Page 262 of 801
YH4
GRAND
VITARA
1. Oil filler / level plug
2. Front drain plug
1. Circlip
2. Washer
1. Drive shaft flange
bolts and nuts
1. Oil seal
FRONT DRIVE SHAFT / SHAFT BEARING, OIL SEAL 4A2-3
ON-VEHICLE SERVICE
DRIVE SHAFT
REMOVAL (LEFT SIDE)
1) Hoist vehicle and remove wheel.
2) Remove axle shaft drive flange.
3) Remove drive shaft circlip and front spindle thrust washer.
4) Remove drive shaft flange bolts and nuts.
5) Remove drive shaft assembly to differential side as shown in left
figure.
CAUTION:
To prevent breakage of boots (wheel side and differential
side), be careful not to bring them into contact with other
parts when removing drive shaft assembly.
6) Remove drive shaft thrust washer (vehicle with G16 or J20 en-
gine) from drive shaft and remove drive shaft oil seal as shown
in figure.
CAUTION:
Be careful not to cause damage to drive shaft joint.
Page 263 of 801
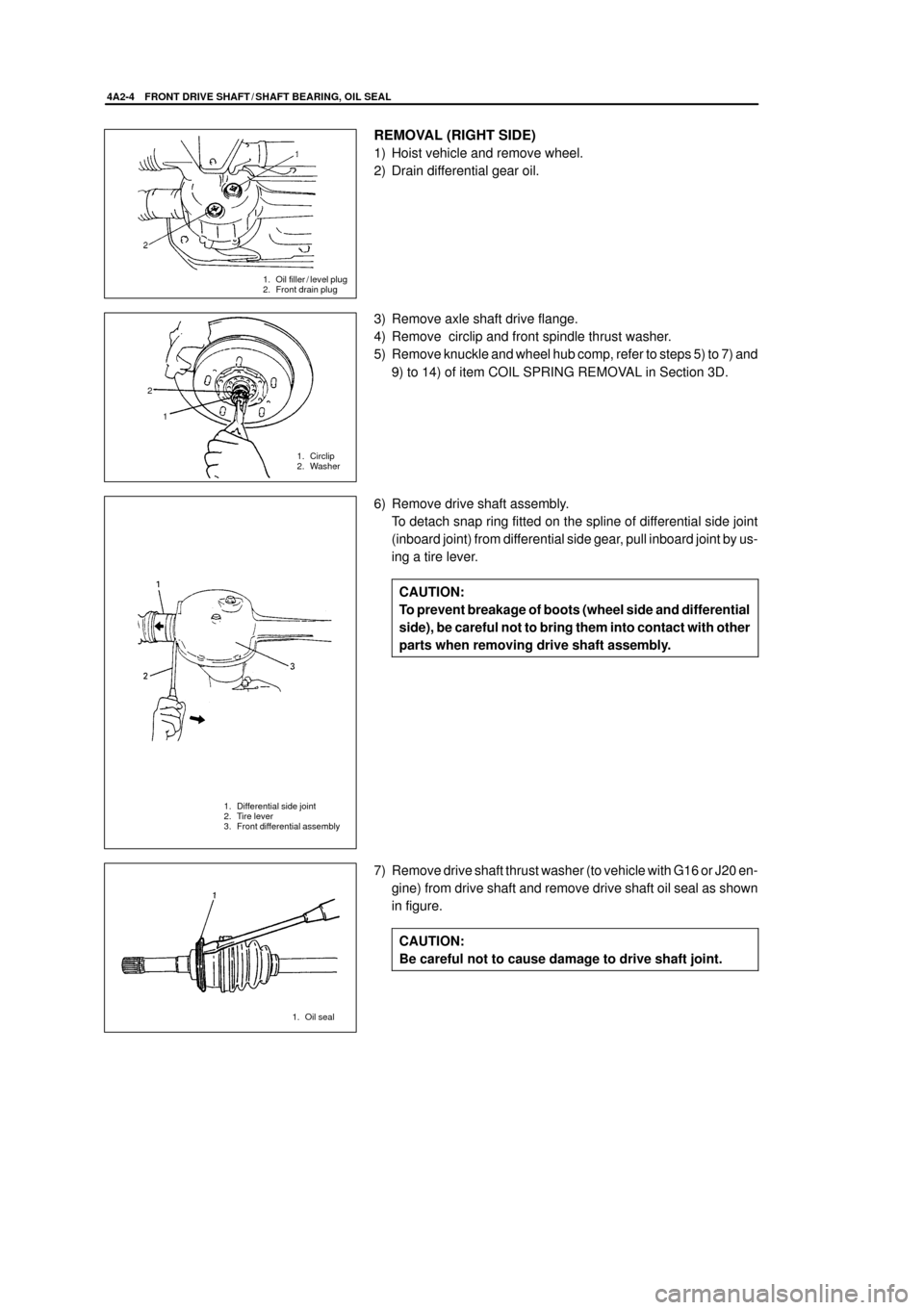
YH4
GRAND
VITARA
1. Oil filler / level plug
2. Front drain plug
1. Circlip
2. Washer
1. Differential side joint
2. Tire lever
3. Front differential assembly
1. Oil seal 2
1
4A2-4 FRONT DRIVE SHAFT / SHAFT BEARING, OIL SEAL
REMOVAL (RIGHT SIDE)
1) Hoist vehicle and remove wheel.
