Page 194 of 510
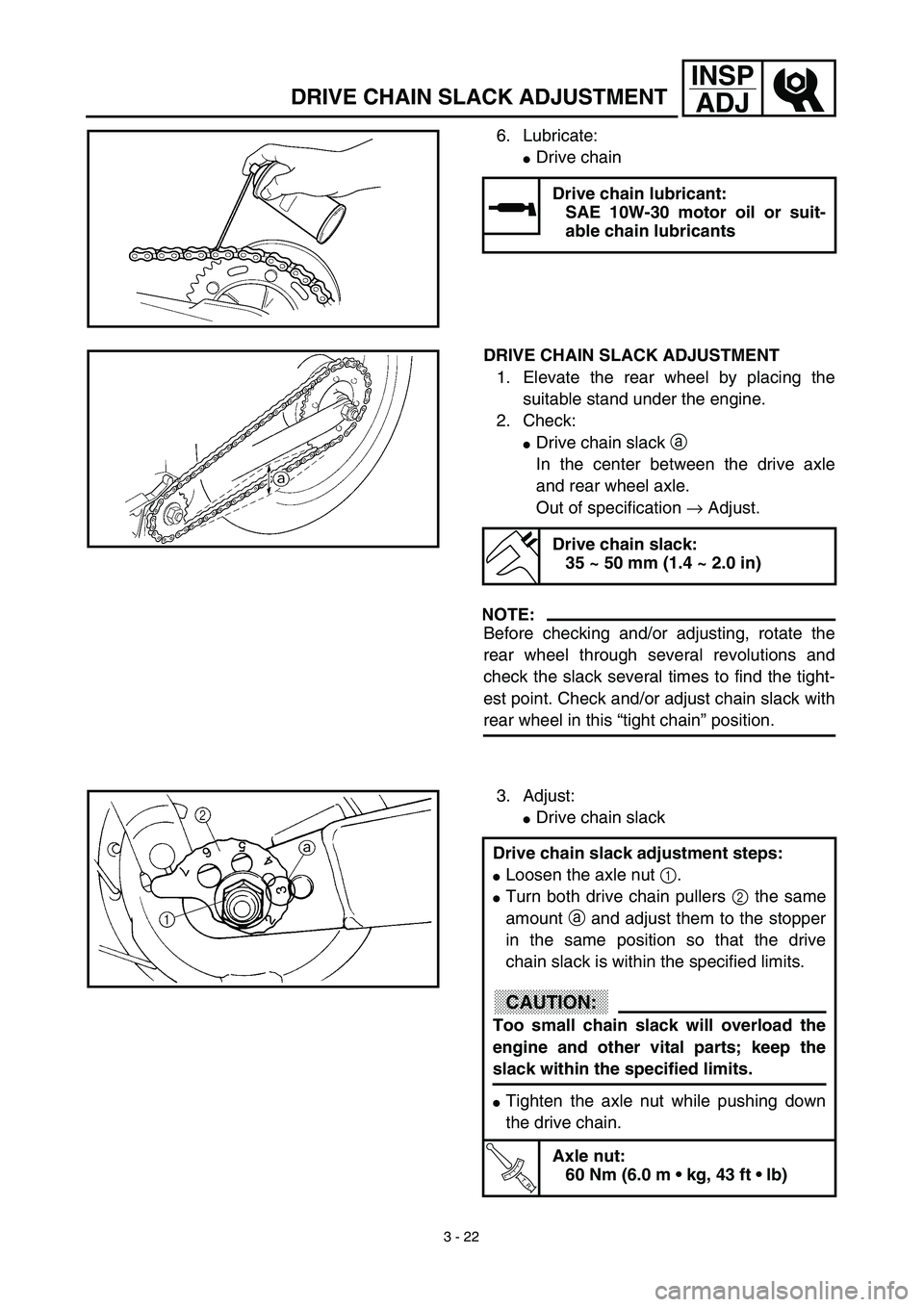
3 - 22
INSP
ADJ
DRIVE CHAIN SLACK ADJUSTMENT
6. Lubricate:
Drive chain
Drive chain lubricant:
SAE 10W-30 motor oil or suit-
able chain lubricants
DRIVE CHAIN SLACK ADJUSTMENT
1. Elevate the rear wheel by placing the
suitable stand under the engine.
