Page 149 of 626
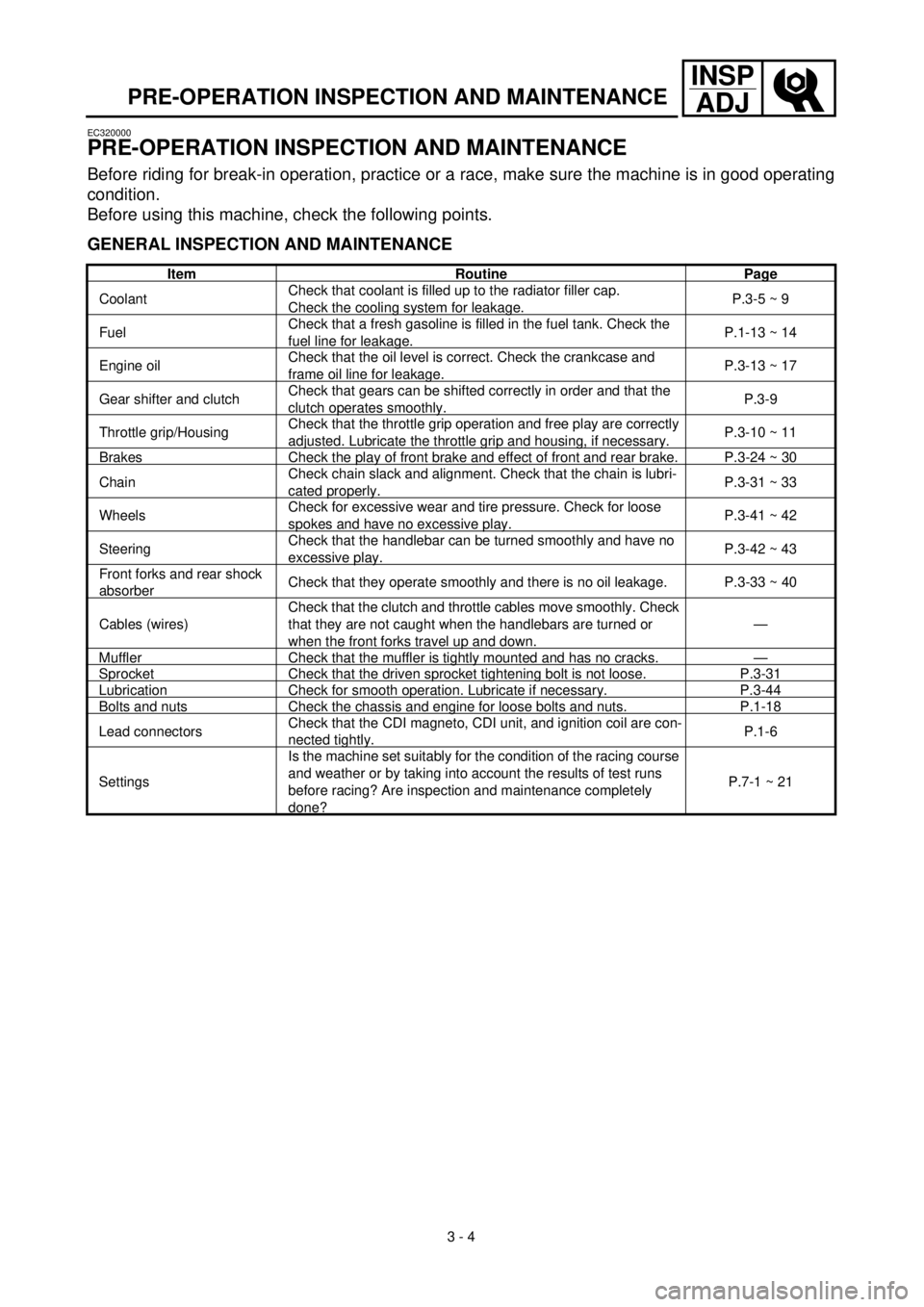
3 - 4
INSP
ADJ
PRE-OPERATION INSPECTION AND MAINTENANCE
EC320000
PRE-OPERATION INSPECTION AND MAINTENANCE
Before riding for break-in operation, practice or a race, make sure the machine is in good operating
condition.
Before using this machine, check the following points.
GENERAL INSPECTION AND MAINTENANCE
Item Routine Page
CoolantCheck that coolant is filled up to the radiator filler cap.