2) Drain differential gear oil.
3) Remove axle shaft drive flange.
4) Remove circlip and front spindle thrust washer.
5) Remove knuckle and wheel hub comp, refer to steps 5) to 7) and
9) to 14) of item COIL SPRING REMOVAL in Section 3D.
6) Remove drive shaft assembly.
To detach snap ring fitted on the spline of differential side joint
(inboard joint) from differential side gear, pull inboard joint by us-
ing a tire lever.
CAUTION:
To prevent breakage of boots (wheel side and differential
side), be careful not to bring them into contact with other
parts when removing drive shaft assembly.
7) Remove drive shaft thrust washer (to vehicle with G16 or J20 en-
gine) from drive shaft and remove drive shaft oil seal as shown
in figure.
CAUTION:
Be careful not to cause damage to drive shaft joint.
Page 267 of 801
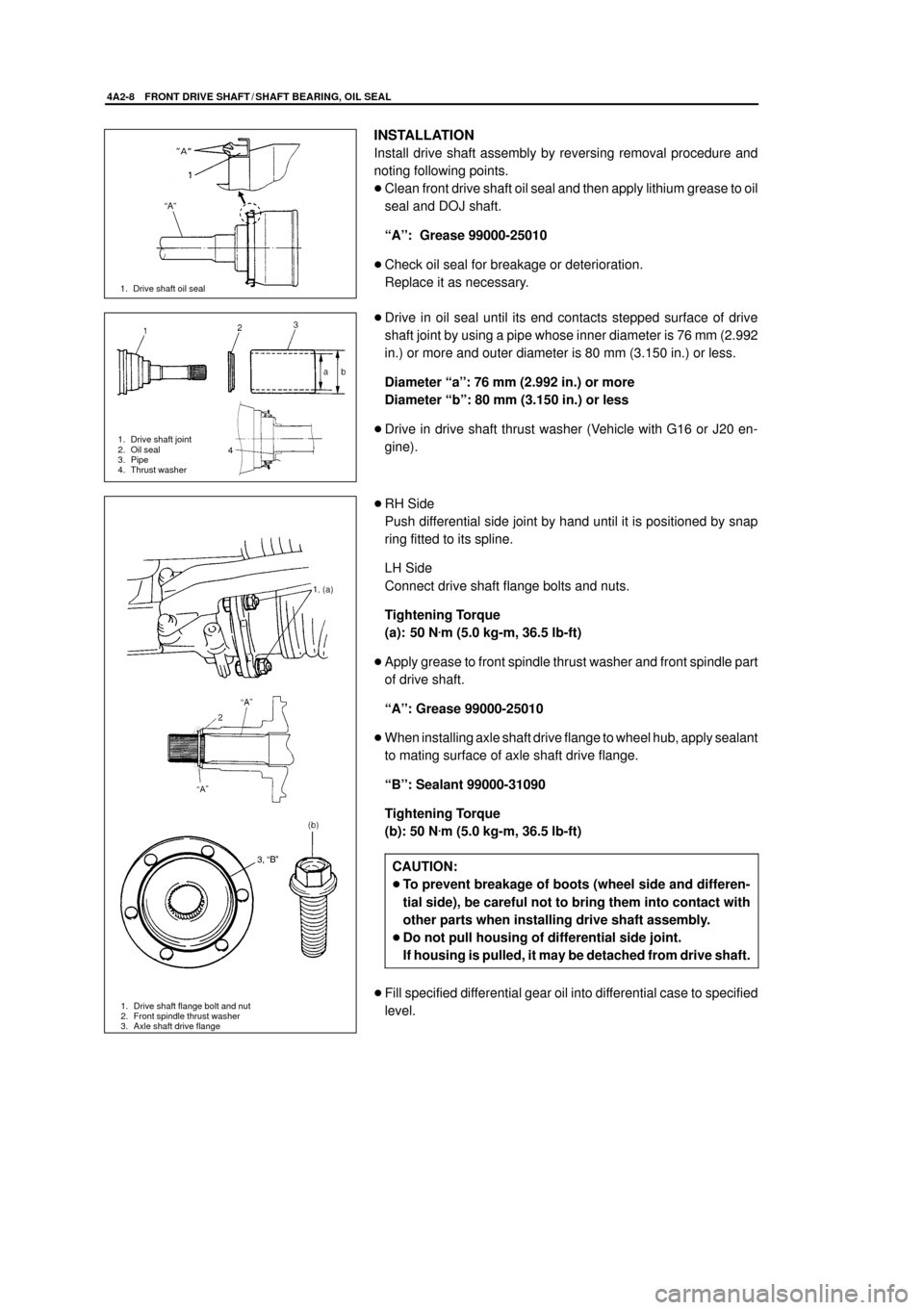
YH4
GRAND
VITARA
1. Drive shaft oil seal
1. Drive shaft flange bolt and nut
2. Front spindle thrust washer
3. Axle shaft drive flange
ªAº
1. Drive shaft joint
2. Oil seal
3. Pipe
4. Thrust washer4
4A2-8 FRONT DRIVE SHAFT / SHAFT BEARING, OIL SEAL
INSTALLATION
Install drive shaft assembly by reversing removal procedure and
noting following points.
