Page 39 of 762
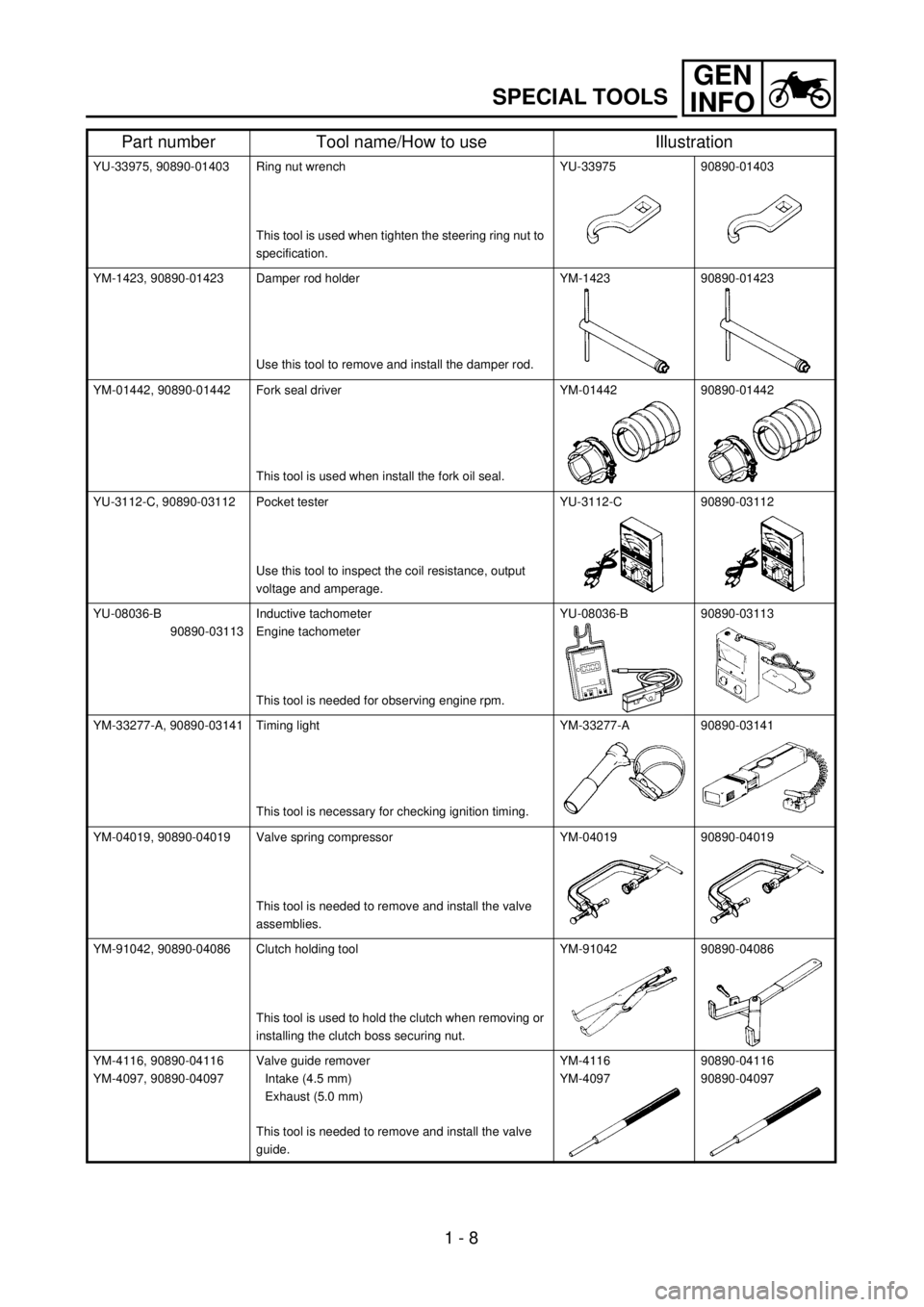
1 - 8
GEN
INFO
SPECIAL TOOLS
YU-33975, 90890-01403 Ring nut wrench
This tool is used when tighten the steering ring nut to
specification.YU-33975 90890-01403
YM-1423, 90890-01423 Damper rod holder
Use this tool to remove and install the damper rod.YM-1423 90890-01423
YM-01442, 90890-01442 Fork seal driver
This tool is used when install the fork oil seal.YM-01442 90890-01442
YU-3112-C, 90890-03112 Pocket tester
Use this tool to inspect the coil resistance, output
voltage and amperage.YU-3112-C 90890-03112
YU-08036-B
90890-03113Inductive tachometer
Engine tachometer
This tool is needed for observing engine rpm.YU-08036-B 90890-03113
YM-33277-A, 90890-03141 Timing light
This tool is necessary for checking ignition timing.YM-33277-A 90890-03141
YM-04019, 90890-04019 Valve spring compressor
This tool is needed to remove and install the valve
assemblies.YM-04019 90890-04019
YM-91042, 90890-04086 Clutch holding tool
This tool is used to hold the clutch when removing or
installing the clutch boss securing nut.YM-91042 90890-04086
