Page 710 of 1463
M161 ENGINE CONTROLS 1F2-61
Notice
Replace the fuel pump relay if the measured value is over
9A. Notice
Check the fuel filter and fuel line when the fuel delivery is
not within specified value.
Measure the Current Consumption of Fuel Pump
1. Remove the fuel pump relay from fuse and relay box in
trunk, and turn the ignition switch to "ON" position.
2. Using a multi-tester, measure the current consumption by
connecting the terminal No.1 and No.3 of pump.
Measure the Fuel Delivery From the Fuel Pump
1. Disconnect the return pipe from fuel distributor and insert
the appropriate hose into it.
2 . Place the hose end into the beaker with the minimum capacity
of 1Liter.
3. Turn the ignition switch to "ON" position.
4. Connect the terminal No.33 and No.5 of ECU with a service
wire.
5. Measure the fuel delivery from the fuel pump.
1Liter/max.35sec. Specifed Value
5 - 9A Specifed Value
Page 721 of 1463
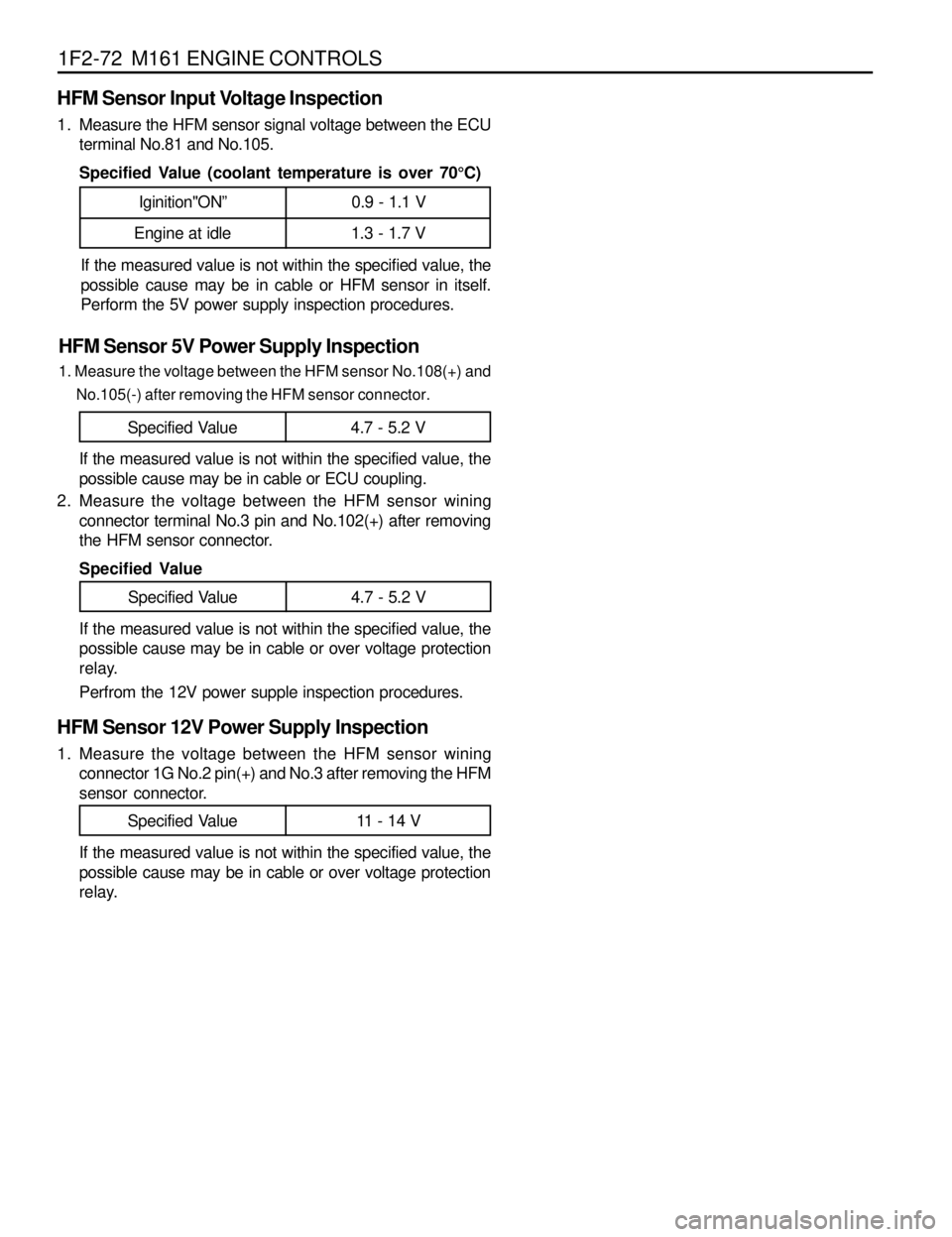
1F2-72 M161 ENGINE CONTROLS
If the measured value is not within the specified value, the
possible cause may be in cable or HFM sensor in itself.
