Page 274 of 608
4 - 20
ENGCAMSHAFTS
6. Remove:
lClips
lDowel pins
lExhaust camshaft 1
lIntake camshaft 2
NOTE:
Attach a wire 3 to the timing chain to prevent
it from falling into the crankcase.
INSPECTION
Camshaft
1. Inspect:
lCam lobes
Pitting/scratches/blue discoloration ®
Replace.
2. Measure:
lCam lobes length a and b
Out of specification ® Replace.
Cam lobes length limit:
Intake:
a 31.6 mm (1.244 in)
b 22.85 mm (0.900 in)
Exhaust:
a 31.1 mm (1.224 in)
b 22.85 mm (0.900 in)
3. Measure:
lRunout (camshaft)
Out of specification ® Replace.
Runout (camshaft):
Less than 0.03 mm (0.0012 in)
4. Measure:
lCamshaft-to-cap clearance
Out of specification ® Measure bearing
diameter (camshaft)
Camshaft-to-cap clearance:
0.020 ~ 0.051 mm
(0.0008 ~ 0.0020 in)
Page 296 of 608
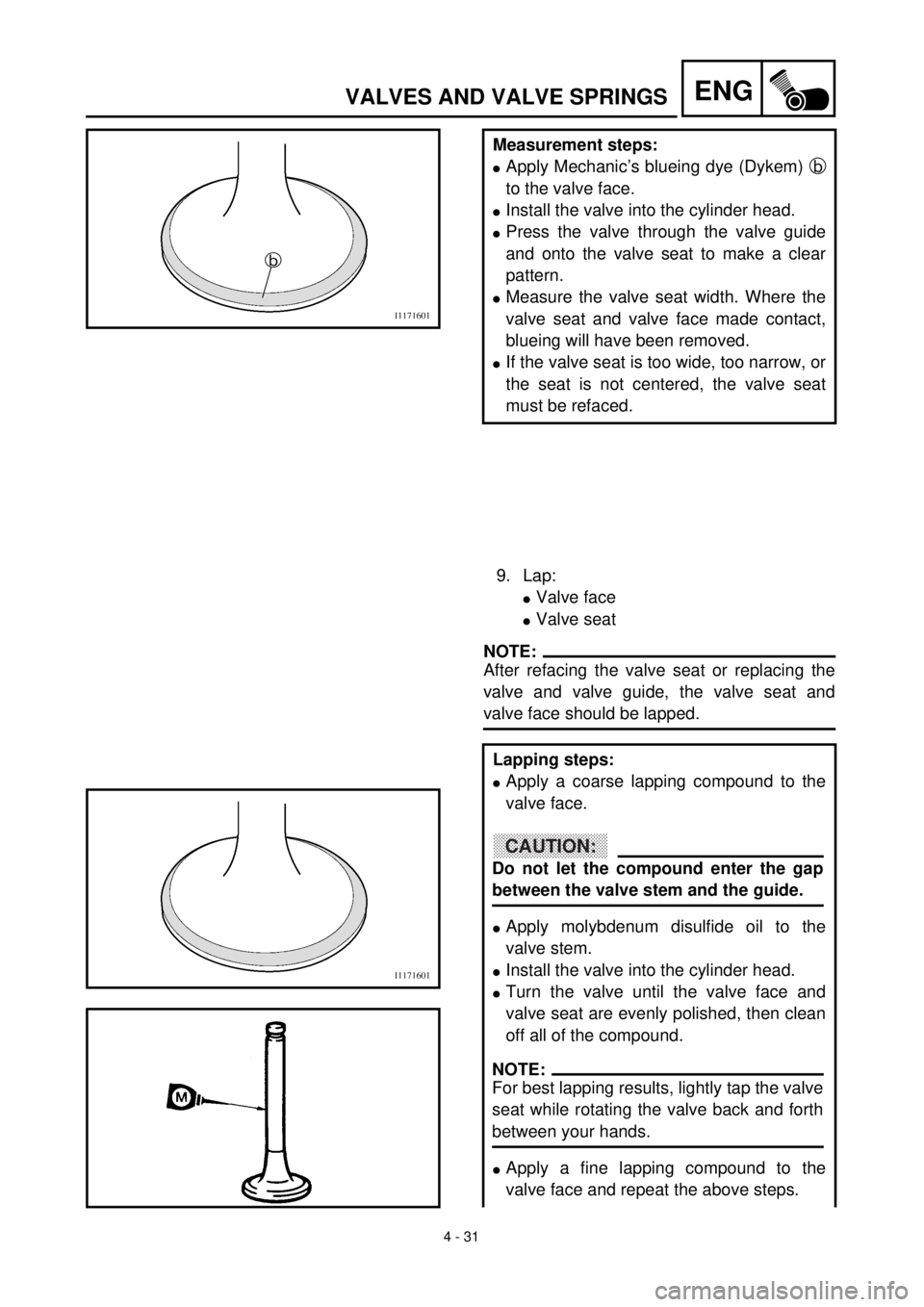
4 - 31
ENGVALVES AND VALVE SPRINGS
Measurement steps:
lApply Mechanic’s blueing dye (Dykem) b
to the valve face.