Clean front drive shaft oil seal and then apply lithium grease to oil
seal and DOJ shaft.
ªAº: Grease 99000-25010
Check oil seal for breakage or deterioration.
Replace it as necessary.
Drive in oil seal until its end contacts stepped surface of drive
shaft joint by using a pipe whose inner diameter is 76 mm (2.992
in.) or more and outer diameter is 80 mm (3.150 in.) or less.
Diameter ªaº: 76 mm (2.992 in.) or more
Diameter ªbº: 80 mm (3.150 in.) or less
Drive in drive shaft thrust washer (Vehicle with G16 or J20 en-
gine).
RH Side
Push differential side joint by hand until it is positioned by snap
ring fitted to its spline.
LH Side
Connect drive shaft flange bolts and nuts.
Tightening Torque
(a): 50 N
.m (5.0 kg-m, 36.5 lb-ft)
Apply grease to front spindle thrust washer and front spindle part
of drive shaft.
ªAº: Grease 99000-25010
When installing axle shaft drive flange to wheel hub, apply sealant
to mating surface of axle shaft drive flange.
ªBº: Sealant 99000-31090
Tightening Torque
(b): 50 N
.m (5.0 kg-m, 36.5 lb-ft)
CAUTION:
To prevent breakage of boots (wheel side and differen-
tial side), be careful not to bring them into contact with
other parts when installing drive shaft assembly.