YM-4116, 90890-04116
YM-4097, 90890-04097Valve guide remover
Intake (4.5 mm)
Exhaust (5.0 mm)
This tool is needed to remove and install the valve
guide.YM-4116
YM-409790890-04116
90890-04097
Part number Tool name/How to use Illustration
Page 89 of 762
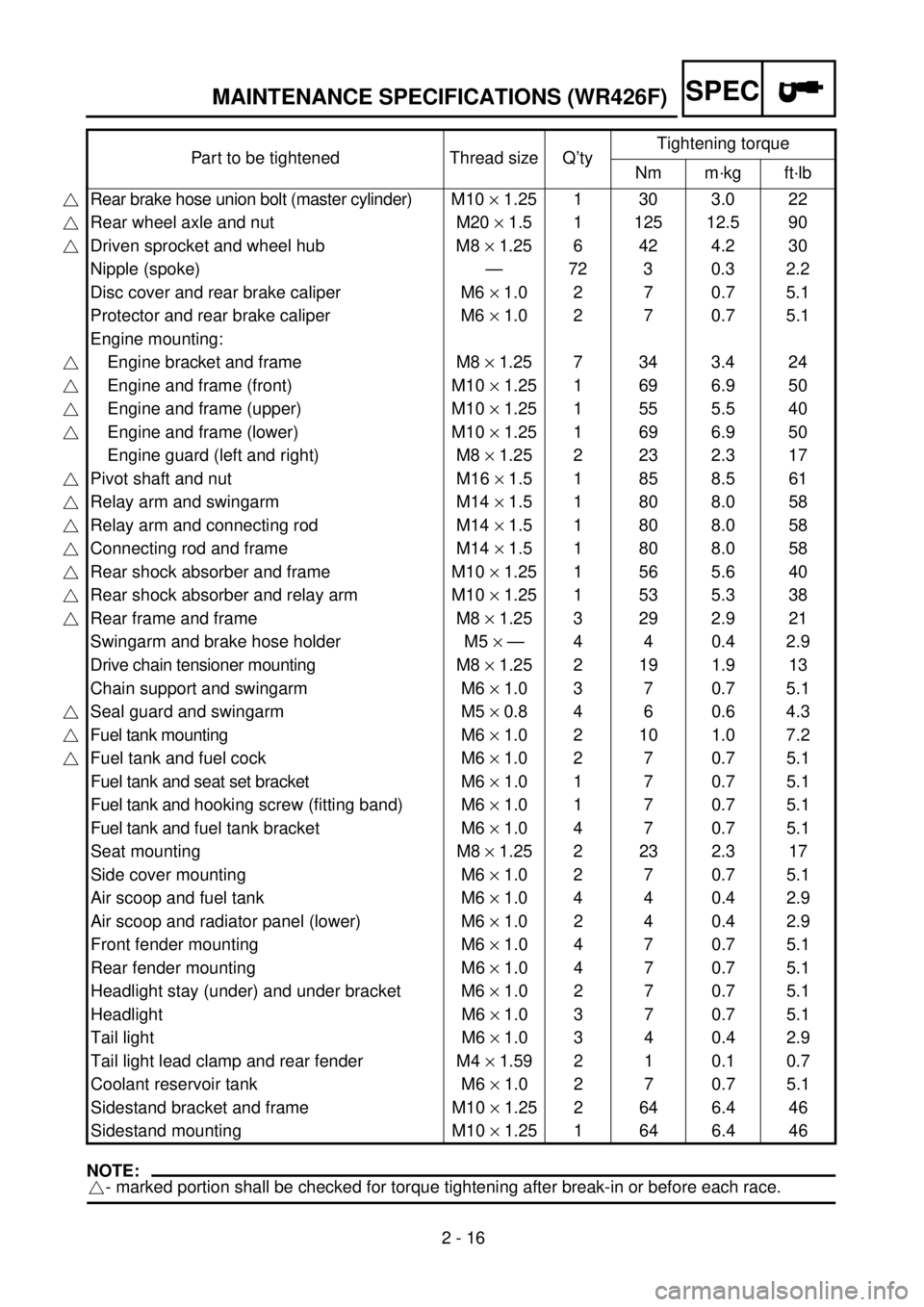
2 - 16
SPECMAINTENANCE SPECIFICATIONS (WR426F)
NOTE:
- marked portion shall be checked for torque tightening after break-in or before each race.Part to be tightened Thread size Q’tyTightening torque
Nm m·kg ft·lb
Rear brake hose union bolt (master cylinder)M10 ´ 1.25 1 30 3.0 22
Rear wheel axle and nut M20 ´ 1.5 1 125 12.5 90
Driven sprocket and wheel hub M8 ´ 1.25 6 42 4.2 30
Nipple (spoke) — 72 3 0.3 2.2
Disc cover and rear brake caliper M6 ´ 1.0 2 7 0.7 5.1
Protector and rear brake caliper M6 ´ 1.0 2 7 0.7 5.1
Engine mounting:
Engine bracket and frame M8 ´ 1.25 7 34 3.4 24
Engine and frame (front) M10 ´ 1.25 1 69 6.9 50
Engine and frame (upper) M10 ´ 1.25 1 55 5.5 40
Engine and frame (lower) M10 ´ 1.25 1 69 6.9 50
Engine guard (left and right) M8 ´ 1.25 2 23 2.3 17
