Page 156 of 444
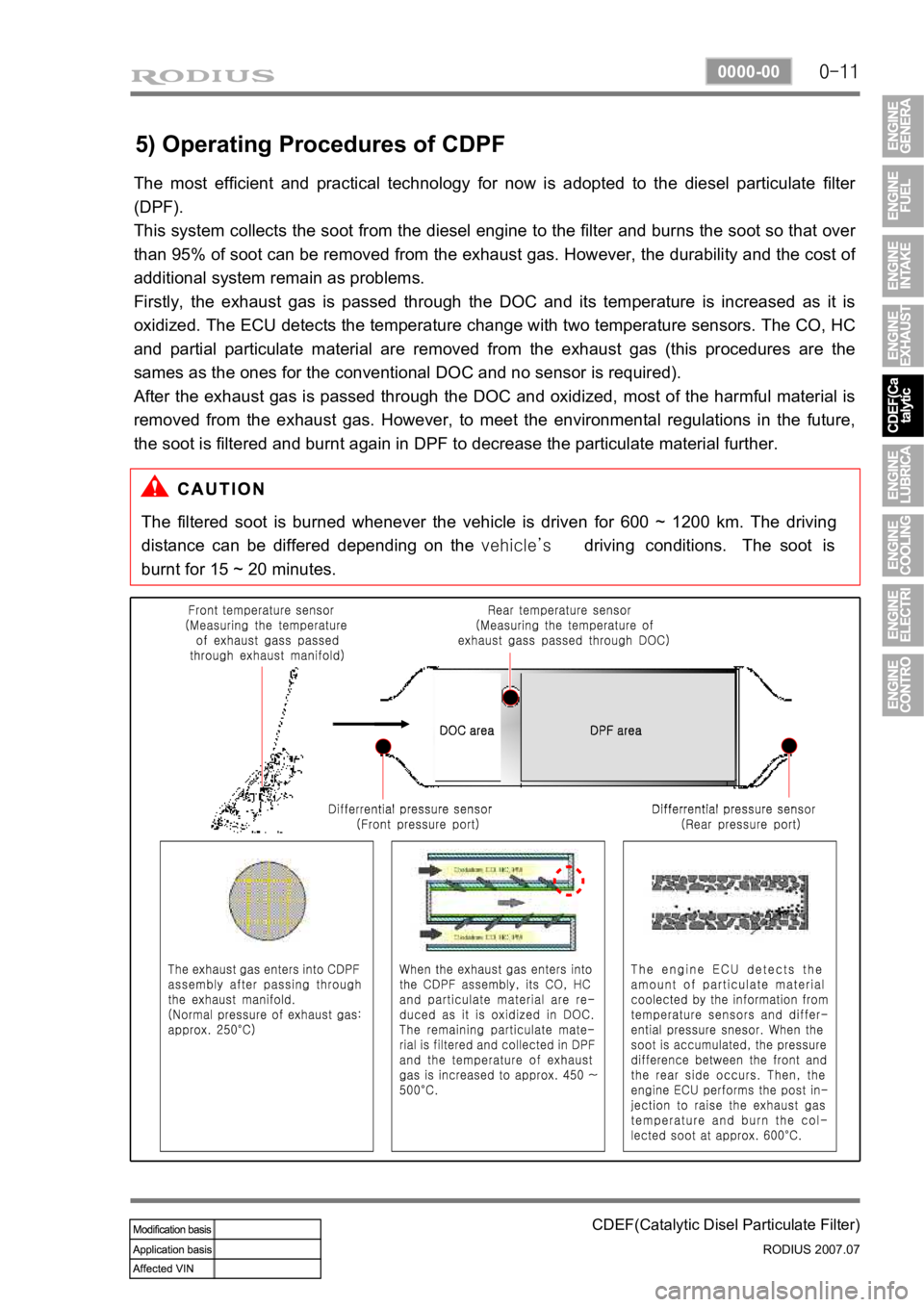
0-11
CDEF(Catalytic Disel Particulate Filter)
RODIUS 2007.07
0000-00
5) Operating Procedures of CDPF
The most efficient and practical technology for now is adopted to the diesel particulate filter
(DPF).
