Page 24 of 668
CHAPTER 6
ELECTRICAL
ELECTRICAL COMPONENTS
AND WIRING DIAGRAM ...........................6-1
MAP-CONTROLLED CDI UNIT .................6-2
IGNITION SYSTEM ....................................6-3
THROTTLE POSITION SENSOR
SYSTEM .....................................................6-7
CHAPTER 7
TUNING
ENGINE ......................................................7-1
CHASSIS .................................................7-11
Page 39 of 668
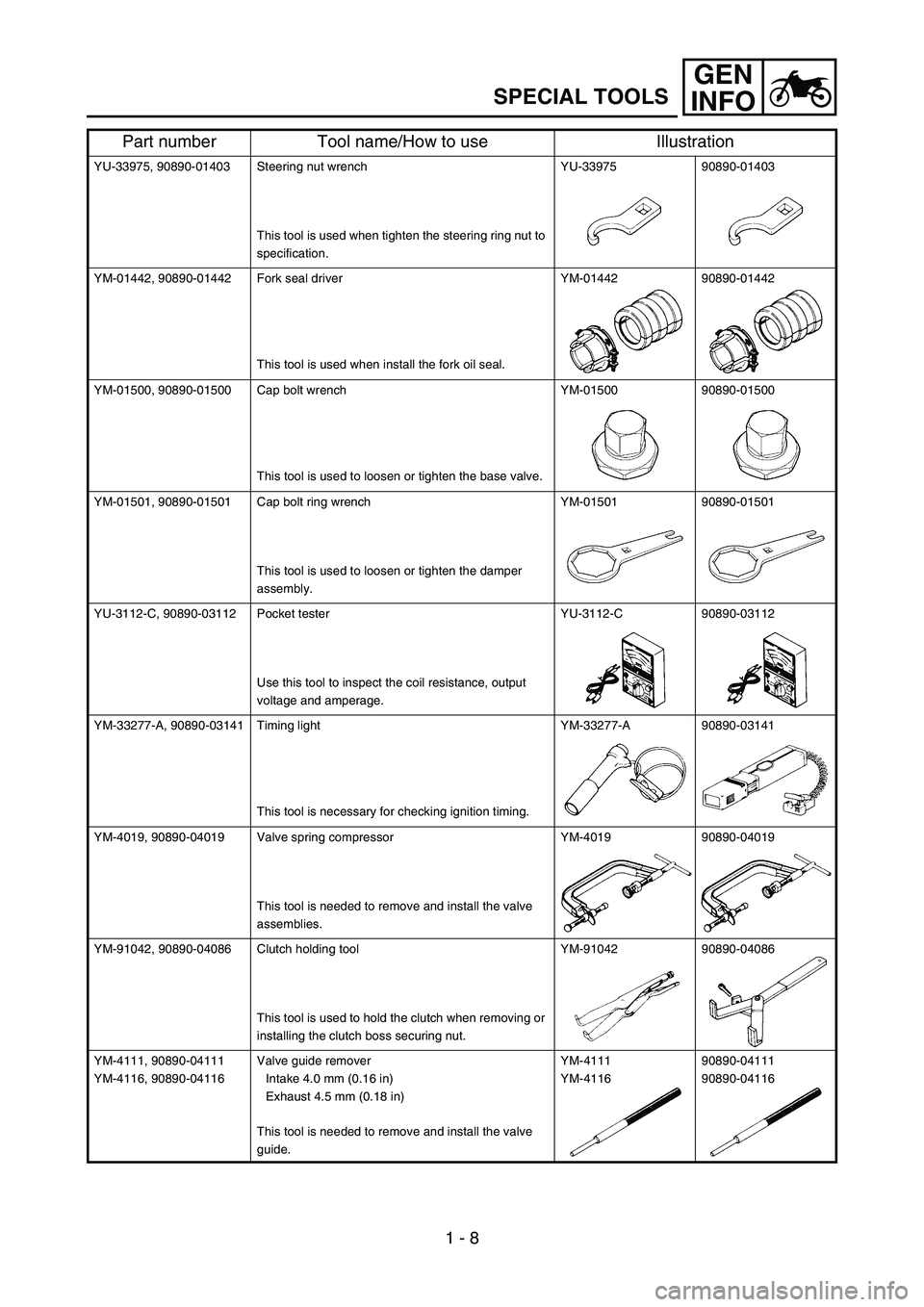
GEN
INFO
1 - 8
SPECIAL TOOLS
YU-33975, 90890-01403 Steering nut wrench
This tool is used when tighten the steering ring nut to
specification.YU-33975 90890-01403
YM-01442, 90890-01442 Fork seal driver
This tool is used when install the fork oil seal.YM-01442 90890-01442
YM-01500, 90890-01500 Cap bolt wrench
This tool is used to loosen or tighten the base valve.YM-01500 90890-01500
YM-01501, 90890-01501 Cap bolt ring wrench
This tool is used to loosen or tighten the damper
assembly.YM-01501 90890-01501
YU-3112-C, 90890-03112 Pocket tester
Use this tool to inspect the coil resistance, output
voltage and amperage.YU-3112-C 90890-03112
YM-33277-A, 90890-03141 Timing light
This tool is necessary for checking ignition timing.YM-33277-A 90890-03141
