Page 138 of 273
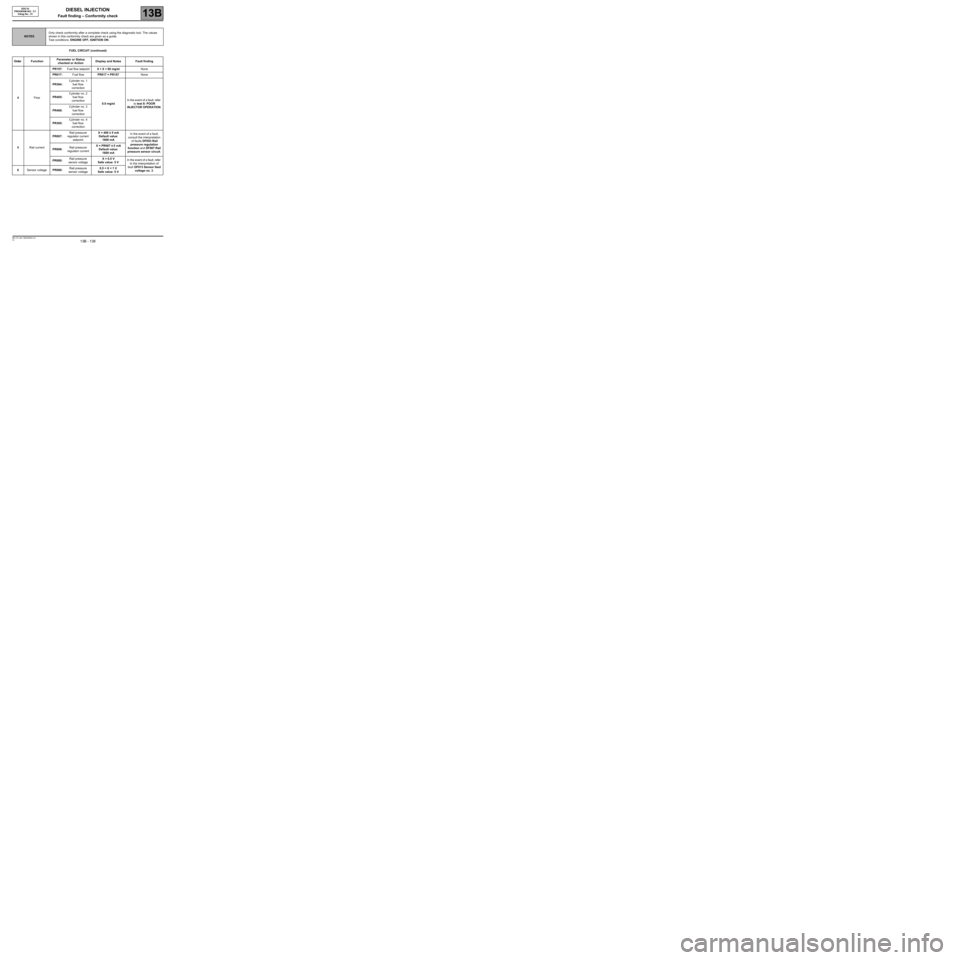
DIESEL INJECTION
Fault finding – Conformity check13B
13B - 138V3 MR-372-J84-13B250$450.mif
EDC16
PROGRAM NO.: C1
Vdiag No.: 51
FUEL CIRCUIT (continued)
NOTESOnly check conformity after a complete check using the diagnostic tool. The values
shown in this conformity check are given as a guide.
Test conditions: ENGINE OFF, IGNITION ON.
