Page 31 of 101
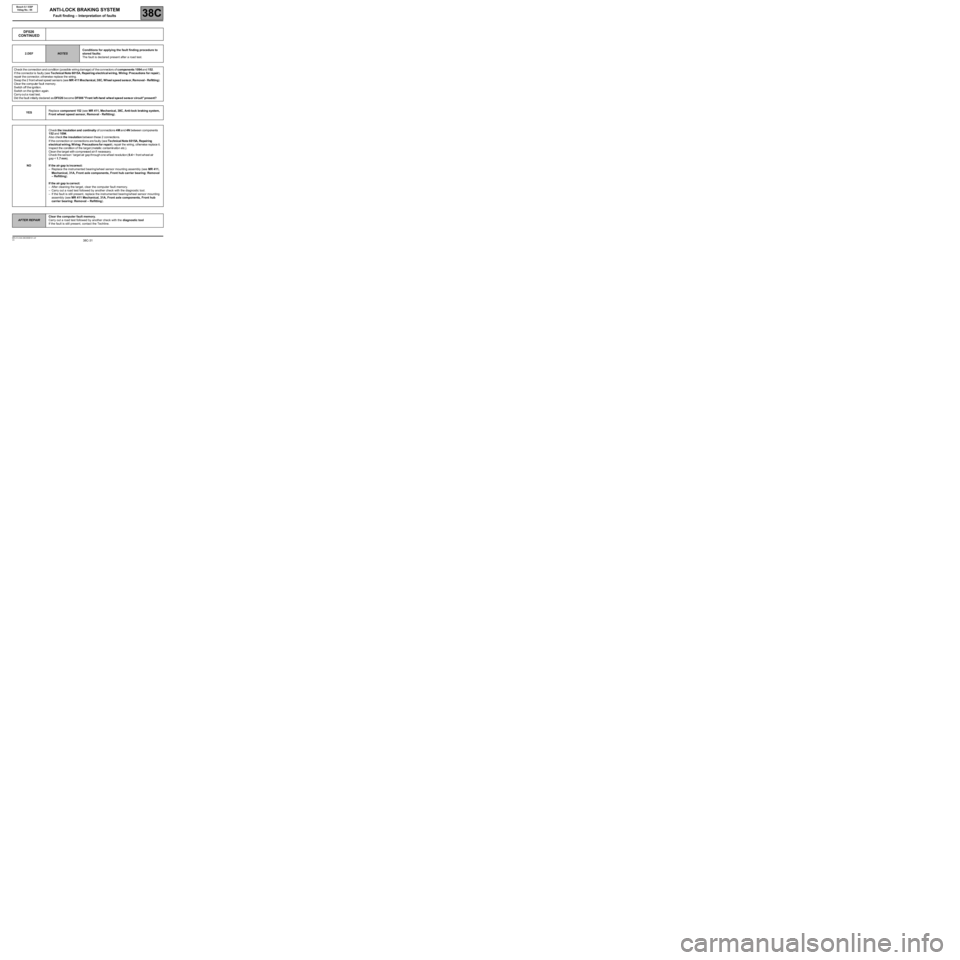
38C-31
AFTER REPAIRClear the computer fault memory.
Carry out a road test followed by another check with the diagnostic tool
If the fault is still present, contact the Techline.
V3 MR-413-X44-38C050$101.mif
ANTI-LOCK BRAKING SYSTEM
Fault finding – Interpretation of faults38C
Bosch 8.1 ESP
Vdiag No.: 05
DF026
CONTINUED
2.DEFNOTESConditions for applying the fault finding procedure to
stored faults:
The fault is declared present after a road test.
Check the connection and condition (possible wiring damage) of the connectors ofcomponents 1 094and152.
Iftheconnector is faulty (seeTe chnical Note 6015A, Repairing e lectrical wiring, Wiring: Precautions for repair),
repair the connector, otherwise replace the wiring.
Swap the 2 front wheel speed sensors (seeMR 411 M echanical, 38C, W heel speed sensor, Removal - Refitting).
Clearthecomputer fault memory.
Switch offtheignition.
Switch on the ignit io nagain.
Carry out a road test.
Did the fault i nitially declared asDF0 26becomeDF006 "Front left-hand wheel speed sensor circuit" present?
YESReplace component 152 (see MR 411, Mechanical, 38C, Anti-lock braking system,
Front wheel speed sensor, Removal - Refitting).
NOCh eckthe insulatio n a nd c on t i n ui t yof connections4Mand4Nbetween components
152and1094.
Alsocheckthe insulationbetween these 2 connections.