YM-4019, 90890-04019 Valve spring compressor
This tool is needed to remove and install the valve
assemblies.YM-4019 90890-04019
YM-91042, 90890-04086 Clutch holding tool
This tool is used to hold the clutch when removing or
installing the clutch boss securing nut.YM-91042 90890-04086
YM-4111, 90890-04111
YM-4116, 90890-04116Valve guide remover
Intake 4.0 mm (0.16 in)
Exhaust 4.5 mm (0.18 in)
This tool is needed to remove and install the valve
guide.YM-4111
YM-411690890-04111
90890-04116
Part number Tool name/How to use Illustration
Page 40 of 668
GEN
INFO
1 - 9
SPECIAL TOOLS
YM-4112, 90890-04112
YM-4117, 90890-04117Valve guide installer
Intake 4.0 mm (0.16 in)
Exhaust 4.5 mm (0.18 in)
This tool is needed to install the valve guide.YM-4112
YM-411790890-04112
90890-04117
YM-4113, 90890-04113
YM-4118, 90890-04118Valve guide reamer
Intake 4.0 mm (0.16 in)
Exhaust 4.5 mm (0.18 in)
This tool is needed to rebore the new valve guide.YM-4113
YM-411890890-04113
90890-04118
YM-34487
90890-06754Dynamic spark tester
Ignition checker
This instrument is necessary for checking the ignition
system components.YM-34487 90890-06754
ACC-QUICK-GS-KT
90890-85505Quick gasket
YAMAHA Bond No. 1215