Do not pull housing of differential side joint.
If housing is pulled, it may be detached from drive shaft.
Fill specified differential gear oil into differential case to specified
level.
Page 270 of 801
YH4
GRAND
VITARA
FRONT DRIVE SHAFT / SHAFT BEARING, OIL SEAL 4A2-11
09913-75520
Bearing installer09924-74510
Installer attachment09930-30102
Sliding shaft09941-64510
Bearing remover
09951-16090
Oil seal installer
TIGHTENING TORQUE SPECIFICATIONS
FasteningpartsTightening torqueFastening artsN.mkg-mlb-ft
Drive shaft flange nut (Dif. side)505.036.5
Oil level plug232.317.0
Drain plug232.317.0
Axle shaft drive flange bolt484.835.0
NOTE:
Refer to standard tightening torque specifications, if no description or specification is provided.
REQUIRED SERVICE MATERIALS
MATERIALRECOMMENDED
SUZUKI PRODUCTUSE
Joint grease
(Molybdenum grease)SUZUKI SUPER GREASE H
(99000-25120)Drive axle joint
Lithium greaseSUZUKI SUPER GREASE A
(99000-25010)Drive shaft oil seal
Wheel spindle part of differential side
drive shaft (RH)
SealantSEALING COMPOUND 366E
(99000-31090)Axle shaft drive flange
SPECIAL TOOLS
Page 273 of 801
YH4
GRAND
VITARA
1. Match mark
PROPELLER SHAFTS 4B-3
ON-VEHICLE SERVICE
PROPELLER SHAFT
REMOVAL
1) Hoist vehicle.
2) Drain transfer oil only when servicing front propeller shaft.
3) Before removing propeller shaft, give match marks on joint
flange and propeller shaft as shown.
4) Remove propeller shaft.
DISASSEMBLY
1) Using special tool(A), remove 2 circlips.
Special Tool
(A): 09900-06108
2) Using special tool(B), push spider bearing race out 3 ± 4 mm
(0.12 ± 0.16 in.) from shaft yoke race.
NOTE:
