
IMPORTANT
Wear leaktight gloves (Nitrile type) for this opera-
tion.
WARNING
To avoid any corrosion or damage, protect the
areas on which fuel is likely to run.
116887
D4F
Page 355 of 652
13A-12
FUEL SUPPLY
Fuel pressure: Check
K4M
13A
CHECK
aI - PREPARATION OPERATION FOR CHECK
aEnsure you have a checking tool (Mot. 1311-01) and
a “T” union (Mot. 1311-08).
II - TEST OPERATION
aDisconnect the fuel supply union from the injector
rail.
aConnect:
-the pipe fitted with a test pressure gauge (Mot.
1311-01) with the "T" union (Mot. 1311-08),
-the "T" union (Mot. 1311-08) on the injector rail, Special tooling required
Mot. 1311-01Pressure gauges and petrol
pressure measur ing unions.
Mot. 1311-08Union for taking fuel pres-
sure measurements .
IMPORTANT
During this operation, be sure to:
-refrain from smoking or bringing red hot objects
close to the working area,
-be careful of fuel splashes when disconnecting
the union.
IMPORTANT
Wear goggles with side protectors for this opera-
tion.
IMPORTANT
Wear leaktight gloves (Nitrile type) for this opera-
tion.
WARNING
To avoid any corrosion or damage, protect the
areas on which fuel is likely to run.
116887
132333
Page 357 of 652
13A-14
FUEL SUPPLY
Fuel flow: Check
D4F or D7F
13A
CHECK
a
I - PREPARATION OPERATION FOR CHECK
aRemove the oil filler neck.
aDisconnect the fuel supply union.aFit a “T” union to the fuel supply union (Mot. 1311-
08).
aFit a pipe which is long enough to drain the pump
into a container to the “T” outlet union. Special tooling required
Mot. 1311-08Union for taking fuel pres-
sure measurements .
Equipment required
graduated measuring cylinder
IMPORTANT
During this operation, be sure to:
-refrain from smoking or bringing red hot objects
close to the working area,
-be careful of fuel splashes when disconnecting
the union.
IMPORTANT
Wear goggles with side protectors for this opera-
tion.
IMPORTANT
Wear leaktight gloves (Nitrile type) for this opera-
tion.
WARNING
To avoid any corrosion or damage, protect the
areas on which fuel is likely to run.
D4F
D4F, and 772
121778
Page 360 of 652
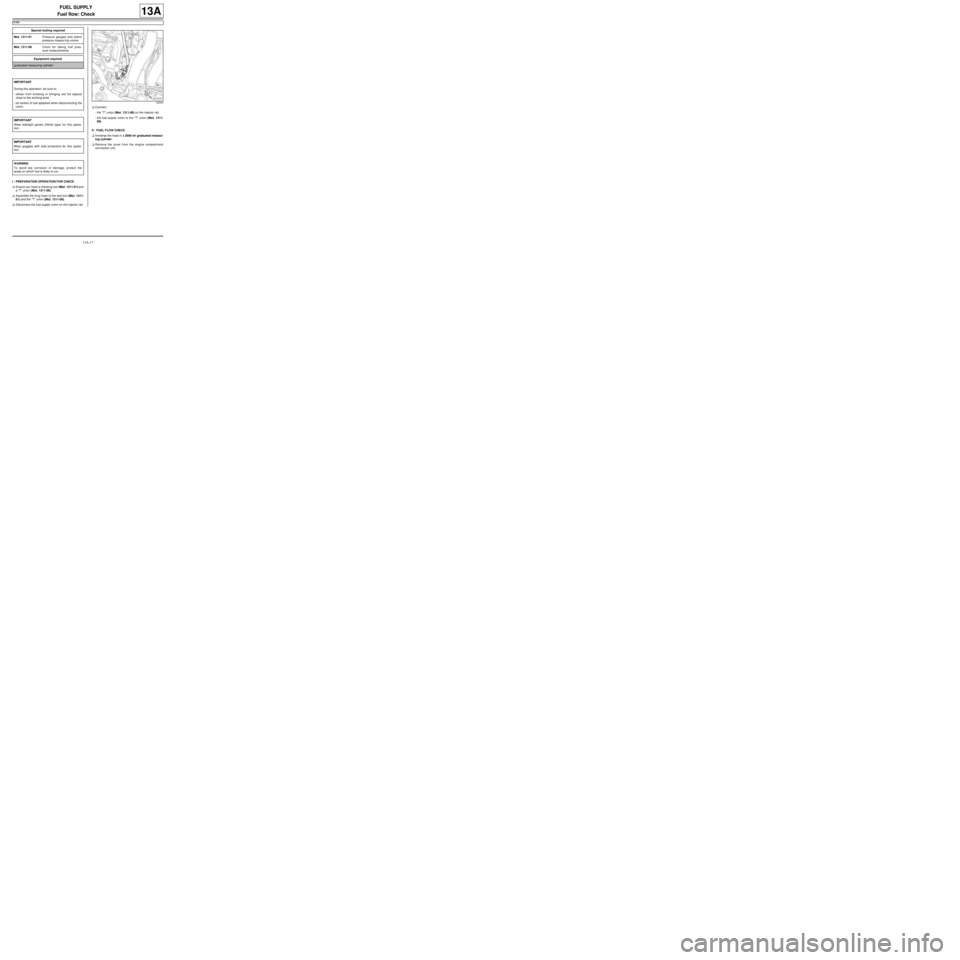
13A-17
FUEL SUPPLY
Fuel flow: Check
K4M
13A
I - PREPARATION OPERATION FOR CHECK
aEnsure you have a checking tool (Mot. 1311-01) and
a “T” union (Mot. 1311-08).