This sealant (Bond) is used for crankcase mating sur-
face, etc.ACC-QUICK-GS-KT 90890-85505
Part number Tool name/How to use Illustration
Page 76 of 668
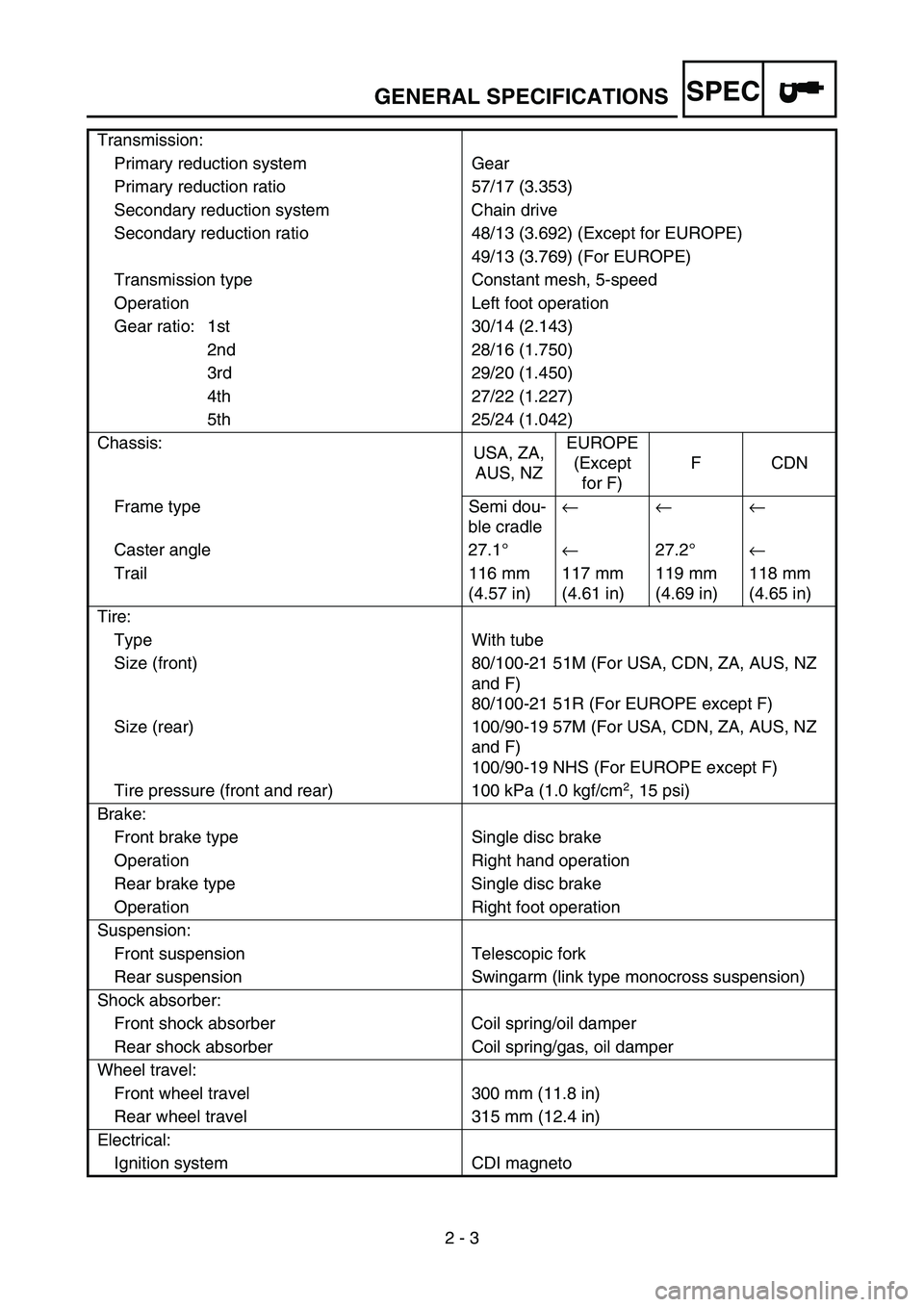
SPEC
2 - 3 Transmission:
Primary reduction system Gear
Primary reduction ratio 57/17 (3.353)
Secondary reduction system Chain drive
Secondary reduction ratio 48/13 (3.692) (Except for EUROPE)
49/13 (3.769) (For EUROPE)
Transmission type Constant mesh, 5-speed
Operation Left foot operation
Gear ratio: 1st 30/14 (2.143)
2nd 28/16 (1.750)
3rd 29/20 (1.450)
4th 27/22 (1.227)
5th 25/24 (1.042)
Chassis:
USA, ZA,
AUS, NZEUROPE
(Except
for F)FCDN
Frame type Semi dou-
ble cradle← ← ←
Caster angle 27.1°← 27.2°←
Trail 116 mm
(4.57 in)117 mm
(4.61 in)119 mm
(4.69 in)118 mm
(4.65 in)
Tire:
Type With tube
Size (front) 80/100-21 51M (For USA, CDN, ZA, AUS, NZ
and F)
80/100-21 51R (For EUROPE except F)
Size (rear) 100/90-19 57M (For USA, CDN, ZA, AUS, NZ
and F)
100/90-19 NHS (For EUROPE except F)
Tire pressure (front and rear) 100 kPa (1.0 kgf/cm
2, 15 psi)
Brake:
Front brake type Single disc brake
Operation Right hand operation
Rear brake type Single disc brake
Operation Right foot operation
Suspension:
Front suspension Telescopic fork