Perform the 5V power supply inspection procedures.
HFM Sensor 5V Power Supply Inspection
1. Measure the voltage between the HFM sensor No.108(+) and
No.105(-) after removing the HFM sensor connector.
HFM Sensor Input Voltage Inspection
1. Measure the HFM sensor signal voltage between the ECU
terminal No.81 and No.105.
Specified Value (coolant temperature is over 70°C)
If the measured value is not within the specified value, the
possible cause may be in cable or ECU coupling.
Iginition"ON” 0.9 - 1.1 V
Engine at idle 1.3 - 1.7 V
Specified Value 4.7 - 5.2 V
2. Measure the voltage between the HFM sensor wining
connector terminal No.3 pin and No.102(+) after removing
the HFM sensor connector.
Specified Value
If the measured value is not within the specified value, the
possible cause may be in cable or over voltage protection
relay.
Perfrom the 12V power supple inspection procedures.
Specified Value 4.7 - 5.2 V
HFM Sensor 12V Power Supply Inspection
1. Measure the voltage between the HFM sensor wining
connector 1G No.2 pin(+) and No.3 after removing the HFM
sensor connector.
If the measured value is not within the specified value, the
possible cause may be in cable or over voltage protection
relay.
Specified Value 11 - 14 V
Page 851 of 1463
2C-14 FRONT SUSPENSION
ECS (ECU)
1 Electronically Controlled Suspension (ECU)
2 Connector
3 Bolts (2 pieces)
Removal & Installation Procedure
1. Disconnect each connectors from the console box and
remove the console box.
2. Disconnect ECU connector.
3. Unscrew 10mm x 2 bolts and remove ECS (ECU).