Iftheconnection or connections are faulty (seeTe chnical Note 6 015A, Repairing
electrical wiring, W iring: Precautions for repair), repair the wiring, otherwise replace it.
Inspect the condition of the target (metallic contamination etc.).
Cle an the target with compressed air if necessary.
Ch eck the sensor / target air gap through one wheel revolution (0.4
gap <1.7 mm).
If the air gap isincorrect:
–Replace the instrumented bearing/wheel sensor mounting assembly (see MR 411,
Mechanical, 31A, Front axle components, Front hub carrier bearing: Removal
– Refitting).
If the air gap iscorrect:
–After cleaning the target, clear the computer fault memory.
–Carry out a road test followed by another check with the diagnostic tool.
–If the fault is still present, replace the instrumented bearing/wheel sensor mounting
assembly (see MR 411 Mechanical, 31A, Front axle components, Front hub
carrier bearing: Removal – Refitting).
Page 34 of 101
38C-34
AFTER REPAIRClear the computer fault memory.
Carry out a road test followed by another check with the diagnostic tool
If the fault is still present, contact the Techline.
V3 MR-413-X44-38C050$101.mif
ANTI-LOCK BRAKING SYSTEM
Fault finding – Interpretation of faults38C
Bosch 8.1 ESP
Vdiag No.: 05
DF055
PRESENTVEHICLE PARAMETER PROGRAMMINGDEF: configuration absent or incorrect
NOTESNone.
Configure the vehicle parameters using command VP004 Vehicle parameters (see help table in clip).
Clear the fault memory, and initialise the computer (switch the + after ignition feed off and on again).
Check for any possible faults.
ESP_V05_DF055
Page 50 of 101
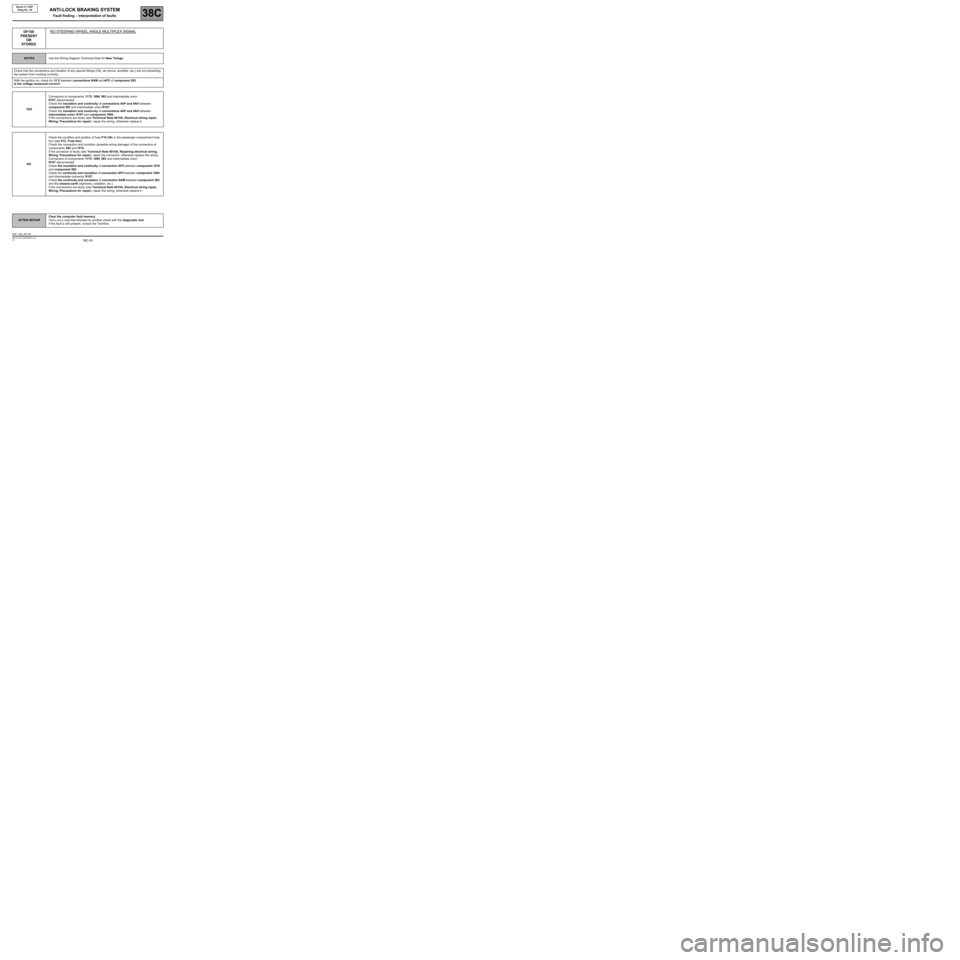
38C-50
AFTER REPAIRClear the computer fault memory.