This system collects the soot from the diesel engine to the filter and burns the soot so that ove
r
than 95% of soot can be removed from the exhaust gas. However, the durability and the cost o
f
additional system remain as problems.
Firstly, the exhaust gas is passed through the DOC and its temperature is increased as it is
oxidized. The ECU detects the temperature change with two temperature sensors. The CO, HC
and partial particulate material are removed from the exhaust gas (this procedures are the
sames as the ones for the conventional DOC and no sensor is required).
After the exhaust gas is passed through the DOC and oxidized, most of the harmful material is
removed from the exhaust gas. However, to meet the environmental regulations in the future,
the soot is filtered and burnt again in DPF to decrease the particulate material further.
The filtered soot is burned whenever the vehicle is driven for 600 ~ 1200 km. The driving
distance can be differed depending on the vehicle’s driving conditions. The soot is
burnt for 15 ~ 20 minutes.
Page 157 of 444
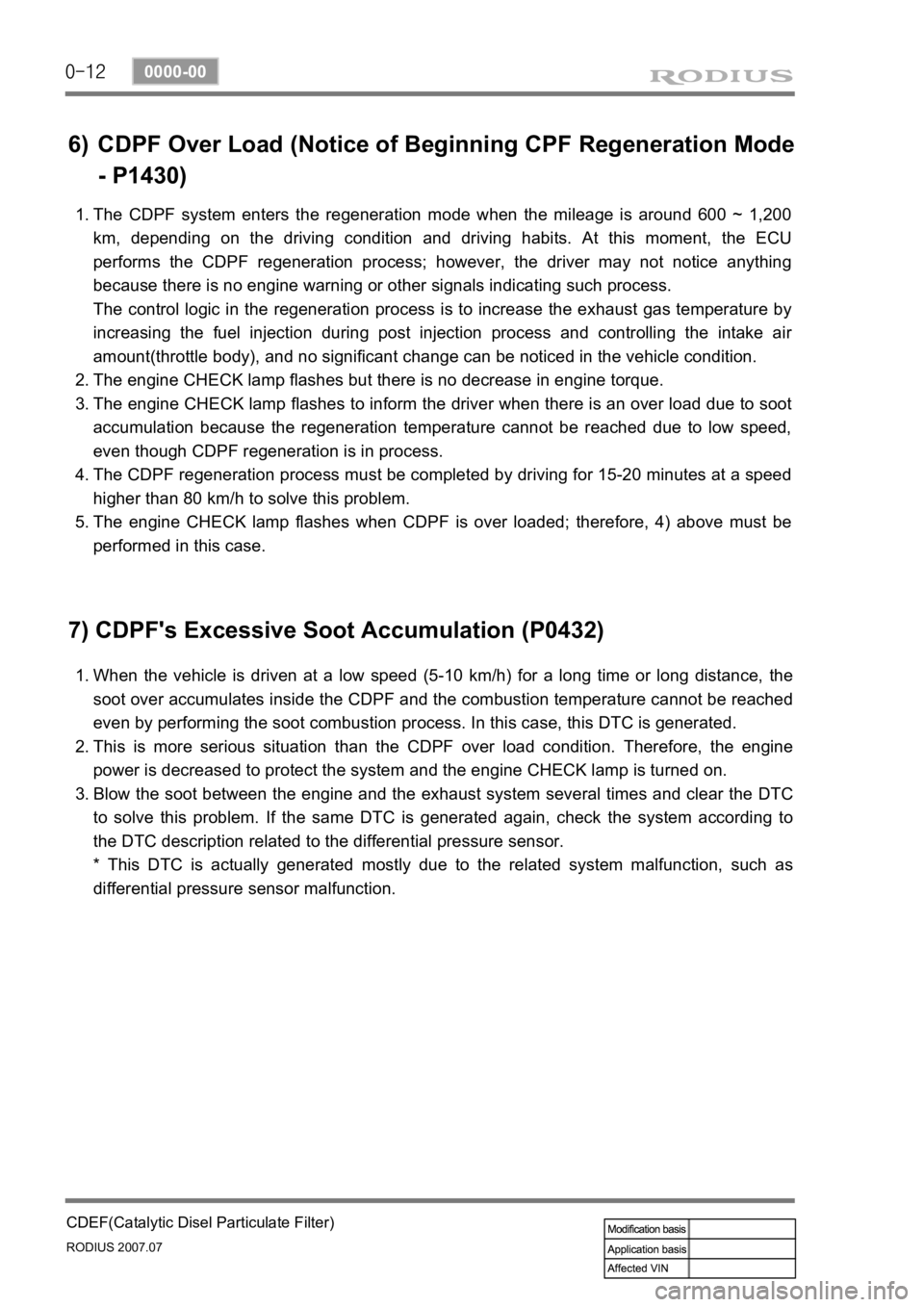
0-12
RODIUS 2007.07
0000-00
CDEF(Catalytic Disel Particulate Filter)
6) CDPF Over Load (Notice of Beginning CPF Regeneration Mode
- P1430)
The CDPF system enters the regeneration mode when the mileage is around 600 ~ 1,200
km, depending on the driving condition and driving habits. At this moment, the ECU
performs the CDPF regeneration process; however, the driver may not notice anything
because there is no engine warning or other signals indicating such process.
The control logic in the regeneration process is to increase the exhaust gas temperature by
increasing the fuel injection during post injection process and controlling the intake ai
r
amount(throttle body), and no significant change can be noticed in the vehicle condition.
The engine CHECK lamp flashes but there is no decrease in engine torque.
The engine CHECK lamp flashes to inform the driver when there is an over load due to soot
accumulation because the regeneration temperature cannot be reached due to low speed,
even though CDPF regeneration is in process.