Pivot shaft and nut M16 ´ 1.5 1 85 8.5 61
Relay arm and swingarm M14 ´ 1.5 1 80 8.0 58
Relay arm and connecting rod M14 ´ 1.5 1 80 8.0 58
Connecting rod and frame M14 ´ 1.5 1 80 8.0 58
Rear shock absorber and frame M10 ´ 1.25 1 56 5.6 40
Rear shock absorber and relay arm M10 ´ 1.25 1 53 5.3 38
Rear frame and frame M8 ´ 1.25 3 29 2.9 21
Swingarm and brake hose holder M5 ´ — 4 4 0.4 2.9
Drive chain tensioner mounting M8 ´ 1.25 2 19 1.9 13
Chain support and swingarm M6 ´ 1.0 3 7 0.7 5.1
Seal guard and swingarm M5 ´ 0.8 4 6 0.6 4.3
Fuel tank mounting M6 ´ 1.0 2 10 1.0 7.2
Fuel tank and fuel cock M6 ´ 1.0 2 7 0.7 5.1
Fuel tank and seat set bracket M6 ´ 1.0 1 7 0.7 5.1
Fuel tank and hooking screw (fitting band) M6 ´ 1.0 1 7 0.7 5.1
Fuel tank and fuel tank bracket M6 ´ 1.0 4 7 0.7 5.1
Seat mounting M8 ´ 1.25 2 23 2.3 17
Side cover mounting M6 ´ 1.0 2 7 0.7 5.1
Air scoop and fuel tank M6 ´ 1.0 4 4 0.4 2.9
Air scoop and radiator panel (lower) M6 ´ 1.0 2 4 0.4 2.9
Front fender mounting M6 ´ 1.0 4 7 0.7 5.1
Rear fender mounting M6 ´ 1.0 4 7 0.7 5.1