Carry out a road test followed by another check with the diagnostic tool
If the fault is still present, contact the Techline.
V3 MR-413-X44-38C050$101.mif
ANTI-LOCK BRAKING SYSTEM
Fault finding – Interpretation of faults38C
Bosch 8.1 ESP
Vdiag No.: 05
DF100
PRESENT
OR
STOREDNO STEERING WHEEL ANGLE MULTIPLEX SIGNAL
NOTESUse the Wiring Diagram Technical Note for New Twingo.
Check that the connections and location of any special fittings (CB, car phone, amplifier, etc.) are not preventing
the system from working correctly.
With the ignition on, check for 12 V between connections NAM and AP5 of component 583.
Is the voltage measured correct?
YESConnectors of components 1175, 1094, 583 and intermediate union
R107 disconnected.
Check the insulation and continuity of connections 4AP and 4AH between
component 583 and intermediate union R107.
Check the insulation and continuity of connections 4AP and 4AH between
intermediate union R107 and component 1094.
If the connections are faulty (see Technical Note 6015A, Electrical wiring repair,
Wiring: Precautions for repair), repair the wiring, otherwise replace it.
NOCheck the condition and position of fuse F10 (5A) in the passenger compartment fuse
box (see 81C, Fuse box).
Check the connection and condition (possible wiring damage) of the connectors of
components 583 and 1016.
If the connector is faulty (see Technical Note 6015A, Repairing electrical wiring,
Wiring: Precautions for repair), repair the connector, otherwise replace the wiring.
Connectors of components 1175, 1094, 583 and intermediate union
R107 disconnected.
Check the insulation and continuity of connection AP5 between component 1016
and component 583.
Check the continuity and insulation of connection AP5 between component 1094
and intermediate connector R107.
Check the continuity and insulation of connection NAM between component 583
and the chassis earth (tightness, oxidation, etc.).
If the connections are faulty (see Technical Note 6015A, Electrical wiring repair,
Wiring: Precautions for repair), repair the wiring, otherwise replace it.
ESP_V05_DF100
Page 72 of 101
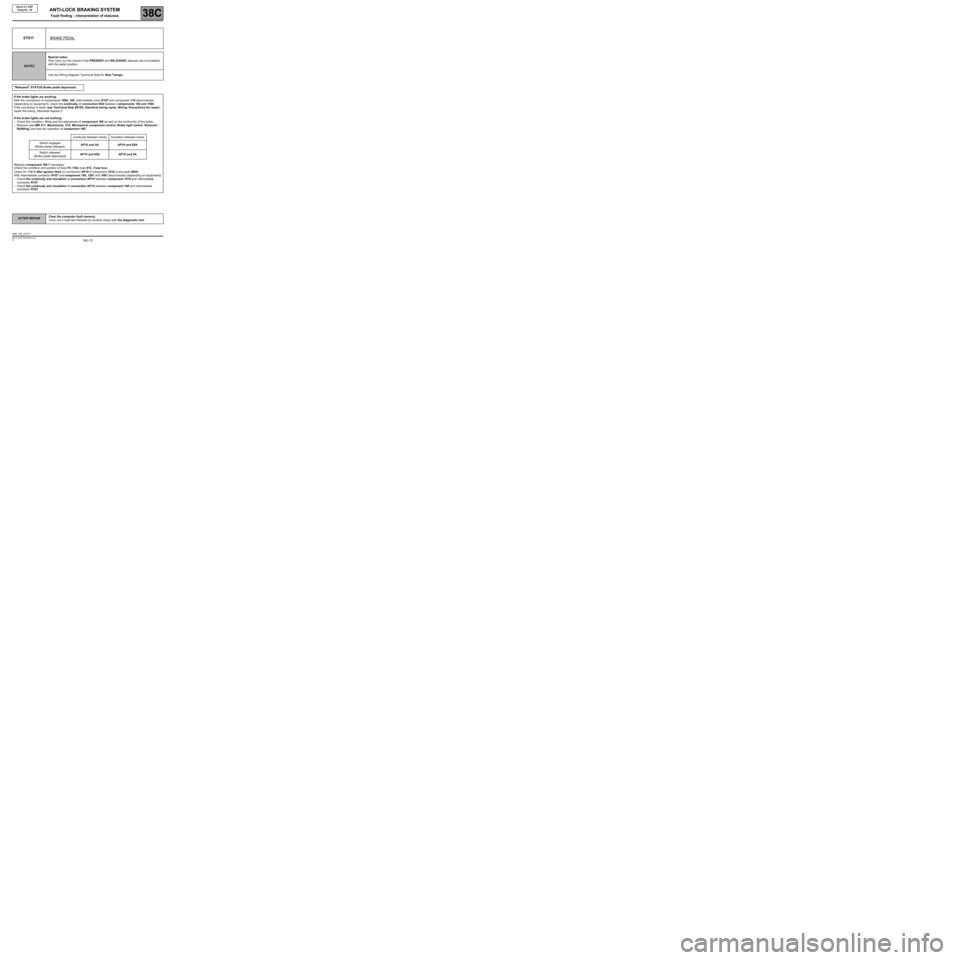
38C-72
AFTER REPAIRClear the computer fault memory.