4. Installation should follow the removal procedure in the
reverse order.
4 Parking Brake Lever
5 Over Voltage Protection Relay
Page 961 of 1463
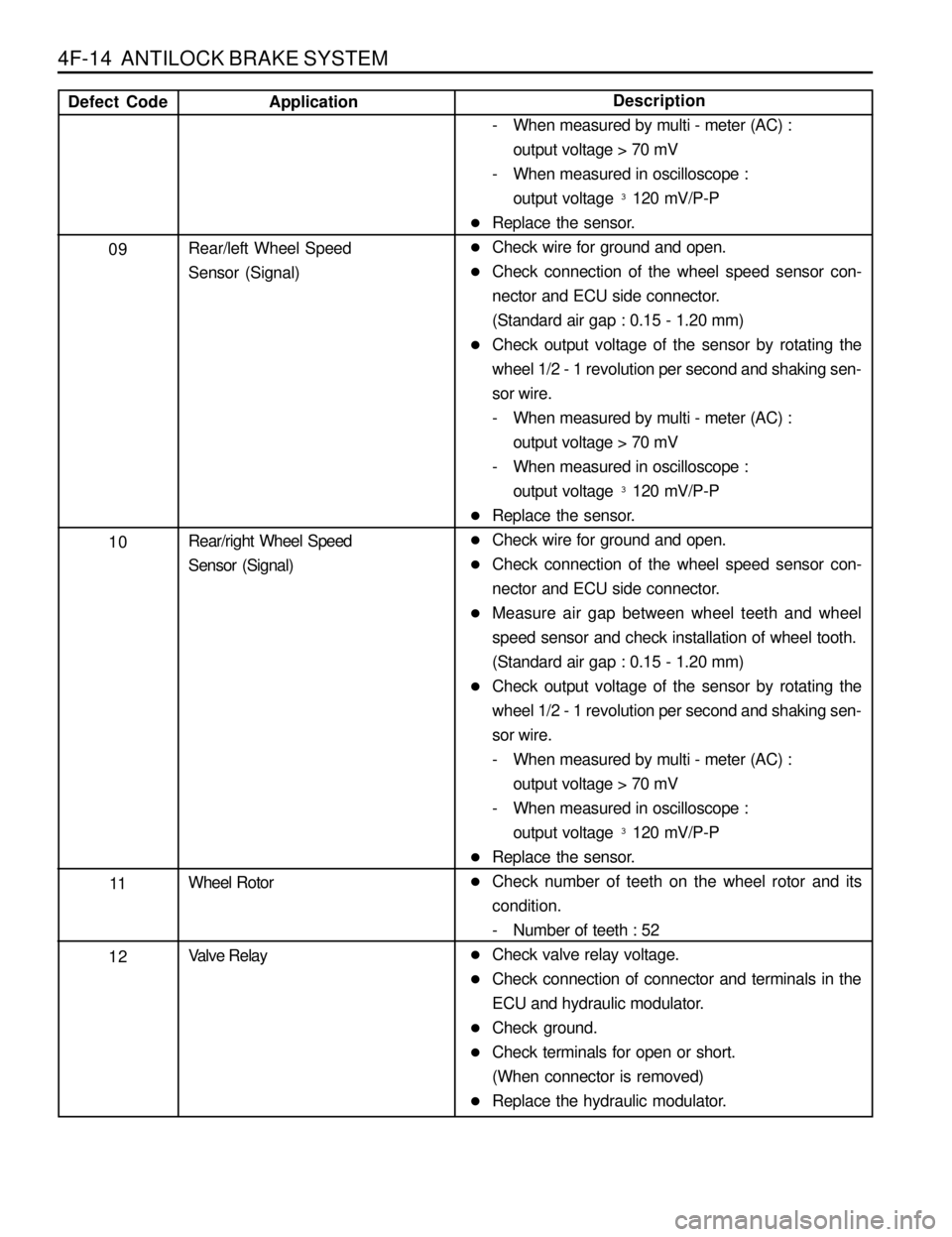
4F-14 ANTILOCK BRAKE SYSTEM
Description
- When measured by multi - meter (AC) :
output voltage > 70 mV
- When measured in oscilloscope :
output voltage ³ 120 mV/P-P
lReplace the sensor.
lCheck wire for ground and open.
lCheck connection of the wheel speed sensor con-
nector and ECU side connector.
(Standard air gap : 0.15 - 1.20 mm)
lCheck output voltage of the sensor by rotating the
wheel 1/2 - 1 revolution per second and shaking sen-
sor wire.
- When measured by multi - meter (AC) :
output voltage > 70 mV
- When measured in oscilloscope :
output voltage ³ 120 mV/P-P
lReplace the sensor.
lCheck wire for ground and open.
lCheck connection of the wheel speed sensor con-
nector and ECU side connector.
lMeasure air gap between wheel teeth and wheel
speed sensor and check installation of wheel tooth.
(Standard air gap : 0.15 - 1.20 mm)
lCheck output voltage of the sensor by rotating the
wheel 1/2 - 1 revolution per second and shaking sen-
sor wire.
- When measured by multi - meter (AC) :
output voltage > 70 mV
- When measured in oscilloscope :
output voltage ³ 120 mV/P-P
lReplace the sensor.
lCheck number of teeth on the wheel rotor and its
condition.
- Number of teeth : 52
lCheck valve relay voltage.
lCheck connection of connector and terminals in the
ECU and hydraulic modulator.
lCheck ground.
lCheck terminals for open or short.
