Page 11 of 52
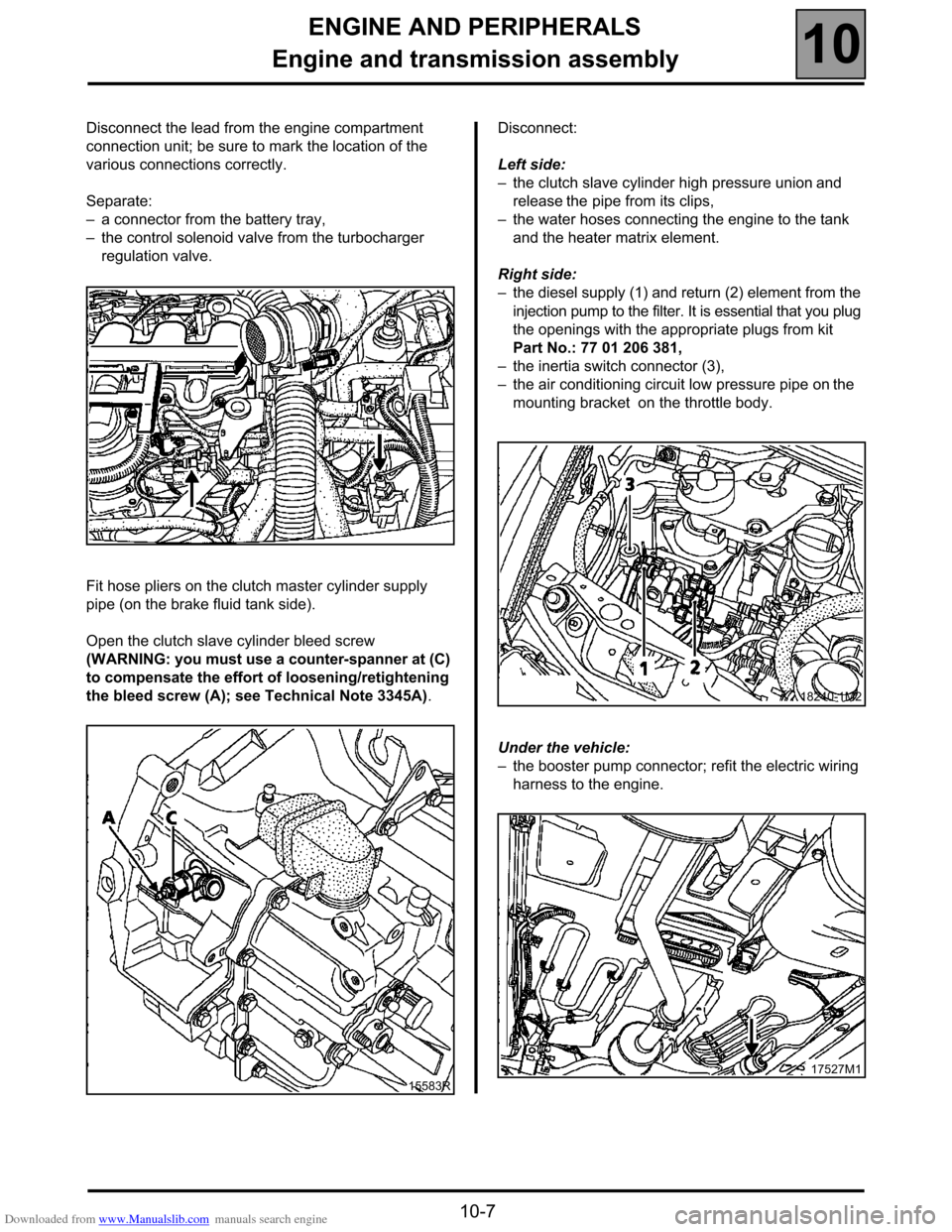
Downloaded from www.Manualslib.com manuals search engine ENGINE AND PERIPHERALS
Engine and transmission assembly
10
10-7
Disconnect the lead from the engine compartment
connection unit; be sure to mark the location of the
various connections correctly.