2. Check:
Drive chain slack a
In the center between the drive axle
and rear wheel axle.
Out of specification → Adjust.
NOTE:
Before checking and/or adjusting, rotate the
rear wheel through several revolutions and
check the slack several times to find the tight-
est point. Check and/or adjust chain slack with
rear wheel in this “tight chain” position.
Drive chain slack:
35 ~ 50 mm (1.4 ~ 2.0 in)
3. Adjust:
Drive chain slack
Drive chain slack adjustment steps:
Loosen the axle nut 1.
Turn both drive chain pullers 2 the same
amount a and adjust them to the stopper
in the same position so that the drive
chain slack is within the specified limits.
CAUTION:
Too small chain slack will overload the
engine and other vital parts; keep the
slack within the specified limits.
Tighten the axle nut while pushing down
the drive chain.
T R..
Axle nut:
60 Nm (6.0 m • kg, 43 ft • lb)
Page 200 of 510
3 - 25
INSP
ADJSPOKES INSPECTION AND TIGHTENING/WHEEL INSPECTION/
STEERING HEAD INSPECTION AND ADJUSTMENT
SPOKES INSPECTION AND TIGHTENING
1. Inspect:
Spokes 1
Bend/damage → Replace.
Loose spoke → Retighten.
2. Tighten:
Spokes
NOTE:
Be sure to retighten these spokes before and
after break-in. After a practice check spokes
for looseness.
T R..Front 2 Nm (0.2 m · kg, 1.4 ft · lb)
Rear 3 Nm (0.3 m · kg, 2.2 ft · lb)
EC36T000
WHEEL INSPECTION
1. Inspect:
Wheel runout
Elevate the wheel and turn it.
Abnormal runout → Replace.
2. Inspect:
Bearing free play
Exist play → Replace.
STEERING HEAD INSPECTION AND
ADJUSTMENT
1. Elevate the front wheel by placing a suit-
able stand under the engine.
2. Check:
Steering shaft
Grasp the bottom of the forks and gen-
tly rock the fork assembly back and
forth.
Free play → Adjust steering head.
Page 208 of 510
3 - 29
INSP
ADJ
ELECTRICAL/SPARK PLUG INSPECTION
EC370000
ELECTRICAL
EC371001
SPARK PLUG INSPECTION
1. Remove:
Spark plug
2. Inspect:
Electrode 1
Wear/damage → Replace.
Insulator color 2
Normal condition is a medium to light
tan color.
Distinctly different color → Check the
engine condition.
NOTE:
When the engine runs for many hours at low
speeds, the spark plug insulator will become
sooty, even if the engine and carburetor are in
good operating condition.
3. Measure:
Plug gap a
Use a wire gauge or thickness gauge.
Out of specification → Regap.
4. Clean the plug with a spark plug cleaner
if necessary.
Spark plug gap:
0.6 ~ 0.7 mm (0.02 ~ 0.03 in)
Standard spark plug:
CR7HSA (NGK)
U22FSR-U (DENSO)
5. Tighten:
Spark plug
NOTE:
Before installing a spark plug, clean the gas-
ket surface and plug surface.
Finger-tighten a the spark plug before
torquing to specification b.
T R..13 Nm (1.3 m · kg, 9.4 ft · lb)
Page 246 of 510
4 - 19
ENGCYLINDER HEAD
9. Check:
Valve clearance
Out of specification → Adjust.
Refer to “VALVE CLEARANCE
INSPECTION AND ADJUSTMENT”
section in the CHAPTER 3.
10. Apply:
Engine oil
On camshaft.