(When connector is removed)
lReplace the hydraulic modulator. Defect Code
09
10
11
12Application
Rear/left Wheel Speed
Sensor (Signal)
Rear/right Wheel Speed
Sensor (Signal)
Wheel Rotor
Valve Relay
Page 963 of 1463
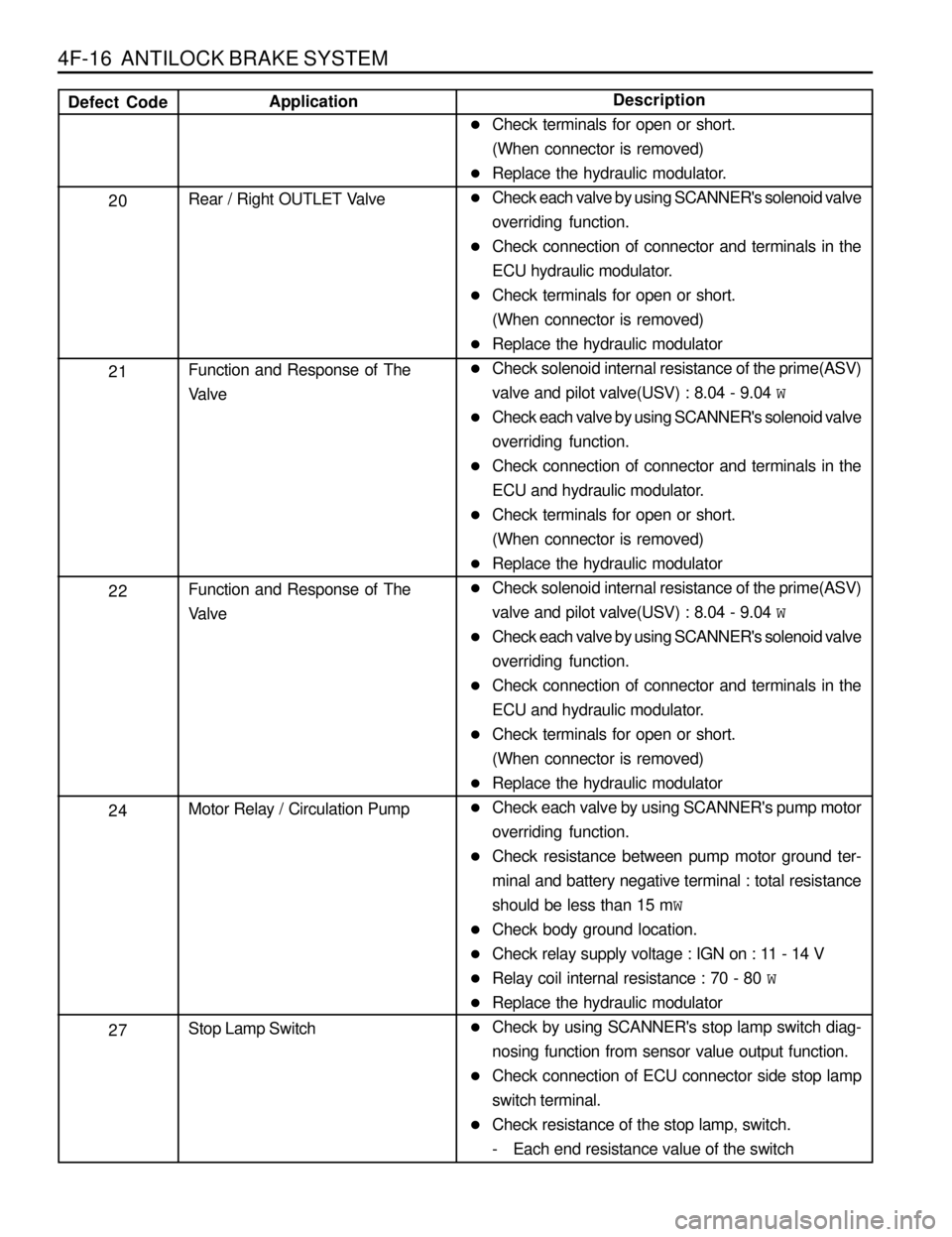
4F-16 ANTILOCK BRAKE SYSTEM
Description
lCheck terminals for open or short.
