Page 312 of 801
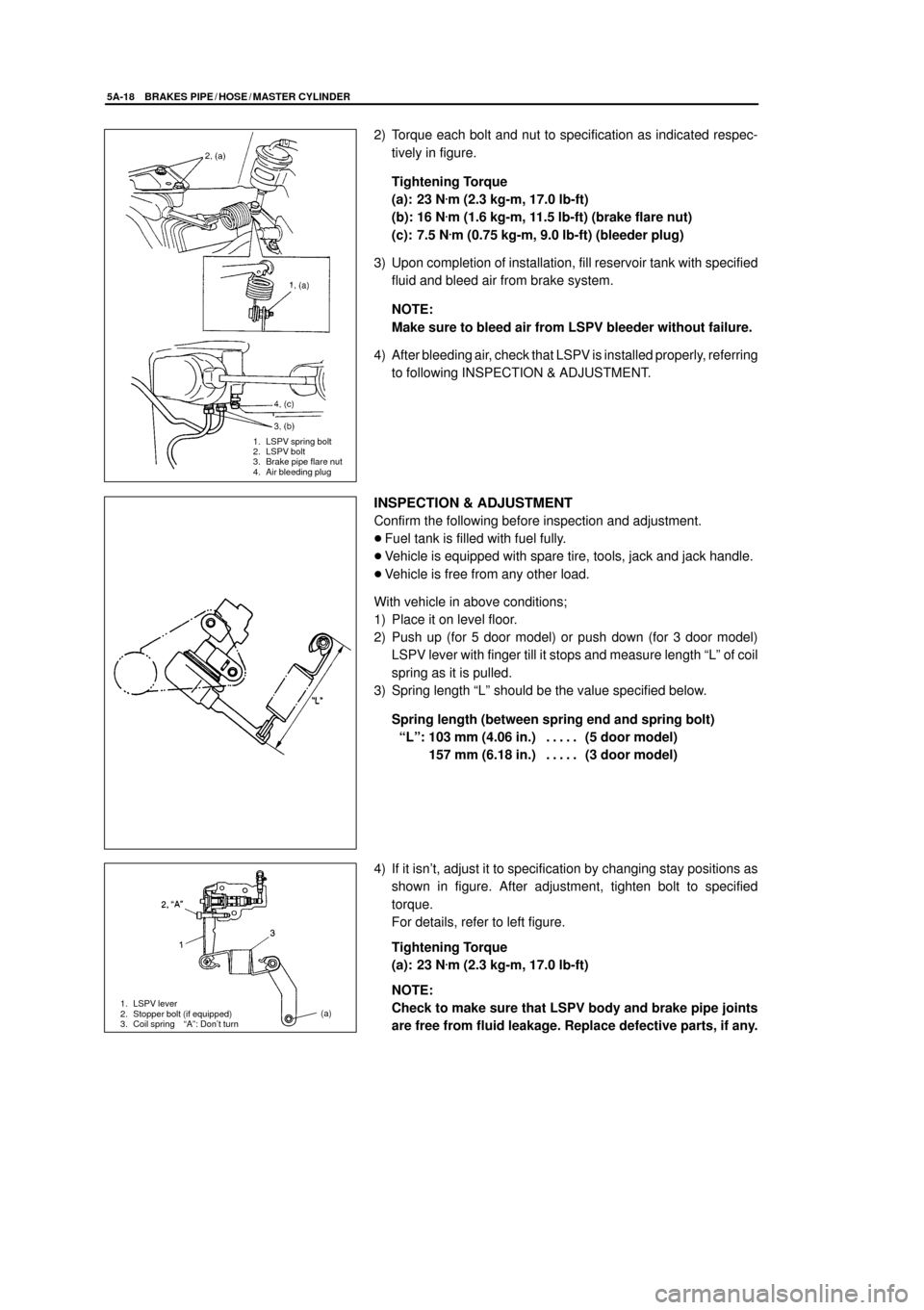
YH4
GRAND
VITARA
5A-18 BRAKES PIPE / HOSE / MASTER CYLINDER
1. LSPV spring bolt
2. LSPV bolt
3. Brake pipe flare nut
4. Air bleeding plug
1. LSPV lever
2. Stopper bolt (if equipped)
3. Coil spring ªAº: Don't turn(a)
2) Torque each bolt and nut to specification as indicated respec-
tively in figure.