Check the cooling system for leakage.P.3-5 ~ 9
FuelCheck that a fresh gasoline is filled in the fuel tank. Check the
fuel line for leakage.P.1-13 ~ 14
Engine oilCheck that the oil level is correct. Check the crankcase and
frame oil line for leakage.P.3-13 ~ 17
Gear shifter and clutchCheck that gears can be shifted correctly in order and that the
clutch operates smoothly.P.3-9
Throttle grip/HousingCheck that the throttle grip operation and free play are correctly
adjusted. Lubricate the throttle grip and housing, if necessary.P.3-10 ~ 11
Brakes Check the play of front brake and effect of front and rear brake. P.3-24 ~ 30
ChainCheck chain slack and alignment. Check that the chain is lubri-
cated properly.P.3-31 ~ 33
WheelsCheck for excessive wear and tire pressure. Check for loose
spokes and have no excessive play.P.3-41 ~ 42
SteeringCheck that the handlebar can be turned smoothly and have no
excessive play.P.3-42 ~ 43
Front forks and rear shock
absorberCheck that they operate smoothly and there is no oil leakage. P.3-33 ~ 40
Cables (wires)Check that the clutch and throttle cables move smoothly. Check
that they are not caught when the handlebars are turned or
when the front forks travel up and down.—
Muffler Check that the muffler is tightly mounted and has no cracks. —
Sprocket Check that the driven sprocket tightening bolt is not loose. P.3-31
Lubrication Check for smooth operation. Lubricate if necessary. P.3-44
Bolts and nuts Check the chassis and engine for loose bolts and nuts. P.1-18
Lead connectorsCheck that the CDI magneto, CDI unit, and ignition coil are con-
nected tightly.P.1-6
SettingsIs the machine set suitably for the condition of the racing course
and weather or by taking into account the results of test runs
before racing? Are inspection and maintenance completely
done?P.7-1 ~ 21
Page 152 of 626
3 - 5
INSP
ADJ
EC350000
ENGINE
EC351011
COOLANT LEVEL INSPECTION
WARNING
Do not remove the radiator cap 1, drain
bolt and hoses when the engine and radia-
tor are hot. Scalding hot fluid and steam
may be blown out under pressure, which
could cause serious injury.
When the engine has cooled, place a thick
towel over the radiator cap, slowly rotate
the cap counterclockwise to the detent.
This procedure allows any residual pres-
sure to escape. When the hissing sound
has stopped, press down on the cap while
turning counterclockwise and remove it.
CAUTION:
Hard water or salt water is harmful to the
engine parts. You may use distilled water, if
you can’t get soft water.
1. Place the machine on a level place, and
hold it in an upright position.
2. Remove:
lRadiator cap
3. Check:
lCoolant level a
Coolant level low ® Add coolant.
1Radiator
ENGINE/COOLANT LEVEL INSPECTION
Page 156 of 626
3 - 7
INSP
ADJ
RADIATOR CAP INSPECTION
CAUTION:
lDo not mix more than one type of ethyl-
ene glycol antifreeze containing corro-
sion inhibitors for aluminum engine.
lDo not use water containing impurities or
oil.
7. Install:
lRadiator cap
Start the engine and warm it up for a
several minutes.
8. Check:
lCoolant level
Coolant level low ® Add coolant. Handling notes of coolant:
The coolant is harmful so it should be han-
dled with special care.
WARNING
lWhen coolant splashes to your eye.
Thoroughly wash your eye with water
and see your doctor.
lWhen coolant splashes to your clothes.
Quickly wash it away with water and
then with soap.
lWhen coolant is swallowed.
Quickly make him vomit and take him
to a doctor.
EC355000
RADIATOR CAP INSPECTION
1. Inspect:
lSeal (radiator cap) 1
lValve and valve seat 2
Crack/damage ® Replace.
Exist fur deposits 3 ® Clean or
replace.
Page 162 of 626
3 - 10
INSP
ADJ
THROTTLE CABLE ADJUSTMENT
EC35A001
THROTTLE CABLE ADJUSTMENT
1. Check:
lThrottle grip free play a
Out of specification ® Adjust.
Throttle grip free play a:
3 ~ 5 mm (0.12 ~ 0.20 in)
2. Adjust:
lThrottle grip free play
Throttle grip free play adjustment steps:
lRemove the throttle cable cover 1.