(When connector is removed)
lReplace the hydraulic modulator.
lCheck each valve by using SCANNER's solenoid valve
overriding function.
lCheck connection of connector and terminals in the
ECU hydraulic modulator.
lCheck terminals for open or short.
(When connector is removed)
lReplace the hydraulic modulator
lCheck solenoid internal resistance of the prime(ASV)
valve and pilot valve(USV) : 8.04 - 9.04 W
lCheck each valve by using SCANNER's solenoid valve
overriding function.
lCheck connection of connector and terminals in the
ECU and hydraulic modulator.
lCheck terminals for open or short.
(When connector is removed)
lReplace the hydraulic modulator
lCheck solenoid internal resistance of the prime(ASV)
valve and pilot valve(USV) : 8.04 - 9.04 W
lCheck each valve by using SCANNER's solenoid valve
overriding function.
lCheck connection of connector and terminals in the
ECU and hydraulic modulator.
lCheck terminals for open or short.
(When connector is removed)
lReplace the hydraulic modulator
lCheck each valve by using SCANNER's pump motor
overriding function.
lCheck resistance between pump motor ground ter-
minal and battery negative terminal : total resistance
should be less than 15 mW
lCheck body ground location.
lCheck relay supply voltage : IGN on : 11 - 14 V
lRelay coil internal resistance : 70 - 80 W
lReplace the hydraulic modulator
lCheck by using SCANNER's stop lamp switch diag-
nosing function from sensor value output function.