lInstall the valve into the cylinder head.
lPress the valve through the valve guide
and onto the valve seat to make a clear
pattern.
lMeasure the valve seat width. Where the
valve seat and valve face made contact,
blueing will have been removed.
lIf the valve seat is too wide, too narrow, or
the seat is not centered, the valve seat
must be refaced.
9. Lap:
lValve face
lValve seat
NOTE:
After refacing the valve seat or replacing the
valve and valve guide, the valve seat and
valve face should be lapped.
Lapping steps:
lApply a coarse lapping compound to the
valve face.
lApply molybdenum disulfide oil to the
valve stem.
lInstall the valve into the cylinder head.
lTurn the valve until the valve face and
valve seat are evenly polished, then clean
off all of the compound.
lApply a fine lapping compound to the
valve face and repeat the above steps.
CAUTION:
Do not let the compound enter the gap
between the valve stem and the guide.
NOTE:
For best lapping results, lightly tap the valve
seat while rotating the valve back and forth
between your hands.
Page 298 of 608
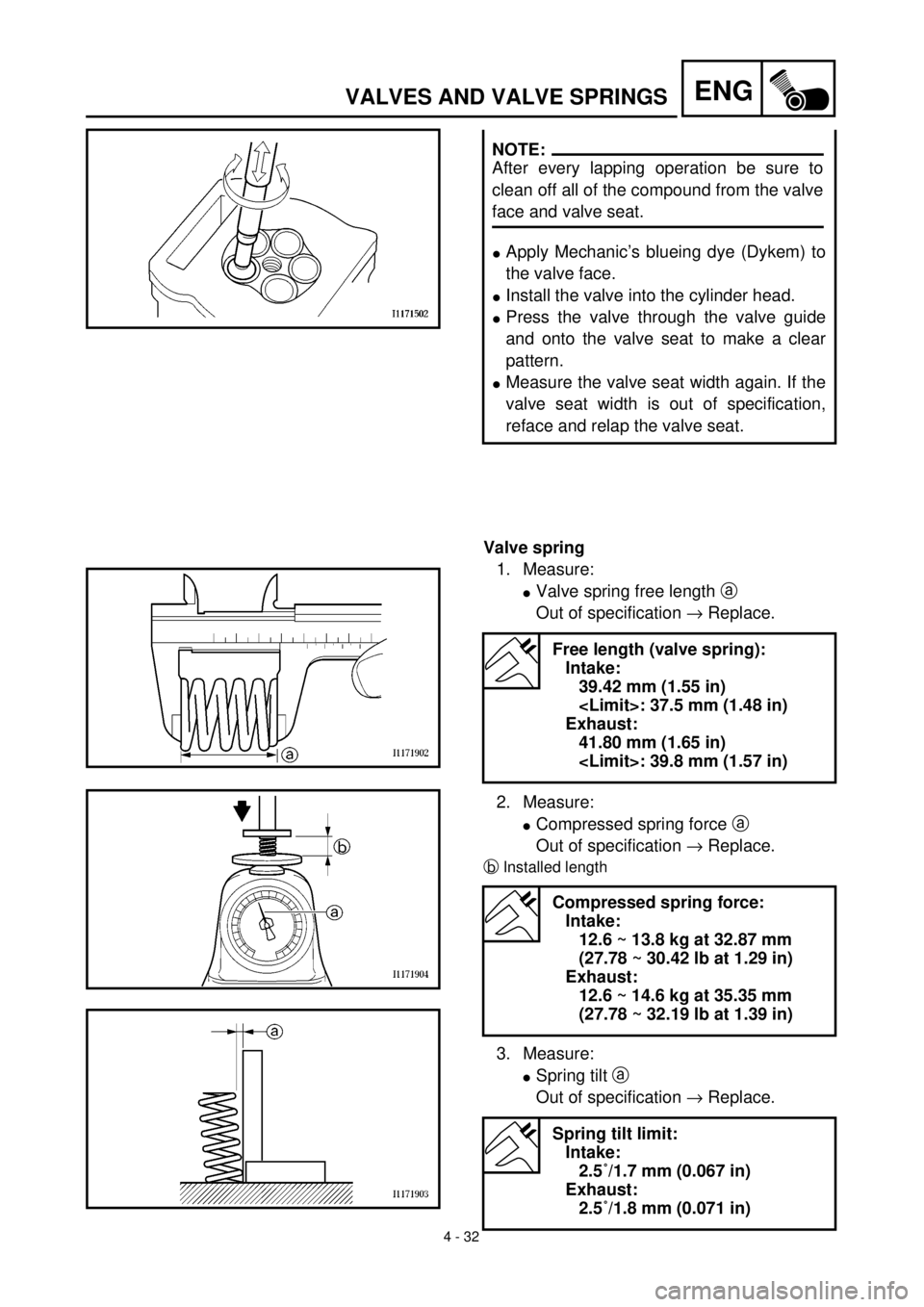
4 - 32
ENGVALVES AND VALVE SPRINGS
lApply Mechanic’s blueing dye (Dykem) to
the valve face.
lInstall the valve into the cylinder head.
lPress the valve through the valve guide
and onto the valve seat to make a clear
pattern.
lMeasure the valve seat width again. If the
valve seat width is out of specification,
reface and relap the valve seat.
NOTE:
After every lapping operation be sure to
clean off all of the compound from the valve
face and valve seat.
Valve spring
1. Measure:
lValve spring free length a
Out of specification ® Replace.
2. Measure:
lCompressed spring force a
Out of specification ® Replace.
bInstalled length
3. Measure:
lSpring tilt a
Out of specification ® Replace.
Free length (valve spring):
Intake:
39.42 mm (1.55 in)
: 37.5 mm (1.48 in)
Exhaust:
41.80 mm (1.65 in)
: 39.8 mm (1.57 in)
Compressed spring force:
Intake:
12.6 ~ 13.8 kg at 32.87 mm
(27.78 ~ 30.42 lb at 1.29 in)
Exhaust:
12.6 ~ 14.6 kg at 35.35 mm
(27.78 ~ 32.19 lb at 1.39 in)
Spring tilt limit:
Intake:
2.5˚/1.7 mm (0.067 in)
Exhaust:
2.5˚/1.8 mm (0.071 in)
Page 312 of 608