Separate:
–a connector from the battery tray,
–the control solenoid valve from the turbocharger
regulation valve.
Fit hose pliers on the clutch master cylinder supply
pipe (on the brake fluid tank side).
Open the clutch slave cylinder bleed screw
(WARNING: you must use a counter-spanner at (C)
to compensate the effort of loosening/retightening
the bleed screw (A); see Technical Note 3345A).Disconnect:
Left side:
–the clutch slave cylinder high pressure union and
release the pipe from its clips,
–the water hoses connecting the engine to the tank
and the heater matrix element.
Right side:
–the diesel supply (1) and return (2) element from the
injection pump to the filter. It is essential that you plug
the openings with the appropriate plugs from kit
Part No.: 77 01 206 381,
–the inertia switch connector (3),
–the air conditioning circuit low pressure pipe on the
mounting bracket on the throttle body.
Under the vehicle:
–the booster pump connector; refit the electric wiring
harness to the engine.
15583R
18240-1M2
17527M1
Page 24 of 52
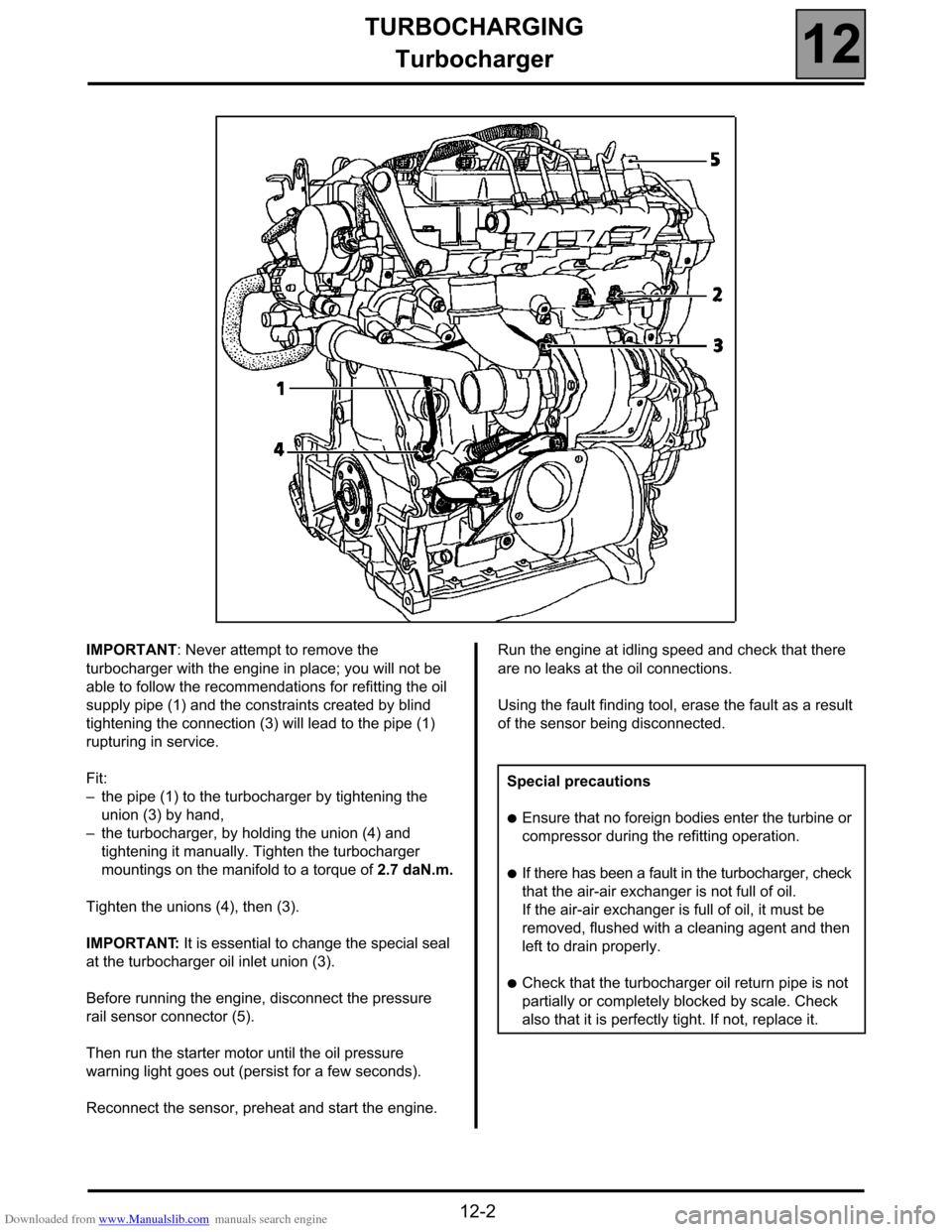
Downloaded from www.Manualslib.com manuals search engine TURBOCHARGING
Turbocharger
12
12-2
IMPORTANT: Never attempt to remove the
turbocharger with the engine in place; you will not be
able to follow the recommendations for refitting the oil
supply pipe (1) and the constraints created by blind
tightening the connection (3) will lead to the pipe (1)
rupturing in service.
Fit:
–the pipe (1) to the turbocharger by tightening the
union (3) by hand,
–the turbocharger, by holding the union (4) and
tightening it manually. Tighten the turbocharger
mountings on the manifold to a torque of 2.7 daN.m.
Tighten the unions (4), then (3).
IMPORTANT: It is essential to change the special seal
at the turbocharger oil inlet union (3).
Before running the engine, disconnect the pressure
rail sensor connector (5).
Then run the starter motor until the oil pressure
warning light goes out (persist for a few seconds).