The CDPF regeneration process must be completed by driving for 15-20 minutes at a speed
higher than 80 km/h to solve this problem.
The engine CHECK lamp flashes when CDPF is over loaded; therefore, 4) above must be
performed in this case. 1.
2.
3.
4.
5.
7) CDPF's Excessive Soot Accumulation (P0432)
When the vehicle is driven at a low speed (5-10 km/h) for a long time or long distance, the
soot over accumulates inside the CDPF and the combustion temperature cannot be reached
even by performing the soot combustion process. In this case, this DTC is generated.
This is more serious situation than the CDPF over load condition. Therefore, the engine
power is decreased to protect the system and the engine CHECK lamp is turned on.
Blow the soot between the engine and the exhaust system several times and clear the DTC
to solve this problem. If the same DTC is generated again, check the system according to
the DTC description related to the differential pressure sensor.
* This DTC is actually generated mostly due to the related system malfunction, such as
differential pressure sensor malfunction. 1.
2.
3.
Page 169 of 444
0-7
ELECTRIC GENERAL
RODIUS 2007.07
0000-00
Sub condenser
Theft deterrent horn (under the washer fluid reservoir)
PTC power supply relay
(PTC system equipped vehicle)
ABS (ESP) HECU
(under the battery)
Fuse and relay box in engine compartmentBrake pressure sensor
Page 178 of 444
0-5
STICS
RODIUS 2007.07
8710-01
The STICS in this vehicle has similar functions with the one used in the new Rexton. Additional
function of diagnosing through SCAN-Tool has been added into new STICS.
The major difference in hardware-wise is that STICS receives vehicle collision signal from G-
sensor in the airbag module to activate automatic door unlock function when the vehicle
collided over 15 km/h of vehicle speed.
1. COMPONENTS LOCATOR
STICS / ICM module
Air bag ECU
Sends the vehicle collision
signals to STICS.
Theft deterrent horn
Installed under the battery. This
horn works only for the theft
deterrent function, panic
function, and remote starting.
SCAN-tool
SCAN-100 is used fo
r
REKES key coding and
trouble diagnosis.