Tightening Torque
(a): 23 N
.m (2.3 kg-m, 17.0 lb-ft)
(b): 16 N
.m (1.6 kg-m, 11.5 lb-ft) (brake flare nut)
(c): 7.5 N
.m (0.75 kg-m, 9.0 lb-ft) (bleeder plug)
3) Upon completion of installation, fill reservoir tank with specified
fluid and bleed air from brake system.
NOTE:
Make sure to bleed air from LSPV bleeder without failure.
4) After bleeding air, check that LSPV is installed properly, referring
to following INSPECTION & ADJUSTMENT.
INSPECTION & ADJUSTMENT
Confirm the following before inspection and adjustment.
Fuel tank is filled with fuel fully.
Vehicle is equipped with spare tire, tools, jack and jack handle.
Vehicle is free from any other load.
With vehicle in above conditions;
1) Place it on level floor.
2) Push up (for 5 door model) or push down (for 3 door model)
LSPV lever with finger till it stops and measure length ªLº of coil
spring as it is pulled.
3) Spring length ªLº should be the value specified below.
Spring length (between spring end and spring bolt)
ªLº: 103 mm (4.06 in.) (5 door model). . . . .
ªLº: 157 mm (6.18 in.) (3 door model). . . . .
4) If it isn't, adjust it to specification by changing stay positions as
shown in figure. After adjustment, tighten bolt to specified
torque.
For details, refer to left figure.
Tightening Torque
(a): 23 N
.m (2.3 kg-m, 17.0 lb-ft)
NOTE:
Check to make sure that LSPV body and brake pipe joints
are free from fluid leakage. Replace defective parts, if any.
Page 443 of 801
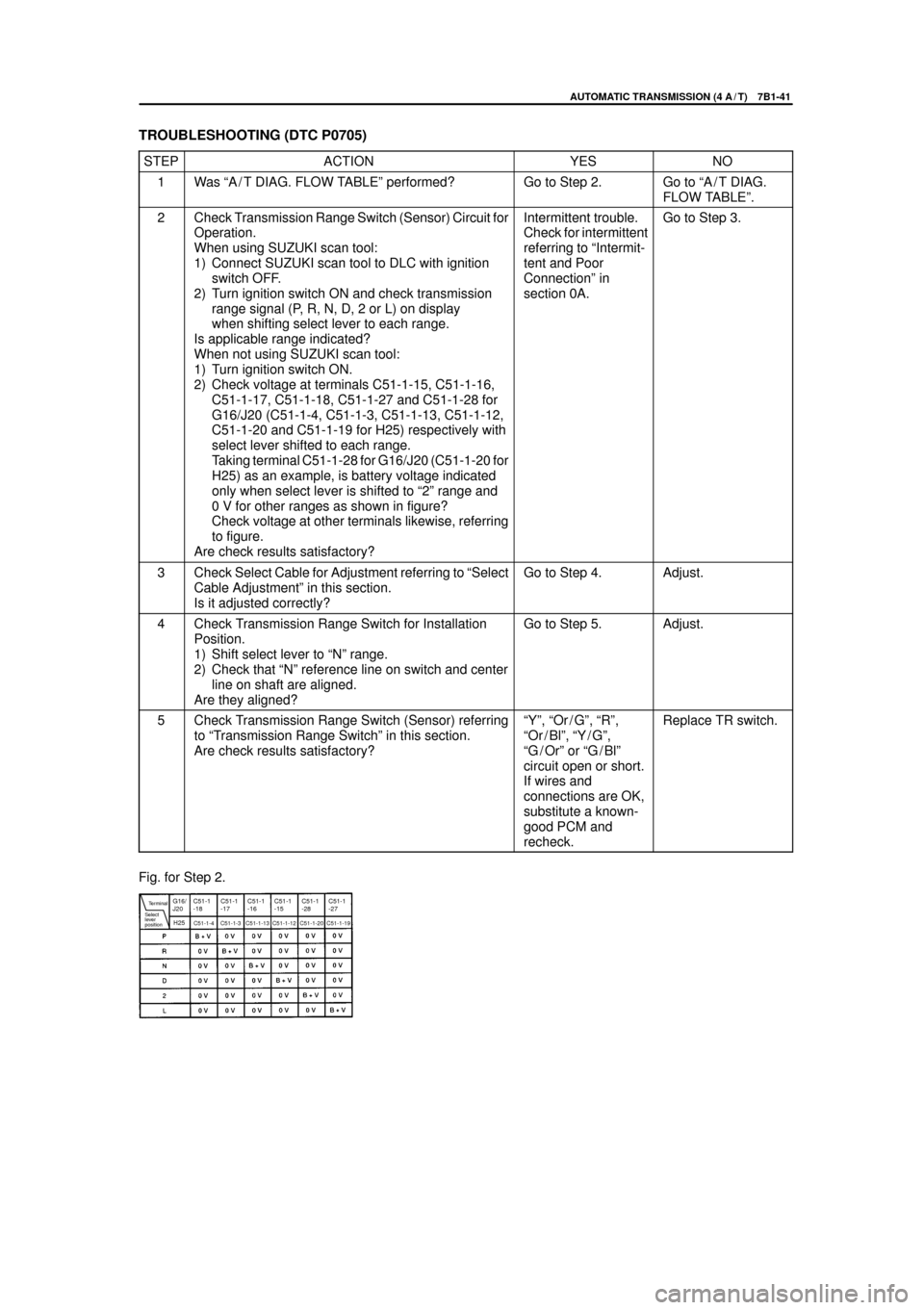
YH4
GRAND
VITARA
AUTOMATIC TRANSMISSION (4 A / T) 7B1-41
C51-1
-18C51-1
-17C51-1
-16C51-1
-15C51-1
-28C51-1
-27 G16/
J20
H25
C51-1-4 C51-1-3 C51-1-13 C51-1-12 C51-1-20 C51-1-19
Terminal
Select
lever
position
TROUBLESHOOTING (DTC P0705)
STEPACTIONYESNO