Reconnect the sensor, preheat and start the engine.Run the engine at idling speed and check that there
are no leaks at the oil connections.
Using the fault finding tool, erase the fault as a result
of the sensor being disconnected.
Special precautions
●Ensure that no foreign bodies enter the turbine or
compressor during the refitting operation.
●If there has been a fault in the turbocharger, check
that the air-air exchanger is not full of oil.
If the air-air exchanger is full of oil, it must be
removed, flushed with a cleaning agent and then
left to drain properly.
●Check that the turbocharger oil return pipe is not
partially or completely blocked by scale. Check
also that it is perfectly tight. If not, replace it.
Page 28 of 52
Downloaded from www.Manualslib.com manuals search engine FUEL MIXTURE
Air intake
12
12-6
Remove:
–the mounting bolt from the low pressure air
conditioning pipe bracket (3),
–the mounting bolts (4) from the throttle body on the
engine housing. Use a 13 mm dowel, a cardan joint
and small extension. If necessary, remove the pipes
to access the bolts.
WARNING: avoid loosening the four self-tapping bolts
(A) which attach the top to the unit body.Remove the connection pipe (5) between the throttle
body and the inlet manifold,
If necessary, unclip the electrical wiring in front of the
damper unit to ease the downwards release of this
unit.
REFITTING
Proceed in the reverse order from removal.
Tighten the mounting clips to 5.5 daN.m.
Check that there are no stored faults using a fault
finding tool. Erase them if necessary.
Page 39 of 52
Downloaded from www.Manualslib.com manuals search engine COOLING SYSTEM
Coolant pump
19
19-3
Coolant pump
REMOVAL
Put the vehicle on a 2 post lift.
Disconnect the battery.
Bleed the engine cooling circuit and engine oil; do not
refit the oil drain plug.
Remove:
–the front right wheel,
–the right-hand wheel arch cover.
Remove the four mounting bolts of the coolant pump
cover.