Before pushing it out, apply penetrate lubricant between
bearing race and yoke race.
Special Tool
(B): 09926-48010
Length ªaº: 3 ± 4 mm (0.12 ± 0.16 in.)
3) Tapping yoke with a hammer, completely remove bearing race.
4) Take out bearing race on the other side in the same way as in
2) and 3).
Page 275 of 801
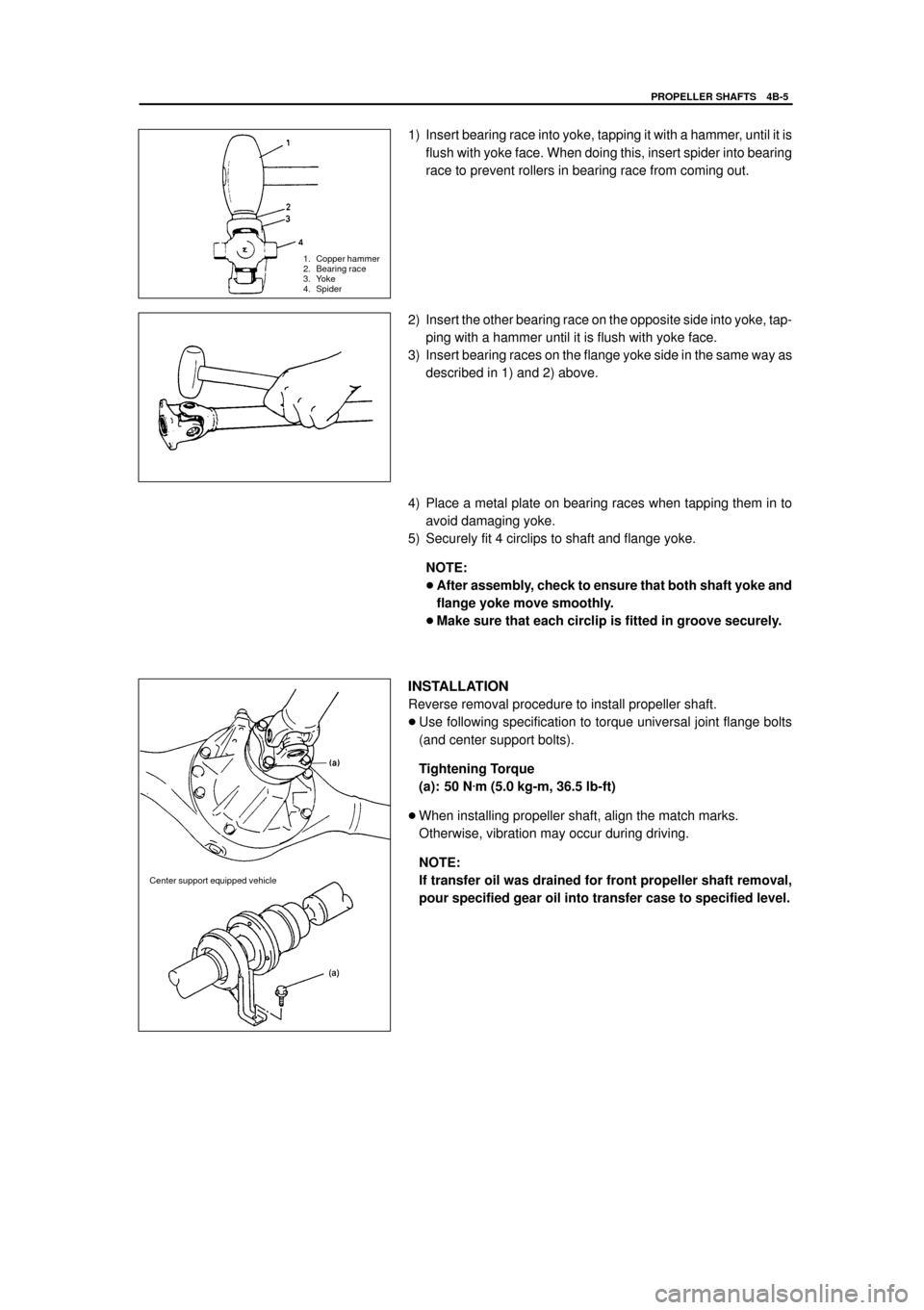
YH4
GRAND
VITARA
1. Copper hammer
2. Bearing race
3. Yoke
4. Spider
Center support equipped vehicle
PROPELLER SHAFTS 4B-5
1) Insert bearing race into yoke, tapping it with a hammer, until it is
flush with yoke face. When doing this, insert spider into bearing
race to prevent rollers in bearing race from coming out.
2) Insert the other bearing race on the opposite side into yoke, tap-
ping with a hammer until it is flush with yoke face.
3) Insert bearing races on the flange yoke side in the same way as
described in 1) and 2) above.
4) Place a metal plate on bearing races when tapping them in to
avoid damaging yoke.
5) Securely fit 4 circlips to shaft and flange yoke.
NOTE:
After assembly, check to ensure that both shaft yoke and
flange yoke move smoothly.
Make sure that each circlip is fitted in groove securely.
INSTALLATION
Reverse removal procedure to install propeller shaft.
Use following specification to torque universal joint flange bolts
(and center support bolts).
Tightening Torque
(a): 50 N
.m (5.0 kg-m, 36.5 lb-ft)
When installing propeller shaft, align the match marks.
Otherwise, vibration may occur during driving.
NOTE:
If transfer oil was drained for front propeller shaft removal,
pour specified gear oil into transfer case to specified level.