1Was ªA / T DIAG. FLOW TABLEº performed?Go to Step 2.Go to ªA / T DIAG.
FLOW TABLEº.
2Check Transmission Range Switch (Sensor) Circuit for
Operation.
When using SUZUKI scan tool:
1) Connect SUZUKI scan tool to DLC with ignition
switch OFF.
2) Turn ignition switch ON and check transmission
range signal (P, R, N, D, 2 or L) on display
when shifting select lever to each range.
Is applicable range indicated?
When not using SUZUKI scan tool:
1) Turn ignition switch ON.
2) Check voltage at terminals C51-1-15, C51-1-16,
C51-1-17, C51-1-18, C51-1-27 and C51-1-28 for
G16/J20 (C51-1-4, C51-1-3, C51-1-13, C51-1-12,
C51-1-20 and C51-1-19 for H25) respectively with
select lever shifted to each range.
Taking terminal C51-1-28 for G16/J20 (C51-1-20 for
H25) as an example, is battery voltage indicated
only when select lever is shifted to ª2º range and
0 V for other ranges as shown in figure?
Check voltage at other terminals likewise, referring
to figure.
Are check results satisfactory?Intermittent trouble.
Check for intermittent
referring to ªIntermit-
tent and Poor
Connectionº in
section 0A.Go to Step 3.
3Check Select Cable for Adjustment referring to ªSelect
Cable Adjustmentº in this section.
Is it adjusted correctly?Go to Step 4.Adjust.
4Check Transmission Range Switch for Installation
Position.
1) Shift select lever to ªNº range.
2) Check that ªNº reference line on switch and center
line on shaft are aligned.
Are they aligned?Go to Step 5.Adjust.
5Check Transmission Range Switch (Sensor) referring
to ªTransmission Range Switchº in this section.
Are check results satisfactory?ªYº, ªOr / Gº, ªRº,
ªOr / Blº, ªY / Gº,
ªG / Orº or ªG / Blº
circuit open or short.
If wires and
connections are OK,
substitute a known-
good PCM and
recheck.Replace TR switch.
Fig. for Step 2.