Lock the crankshaft using a screwdriver in the starter
crown.
Remove the 30 hub lock nut from the coolant pump.Remove the coolant pump sprocket using the
U 14 L FACOM hub extractor
REFITTING
Replace the coolant pump.
WARNING: the rest of the coolant will drop into the
engine housing.
Ensure that the mating surface on the pump is clean
and that the coolant escapes from the engine housing
(oil change).
Refitting is the reverse of removal.
ESSENTIAL SPECIAL TOOLING
FACOM U 14 L sprocket extractor
14572-1S
14572S
18001M
Page 44 of 52
Downloaded from www.Manualslib.com manuals search engine MANUAL GEARBOX
Lubricants
21
21-3
Lubricants
OIL CAPACITY :
–Maximum: 2.8 l
–Minimum: 2.3 l
OIL LEVEL
The oil level is adjusted using a locally manufactured
dipstick, inserting into the oil filler hole (2) (see
Technical Note 2579A).
To check the level it is necessary to remove the left
hand front wheel and the left hand wheel arch cover.
The oil can also be changed and refilled with the
recommended quantity.
1 Drain plug
2 Fuel filler cap
WARNING: the fuel filler cap (2) should not be used to
check the level by overfilling; using too much oil may
damage the seals and overheat the oil. Marks to graduate:
–B: 22 ± 0.5 mm
–C: 30 ± 0.5 mm
95321M
Page 51 of 52
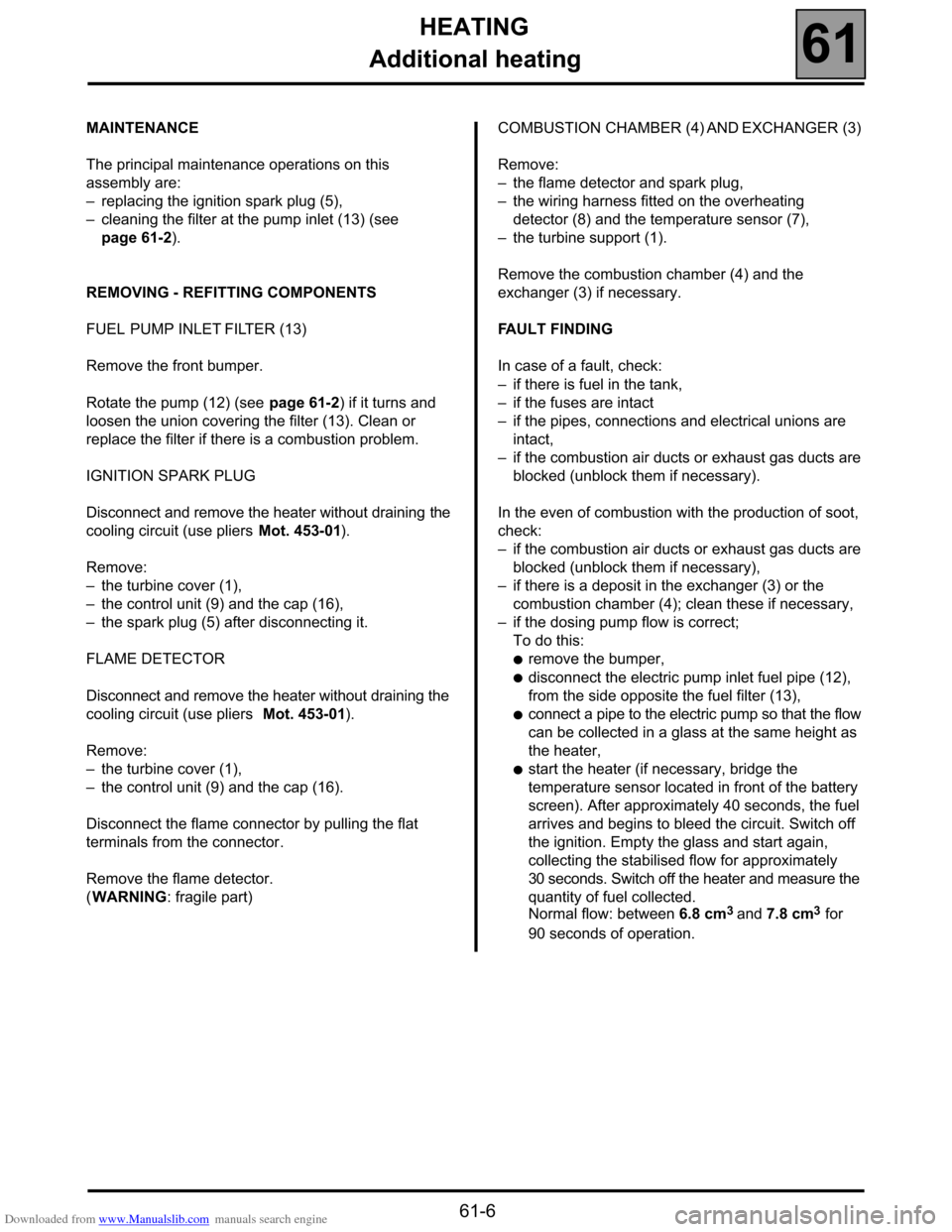
Downloaded from www.Manualslib.com manuals search engine HEATING
Additional heating
61
61-6
MAINTENANCE
The principal maintenance operations on this
assembly are:
–replacing the ignition spark plug (5),
–cleaning the filter at the pump inlet (13) (see
page 61-2).
REMOVING - REFITTING COMPONENTS
FUEL PUMP INLET FILTER (13)
Remove the front bumper.
Rotate the pump (12) (see page 61-2) if it turns and
loosen the union covering the filter (13). Clean or
replace the filter if there is a combustion problem.
IGNITION SPARK PLUG
Disconnect and remove the heater without draining the
cooling circuit (use pliers Mot. 453-01).