NOTE:
lBefore adjusting the throttle cable free
play, the engine idle speed should be
adjusted.
lWhen the motorcycle is accelerating,
throttle cable #1 2 is pulled and throttle
cable #2 3 is pushed.
1st step:
lLoosen the locknuts 4 on throttle cable #2.
lAdjust the free play by changing their
tightening position.
2nd step:
lLoosen the locknuts 5 on throttle cable #1.
lAdjust the free play by changing their
tightening position.
lTighten the locknuts.
WARNING
After adjusting, turn the handlebar to
right and left and make sure that the
engine idling does not run faster.
lInstall the throttle cable cover.
Page 164 of 626
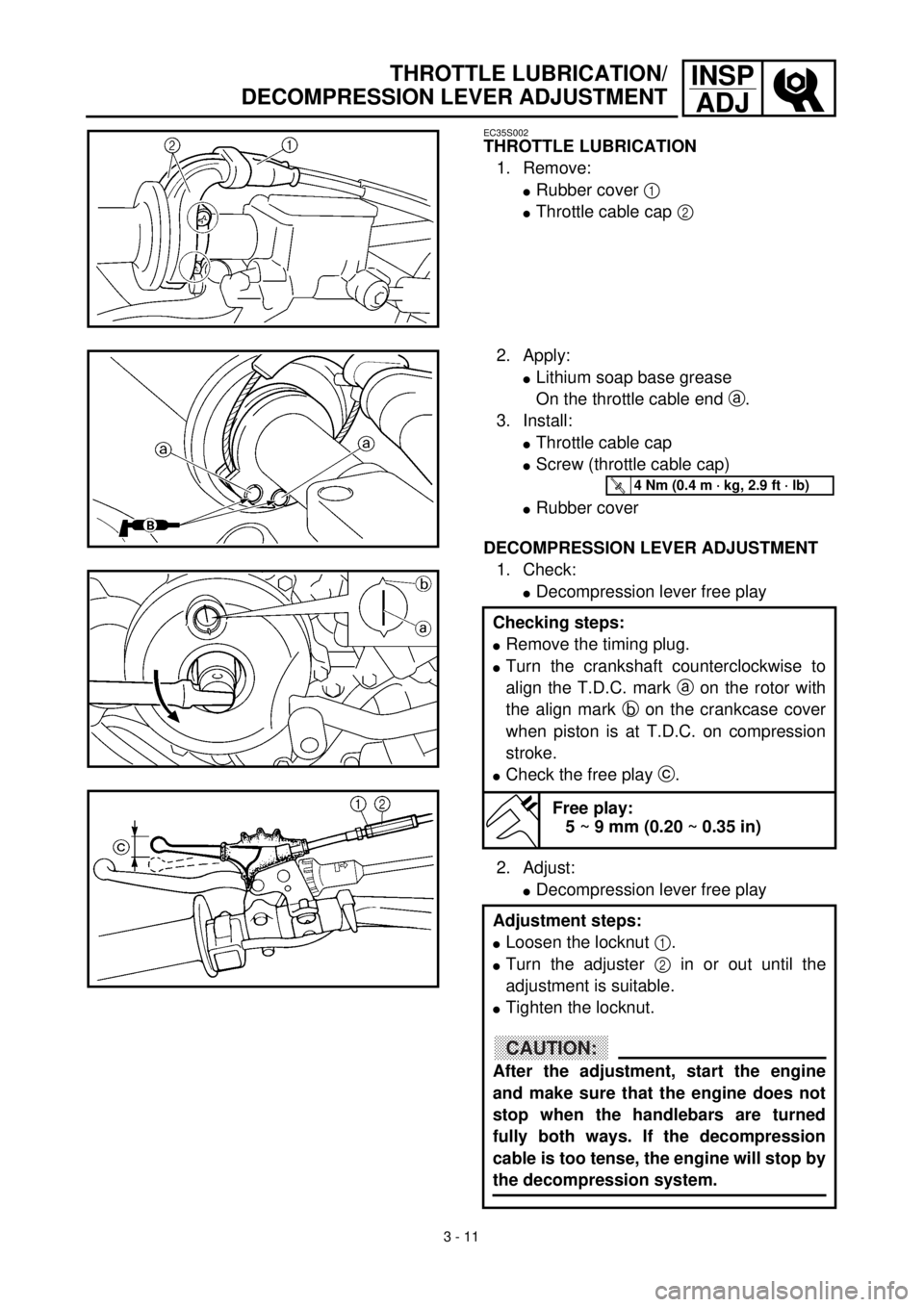
3 - 11
INSP
ADJTHROTTLE LUBRICATION/
DECOMPRESSION LEVER ADJUSTMENT
EC35S002
THROTTLE LUBRICATION
1. Remove:
lRubber cover 1
lThrottle cable cap 2
2. Apply:
lLithium soap base grease
On the throttle cable end a.