Page 538 of 801
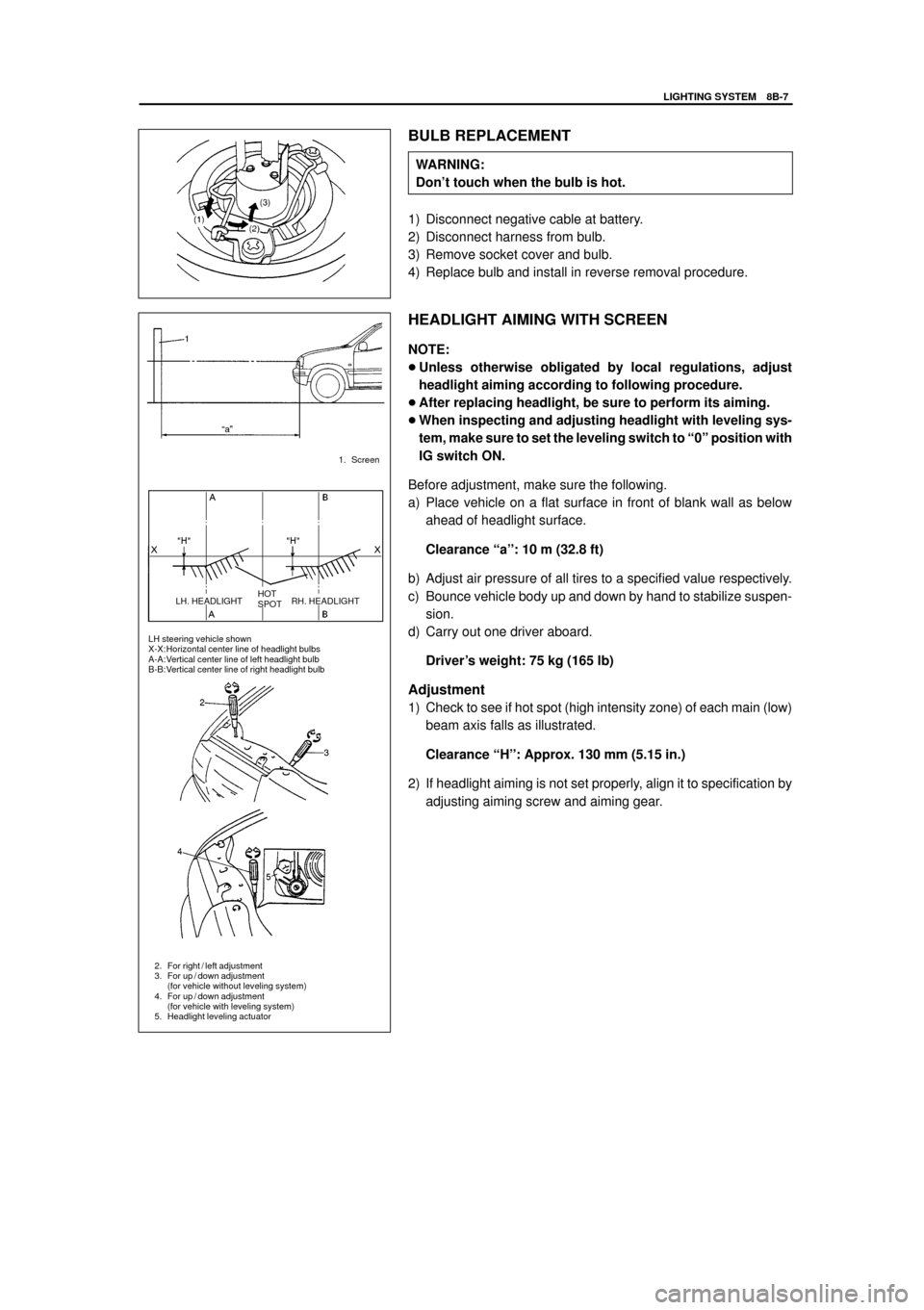
YH4
GRAND
VITARA
LH steering vehicle shown
X-X:Horizontal center line of headlight bulbs
A-A:Vertical center line of left headlight bulb
B-B:Vertical center line of right headlight bulb1. Screen
2. For right / left adjustment
3. For up / down adjustment
(for vehicle without leveling system)
4. For up / down adjustment
(for vehicle with leveling system)
5. Headlight leveling actuatorHOT
SPOT LH. HEADLIGHT RH. HEADLIGHT
LIGHTING SYSTEM 8B-7
BULB REPLACEMENT
WARNING:
Don't touch when the bulb is hot.
1) Disconnect negative cable at battery.
2) Disconnect harness from bulb.
3) Remove socket cover and bulb.
4) Replace bulb and install in reverse removal procedure.
HEADLIGHT AIMING WITH SCREEN
NOTE:
Unless otherwise obligated by local regulations, adjust
headlight aiming according to following procedure.
After replacing headlight, be sure to perform its aiming.
When inspecting and adjusting headlight with leveling sys-
tem, make sure to set the leveling switch to ª0º position with
IG switch ON.
Before adjustment, make sure the following.
a) Place vehicle on a flat surface in front of blank wall as below
ahead of headlight surface.
Clearance ªaº: 10 m (32.8 ft)
b) Adjust air pressure of all tires to a specified value respectively.
c) Bounce vehicle body up and down by hand to stabilize suspen-
sion.
d) Carry out one driver aboard.
Driver's weight: 75 kg (165 lb)
Adjustment
1) Check to see if hot spot (high intensity zone) of each main (low)
beam axis falls as illustrated.
Clearance ªHº: Approx. 130 mm (5.15 in.)