Rear suspension Swingarm (link type monocross suspension)
Shock absorber:
Front shock absorber Coil spring/oil damper
Rear shock absorber Coil spring/gas, oil damper
Wheel travel:
Front wheel travel 300 mm (11.8 in)
Rear wheel travel 315 mm (12.4 in)
Electrical:
Ignition system CDI magneto
GENERAL SPECIFICATIONS
Page 89 of 668
SPEC
2 - 16
EC212300
ELECTRICAL
Item Standard Limit
Ignition system:
Advancer type Electrical ----
CDI:
Magneto-model (stator)/manufac-
turer5XD-00/YAMAHA ----
Charging coil 1 resistance (color) 720 ~ 1,080 Ω at 20 °C (68 °F)
(Green – Brown)----
Charging coil 2 resistance (color) 44 ~ 66 Ω at 20°C (68 °F)
(Black – Pink)----
Pickup coil resistance (color) 248 ~ 372 Ω at 20°C (68 °F)
(White – Red)----
CDI unit-model/manufacturer 5XC-50/YAMAHA (For USA)
5XC-60/YAMAHA (Except for USA)----
----
Ignition coil:
Model/manufacturer 5UL-10/DENSO ----
Minimum spark gap 6 mm (0.24 in) ----
Primary coil resistance 0.08 ~ 0.10 Ω at 20 °C (68 °F) ----
Secondary coil resistance 4.6 ~ 6.8 kΩ at 20 °C (68 °F) ----
Part to be tightened Thread size Q’tyTightening torque
Nm m·kg ft·lb
Stator M6 × 1.0 3 10 1.0 7.2
Rotor M12 × 1.25 1 56 5.6 40
Neutral switch M5 × 0.8 2 4 0.4 2.9
MAINTENANCE SPECIFICATIONS
Page 142 of 668