Order FunctionParameter or Status
checked or ActionDisplay and Notes Fault finding
4FlowPR157:Fuel flow setpoint0 < X < 60 mg/stNone
PR017:Fuel flowPR017 = PR157None
PR364:Cylinder no. 1
fuel flow
correction
0.0 mg/stIn the event of a fault, refer
to test 8: POOR
INJECTOR OPERATION. PR405:Cylinder no. 2
fuel flow
correction
PR406:Cylinder no. 3
fuel flow
correction
PR365:Cylinder no. 4
fuel flow
correction
5Rail currentPR007:Rail pressure
regulator current
setpointX = 400 ± 5 mA
Default value:
1600 mAIn the event of a fault,
consult the interpretation
of faults DF053 Rail
pressure regulation
function and DF007 Rail
pressure sensor circuit. PR006:Rail pressure
regulator currentX = PR007 ± 5 mA
Default value:
1600 mA
PR080:Rail pressure
sensor voltageX = 0.5 V
Safe value: 5 VIn the event of a fault, refer
to the interpretation of
fault DF013 Sensor feed
voltage no. 3. 6Sensor voltagePR080:Rail pressure
sensor voltage0.5 < X < 1 V
Safe value: 5 V
Page 156 of 273
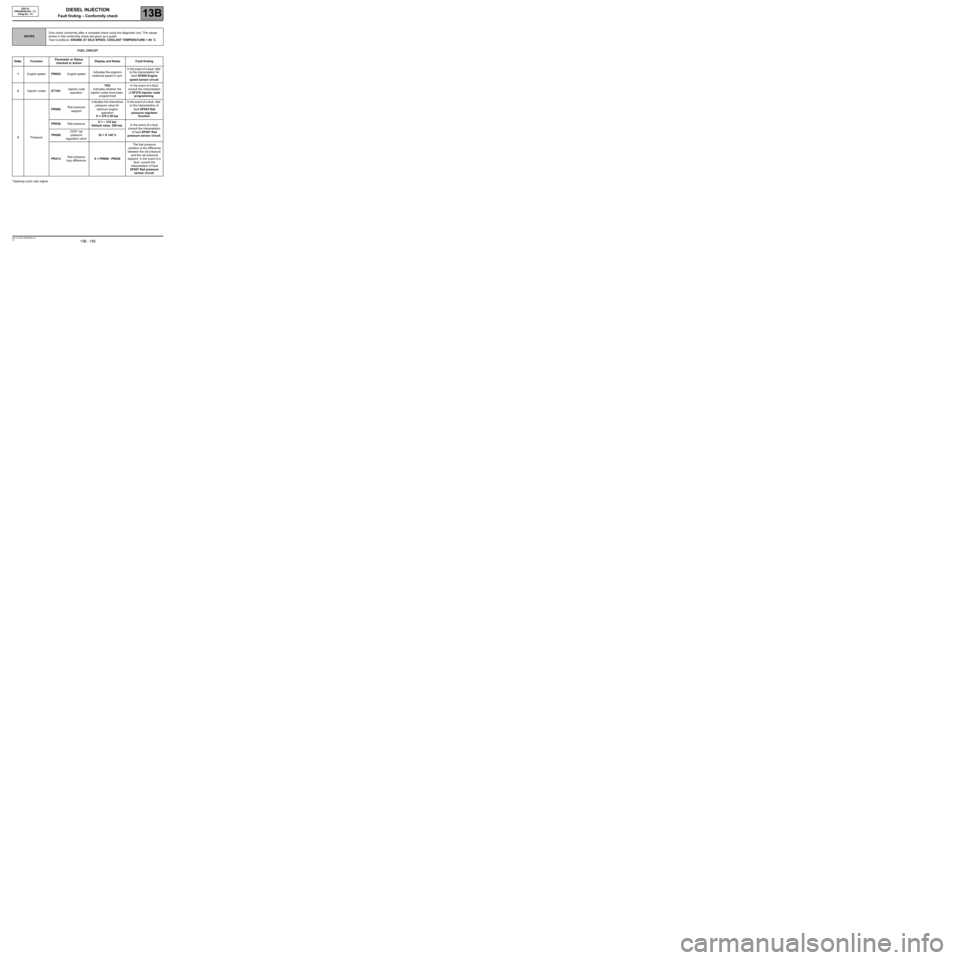
DIESEL INJECTION
Fault finding – Conformity check13B
13B - 156V3 MR-372-J84-13B250$450.mif
EDC16
PROGRAM NO.: C1
Vdiag No.: 51
FUEL CIRCUIT
*Opening cyclic ratio signal
NOTESOnly check conformity after a complete check using the diagnostic tool. The values
shown in this conformity check are given as a guide.