2) If headlight aiming is not set properly, align it to specification by
adjusting aiming screw and aiming gear.
Page 565 of 801
YH4
GRAND
VITARA
Type B Type A
Type C
1. Washer tank
8D-10 WINDOWS, MIRRORS, SECURITY AND LOCKS
2) Testing automatic stop action.
a) Connect 12 V battery (+) terminal to terminal ªAº of wiper mo-
tor (1) and (±) terminal to Black lead wire (2) (Type A, B) or
terminal ªEº (Type C), and let the motor turn.
b) Disconnect terminal ªAº from battery, and let the motor stop.
c) Connect terminal ªAº and ªDº with a jumper wire (3), and con-
nect terminal ªCº to battery (+) terminal. Observe the motor
turns once again then stops at a given position.
d) Repeat a) thru c) several times and inspect if the motor stops
at the given position every time.
Washer Pump
Connect battery (+) and (±) terminals to pump (+) and (±) terminals
respectively to check pumping rate.
Check for both front (3) and rear (2) (if equipped) washer pump.
Pumping Rate:
Front and Rear (if equipped) more than 1.0 l / min.
(2.1 US pt. / min.,
1.76 lmp pt. / min.).
Page 568 of 801
YH4
GRAND
VITARA
Terminal
Switch
Terminal
Switch
ON
INT
WASHER
ON
BRINT
WINDOWS, MIRRORS, SECURITY AND LOCKS 8D-13
REAR WIPER AND WASHER (IF EQUIPPED)
INSPECTION
Rear Wiper and Washer Switch (in Combination Switch)
1) Disconnect negative cable at battery.
2) Disconnect combination switch lead wire coupler.
3) Check for continuity between terminals at each switch position
as shown below. If check result is not as specified, replace
switch.