Carry out a road test followed by another check with the diagnostic tool.
V3 MR-413-X44-38C050$130.mif
38C
Bosch 8.1 ESP
Vdiag No.: 05
ET017BRAKE PEDAL
NOTESSpecial notes:
Only carry out the checks if the PRESSED and RELEASED statuses are inconsistent
with the pedal position.
Use the Wiring Diagram Technical Note for New Twingo.
"Released" STATUS Brake pedal depressed.
If the brake lights are working:
With the connectors of components 1094, 160, intermediate union R107 and component 119 disconnected
(depending on equipment), check the continuity of connection 65A between components 160 and 1094.
If the connection is faulty (see Technical Note 6015A, Electrical wiring repair, Wiring: Precautions for repair),
repair the wiring, otherwise replace it.
If the brake lights are not working:
–Check the condition, fitting and the adjustment of component 160 as well as the conformity of the bulbs.
–Remove (see MR 411, Mechanical, 37A, Mechanical component control, Brake light switch: Removal -
Refitting) and test the operation of component 160:
Continuity between tracks Insulation between tracks
Switch engaged
(Brake pedal released)AP10 and 5A AP10 and 65A
Switch released
(Brake pedal depressed)AP10 and 65A AP10 and 5A
Replace component 160 if necessary.
Check the condition and position of fuse F5 (15A) (see 81C, Fuse box).
Check for +12 V after ignition feed on connection AP10 of component 1016 to the earth MAH.
With intermediate connector R107 and component 160, 1281 and 1081 disconnected (depending on equipment):
–Check the continuity and insulation of connection AP10 between component 1016 and intermediate
connector R107.
–Check the continuity and insulation of connection AP10 between component 160 and intermediate
connector R107.
ESP_V05_ET017
ANTI-LOCK BRAKING SYSTEM
Fault finding – Interpretation of statuses
Page 79 of 101
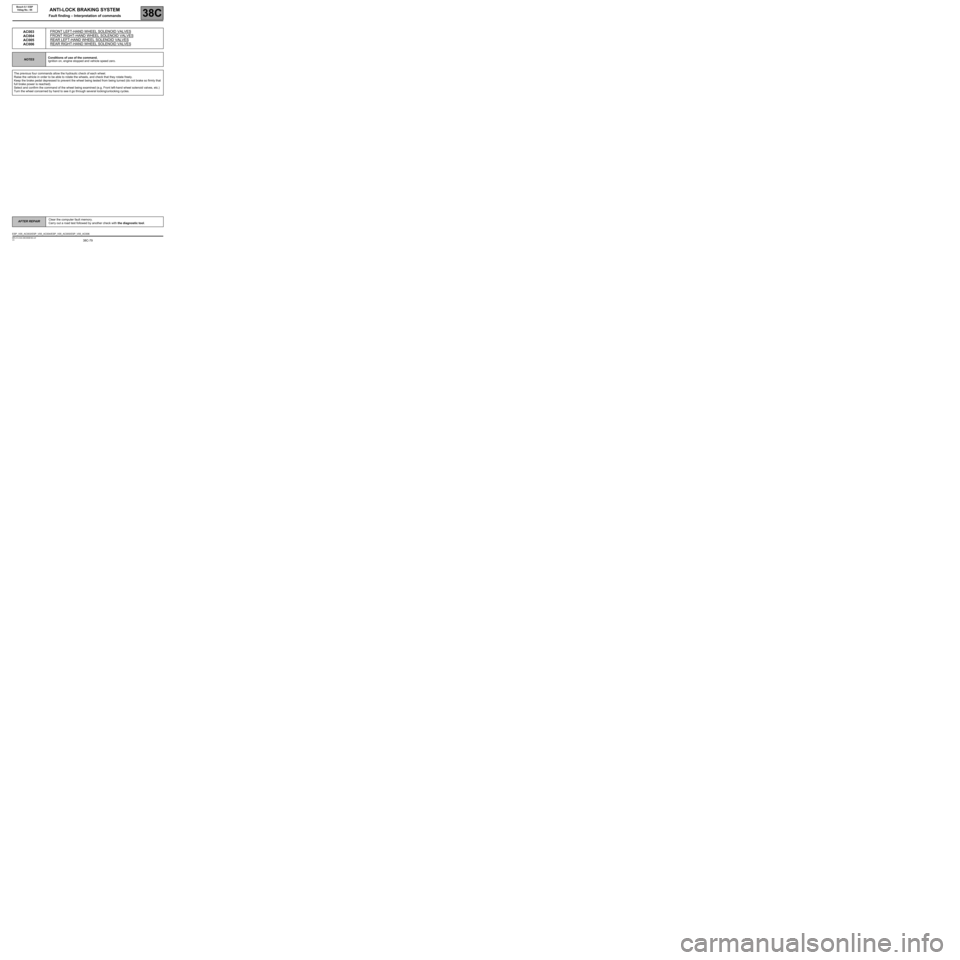
38C-79
AFTER REPAIRClear the computer fault memory.
Carry out a road test followed by another check with the diagnostic tool.
V3 MR-413-X44-38C050$160.mif
38C
Bosch 8.1 ESP
Vdiag No.: 05
AC003
AC004
AC005
AC006FRONT LEFT-HAND WHEEL SOLENOID VALVES
FRONT RIGHT-HAND WHEEL SOLENOID VALVES
REAR LEFT-HAND WHEEL SOLENOID VALVES
REAR RIGHT-HAND WHEEL SOLENOID VALVES
NOTESConditions of use of the command.