3. Install:
lThrottle cable cap
lScrew (throttle cable cap)
lRubber cover
DECOMPRESSION LEVER ADJUSTMENT
1. Check:
lDecompression lever free play
2. Adjust:
lDecompression lever free play Checking steps:
lRemove the timing plug.
lTurn the crankshaft counterclockwise to
align the T.D.C. mark a on the rotor with
the align mark b on the crankcase cover
when piston is at T.D.C. on compression
stroke.
lCheck the free play c.
Free play:
5 ~ 9 mm (0.20 ~ 0.35 in)
Adjustment steps:
lLoosen the locknut 1.
lTurn the adjuster 2 in or out until the
adjustment is suitable.
lTighten the locknut.
CAUTION:
After the adjustment, start the engine
and make sure that the engine does not
stop when the handlebars are turned
fully both ways. If the decompression
cable is too tense, the engine will stop by
the decompression system.
T R..4 Nm (0.4 m · kg, 2.9 ft · lb)
Page 168 of 626
3 - 13
INSP
ADJ
ENGINE OIL LEVEL INSPECTION
6. Apply:
lLithium soap base grease
On the matching surface a on air filter
element.
7. Install:
lAir filter element 1
lWasher
lFitting bolt
NOTE:
Align the projection a on filter guide with the
hole b in air filter case.
T R..2 Nm (0.2 m · kg, 1.4 ft · lb)
ENGINE OIL LEVEL INSPECTION
1. Stand the motorcycle on a level surface.
NOTE:
lWhen checking the oil level make sure that
the motorcycle is upright.
lPlace the motorcycle on a suitable stand.