Page 286 of 801
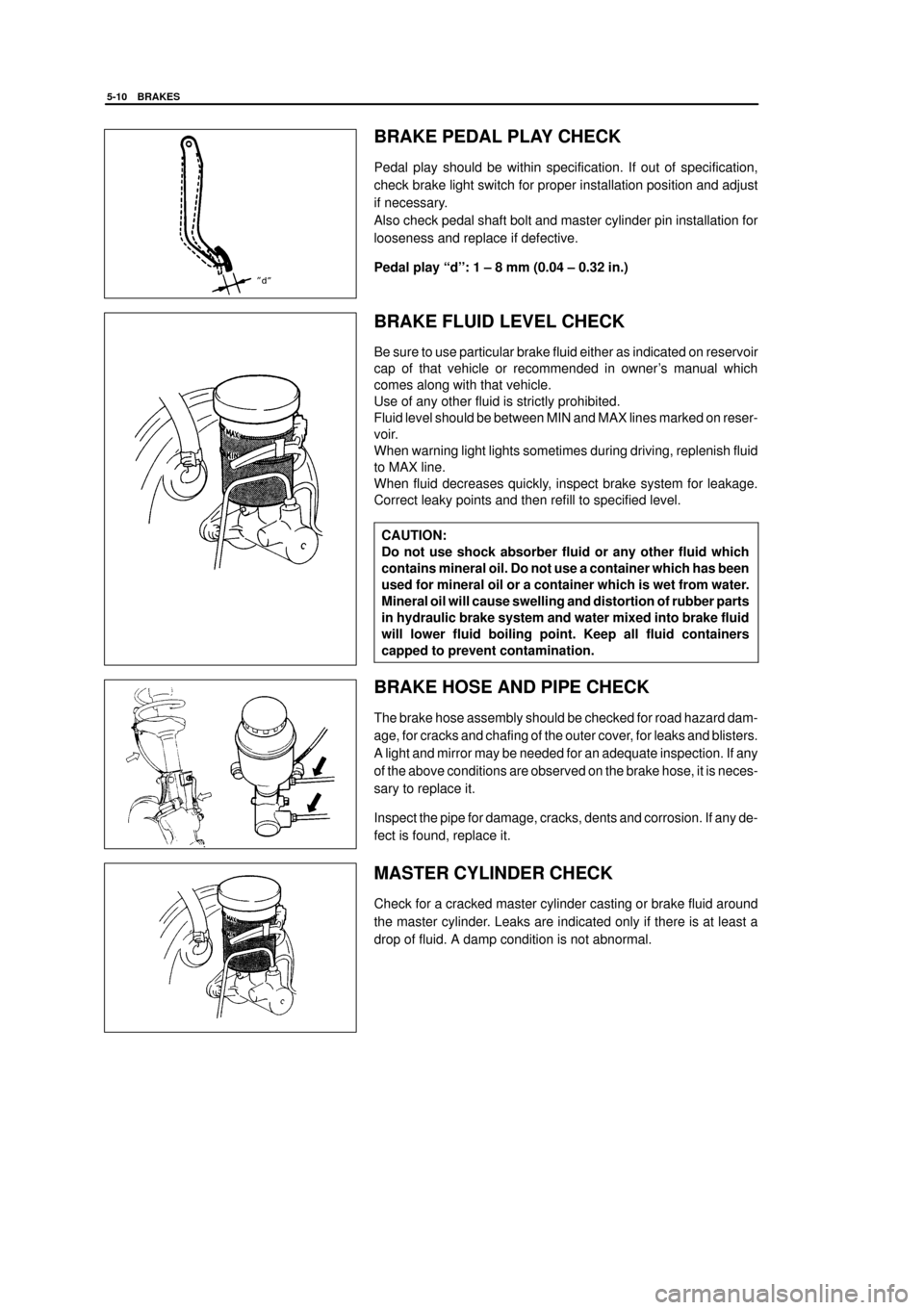
YH4
GRAND
VITARA
5-10 BRAKES
BRAKE PEDAL PLAY CHECK
Pedal play should be within specification. If out of specification,
check brake light switch for proper installation position and adjust
if necessary.
Also check pedal shaft bolt and master cylinder pin installation for
looseness and replace if defective.
Pedal play ªdº: 1 ± 8 mm (0.04 ± 0.32 in.)