REKES
Added the escort and
panic function
RK STICS
ICM module
This module contains
various relays, chime and
buzzer controlled by
STICS
Page 279 of 444
0-6
RODIUS 2007.07
3240-01
TORQUE ON DEMAND
When turning on the road with low friction rate ▶
During cornering on roads such as unpaved, snowy, icy and muddy, ground grab capacity is
increased by distributing required torque and, at the same time, comfortable steering operation
is maintained by controlling the ground grab capacity at high level.
Distribution ratio: 30 % for front wheels and 70 % for rear wheels.
When climbing or starting off on the road with low friction rate ▶
In order to secure the maximum ground grab capacity and driving force during climbing o
r
starting off on the roads such as unpaved, snowy and icy road, the system controls the driving
force to distribute properly in full 4WD mode.
Distribution ratio: 44 % for front wheels and 56 % for rear wheels.
Page 303 of 444
0-4
RODIUS 2007.07
4892-01
ESP SYSTEM
1. COMPONENTS AND LOCATIONS
2WD vehicle has the longitudinal sensor in the HECU.
1. HECU: (Hydraulic &
Engine conrol unit) 2. Pressure sensor 3. Wheel speed sensor
4. Sensor cluster:
(Yaw rate + lateral sensor + longitudinal sensor) 5. Steering wheel angle
sensor 6. ESP off switch (Electronic
Stability Program Switch) ESP Warning lamp
Page 305 of 444
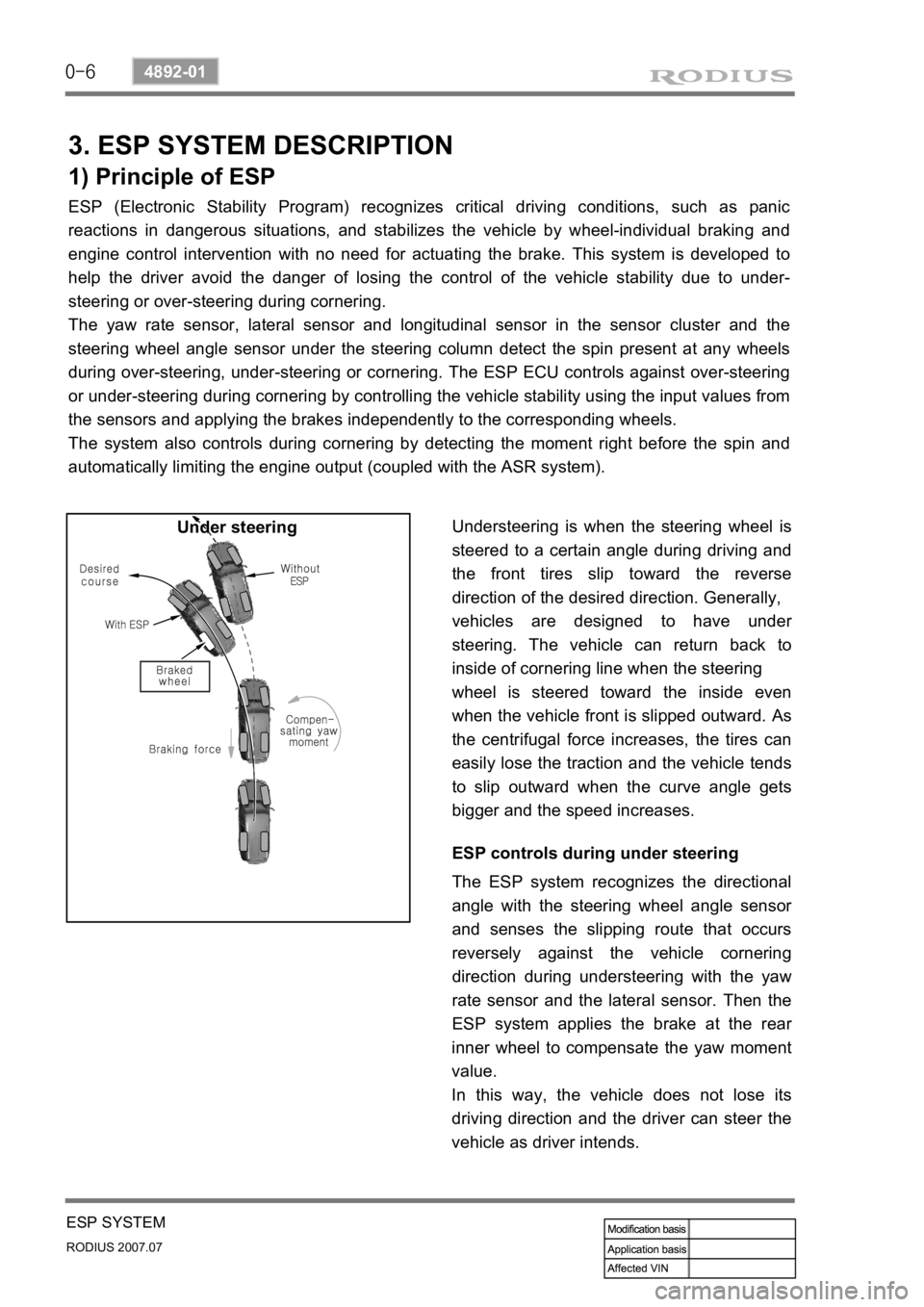
0-6
RODIUS 2007.07
4892-01
ESP SYSTEM
3. ESP SYSTEM DESCRIPTION
1) Principle of ESP
ESP (Electronic Stability Program) recognizes critical driving conditions, such as panic
reactions in dangerous situations, and stabilizes the vehicle by wheel-individual braking and
engine control intervention with no need for actuating the brake. This system is developed to