aAssemble the long hose of the test tool (Mot. 1311-
01) and the "T" union (Mot. 1311-08).
aDisconnect the fuel supply union on the injector rail.aConnect:
-the "T" union (Mot. 1311-08) on the injector rail,
-the fuel supply union to the "T" union (Mot. 1311-
08).
II - FUEL FLOW CHECK
aImmerse the hose in a 2000 ml graduated measur-
ing cylinder.
aRemove the cover from the engine compartment
connection unit. Special tooling required
Mot. 1311-01Pressure gauges and petrol
pressure measur ing unions.
Mot. 1311-08Union for taking fuel pres-
sure measurements .
Equipment required
graduated measuring cylinder
IMPORTANT
During this oper ation, be sure to:
-refrain from smoking or bringing red hot objects
close to the working area,
-be careful of fuel splashes when disconnecting the
union.
IMPORTANT
Wear leaktight gloves (Nitrile type) for this opera-
tion.
IMPORTANT
Wear goggles with side protectors for this opera-
tion.
WARNING
To avoid any corrosion or damage, protect the
areas on which fuel is likely to run.
132334
Page 363 of 652
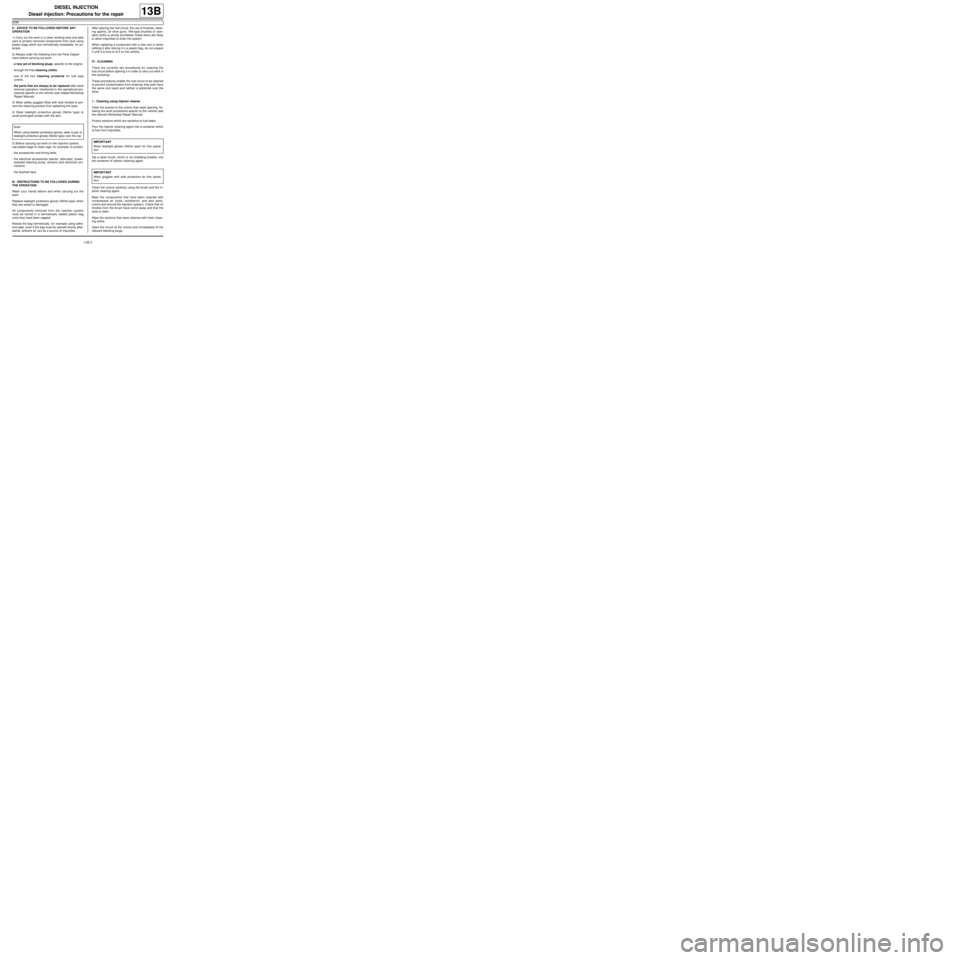
13B-2
DIESEL INJECTION
Diesel injection: Precautions for the repair
K9K
13B
II - ADVICE TO BE FOLLOWED BEFORE ANY
OPERATION
1) Carry out the work in a clean working area and take
care to protect removed components from dust using
plastic bags which are hermetically-resealable, for ex-
ample.
2) Always order the following from the Parts Depart-
ment before carrying out work:
-a new set of blanking plugs, specific to the engine,
-enough lint-free cleaning cloths.
-one of the two cleaning products for fuel pipe
unions,
-the parts that are always to be replaced after each
removal operation, mentioned in the operational pro-
cedures specific to the vehicle (see related Workshop
Repair Manual).
3) Wear safety goggles fitted with side shields to pre-
vent the cleaning product from splashing the eyes.
4) Wear leaktight protective gloves (Nitrile type) to
avoid prolonged contact with the skin.
5) Before carrying out work on the injection system,
use plastic bags or clean rags, for example, to protect:
-the accessories and timing belts,
-the electrical accessories (starter, alternator, power-
assisted steering pump, sensors and electrical con-
nectors),
-the flywheel face.