Test Conditions: ENGINE AT IDLE SPEED, COOLANT TEMPERATURE > 80 ˚C.
Order FunctionParameter or Status
checked or ActionDisplay and Notes Fault finding
1Engine speedPR055:Engine speedIndicates the engine's
rotational speed in rpm.In the event of a fault, refer
to the interpretation for
fault DF005 Engine
speed sensor circuit.
2Injector codesET104:Injector code
operationYES
Indicates whether the
injector codes have been
programmedIn the event of a fault,
consult the interpretation
of DF276 Injector code
programming.
3PressurePR008:Rail pressure
setpointIndicates the theoretical
pressure value for
optimum engine
operation
X = 270 ± 50 barIn the event of a fault, refer
to the interpretation of
fault DF053 Rail
pressure regulator
function.
PR038:Rail pressureX = ~ 315 bar
Default value: 250 bar.In the event of a fault,
consult the interpretation
of fault DF007 Rail
pressure sensor circuit. PR048:OCR* rail
pressure
regulation valve35 < X <45 %
PR213:Rail pressure
loop differenceX = PR008 - PR038The fuel pressure
variation is the difference
between the rail pressure
and the rail pressure
setpoint. In the event of a
fault, consult the
interpretation of fault
DF007 Rail pressure
sensor circuit.
Page 224 of 273
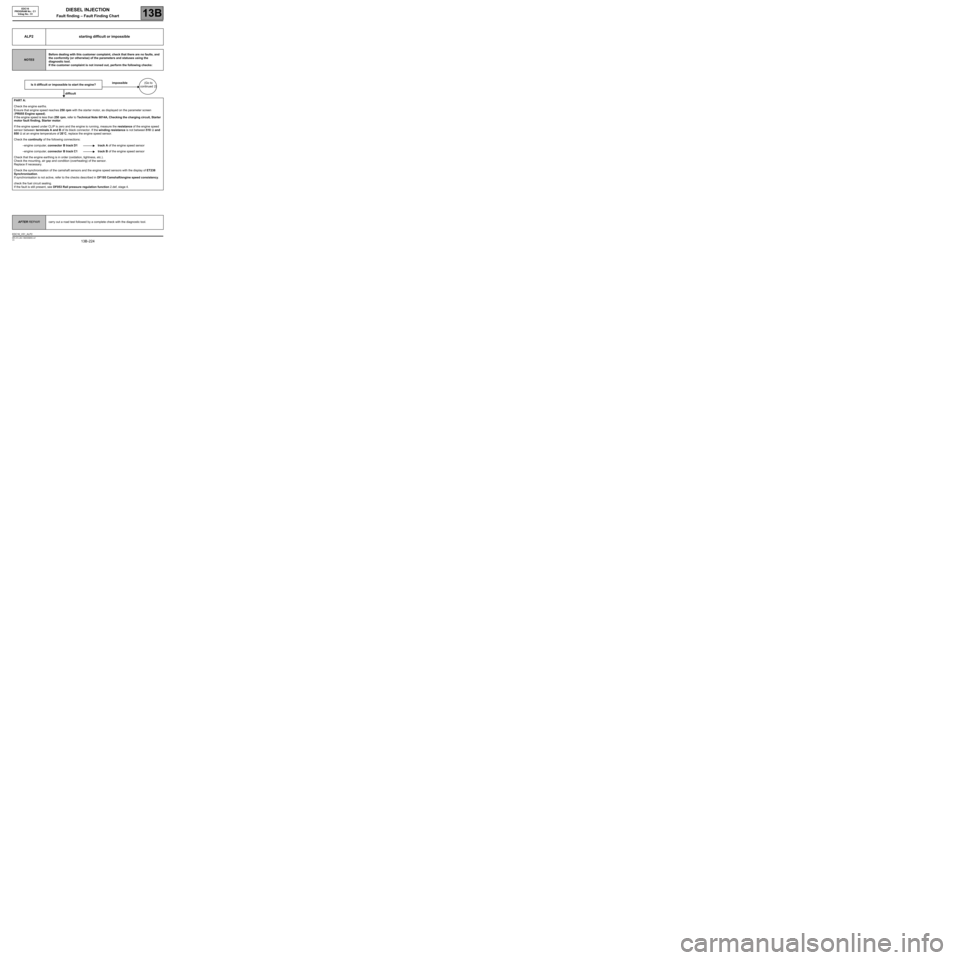
DIESEL INJECTION
Fault finding – Fault Finding Chart13B
13B -224V3 MR-372-J84-13B250$855.mif
EDC16
PROGRAM No.: C1
Vdiag No.: 51
ALP2 starting difficult or impossible
NOTESBefore dealing with this customer complaint, check that there are no faults, and
the conformity (or otherwise) of the parameters and statuses using the
