Page 122 of 241
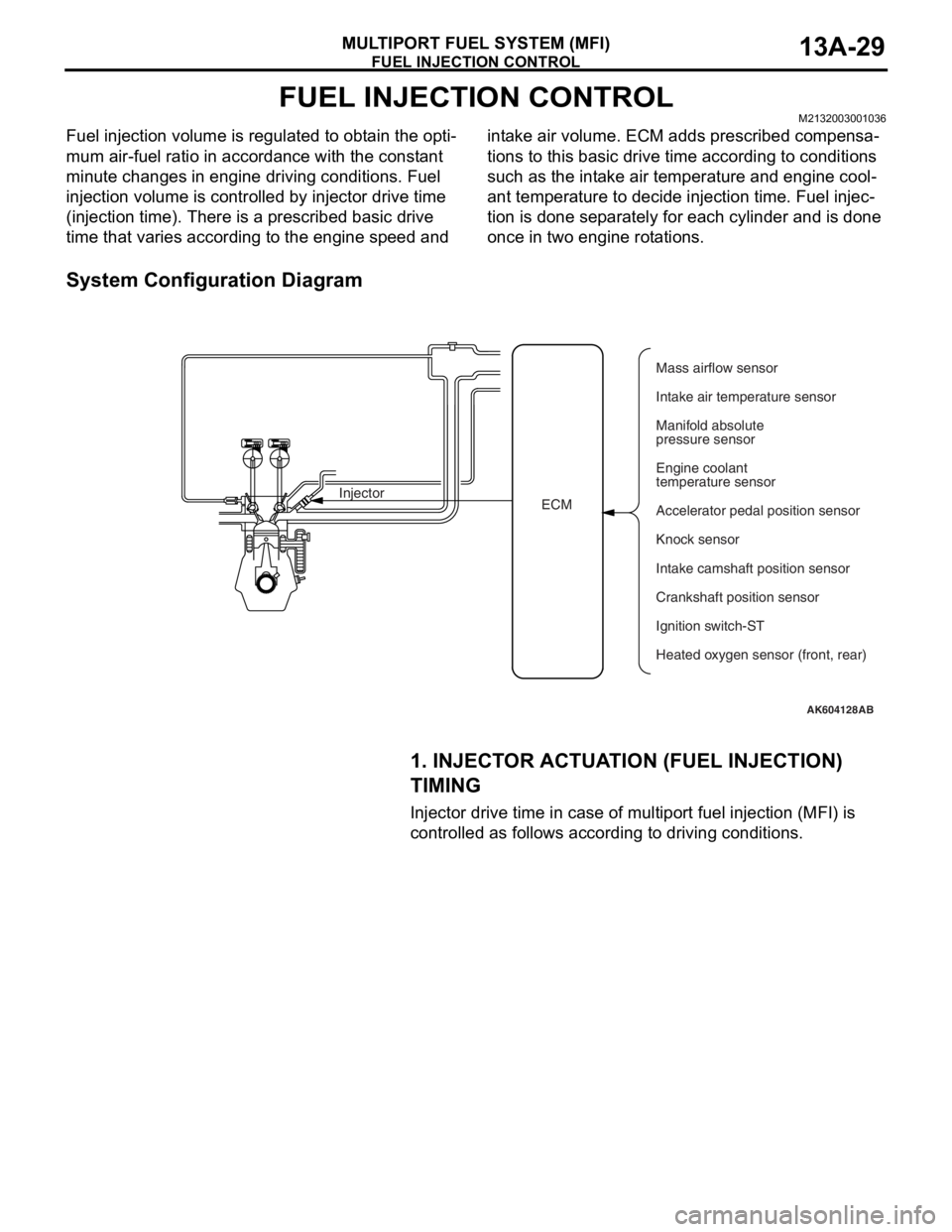
FUEL INJECTION CONTROL
MULTIPORT FUEL SYSTEM (MFI)13A-29
FUEL INJECTION CONTROLM2132003001036
Fuel injection volume is regulated to obtain the opti-
mum air-fuel ratio in accordance with the constant
minute changes in engine driving conditions. Fuel
injection volume is controlled by injector drive time
(injection time). There is a prescribed basic drive
time that varies according to the engine speed and intake air volume. ECM adds prescribed compensa
-
tions to this basic drive time according to conditions
such as the intake air temperature and engine cool
-
ant temperature to decide injection time. Fuel injec-
tion is done separately for each cylinder and is done
once in two engine rotations.