help the driver avoid the danger of losing the control of the vehicle stability due to under-
steering or over-steering during cornering.
The yaw rate sensor, lateral sensor and longitudinal sensor in the sensor cluster and the
steering wheel angle sensor under the steering column detect the spin present at any wheels
during over-steering, under-steering or cornering. The ESP ECU controls against over-steering
or under-steering during cornering by controlling the vehicle stability using the input values from
the sensors and applying the brakes independently to the corresponding wheels.
The system also controls during cornering by detecting the moment right before the spin and
automatically limiting the engine output (coupled with the ASR system).
Understeering is when the steering wheel is
steered to a certain angle during driving and
the front tires slip toward the reverse
direction of the desired direction. Generally,
vehicles are designed to have unde
r
steering. The vehicle can return back to
inside of cornering line when the steering
wheel is steered toward the inside even
when the vehicle front is slipped outward.
As
the centrifugal force increases, the tires can
easily lose the traction and the vehicle tends
to slip outward when the curve angle gets
bigger and the speed increases. Under steering
ESP controls during under steering
The ESP system recognizes the directional
angle with the steering wheel angle senso
r
and senses the slipping route that occurs
reversely against the vehicle cornering
direction during understeering with the yaw
rate sensor and the lateral sensor. Then the
ESP system applies the brake at the rea
r
inner wheel to compensate the yaw moment
value.
In this way, the vehicle does not lose its
driving direction and the driver can steer the
vehicle as driver intends.