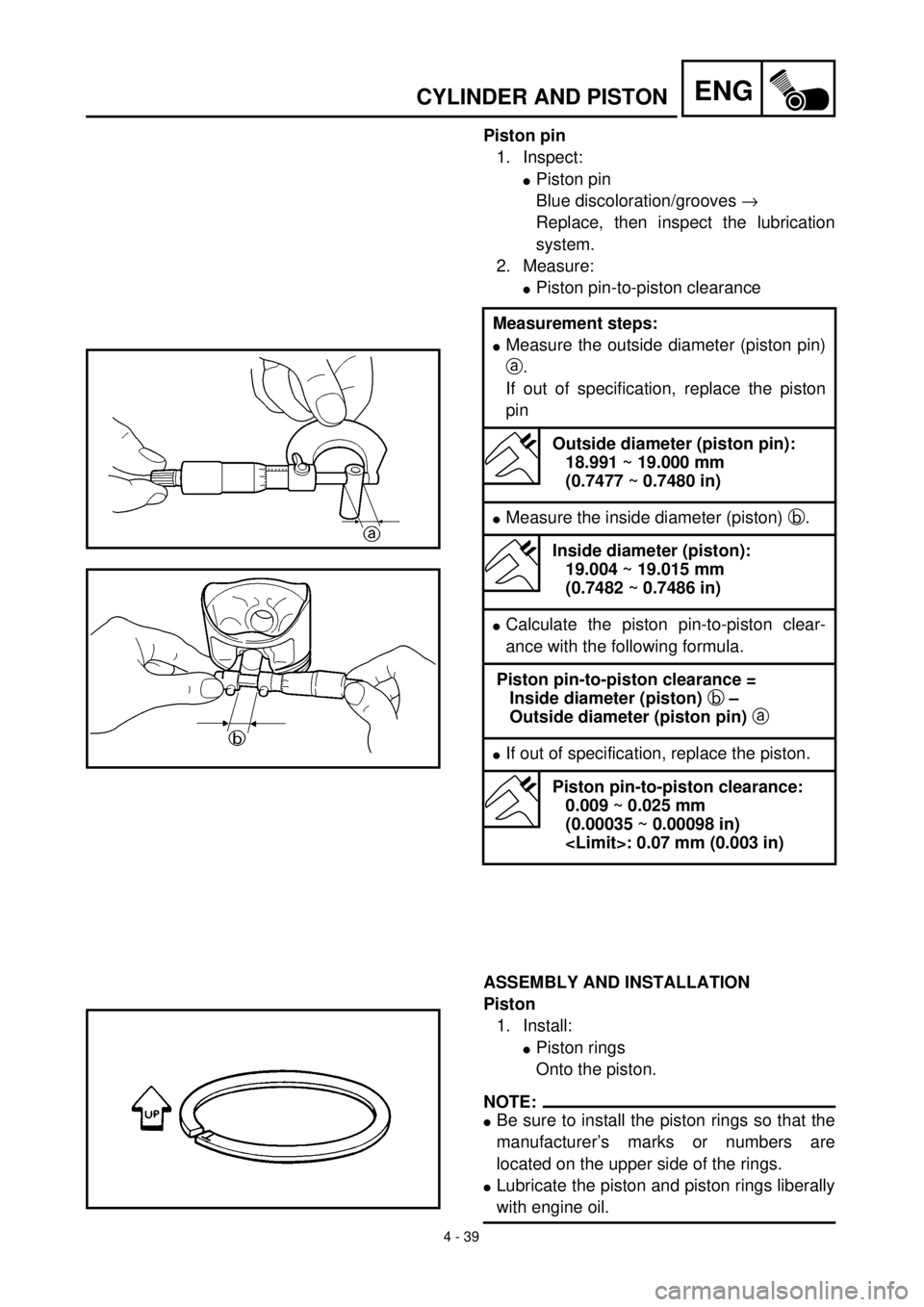
4 - 39
ENGCYLINDER AND PISTON
Piston pin
1. Inspect:
lPiston pin
Blue discoloration/grooves ®
Replace, then inspect the lubrication
system.
2. Measure:
lPiston pin-to-piston clearance
Measurement steps:
lMeasure the outside diameter (piston pin)
a.
If out of specification, replace the piston
pin
Outside diameter (piston pin):
18.991 ~ 19.000 mm
(0.7477 ~ 0.7480 in)
lMeasure the inside diameter (piston) b.
Inside diameter (piston):
19.004 ~ 19.015 mm
(0.7482 ~ 0.7486 in)
lCalculate the piston pin-to-piston clear-
ance with the following formula.
Piston pin-to-piston clearance =
Inside diameter (piston) b –
Outside diameter (piston pin) a
lIf out of specification, replace the piston.
Piston pin-to-piston clearance:
0.009 ~ 0.025 mm
(0.00035 ~ 0.00098 in)
: 0.07 mm (0.003 in)
ASSEMBLY AND INSTALLATION
Piston
1. Install:
lPiston rings
Onto the piston.
NOTE:
lBe sure to install the piston rings so that the
manufacturer’s marks or numbers are
located on the upper side of the rings.
lLubricate the piston and piston rings liberally
with engine oil.