Headlight stay (under) and under bracket M6 ´ 1.0 2 7 0.7 5.1
Headlight M6 ´ 1.0 3 7 0.7 5.1
Tail light M6 ´ 1.0 3 4 0.4 2.9
Tail light lead clamp and rear fender M4 ´ 1.59 2 1 0.1 0.7
Coolant reservoir tank M6 ´ 1.0 2 7 0.7 5.1
Sidestand bracket and frame M10 ´ 1.25 2 64 6.4 46
Sidestand mounting M10 ´ 1.25 1 64 6.4 46
Page 106 of 762
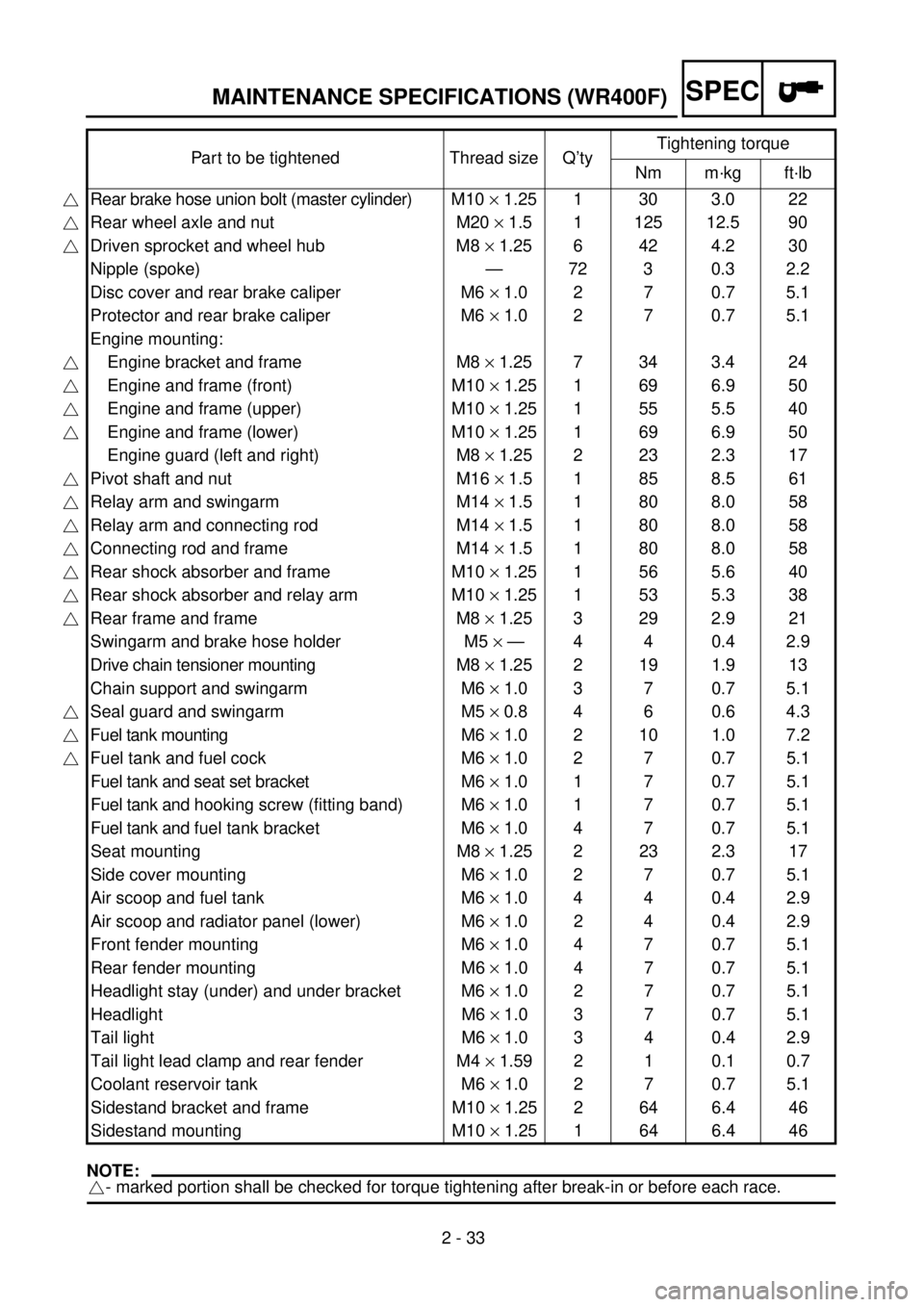
2 - 33
SPECMAINTENANCE SPECIFICATIONS (WR400F)
NOTE:
- marked portion shall be checked for torque tightening after break-in or before each race.Part to be tightened Thread size Q’tyTightening torque
Nm m·kg ft·lb
Rear brake hose union bolt (master cylinder)M10 ´ 1.25 1 30 3.0 22
Rear wheel axle and nut M20 ´ 1.5 1 125 12.5 90
Driven sprocket and wheel hub M8 ´ 1.25 6 42 4.2 30
Nipple (spoke) — 72 3 0.3 2.2
Disc cover and rear brake caliper M6 ´ 1.0 2 7 0.7 5.1
Protector and rear brake caliper M6 ´ 1.0 2 7 0.7 5.1
Engine mounting:
Engine bracket and frame M8 ´ 1.25 7 34 3.4 24
Engine and frame (front) M10 ´ 1.25 1 69 6.9 50
Engine and frame (upper) M10 ´ 1.25 1 55 5.5 40
Engine and frame (lower) M10 ´ 1.25 1 69 6.9 50