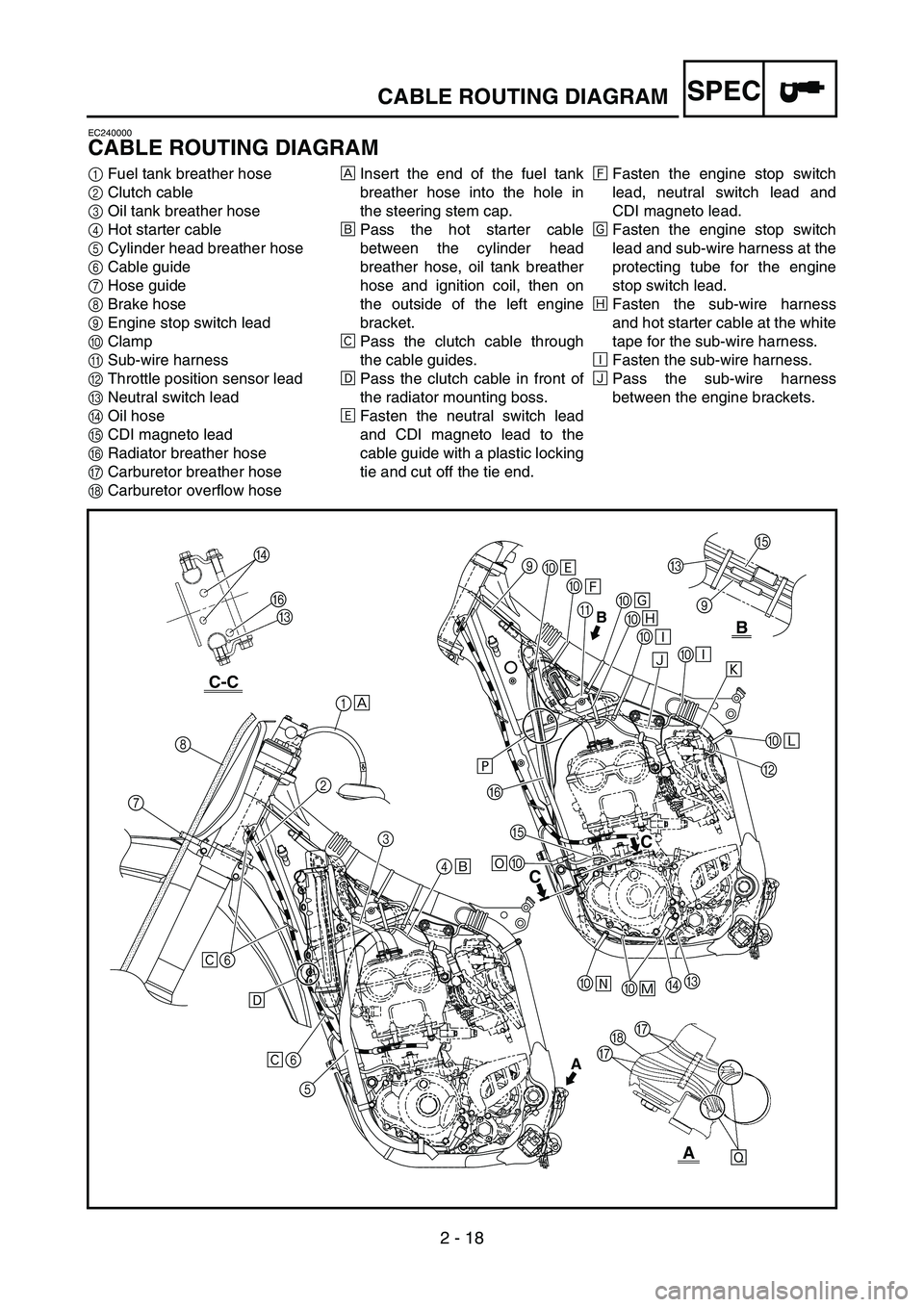
2 - 18
SPECCABLE ROUTING DIAGRAM
EC240000
CABLE ROUTING DIAGRAM
1Fuel tank breather hose
2Clutch cable
3Oil tank breather hose
4Hot starter cable
5Cylinder head breather hose
6Cable guide
7Hose guide
8Brake hose
9Engine stop switch lead
0Clamp
ASub-wire harness
BThrottle position sensor lead
CNeutral switch lead
DOil hose
ECDI magneto lead
FRadiator breather hose
GCarburetor breather hose
HCarburetor overflow hoseÈInsert the end of the fuel tank
breather hose into the hole in
the steering stem cap.
ÉPass the hot starter cable
between the cylinder head
breather hose, oil tank breather
hose and ignition coil, then on
the outside of the left engine
bracket.
ÊPass the clutch cable through
the cable guides.
ËPass the clutch cable in front of
the radiator mounting boss.
ÌFasten the neutral switch lead
and CDI magneto lead to the
cable guide with a plastic locking
tie and cut off the tie end.ÍFasten the engine stop switch
lead, neutral switch lead and
CDI magneto lead.
ÎFasten the engine stop switch
lead and sub-wire harness at the
protecting tube for the engine
stop switch lead.
ÏFasten the sub-wire harness
and hot starter cable at the white
tape for the sub-wire harness.