lCheck connection of ECU connector side stop lamp
switch terminal.
lCheck resistance of the stop lamp, switch.
- Each end resistance value of the switch Application
Rear / Right OUTLET Valve
Function and Response of The
Valve
Function and Response of The
Valve
Motor Relay / Circulation Pump
Stop Lamp Switch
Defect Code
20
21
22
24
27
Page 1239 of 1463
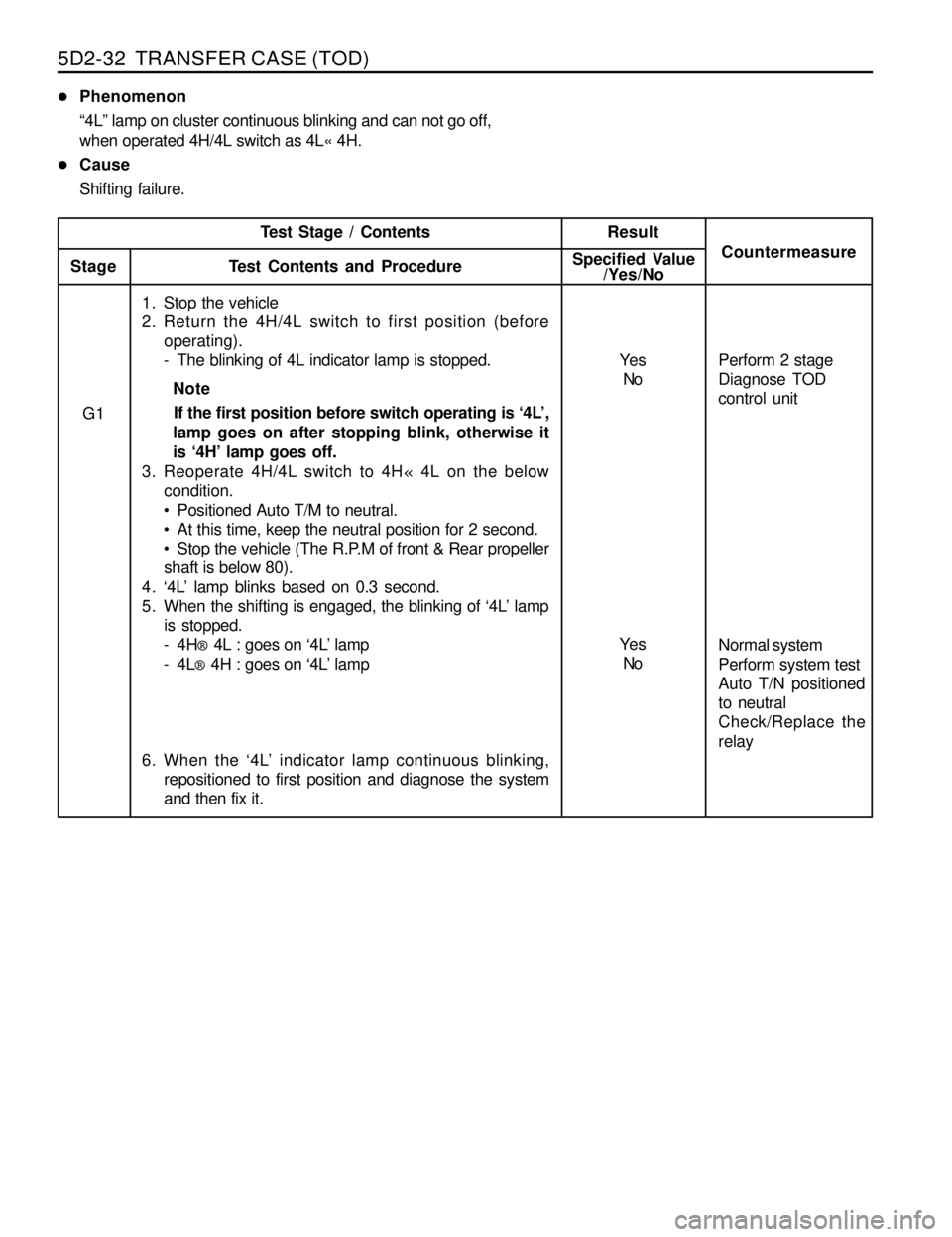
5D2-32 TRANSFER CASE (TOD)
lPhenomenon
“4L” lamp on cluster continuous blinking and can not go off,
when operated 4H/4L switch as 4L« 4H.
lCause
Shifting failure.
1. Stop the vehicle
2. Return the 4H/4L switch to first position (before
operating).
- The blinking of 4L indicator lamp is stopped.
Note
If the first position before switch operating is ‘4L’,
lamp goes on after stopping blink, otherwise it
is ‘4H’ lamp goes off.
3. Reoperate 4H/4L switch to 4H«4L on the below
condition.
• Positioned Auto T/M to neutral.
• At this time, keep the neutral position for 2 second.
• Stop the vehicle (The R.P.M of front & Rear propeller
shaft is below 80).
4. ‘4L’ lamp blinks based on 0.3 second.
5. When the shifting is engaged, the blinking of ‘4L’ lamp
is stopped.
-4H®4L : goes on ‘4L’ lamp
-4L®4H : goes on ‘4L’ lamp
6. When the ‘4L’ indicator lamp continuous blinking,
repositioned to first position and diagnose the system
and then fix it.Ye s
No
G1
Ye s
No Test Stage / Contents
Result
Stage Test Contents and ProcedureSpecified Value
/Yes/NoCountermeasure
Perform 2 stage
Diagnose TOD