Engine guard (left and right) M8 ´ 1.25 2 23 2.3 17
Pivot shaft and nut M16 ´ 1.5 1 85 8.5 61
Relay arm and swingarm M14 ´ 1.5 1 80 8.0 58
Relay arm and connecting rod M14 ´ 1.5 1 80 8.0 58
Connecting rod and frame M14 ´ 1.5 1 80 8.0 58
Rear shock absorber and frame M10 ´ 1.25 1 56 5.6 40
Rear shock absorber and relay arm M10 ´ 1.25 1 53 5.3 38
Rear frame and frame M8 ´ 1.25 3 29 2.9 21
Swingarm and brake hose holder M5 ´ — 4 4 0.4 2.9
Drive chain tensioner mounting M8 ´ 1.25 2 19 1.9 13
Chain support and swingarm M6 ´ 1.0 3 7 0.7 5.1
Seal guard and swingarm M5 ´ 0.8 4 6 0.6 4.3
Fuel tank mounting M6 ´ 1.0 2 10 1.0 7.2
Fuel tank and fuel cock M6 ´ 1.0 2 7 0.7 5.1
Fuel tank and seat set bracket M6 ´ 1.0 1 7 0.7 5.1
Fuel tank and hooking screw (fitting band) M6 ´ 1.0 1 7 0.7 5.1
Fuel tank and fuel tank bracket M6 ´ 1.0 4 7 0.7 5.1
Seat mounting M8 ´ 1.25 2 23 2.3 17
Side cover mounting M6 ´ 1.0 2 7 0.7 5.1
Air scoop and fuel tank M6 ´ 1.0 4 4 0.4 2.9
Air scoop and radiator panel (lower) M6 ´ 1.0 2 4 0.4 2.9
Front fender mounting M6 ´ 1.0 4 7 0.7 5.1