Rear Wiper Switch
BRINT+IRBRINT+IR
OFF
INT
ON
Rear Washer Switch
BRWRBRWR
OFF
ON
Washer Pump
Refer to FRONT WIPER AND WASHER INSPECTION in this sec-
tion.
Wiper Motor
1) TESTING WIPER MOTOR
As shown left, use a 12 V battery to connect its (+) and (±) termi-
nals to terminal ªDº and Black lead wire (2) respectively. Then
motor (1) should rotate at 35 to 45 rpm.
Page 590 of 801
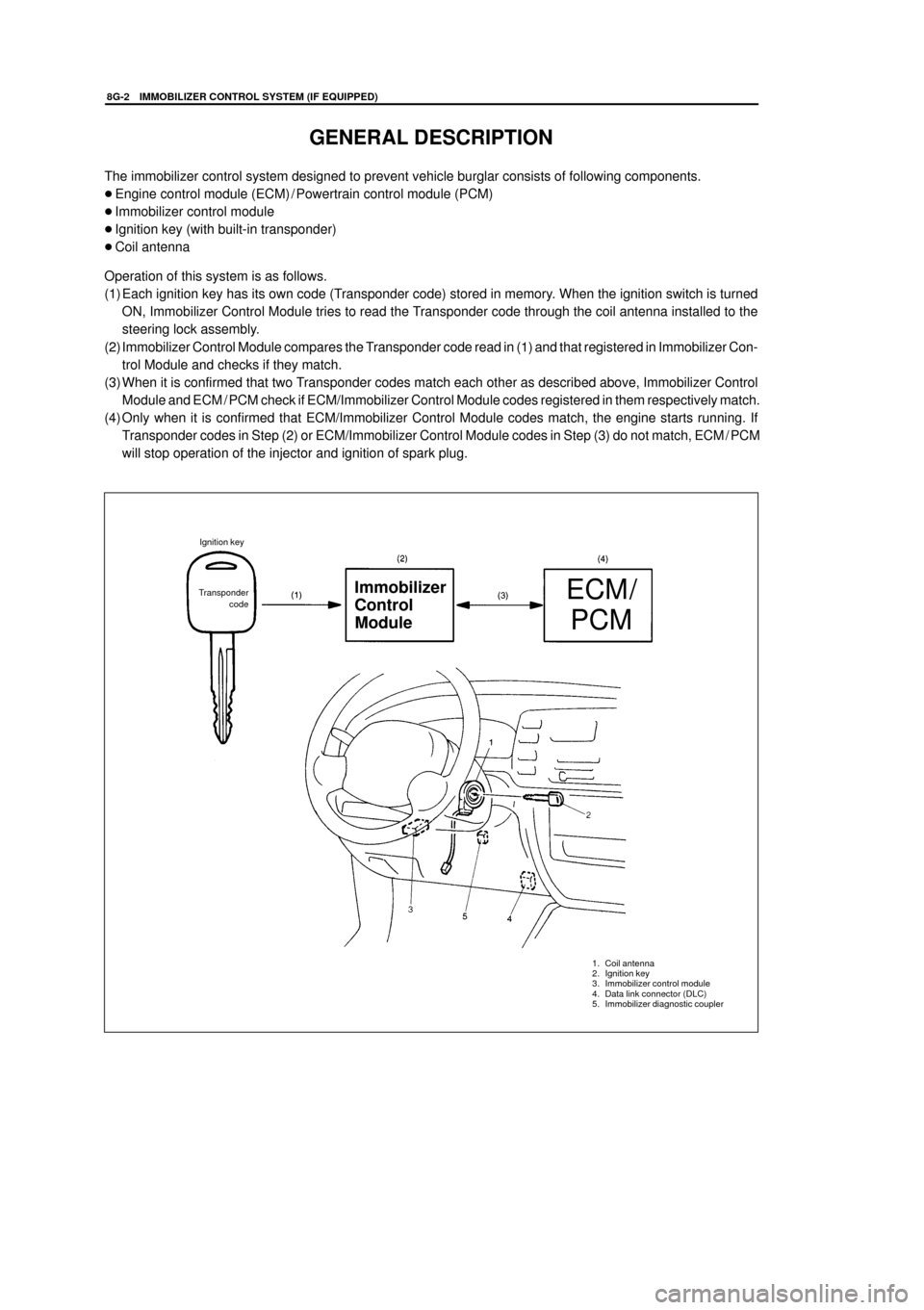
YH4
GRAND
VITARA
1. Coil antenna
2. Ignition key
3. Immobilizer control module
4. Data link connector (DLC)
5. Immobilizer diagnostic coupler Ignition key
Transponder
code
Immobilizer
Control
ModuleECM/
PCM
8G-2 IMMOBILIZER CONTROL SYSTEM (IF EQUIPPED)
GENERAL DESCRIPTION
The immobilizer control system designed to prevent vehicle burglar consists of following components.
Engine control module (ECM) / Powertrain control module (PCM)
Immobilizer control module
Ignition key (with built-in transponder)
Coil antenna
Operation of this system is as follows.
(1) Each ignition key has its own code (Transponder code) stored in memory. When the ignition switch is turned
ON, Immobilizer Control Module tries to read the Transponder code through the coil antenna installed to the
steering lock assembly.
(2) Immobilizer Control Module compares the Transponder code read in (1) and that registered in Immobilizer Con-
trol Module and checks if they match.
(3) When it is confirmed that two Transponder codes match each other as described above, Immobilizer Control