System Configuration Diagram
1. INJECTOR ACTUATION (FUEL INJECTION)
TIMING
Injector drive time in case of multiport fuel injection (MFI) is
controlled as follows according to driving conditions.
AK604128AB
ECM InjectorMass airflow sensor
Intake air temperature sensor
Manifold absolute
pressure sensor
Engine coolant
temperature sensor
Accelerator pedal position sensor
Knock sensor
Intake camshaft position sensor
Ignition switch-ST
Heated oxygen sensor (front, rear) Crankshaft position sensor
Page 123 of 241
FUEL INJECTION CONTROL
MULTIPORT FUEL SYSTEM (MFI)13A-30
Fuel Injection During Cranking and Normal Operation
Fuel injection to each cylinder is done by driving the injector at
optimum timing while it is in exhaust process based on the
crankshaft position sensor signal. ECM compares the crank
-
shaft position sensor output pulse signal and intake camshaft
position sensor output pulse signal to identify the cylinder.
Using this as a base, it performs sequential injection in the
sequence of cylinders 1, 3, 4, 2.
AK604622AB
Cylinder stroke
No. 1 Cylinder
No. 3 Cylinder
No. 4 Cylinder
No. 2 CylinderCombustion
Intake
Exhaust
CombustionExhaust
Compression: Fuel injection
Intake
Exhaust CompressionCombustion
Intake CompressionIntake
Exhaust
Combustion
Compression
H
L H
L
H
L Crankshaft
position
sensor signal
Intake camshaft
position sensor
signal
Exhaust camshaft
position sensor
signal
Page 124 of 241
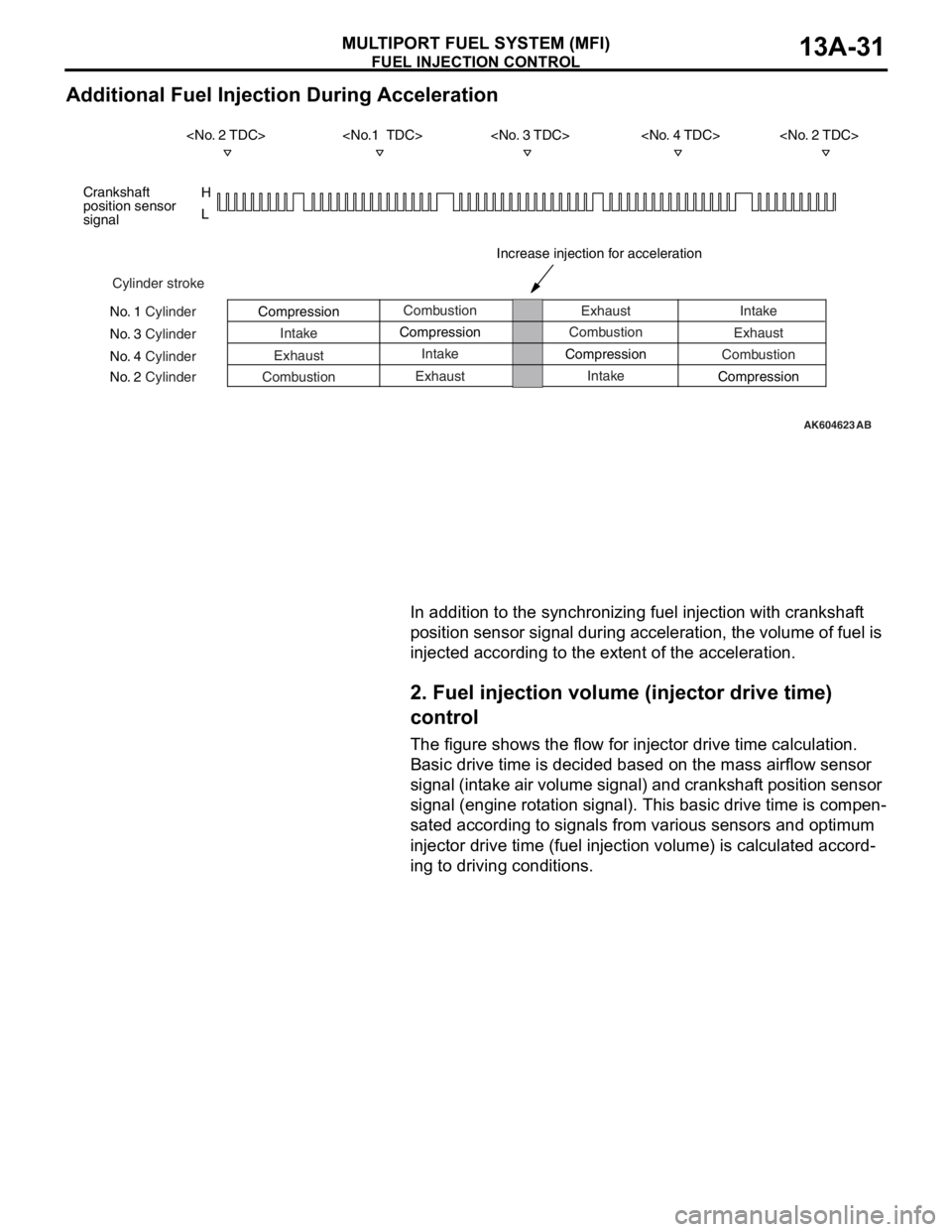
FUEL INJECTION CONTROL
MULTIPORT FUEL SYSTEM (MFI)13A-31
Additional Fuel Injection During Acceleration
In addition to the synchronizing fuel injection with crankshaft
position sensor signal during acceleration, the volume of fuel is
injected according to the extent of the acceleration.