Page 309 of 444
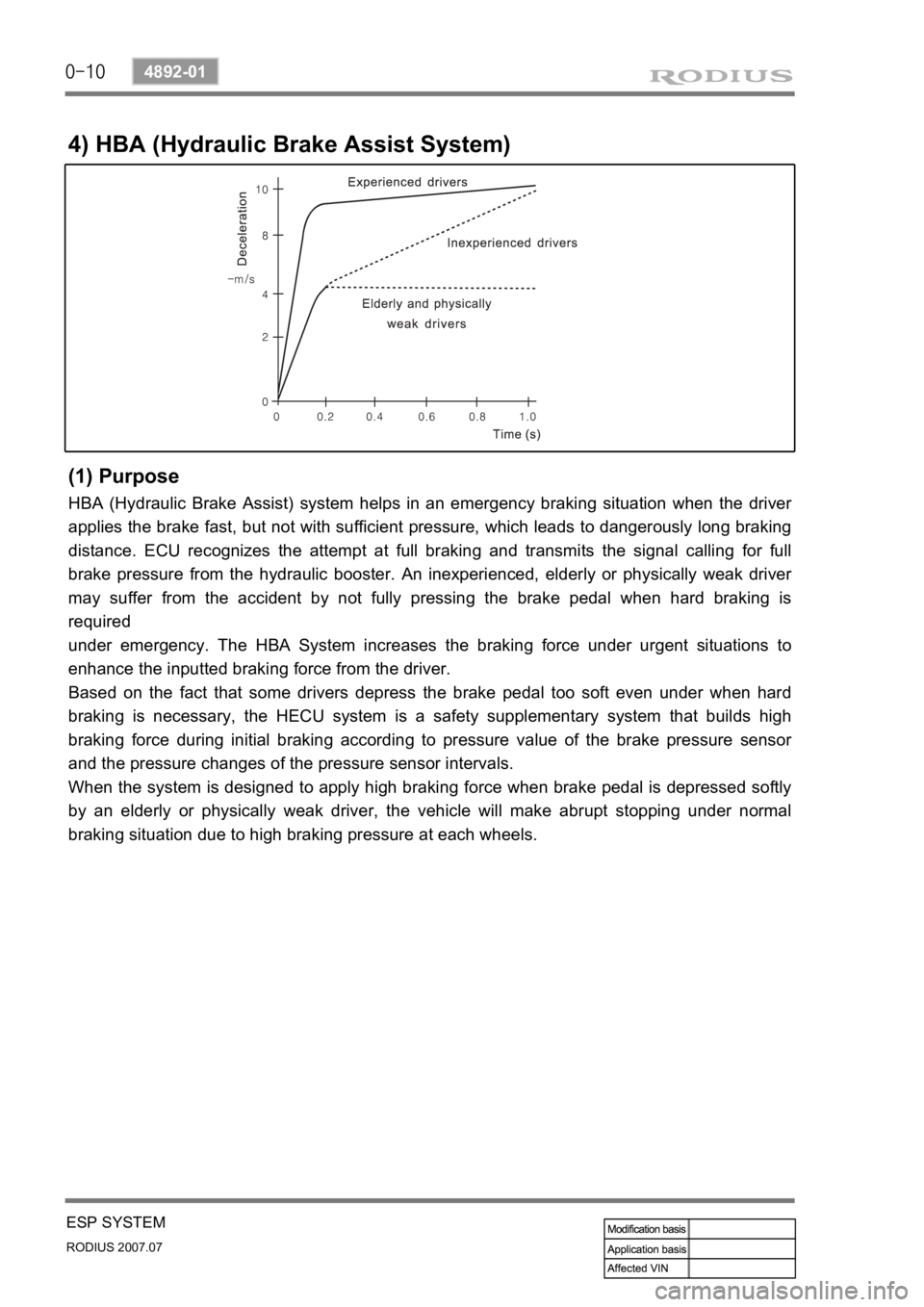
0-10
RODIUS 2007.07
4892-01
ESP SYSTEM
4) HBA (Hydraulic Brake Assist System)
(1) Purpose
HBA (Hydraulic Brake Assist) system helps in an emergency braking situation when the driver
applies the brake fast, but not with sufficient pressure, which leads to dangerously long braking
distance. ECU recognizes the attempt at full braking and transmits the signal calling for full
brake pressure from the hydraulic booster. An inexperienced, elderly or physically weak drive
r
may suffer from the accident by not fully pressing the brake pedal when hard braking is
required
under emergency. The HBA System increases the braking force under urgent situations to
enhance the inputted braking force from the driver.
Based on the fact that some drivers depress the brake pedal too soft even under when hard
braking is necessary, the HECU system is a safety supplementary system that builds high
braking force during initial braking according to pressure value of the brake pressure senso
r
and the pressure changes of the pressure sensor intervals.
When the system is designed to apply high braking force when brake pedal is depressed softly
by an elderly or physically weak driver, the vehicle will make abrupt stopping under normal
braking situation due to high braking pressure at each wheels.