Module and ECM / PCM check if ECM/Immobilizer Control Module codes registered in them respectively match.
(4) Only when it is confirmed that ECM/Immobilizer Control Module codes match, the engine starts running. If
Transponder codes in Step (2) or ECM/Immobilizer Control Module codes in Step (3) do not match, ECM / PCM
will stop operation of the injector and ignition of spark plug.
Page 601 of 801
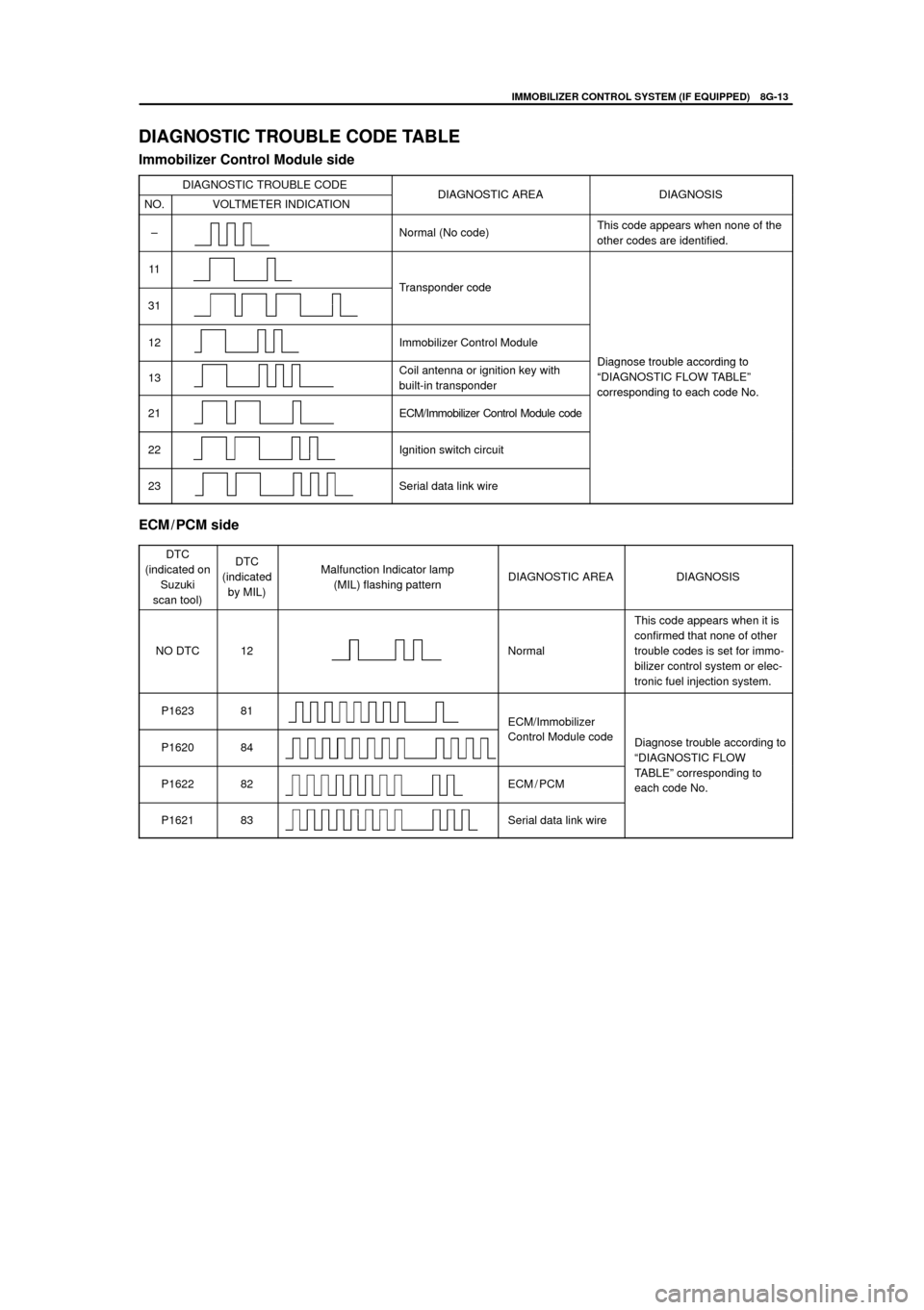
YH4
GRAND
VITARA
IMMOBILIZER CONTROL SYSTEM (IF EQUIPPED) 8G-13
DIAGNOSTIC TROUBLE CODE TABLE
Immobilizer Control Module side
DIAGNOSTIC TROUBLE CODEDIAGNOSTIC AREADIAGNOSISNO.VOLTMETER INDICATIONDIAGNOSTIC AREADIAGNOSIS
±Normal (No code)This code appears when none of the
other codes are identified.
11
Transponder code
31
Trans onder code
12Immobilizer Control Module
Diagnose trouble according to
13Coil antenna or ignition key with
built-in transponderDiagnose trouble according to
ªDIAGNOSTIC FLOW TABLEº
corresponding to each code No.
21ECM/Immobilizer Control Module code
corres onding to each code No.
22Ignition switch circuit
23Serial data link wire
ECM / PCM side
DTC
(indicated on
Suzuki
scan tool)DTC
(indicated
by MIL)Malfunction Indicator lamp
(MIL) flashing patternDIAGNOSTIC AREADIAGNOSIS
NO DTC12Normal
This code appears when it is
confirmed that none of other
trouble codes is set for immo-
bilizer control system or elec-
tronic fuel injection system.
P162381ECM/Immobilizer
P162084Control Module codeDiagnose trouble according to
ªDIAGNOSTIC FLOW
P162282ECM / PCMTABLEº corresponding to
each code No.