Rear fender mounting M6 ´ 1.0 4 7 0.7 5.1
Headlight stay (under) and under bracket M6 ´ 1.0 2 7 0.7 5.1
Headlight M6 ´ 1.0 3 7 0.7 5.1
Tail light M6 ´ 1.0 3 4 0.4 2.9
Tail light lead clamp and rear fender M4 ´ 1.59 2 1 0.1 0.7
Coolant reservoir tank M6 ´ 1.0 2 7 0.7 5.1
Sidestand bracket and frame M10 ´ 1.25 2 64 6.4 46
Sidestand mounting M10 ´ 1.25 1 64 6.4 46
Page 268 of 762
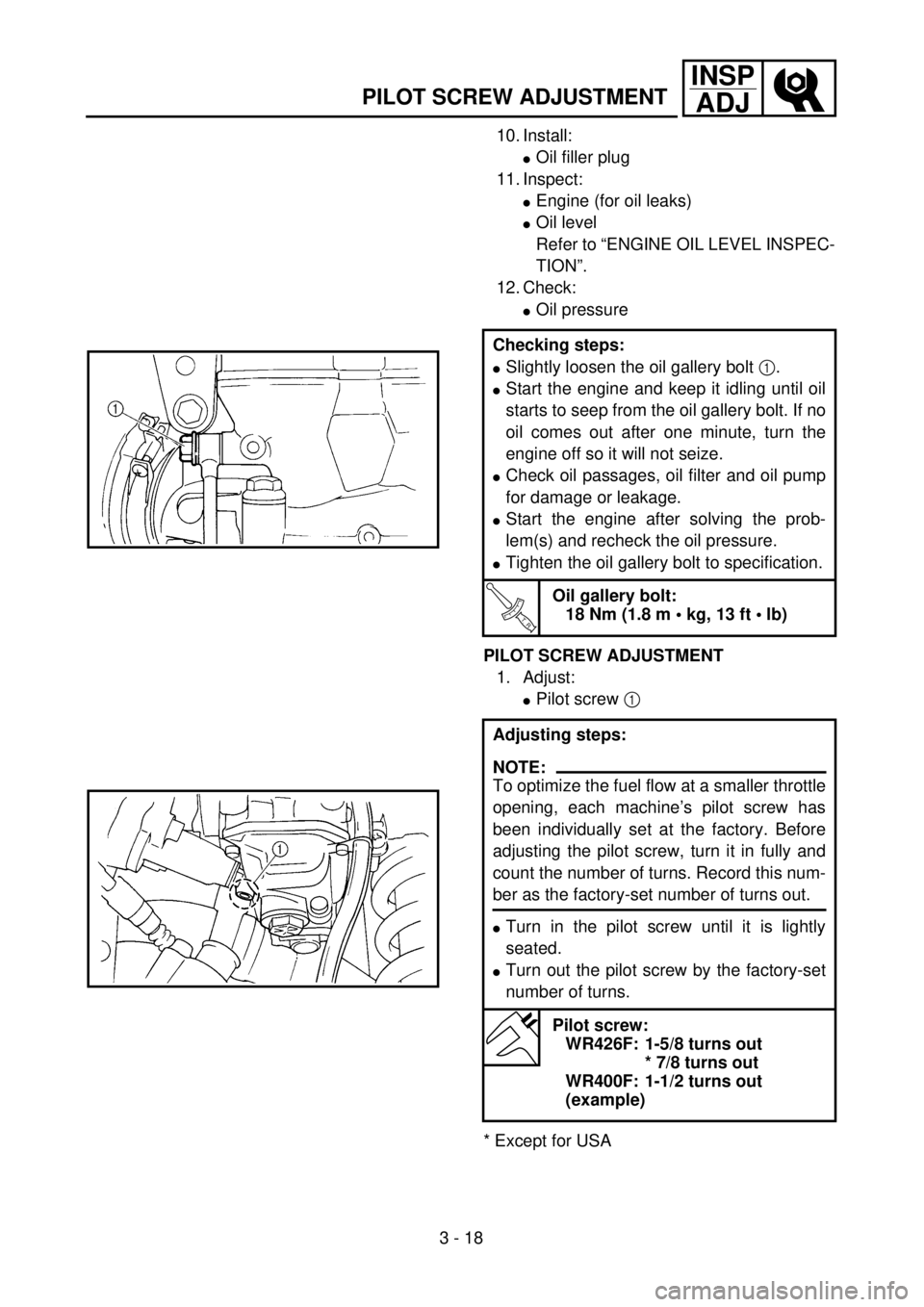
3 - 18
INSP
ADJ
PILOT SCREW ADJUSTMENT
10. Install:
lOil filler plug
11. Inspect:
lEngine (for oil leaks)
lOil level
Refer to “ENGINE OIL LEVEL INSPEC-
TION”.
12. Check:
lOil pressure
PILOT SCREW ADJUSTMENT
1. Adjust:
lPilot screw 1
* Except for USAChecking steps:
lSlightly loosen the oil gallery bolt 1.
lStart the engine and keep it idling until oil
starts to seep from the oil gallery bolt. If no
oil comes out after one minute, turn the
engine off so it will not seize.
lCheck oil passages, oil filter and oil pump
for damage or leakage.
lStart the engine after solving the prob-
lem(s) and recheck the oil pressure.
lTighten the oil gallery bolt to specification.
T R..