Ignition on, engine stopped and vehicle speed zero.
The previous four commands allow the hydraulic check of each wheel.
Raise the vehicle in order to be able to rotate the wheels, and check that they rotate freely.
Keep the brake pedal depressed to prevent the wheel being tested from being turned (do not brake so firmly that
full brake power is reached).
Select and confirm the command of the wheel being examined (e.g. Front left-hand wheel solenoid valves, etc.)
Turn the wheel concerned by hand to see it go through several locking/unlocking cycles.
ESP_V05_AC003/ESP_V05_AC004/ESP_V05_AC005/ESP_V05_AC006
ANTI-LOCK BRAKING SYSTEM
Fault finding – Interpretation of commands
Page 80 of 101
38C-80
AFTER REPAIRClear the computer fault memory.
Carry out a road test followed by another check with the diagnostic tool.
V3 MR-413-X44-38C050$160.mif
ANTI-LOCK BRAKING SYSTEM
Fault finding – Interpretation of commands38C
Bosch 8.1 ESP
Vdiag No.: 05
AC013WHEEL SPEED SENSOR SUPPLY TEST
NOTESConditions of use of the command.
Ignition on, engine off.
This command is used to test the supply to every wheel speed sensor.
Select command AC013 and check for 12 V between:
–connections 4T and 4S of component 150,
–connections 4H and 4G of component 151,
–connections 4E and 4C of component 153,
–connections 4N and 4M of component 152.
ESP_V05_AC013
Page 81 of 101
38C-81
AFTER REPAIRClear the computer fault memory.
Carry out a road test followed by another check with the diagnostic tool.
V3 MR-413-X44-38C050$160.mif
ANTI-LOCK BRAKING SYSTEM
Fault finding – Interpretation of commands38C
Bosch 8.1 ESP
Vdiag No.: 05
AC016PUMP MOTOR TEST
NOTESConditions of use of the command.
Ignition on, engine off.
This command is used to test the pump motor control circuit.
Select the command AC016.
Engine operation must be audible.
ESP_V05_AC016
Page 82 of 101
38C-82
AFTER REPAIRClear the computer fault memory.
Carry out a road test followed by another check with the diagnostic tool.
V3 MR-413-X44-38C050$160.mif
ANTI-LOCK BRAKING SYSTEM
Fault finding – Interpretation of commands38C
Bosch 8.1 ESP
Vdiag No.: 05
AC187BRAKE LIGHT ACTIVATION RELAY
NOTESConditions of use of the command.
Ignition on, engine off.
This command is used to test brake light activation by the ESP when controlling oversteer with sharp deceleration.
ESP_V05_AC187