P162183Serial data link wire
Page 623 of 801
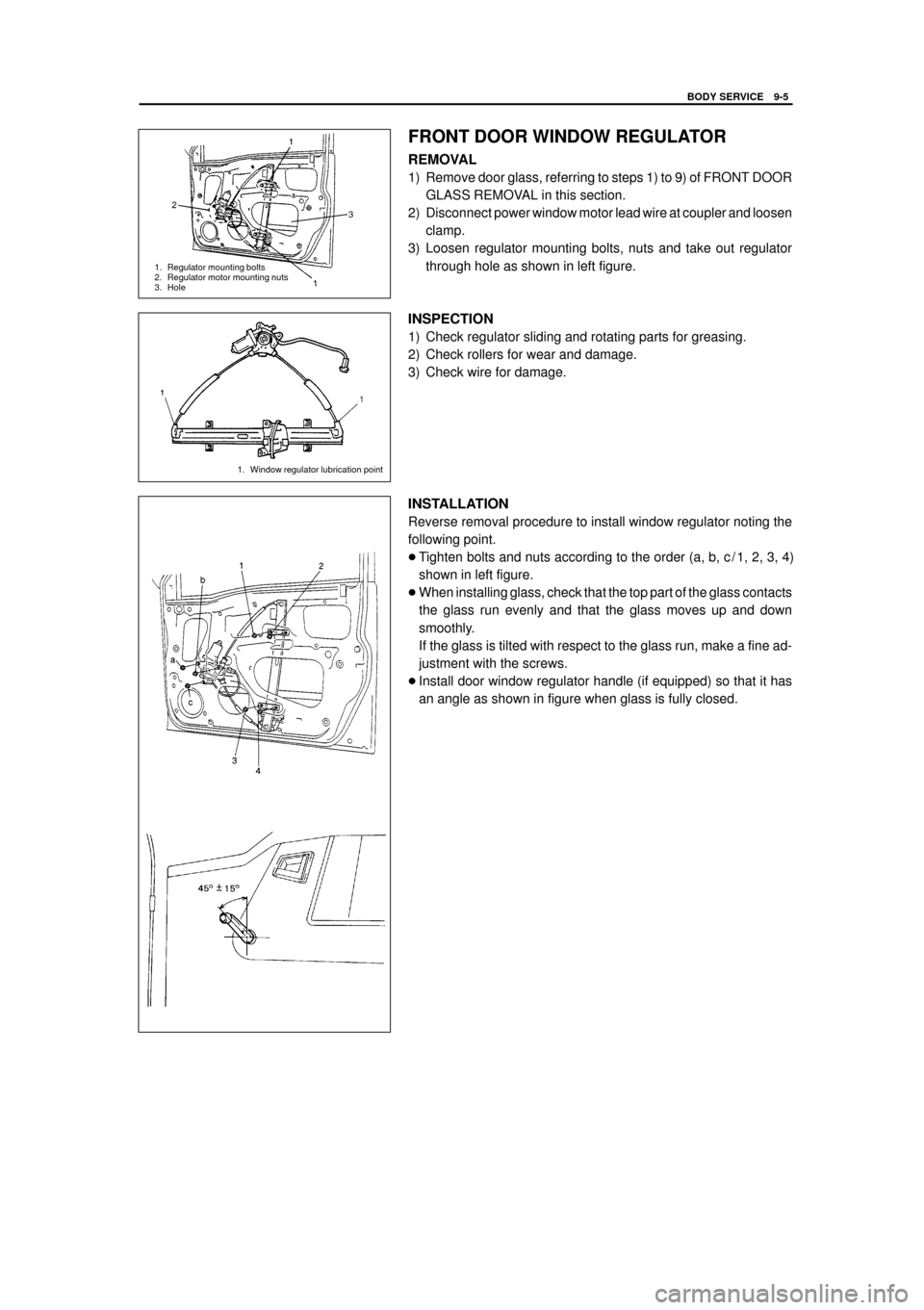
YH4
GRAND
VITARA
1. Window regulator lubrication point 1. Regulator mounting bolts
2. Regulator motor mounting nuts
3. Hole
BODY SERVICE 9-5
FRONT DOOR WINDOW REGULATOR
REMOVAL
1) Remove door glass, referring to steps 1) to 9) of FRONT DOOR
GLASS REMOVAL in this section.
2) Disconnect power window motor lead wire at coupler and loosen
clamp.
3) Loosen regulator mounting bolts, nuts and take out regulator
through hole as shown in left figure.
INSPECTION
1) Check regulator sliding and rotating parts for greasing.
2) Check rollers for wear and damage.
3) Check wire for damage.
INSTALLATION
Reverse removal procedure to install window regulator noting the
following point.
Tighten bolts and nuts according to the order (a, b, c / 1, 2, 3, 4)
shown in left figure.
When installing glass, check that the top part of the glass contacts
the glass run evenly and that the glass moves up and down
smoothly.
If the glass is tilted with respect to the glass run, make a fine ad-
justment with the screws.
Install door window regulator handle (if equipped) so that it has
an angle as shown in figure when glass is fully closed.