Oil gallery bolt:
18 Nm (1.8 m • kg, 13 ft • lb)
Adjusting steps:
NOTE:
To optimize the fuel flow at a smaller throttle
opening, each machine’s pilot screw has
been individually set at the factory. Before
adjusting the pilot screw, turn it in fully and
count the number of turns. Record this num-
ber as the factory-set number of turns out.
lTurn in the pilot screw until it is lightly
seated.
lTurn out the pilot screw by the factory-set
number of turns.
Pilot screw:
WR426F: 1-5/8 turns out
* 7/8 turns out
WR400F: 1-1/2 turns out
(example)
Page 322 of 762
3 - 44
INSP
ADJ
STEERING HEAD INSPECTION AND ADJUSTMENT
2. Inspect:
lBearing free play
Exist play ® Replace.
STEERING HEAD INSPECTION AND
ADJUSTMENT
1. Elevate the front wheel by placing a suit-
able stand under the engine.
2. Check:
lSteering shaft
Grasp the bottom of the forks and gen-
tly rock the fork assembly back and
forth.
Free play ® Adjust steering head.
3. Check:
lSteering smooth action
Turn the handlebar lock to lock.
Unsmooth action ® Adjust steering ring
nut.
4. Adjust:
lSteering ring nut
Steering ring nut adjustment steps:
lRemove the headlight.
lRemove the handlebar and handle crown.
lLoosen the ring nut 1 using the ring nut
wrench 2.
Ring nut wrench:
YU-33975/90890-01403
Page 328 of 762
3 - 47
INSP
ADJ
ELECTRICAL/SPARK PLUG INSPECTION
EC370000
ELECTRICAL
EC371001
SPARK PLUG INSPECTION
1. Remove:
lSpark plug
2. Inspect:
lElectrode 1
Wear/damage ® Replace.
lInsulator color 2
Normal condition is a medium to light
tan color.
Distinctly different color ® Check the
engine condition.
NOTE:
When the engine runs for many hours at low
speeds, the spark plug insulator will become
sooty, even if the engine and carburetor are in
good operating condition.
3. Measure:
lPlug gap a
Use a wire gauge or thickness gauge.
Out of specification ® Re-gap.
Spark plug gap:
0.7 ~ 0.8 mm (0.028 ~ 0.031 in)
4. Clean the plug with a spark plug cleaner
if necessary.
5. Tighten:
lSpark plug
NOTE:
lBefore installing a spark plug, clean the gas-
ket surface and plug surface.
lFinger-tighten a the spark plug before
torquing to specification b.
T R..13 Nm (1.3 m · kg, 9.4 ft · lb)
Page 330 of 762
3 - 48
INSP
ADJ
IGNITION TIMING CHECK
IGNITION TIMING CHECK
1. Remove:
lTiming plug 1
2. Attach:
lTiming light
lInductive tachometer
To the spark plug lead.
3. Check:
lIgnition timing
Timing light:
YM-33277-A/90890-03141
Inductive tachometer:
YU-08036-B
Engine tachometer:
90890-03113
Checking steps:
lStart the engine and let it warm up. Let the
engine run at the specified speed.
Engine speed:
1,700 ~ 1,900 r/min
lVisually check the stationary pointer a is
within the firing range b on the rotor.
Incorrect firing range ® Check rotor and
pickup assembly.