11. Install:
Tappet cover 1
Cylinder head side cover 2
T R..18 Nm (1.8 m · kg, 13 ft · lb)
T R..10 Nm (1.0 m · kg, 7.2 ft · lb)
12. Install:
Timing mark accessing screw 1
Crankshaft end accessing screw 2
T R..7 Nm (0.7 m · kg, 5.1 ft · lb)
T R..7 Nm (0.7 m · kg, 5.1 ft · lb)
13. Install:
Spark plug
Engine bracket
T R..13 Nm (1.3 m · kg, 9.4 ft · lb)
T R..40 Nm (4.0 m · kg, 29 ft · lb)
Page 302 of 510
4 - 47
ENGCLUTCH AND PRIMARY DRIVEN GEAR
5. Install:
Ball
NOTE:
Apply the engine oil on the ball.
6. Install:
Push rod 1 1
Push plate 2
Washer 3
Nut (push rod 1) 4
7. Install:
Pressure plate 1
Clutch spring 2
Bolt (clutch spring) 3
NOTE:
Align the arrow mark a on the pressure
plate with the punched mark b on the clutch
boss.
Tighten the bolts in stage, using a crisscross
pattern.
T R..6 Nm (0.6 m · kg, 4.3 ft · lb)
8. Check:
Push lever position
Push the push lever assembly in the
arrow direction and make sure that the
mach mark are aligned → adjust.
aMatch mark on the push lever assembly
bMatch mark on the crankcase
Page 342 of 510
4 - 67
ENGCRANKCASE, CRANKSHAFT AND BALANCER
REMOVAL POINTS
Crankcase
1. Remove:
Bolt (crankcase)
Lead guide 1
Clutch cable holder 2
NOTE:
Loosen each bolt 1/4 of a turn at a time and
after all the bolts are loosened, remove them.
2. Remove:
Right crankcase 1
Use the crankcase separating tool 2.
NOTE:
Fully tighten the tool holding bolts, but make
sure the tool body is parallel with the case. If
necessary, one screw may be backed out
slightly to level tool body.
As pressure is applied, alternately tap on the
front engine mounting boss and transmission
shafts.
CAUTION:
Use soft hammer to tap on the case half.
Tap only on reinforced portions of case. Do
not tap on gasket mating surface. Work
slowly and carefully. Make sure the case
halves separate evenly. If one end “hangs
up”, take pressure off the push screw, re-
align, and start over. If the cases do not
separate, check for a remaining case screw
or fitting. Do not force.
Crankcase separating tool:
YU-1135-A/90890-01135
Page 364 of 510
4 - 78
ENGTRANSMISSION, SHIFT CAM AND SHIFT FORK
Shift cam and shift fork
1. Install:
Shift fork 1 (L) 1
Shift fork 2 (C) 2
Shift fork 3 (R) 3
NOTE:
Mesh the shift fork #1 (L) with the 2nd wheel
gear and #3 (R) with the 4th wheel gear on
the drive axle.
Mesh the shift fork #2 (C) with the 3rd pinion
gear on the main axle.
2. Install:
Shift cam 1
NOTE:
Apply the engine oil on the shift cam.
3. Install:
Shift fork guide bar 1 (short) 1
Shift fork guide bar 2 (long) 2
NOTE:
Apply the engine oil on the guide bars.
Be sure the long bar is inserted into the shift
forks #1 and #3 and the short one into #2.
4. Check:
Shifter operation
Transmission operation
Unsmooth operation → Repair.
Page 498 of 510
–+ELEC
6 - 2
IGNITION SYSTEM
EC620000
IGNITION SYSTEM
INSPECTION STEPS
Use the following steps for checking the possibility of the malfunctioning engine being attributable to
ignition system failure and for checking the spark plug which will not spark.
*marked: Only when the ignition checker is used.
NOTE:
Remove the following parts before inspection.
1) Seat
2) Fuel tank
Use the following special tools in this inspection.
Spark gap test*Clean or replace
spark plug.
Check entire ignition
system for connection.Repair or replace.
Check engine stop switch. Replace.
Check ignition coil. Primary coil Replace.
Secondary coil Replace.
Check CDI magneto. Pickup coil Replace.
Charging coil Replace.
Replace CDI unit.
Dynamic spark tester:
YM-34487
Ignition checker:
90890-06754Pocket tester:
YU-3112-C/90890-03112
No Spark
OK
OK
OK
OK
Spark
No good
No good
No good
No good
No good
No good