BRAKE FLUID LEVEL CHECK
Be sure to use particular brake fluid either as indicated on reservoir
cap of that vehicle or recommended in owner's manual which
comes along with that vehicle.
Use of any other fluid is strictly prohibited.
Fluid level should be between MIN and MAX lines marked on reser-
voir.
When warning light lights sometimes during driving, replenish fluid
to MAX line.
When fluid decreases quickly, inspect brake system for leakage.
Correct leaky points and then refill to specified level.
CAUTION:
Do not use shock absorber fluid or any other fluid which
contains mineral oil. Do not use a container which has been
used for mineral oil or a container which is wet from water.
Mineral oil will cause swelling and distortion of rubber parts
in hydraulic brake system and water mixed into brake fluid
will lower fluid boiling point. Keep all fluid containers
capped to prevent contamination.
BRAKE HOSE AND PIPE CHECK
The brake hose assembly should be checked for road hazard dam-
age, for cracks and chafing of the outer cover, for leaks and blisters.
A light and mirror may be needed for an adequate inspection. If any
of the above conditions are observed on the brake hose, it is neces-
sary to replace it.
Inspect the pipe for damage, cracks, dents and corrosion. If any de-
fect is found, replace it.
MASTER CYLINDER CHECK
Check for a cracked master cylinder casting or brake fluid around
the master cylinder. Leaks are indicated only if there is at least a
drop of fluid. A damp condition is not abnormal.
Page 297 of 801
![SUZUKI GRAND VITARA 2004 2.G Service Workshop Manual YH4
GRAND
VITARA
1. LSPV
2. LSPV lever
3. Spring
4. LSPV stay
5. Brake flare nut
[A]: Type A
[B]: Type B
1. Plunger
2. Lip seal
3. LSPV lever
4. Sensor spring
5. From master cylinder
primary chamber
( SUZUKI GRAND VITARA 2004 2.G Service Workshop Manual YH4
GRAND
VITARA
1. LSPV
2. LSPV lever
3. Spring
4. LSPV stay
5. Brake flare nut
[A]: Type A
[B]: Type B
1. Plunger
2. Lip seal
3. LSPV lever
4. Sensor spring
5. From master cylinder
primary chamber
(](/manual-img/20/7582/w960_7582-296.png)
YH4
GRAND
VITARA
1. LSPV
2. LSPV lever
3. Spring
4. LSPV stay
5. Brake flare nut
[A]: Type A
[B]: Type B
1. Plunger
2. Lip seal
3. LSPV lever
4. Sensor spring
5. From master cylinder
primary chamber
(Rear wheel brake)
6. From master cylinder
secondary chamber
(Front wheel brake)
7. To rear wheel brake
8. Pin
9. Bolt hole
[A] [B]
44
BRAKES PIPE / HOSE / MASTER CYLINDER 5A-3
LSPV (Load Sensing Proportioning Valve) ASSEMBLY (if equipped)
As shown in figure below, LSPV is included within the brake circuit which connects the master cylinder and the rear
wheel brake. It controls the hydraulic pressure applied to the rear wheel brake according to the loaded state of the
vehicle (or weight of the load), whereby preventing the rear wheels from getting locked prematurely.
Also, it releases the above described control over the hydraulic pressure applied to the rear wheel brake, should
any failure occur in the hydraulic circuit of the front wheel brake so that the hydraulic pressure produced in the mas-
ter cylinder is applied to the rear wheel brake directly to operate it.
CONSTITUTION
The LSPV components are grouped into three sections as follows.
ªAº: Sensor section
The main parts in this section are a lever and a spring which senses variation in the vehicle height as affected
by the loaded condition and converts it into the load.
ªBº: Hydraulic pressure control section
Included in this section are a stepped plunger and valve mechanism to execute proportional control.
ªCº: Fail-safe section
The main parts in this section are a chamber which draws in the hydraulic pressure from the front wheel brake
system and a fail-safe piston which releases the valve mechanism in the control section connected to the rear
wheel brake, should any failure occur in the front wheel brake system.