Remove:
–the turbine cover (1),
–the control unit (9) and the cap (16),
–the spark plug (5) after disconnecting it.
FLAME DETECTOR
Disconnect and remove the heater without draining the
cooling circuit (use pliers Mot. 453-01).
Remove:
–the turbine cover (1),
–the control unit (9) and the cap (16).
Disconnect the flame connector by pulling the flat
terminals from the connector.
Remove the flame detector.
(WARNING: fragile part)COMBUSTION CHAMBER (4) AND EXCHANGER (3)
Remove:
–the flame detector and spark plug,
–the wiring harness fitted on the overheating
detector (8) and the temperature sensor (7),
–the turbine support (1).
Remove the combustion chamber (4) and the
exchanger (3) if necessary.
FAULT FINDING
In case of a fault, check:
–if there is fuel in the tank,
–if the fuses are intact
–if the pipes, connections and electrical unions are
intact,
–if the combustion air ducts or exhaust gas ducts are
blocked (unblock them if necessary).
In the even of combustion with the production of soot,
check:
–if the combustion air ducts or exhaust gas ducts are
blocked (unblock them if necessary),
–if there is a deposit in the exchanger (3) or the
combustion chamber (4); clean these if necessary,
–if the dosing pump flow is correct;
To do this:
●remove the bumper,
●disconnect the electric pump inlet fuel pipe (12),
from the side opposite the fuel filter (13),
●connect a pipe to the electric pump so that the flow
can be collected in a glass at the same height as
the heater,
●start the heater (if necessary, bridge the
temperature sensor located in front of the battery
screen). After approximately 40 seconds, the fuel
arrives and begins to bleed the circuit. Switch off
the ignition. Empty the glass and start again,
collecting the stabilised flow for approximately
30 seconds. Switch off the heater and measure the
quantity of fuel collected.
Normal flow: between 6.8 cm
3 and 7.8 cm3 for
90 seconds of operation.