WARNING
Never remove the oil tank cap just after
high speed operation. The heated oil could
spurt out. causing danger. Wait until the oil
cools down to approximately 70 ˚C (158 ˚F).
2. Idle the engine more than 3 minutes
while keeping the motorcycle upright.
Then stop the engine and inspect the oil
level.
3. Remove:
lOil tank cap 1
Page 174 of 626
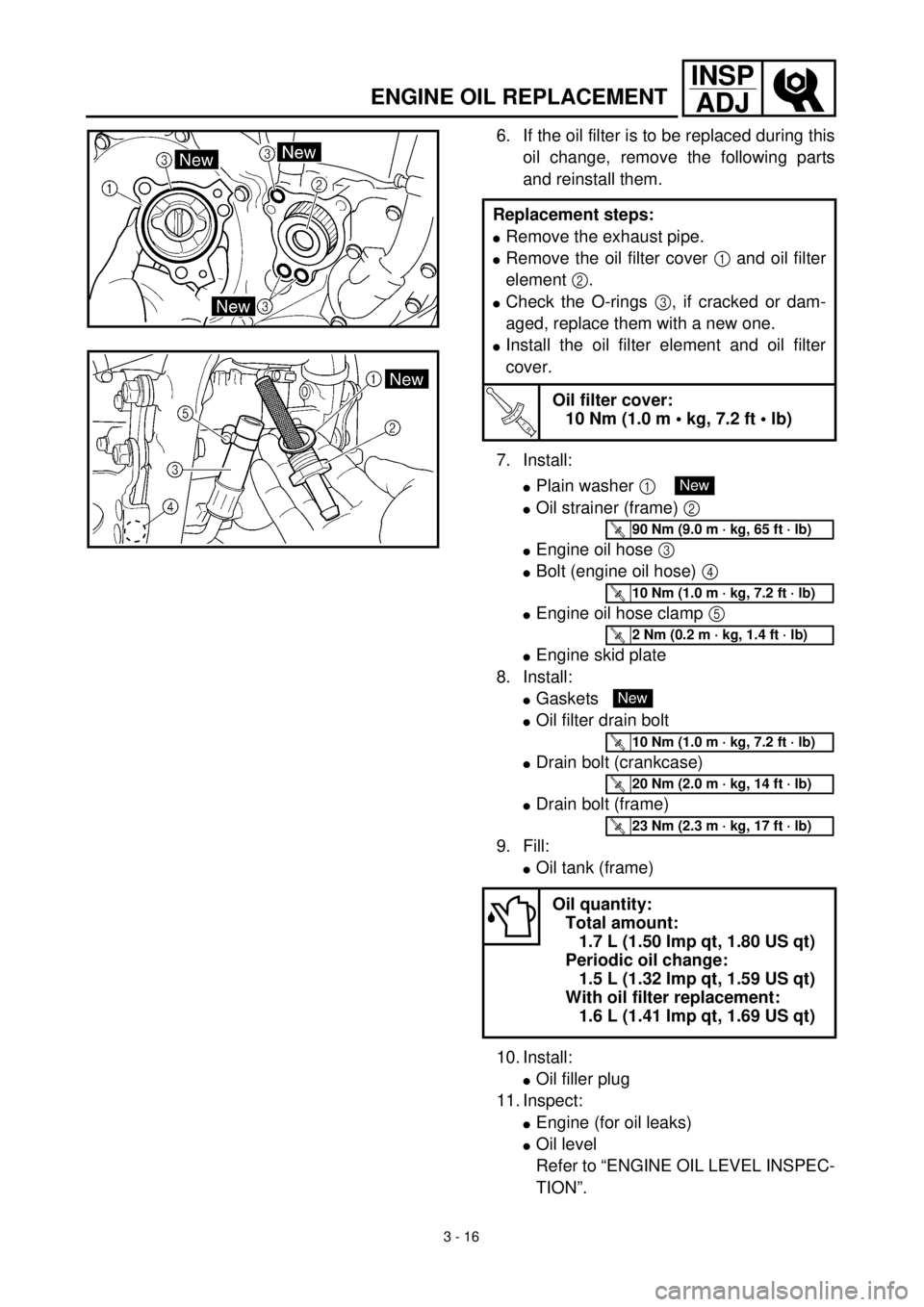
3 - 16
INSP
ADJ
ENGINE OIL REPLACEMENT
6. If the oil filter is to be replaced during this
oil change, remove the following parts
and reinstall them.
7. Install:
lPlain washer 1
lOil strainer (frame) 2
lEngine oil hose 3
lBolt (engine oil hose) 4
lEngine oil hose clamp 5
lEngine skid plate
8. Install:
lGaskets
lOil filter drain bolt
lDrain bolt (crankcase)
lDrain bolt (frame)
9. Fill:
lOil tank (frame)
10. Install:
lOil filler plug
11. Inspect:
lEngine (for oil leaks)
lOil level
Refer to “ENGINE OIL LEVEL INSPEC-
TION”. Replacement steps:
lRemove the exhaust pipe.
lRemove the oil filter cover 1 and oil filter
element 2.
lCheck the O-rings 3, if cracked or dam-
aged, replace them with a new one.
lInstall the oil filter element and oil filter
cover.
T R..
Oil filter cover:
10 Nm (1.0 m • kg, 7.2 ft • lb)
Oil quantity:
Total amount:
1.7 L (1.50 Imp qt, 1.80 US qt)
Periodic oil change:
1.5 L (1.32 Imp qt, 1.59 US qt)
With oil filter replacement:
1.6 L (1.41 Imp qt, 1.69 US qt)
New
T R..90 Nm (9.0 m · kg, 65 ft · lb)
T R..10 Nm (1.0 m · kg, 7.2 ft · lb)
T R..2 Nm (0.2 m · kg, 1.4 ft · lb)
New
T R..10 Nm (1.0 m · kg, 7.2 ft · lb)
T R..20 Nm (2.0 m · kg, 14 ft · lb)
T R..23 Nm (2.3 m · kg, 17 ft · lb)
Page 176 of 626
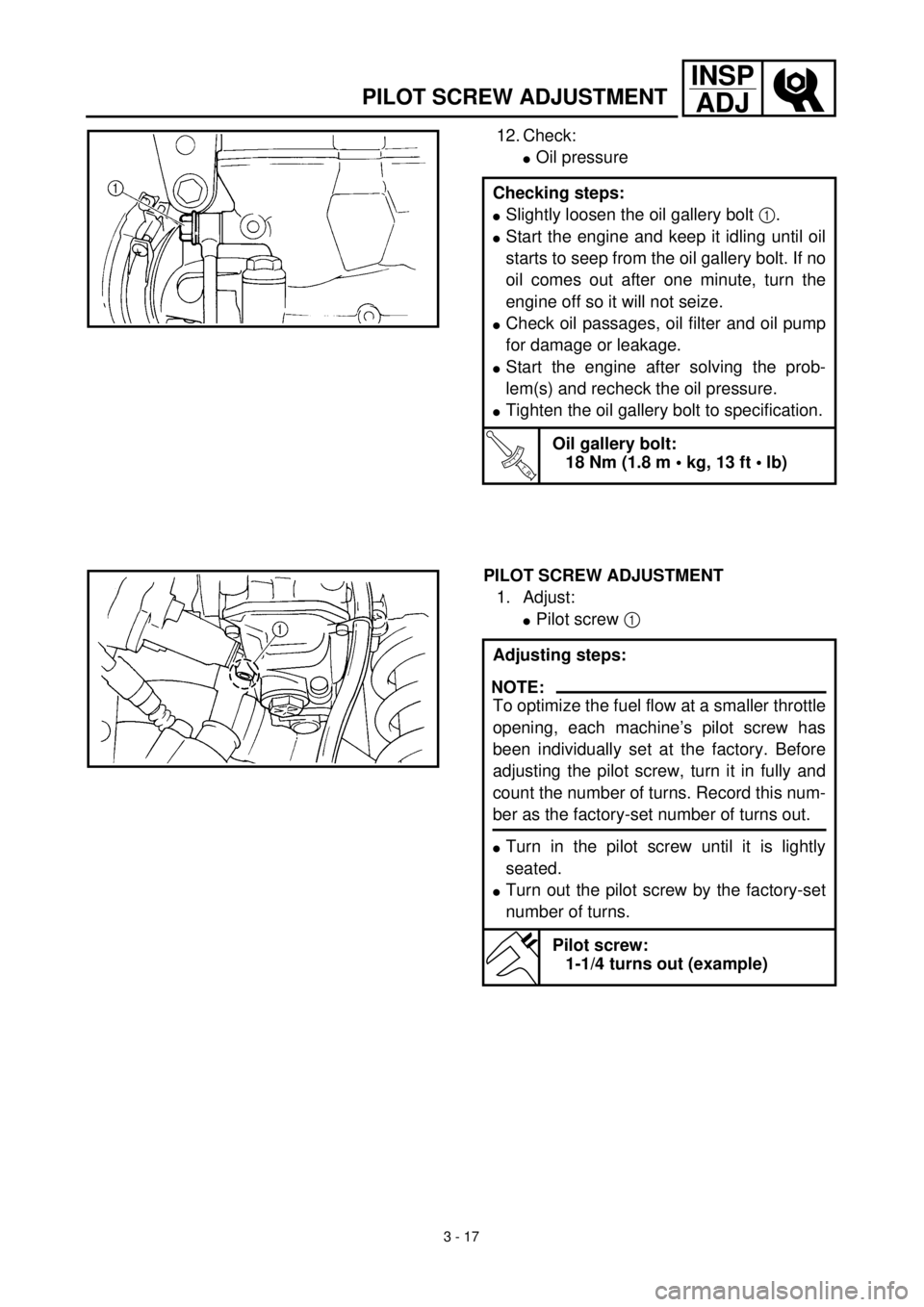
3 - 17
INSP
ADJ
PILOT SCREW ADJUSTMENT
12. Check:
lOil pressure
Checking steps:
lSlightly loosen the oil gallery bolt 1.
lStart the engine and keep it idling until oil
starts to seep from the oil gallery bolt. If no
oil comes out after one minute, turn the
engine off so it will not seize.
lCheck oil passages, oil filter and oil pump
for damage or leakage.
lStart the engine after solving the prob-
lem(s) and recheck the oil pressure.
lTighten the oil gallery bolt to specification.
T R..
Oil gallery bolt:
18 Nm (1.8 m • kg, 13 ft • lb)
PILOT SCREW ADJUSTMENT
1. Adjust:
lPilot screw 1
Adjusting steps:
NOTE:
To optimize the fuel flow at a smaller throttle
opening, each machine’s pilot screw has
been individually set at the factory. Before
adjusting the pilot screw, turn it in fully and
count the number of turns. Record this num-
ber as the factory-set number of turns out.
lTurn in the pilot screw until it is lightly
seated.
lTurn out the pilot screw by the factory-set
number of turns.
Pilot screw:
1-1/4 turns out (example)