4. Install:
lTiming plug
Page 524 of 762
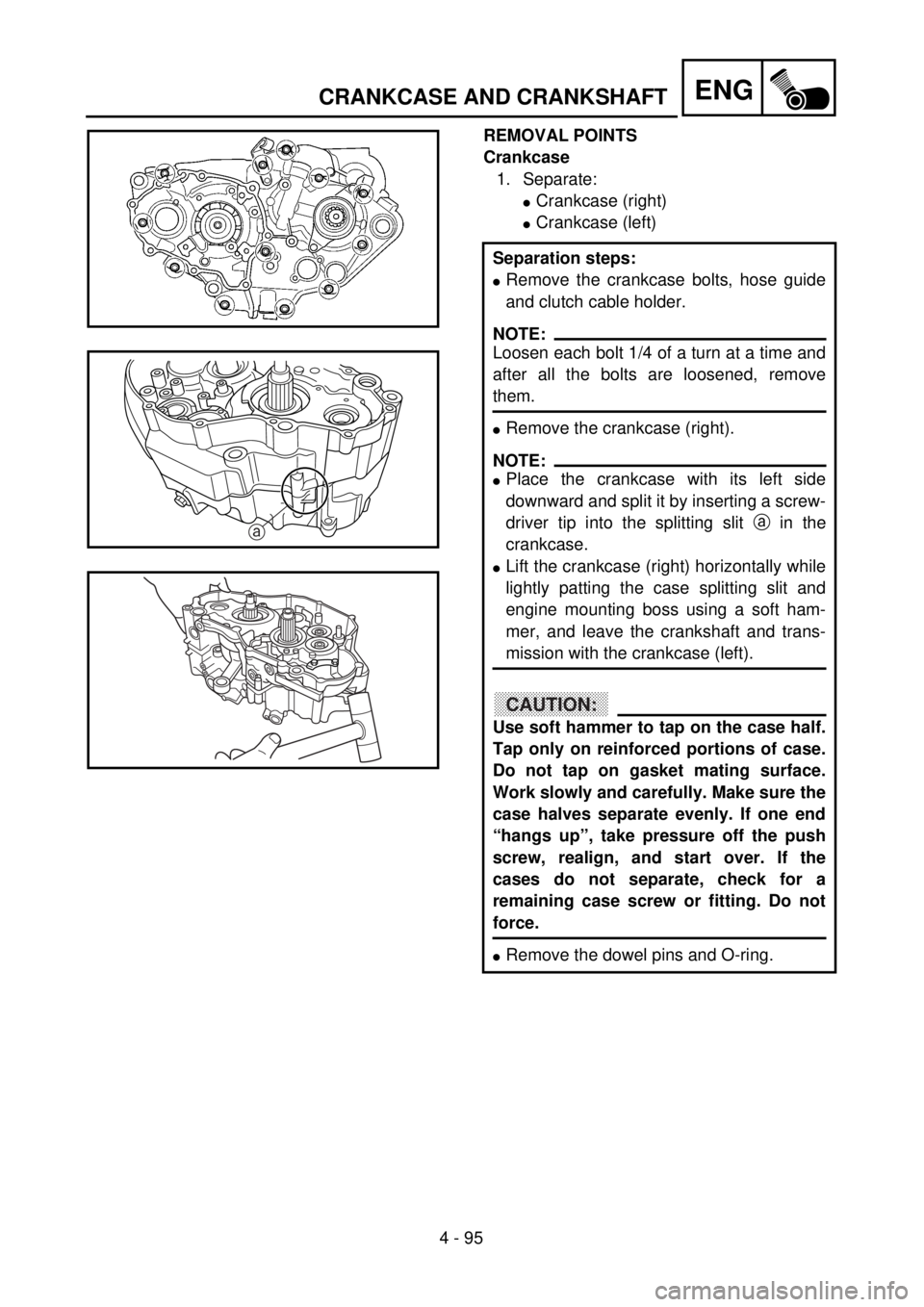
4 - 95
ENGCRANKCASE AND CRANKSHAFT
REMOVAL POINTS
Crankcase
1. Separate:
lCrankcase (right)
lCrankcase (left)
Separation steps:
lRemove the crankcase bolts, hose guide
and clutch cable holder.
NOTE:
Loosen each bolt 1/4 of a turn at a time and
after all the bolts are loosened, remove
them.
lRemove the crankcase (right).
NOTE:
lPlace the crankcase with its left side
downward and split it by inserting a screw-
driver tip into the splitting slit a in the
crankcase.
lLift the crankcase (right) horizontally while
lightly patting the case splitting slit and
engine mounting boss using a soft ham-
mer, and leave the crankshaft and trans-
mission with the crankcase (left).
CAUTION:
Use soft hammer to tap on the case half.
Tap only on reinforced portions of case.
Do not tap on gasket mating surface.
Work slowly and carefully. Make sure the
case halves separate evenly. If one end
“hangs up”, take pressure off the push
screw, realign, and start over. If the
cases do not separate, check for a
remaining case screw or fitting. Do not
force.
lRemove the dowel pins and O-ring.
a