III - INSTRUCTIONS TO BE FOLLOWED DURING
THE OPERATION
Wash your hands before and while carrying out the
work.
Replace leaktight protective gloves (Nitrile type) when
they are soiled or damaged.
All components removed from the injection system
must be stored in a hermetically sealed plastic bag
once they have been capped.
Reseal the bag hermetically, for example using adhe-
sive tape, even if the bag must be opened shortly after-
wards: ambient air can be a source of impurities.After opening the fuel circuit, the use of brushes, clean-
ing agents, air blow guns, rifle-type brushes or stan-
dard cloths is strictly prohibited: these items are likely
to allow impurities to enter the system.
When replacing a component with a new one or when
refitting it after storing it in a plastic bag, do not unpack
it until it is time to fit it on the vehicle.
IV - CLEANING
There are currently two procedures for cleaning the
fuel circuit before opening it in order to carry out work in
the workshop.
These procedures enable the fuel circuit to be cleaned
to prevent contamination from entering: they both have
the same end result and neither is preferred over the
other.
1 - Cleaning using injector cleaner
Clear the access to the unions that need opening, fol-
lowing the work procedures specific to the vehicle (see
the relevant Workshop Repair Manual).
Protect sections which are sensitive to fuel leaks.
Pour the injector cleaning agent into a container which
is free from impurities.
Dip a clean brush, which is not shedding bristles, into
the container of injector cleaning agent.
Clean the unions carefully using the brush and the in-
jector cleaning agent.
Blast the components that have been cleaned with
compressed air (tools, workbench, and also parts,
unions and around the injection system). Check that no
bristles from the brush have come away and that the
area is clean.
Wipe the sections that were cleaned with fresh clean-
ing cloths.
Open the circuit at the unions and immediately fit the
relevant blanking plugs. Note:
When using leather protective gloves, wear a pair of
leaktight protective gloves (Nitrile type) over the top.
IMPORTANT
Wear leaktight gloves (Nitrile type) for this opera-
tion.
IMPORTANT
Wear goggles with side protectors for this opera-
tion.