diagnostic tool.
If the customer complaint is not ironed out, perform the following checks:
Is it difficult or impossible to start the engine?impossible(Go to
continued 2)
difficult
PART A:
Check the engine earths.
Ensure that engine speed reaches 250 rpm with the starter motor, as displayed on the parameter screen
(PR055 Engine speed).
If the engine speed is less than 250 rpm, refer to Technical Note 6014A, Checking the charging circuit, Starter
motor fault finding, Starter motor.
If the engine speed under CLIP is zero and the engine is running, measure the resistance of the engine speed
sensor between terminals A and B of its black connector. If the winding resistance is not between 510 Ω and
850 Ω at an engine temperature of 20˚C, replace the engine speed sensor.
Check the continuity of the following connections:
–engine computer, connector B track D1 track A of the engine speed sensor
–engine computer, connector B track C1 track B of the engine speed sensor
Check that the engine earthing is in order (oxidation, tightness, etc.).
Check the mounting, air gap and condition (overheating) of the sensor.
Replace if necessary.
Check the synchronisation of the camshaft sensors and the engine speed sensors with the display of ET238
Synchronisation.
If synchronisation is not active, refer to the checks described in DF195 Camshaft/engine speed consistency.
check the fuel circuit sealing.
If the fault is still present, see DF053 Rail pressure regulation function 2.def, stage 4.
AFTER REPAIRcarry out a road test followed by a complete check with the diagnostic tool.