2. Fuel injection volume (injector drive time)
control
The figure shows the flow for injector drive time calculation.
Basic drive time is decided based on the mass airflow sensor
signal (intake air volume signal) and crankshaft position sensor
signal (engine rotation signal). This basic drive time is compen
-
sated according to signals from various sensors and optimum
injector drive time (fuel injection volume) is calculated accord
-
ing to driving conditions.
AK604623
H
L
AB
Cylinder stroke
No. 1 Cylinder
No. 3 Cylinder
No. 4 Cylinder
No. 2 CylinderCombustion
Intake
Exhaust
CombustionExhaust
Compression
Intake
Exhaust CompressionCombustion
Intake CompressionIntake
Exhaust
Combustion
Compression Crankshaft
position sensor
signal
Increase injection for acceleration
Page 125 of 241
FUEL INJECTION CONTROL
MULTIPORT FUEL SYSTEM (MFI)13A-32
Fuel Injection Volume Control Block Diagram
.
AK602278AD
Mass airflow sensor
Crankshaft
position sensor
Heated oxygen
sensor
Engine coolant
temperature
compensation Engine coolant
temperature sensor
Manifold absolute
pressure sensorFuel pressure
compensation Barometric pressure
sensor
Battery voltage
compensation Battery voltageBasic fuel
injection time
determinationAir fuel ratio
compensation
(Predetermined
compensation)
Heated oxygen
sensor feedback
compensation
Injector Acceleration-
deceleration
compensation
Page 126 of 241
![MITSUBISHI LANCER EVOLUTION X 2008 Workshop Manual FUEL INJECTION CONTROL
MULTIPORT FUEL SYSTEM (MFI)13A-33
[Injector basic drive time]
Fuel injection is performed once per cycle for each cylinder.
Basic drive time refers to fuel injection volume (in MITSUBISHI LANCER EVOLUTION X 2008 Workshop Manual FUEL INJECTION CONTROL
MULTIPORT FUEL SYSTEM (MFI)13A-33
[Injector basic drive time]
Fuel injection is performed once per cycle for each cylinder.
Basic drive time refers to fuel injection volume (in](/manual-img/19/57326/w960_57326-125.png)
FUEL INJECTION CONTROL
MULTIPORT FUEL SYSTEM (MFI)13A-33
[Injector basic drive time]
Fuel injection is performed once per cycle for each cylinder.
Basic drive time refers to fuel injection volume (injector drive
time) to achieve theoretical air-fuel ratio for the intake air vol
-
ume of 1 cycle of 1 cylinder. Fuel injection volume changes
according to the pressure difference (injected fuel pressure)
between manifold absolute pressure and fuel pressure (con
-
stant). So, injected fuel pressure compensation is made to
injector drive time for theoretical air-fuel ratio to arrive at basic
drive time.
Intake air volume of each cycle of 1 cylinder is calculated by
ECM based on the mass airflow sensor signal and crankshaft
position sensor signal. Also, during engine start, the map value
prescribed by the engine coolant temperature sensor signal is
used as basic drive time.
.