Page 538 of 608
6 - 1
–+ELEC
ELECTRICAL COMPONENTS AND WIRING DIAGRAM
EC600000
ELECTRICAL
EC610000
ELECTRICAL COMPONENTS AND WIRING DIAGRAM
EC611000
ELECTRICAL COMPONENTS
1
“ENGINE STOP” button
2
TPS (throttle position sensor)
3
Neutral switch
4
CDI magneto
5
Ignition coil
6
Spark plug
7
CDI unit
COLOR CODE
B...................... Black
Br .................... Brown
G ..................... Green
L ...................... Blue
O ..................... Orange
P...................... Pink
R ..................... Red
EC612000
WIRING DIAGRAM
7
15
6
2 3 4
LY
BYL
B/LL
G
P
W
R
Y
B
G
BR PBrWG
RB Br WP
R/W WL/W SbW R/W Sb L/WY
B/LL Sb B OY
LB/L B OSbSb
L/WR/W
WSb
B/L
B/WB/W
B/WB/W
Br
BB
LBBY
O
N
13
4
5 2
Sb .................... Sky blue
W ..................... White
Y ...................... Yellow
B/L ................... Black/Blue
B/W .................. Black/White
L/W .................. Blue/White
R/W .................. Red/White
6
Page 550 of 608
6 - 6
–+ELECIGNITION SYSTEM
2. Inspect:
lSource coil 1 resistance
Out of specification ® Replace.
3. Inspect:
lSource coil 2 resistance
Out of specification ® Replace. Tester (+) lead ® Brown lead 1
Tester (–) lead ® Green lead 2
Source coil 1
resistanceTester selector
position
720 ~ 1,080 W
at 20 ˚C (68 ˚F)W ´ 100
Tester (+) lead ® Pink lead 1
Tester (–) lead ® Black lead 2
Source coil 2
resistanceTester selector
position
44 ~ 66 W at
20 ˚C (68 ˚F)W ´ 10
NEUTRAL SWITCH INSPECTION
1. Inspect:
lNeutral switch conduct
No continuity while in neutral ® Replace.
Continuity while in gear ® Replace.
EC628000
CDI UNIT INSPECTION
Check all electrical components. If no fault is
found, replace the CDI unit. Then check the
electrical components again.Tester (+) lead ® Sky blue lead 1
Tester (–) lead ® Ground
Sb
1GroundTester selec-
tor position
NEUTRALW ´ 1INGEAR
–+ W´1
1
R/W
W Sb L/W
Page 556 of 608
6 - 8
–+ELECTPS (THROTTLE POSITION SENSOR) SYSTEM
EC624000
COUPLERS AND LEADS CONNECTION
INSPECTION
1. Check:
lCouplers and leads connection
Rust/dust/looseness/short-circuit ®
Repair or replace.
TPS COIL INSPECTION
1. Inspect:
lTPS coil resistance
Out of specification ® Replace.
2. Loosen:
lThrottle stop screw
NOTE:
Turn out the throttle stop screw until the throt-
tle shaft is in the full close position.Tester (+) lead ® Blue lead 1
Tester (–) lead ® Black lead 2
TPS coil
resistanceTester selector
position
4 ~ 6 kW at
20 ˚C (68 ˚F)kW ´ 1
3. Inspect:
lTPS coil variable resistance
Check that the resistance in increased
as the throttle grip is moved from the
full close position to the full open posi-
tion.
Out of specification ® Replace.
Tester (+) lead ® Yellow lead 1
Tester (–) lead ® Black lead 2
TPS coil variable
resistanceTester selec-
tor position
Full closedFull opened
kW ´ 1 0 ~ 2 kW at
20 ˚C
(68 ˚F)4 ~ 6 kW at
20 ˚C
(68 ˚F)
Page 560 of 608
6 - 10
–+ELECTPS (THROTTLE POSITION SENSOR) SYSTEM
6. Adjust:
lTPS coil resistance at idle speed
Adjustment steps:
Adjust the angle of the TPS 1 to obtain
the resistance calculated (example: 650 ~
750 W)
Tester (+) lead ® Yellow lead 2
Tester (–) lead ® Black lead 3
7. Tighten:
lScrew (TPS) 1
8. Install:
lTPS coupler
EC694000
TPS INPUT VOLTAGE INSPECTION
1. Disconnect the TPS coupler.
2. Start the engine.
3. Inspect:
lTPS input voltage
Out of specification ® Replace the CDI
unit.
Tester (+) lead ® Blue lead 1
Tester (–) lead ® Black lead 2
TPS input
voltageTester selector
position
4 ~ 6 V DCV-20