EDC16_V51_ALP2
Page 229 of 273
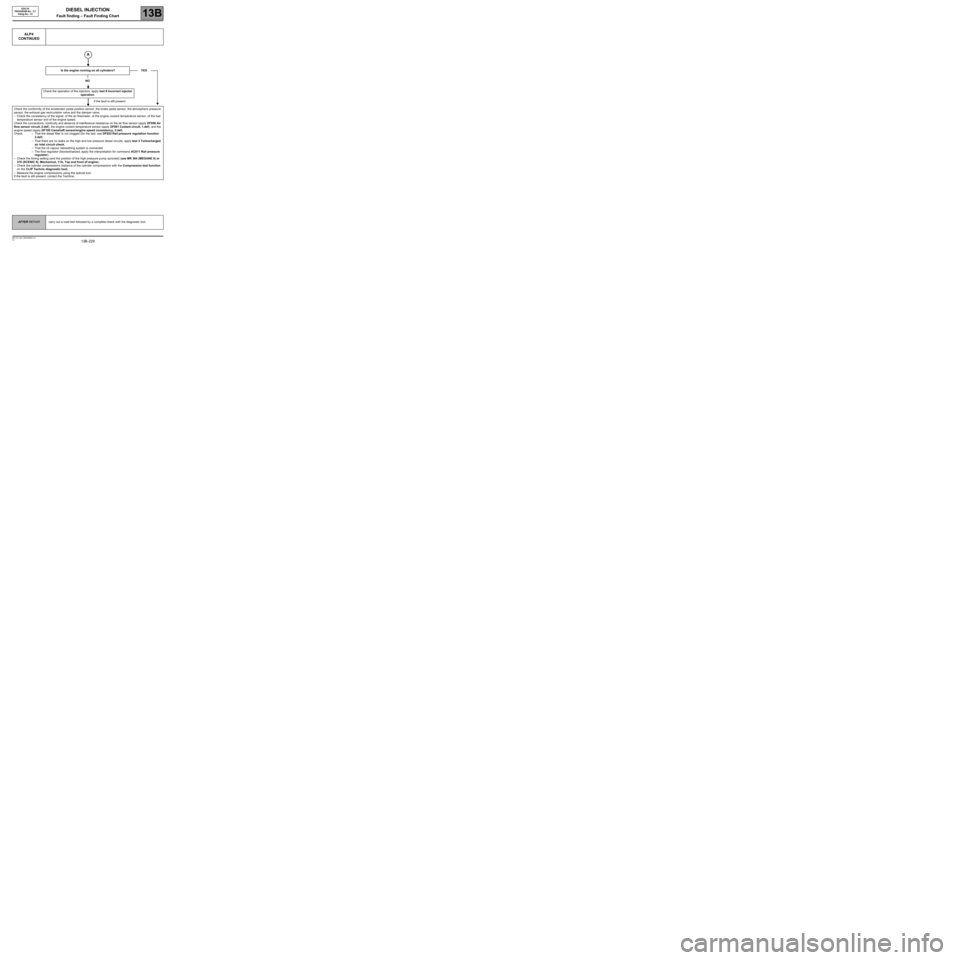
DIESEL INJECTION
Fault finding – Fault Finding Chart13B
13B -229V3 MR-372-J84-13B250$855.mif
ALP4
CONTINUED
Is the engine running on all cylinders?
NO
Check the operation of the injectors: apply test 8 Incorrect injector
operation.
If the fault is still present
Check the conformity of the accelerator pedal position sensor, the brake pedal sensor, the atmospheric pressure
sensor, the exhaust gas recirculation valve and the damper valve.
–Check the consistency of the signal: of the air flowmeter, of the engine coolant temperature sensor, of the fuel
temperature sensor and of the engine speed.
Check the connections, continuity and absence of interference resistance on the air flow sensor (apply DF056 Air
flow sensor circuit, 2.def), the engine coolant temperature sensor (apply DF001 Coolant circuit, 1.def), and the
engine speed (apply DF195 Camshaft sensor/engine speed consistency, 2.def).
Check: – That the diesel filter is not clogged (for the test, see DF053 Rail pressure regulation function
2.def).
–That there are no leaks on the high and low pressure diesel circuits: apply test 3 Turbocharged
air inlet circuit check.
–That the oil vapour rebreathing system is connected.
–The flow regulator (blocked/seized, apply the interpretation for command: AC011 Rail pressure
regulator).
–Check the timing setting (and the position of the high pressure pump sprocket) (see MR 364 (MEGANE II) or
370 (SCENIC II), Mechanical, 11A, Top and front of engine).
–Check the cylinder compressions (balance of the cylinder compressions with the Compression test function
on the CLIP Technic diagnostic tool).
–Measure the engine compressions using the special tool.
If the fault is still present, contact the Techline.YES
EDC16
PROGRAM No.: C1
Vdiag No.: 51
AFTER REPAIRcarry out a road test followed by a complete check with the diagnostic tool.