ÐFasten the sub-wire harness.
ÑPass the sub-wire harness
between the engine brackets.
B
E
C
9
B
C
C
9
0
0
A
0
0
0
0
B 0 Ì
Í
Î
Ï
Ð
Ð
Ñ
Ò
Ó
C
D
0 0 0E F
Ô Õ Ö ×
1
2
3
4
5 6 6 8
7
Ê
Ê ËÈ
É
AGG
H
Ø
D
F
C
Page 146 of 668
2 - 20
SPEC
1CDI unit
2Hot starter cable
3Throttle cable (pull)
4Throttle cable (return)
5Cable guide
6Ignition coil
7Radiator hose 2
8Radiator breather hose
9Radiator hose 4
0CDI unit bracket
ACDI unit bandÈPass the hot starter cable and
throttle cables through the
cable guides.
ÉPass the hot starter cable and
throttle cables between the
radiator and frame, then over
the radiator mounting boss.
ÊPass the throttle cables on the
outside of the ignition coil.
ËPass the radiator breather
hose in front of the radiator
hose 2, on the left of the chas-
sis, and then between the
frame and radiator hose 4.
ÌInsert the CDI unit band over
the CDI unit bracket as far as
possible.ÍFirst install the CDI unit and
CDI unit band to the CDI unit
bracket, then the CDI unit
bracket to the frame.
A10
ÍÌ
B7
8
9Ë
A
2
3
4
5
È 1
É
Ê
6
A
B
CABLE ROUTING DIAGRAM
Page 164 of 668

3 - 4
INSP
ADJ
PRE-OPERATION INSPECTION AND MAINTENANCE
EC320000
PRE-OPERATION INSPECTION AND MAINTENANCE
Before riding for break-in operation, practice or a race, make sure the machine is in good operating
condition.
Before using this machine, check the following points.
GENERAL INSPECTION AND MAINTENANCE
Item Routine Page
CoolantCheck that coolant is filled up to the radiator cap.
Check the cooling system for leakage.P.3-5 ~ 9
FuelCheck that a fresh gasoline is filled in the fuel tank. Check the
fuel line for leakage.P.1-13
Engine oilCheck that the oil level is correct. Check the crankcase and
frame oil line for leakage.P.3-13 ~ 17
Gear shifter and clutchCheck that gears can be shifted correctly in order and that the
clutch operates smoothly.P.3-9
Throttle grip/HousingCheck that the throttle grip operation and free play are correctly
adjusted. Lubricate the throttle grip and housing, if necessary.P.3-10
Brakes Check the play of front brake and effect of front and rear brake. P.3-24 ~ 30
Drive chainCheck drive chain slack and alignment. Check that the drive
chain is lubricated properly.P.3-31 ~ 33
WheelsCheck for excessive wear and tire pressure. Check for loose
spokes and have no excessive play.P.3-41 ~ 42
SteeringCheck that the handlebar can be turned smoothly and have no
excessive play.P.3-42 ~ 44
Front forks and rear shock
absorberCheck that they operate smoothly and there is no oil leakage. P.3-33 ~ 40
Cables (wires)Check that the clutch and throttle cables move smoothly. Check
that they are not caught when the handlebars are turned or
when the front forks travel up and down.—
Exhaust pipeCheck that the exhaust pipe is tightly mounted and has no
cracks.P.4-3 ~ 4
Rear wheel sprocket Check that the rear wheel sprocket tightening bolt is not loose. P.3-31
Lubrication Check for smooth operation. Lubricate if necessary. P.3-45
Bolts and nuts Check the chassis and engine for loose bolts and nuts. P.1-18
Lead connectorsCheck that the CDI magneto, CDI unit, and ignition coil are con-
nected tightly.P.1-6
SettingsIs the machine set suitably for the condition of the racing course
and weather or by taking into account the results of test runs
before racing? Are inspection and maintenance completely
done?P.7-1 ~ 21