AK602279AC
Basic fuel
injection timeFuel injection pressure compensation Intake air amount per cycle per cylinder
Theoretical air-fuel ratio
Page 127 of 241
![MITSUBISHI LANCER EVOLUTION X 2008 Workshop Manual FUEL INJECTION CONTROL
MULTIPORT FUEL SYSTEM (MFI)13A-34
[Injector drive time compensation]
After calculating the injector basic drive time, the ECM makes
the following compensations to control the o MITSUBISHI LANCER EVOLUTION X 2008 Workshop Manual FUEL INJECTION CONTROL
MULTIPORT FUEL SYSTEM (MFI)13A-34
[Injector drive time compensation]
After calculating the injector basic drive time, the ECM makes
the following compensations to control the o](/manual-img/19/57326/w960_57326-126.png)
FUEL INJECTION CONTROL
MULTIPORT FUEL SYSTEM (MFI)13A-34
[Injector drive time compensation]
After calculating the injector basic drive time, the ECM makes
the following compensations to control the optimum fuel injec
-
tion volume according to driving conditions.
List of main compensations for fuel injection control
.
[Fuel limit control during deceleration]
ECM limits fuel when decelerating downhill to prevent exces-
sive rise of catalytic converter temperature and to improve fuel
efficiency.
.
[Fuel-cut control when over-run]
When engine speed exceeds a prescribed limit (6,600 r/min),
ECM cuts fuel supply to prevent overrunning and thus protect
the engine. Also, if engine speed exceeds 4,000 r/min for 15
seconds while vehicle is stationary (no load), it cuts fuel supply
and controls the throttle valve opening angle to protect the
engine.
CompensationsContent
Heated oxygen sensor feedback compensationThe heated oxygen sensor signal is used for
making the compensation to get air-fuel ratio with
best cleaning efficiency of the 3-way catalytic
converter. This compensation might not be made
sometimes in order to improve drivability,
depending on driving conditions. (Air-fuel ratio
compensation is made.)
Air-fuel ratio compensationUnder driving conditions where heated oxygen
sensor feedback compensation is not performed,
compensation is made based on pre-set map
values that vary according to engine speed and
intake air volume.
Engine coolant temperature compensationCompensation is made according to the engine
coolant temperature. The lower the engine coolant
temperature, the greater the fuel injection volume.
Acceleration/ Deceleration compensationCompensation is made according to change in
intake air volume. During acceleration, fuel injection
volume is increased. Also, during deceleration, fuel
injection volume is decreased.
Fuel injection compensationCompensation is made according to the pressure
difference between atmospheric pressure and
manifold absolute pressure. The greater the
difference in pressure, the shorter the injector drive
time.
Battery voltage compensationCompensation is made depending on battery
voltage. The lower the battery voltage, the greater
the injector drive signal time.
Learning value for fuel compensationCompensation amount is learned to compensate
feedback of heated oxygen sensor. This allows
system to compensate in accordance with engine
characteristics.
Page 128 of 241
IGNITION TIMING AND CONTROL FOR CURRENT CARRYING TIME
MULTIPORT FUEL SYSTEM (MFI)13A-35
IGNITION TIMING AND CONTROL FOR CURRENT
CARRYING TIME
M2132027100089
Ignition timing is pre-set according to engine driving
conditions. Compensations are made according to
pre-set values depending on conditions such as
engine coolant temperature, battery voltage etc. to
decide optimum ignition timing. Primary current con
-
nect/disconnect signal is sent to the power transistor
to control ignition timing. Ignition is done in sequence
of cylinders 1, 3, 4, 2.
System Configuration Diagram
AK502722AD
ECM MFI relay
Spark plugs Ignition
coils
Cylinder No. 1 2 3 4Battery
Mass airflow sensor
Intake air temperature sensor
Manifold absolute
pressure sensor
Engine coolant
temperature sensor
Intake camshaft position sensor
Exhaust camshaft position sensor
Crankshaft position sensor
Knock sensor
Ignition switch-ST Throttle position sensor
Page 129 of 241
IGNITION TIMING AND CONTROL FOR CURRENT CARRYING TIME
MULTIPORT FUEL SYSTEM (MFI)13A-36
1. Ignition distribution control
Based on the crankshaft position sensor signal and camshaft
position sensor signal, ECM decides the ignition cylinder, cal
-
culates the ignition timing and sends the ignition coil primary
current connect/disconnect signal to the power transistor of
each cylinder in the ignition sequence.
AK604624
Exhaust
AB
Cylinder stroke
No. 1 Cylinder
No. 3 Cylinder
No. 4 Cylinder
No. 2 CylinderCombustion
Intake
Exhaust
Combustion CompressionIgnition
Intake
Exhaust CompressionCombustion
Intake CompressionIntake
Exhaust
Combustion
Compression H
L
H
L
H
L Crankshaft
position
sensor signal
Intake camshaft
position sensor
signal
Exhaust camshaft
position sensor
signal