control unit
Normal system
Perform system test
Auto T/N positioned
to neutral
Check/Replace the
relay
Page 1279 of 1463
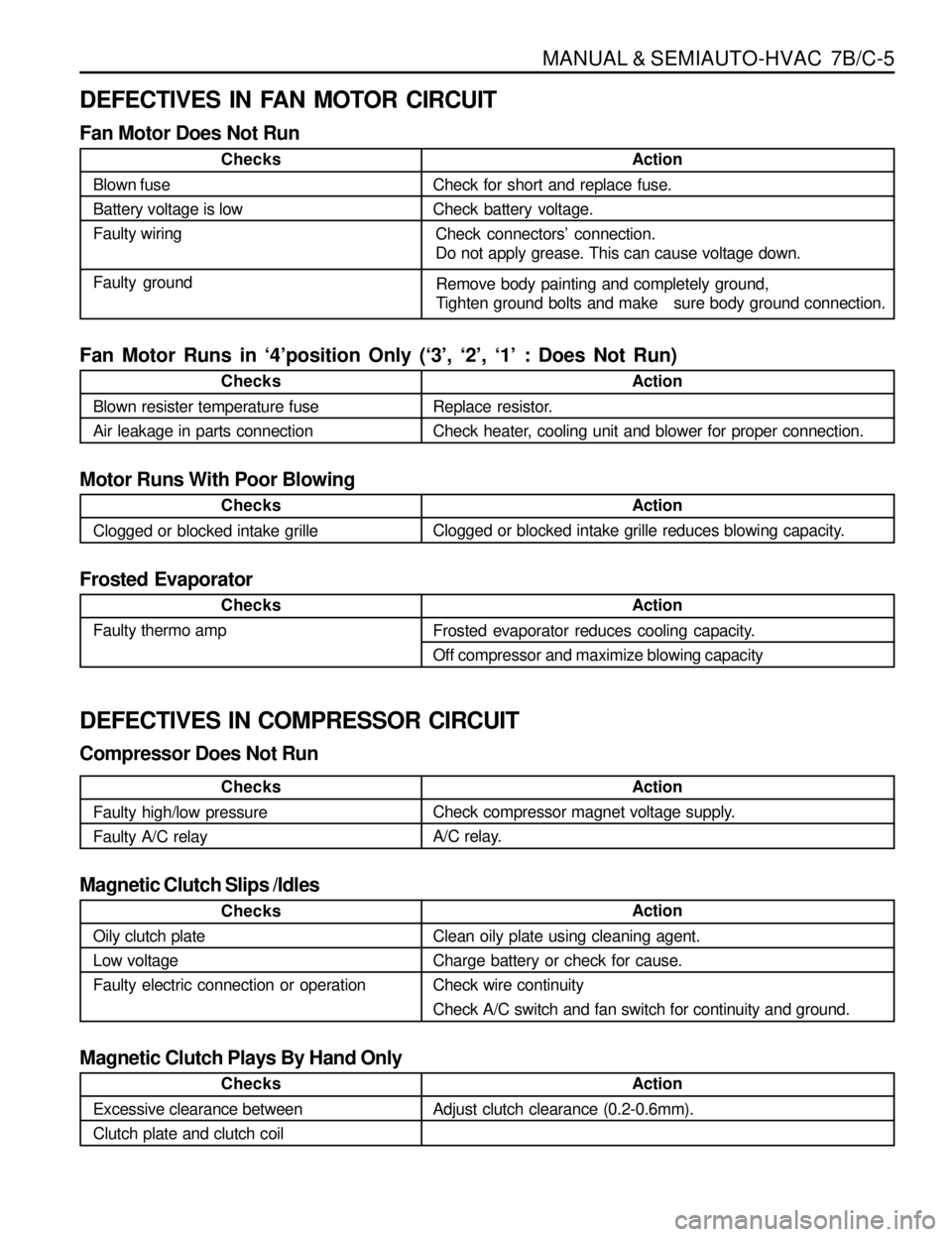
MANUAL & SEMIAUTO-HVAC 7B/C-5
Action
Clean oily plate using cleaning agent.
Charge battery or check for cause.
Check wire continuity
Check A/C switch and fan switch for continuity and ground.
DEFECTIVES IN FAN MOTOR CIRCUIT
Fan Motor Does Not Run
Checks
Blown fuse
Battery voltage is low
Faulty wiring
Faulty groundAction
Check for short and replace fuse.
Check battery voltage.
Check connectors’ connection.
Do not apply grease. This can cause voltage down.
Remove body painting and completely ground,
Tighten ground bolts and make sure body ground connection.
Checks
Blown resister temperature fuse
Air leakage in parts connection
Action
Replace resistor.
Check heater, cooling unit and blower for proper connection.
Fan Motor Runs in ‘4’position Only (‘3’, ‘2’, ‘1’ : Does Not Run)
Frosted Evaporator
DEFECTIVES IN COMPRESSOR CIRCUIT
Compressor Does Not Run
Checks
Faulty thermo ampAction
Frosted evaporator reduces cooling capacity.
Off compressor and maximize blowing capacity
Checks
Faulty high/low pressure
Faulty A/C relayAction
Check compressor magnet voltage supply.
A/C relay.
Checks
Oily clutch plate
Low voltage
Faulty electric connection or operation
Magnetic Clutch Slips /Idles
Checks
Clogged or blocked intake grilleAction
Clogged or blocked intake grille reduces blowing capacity.
Motor Runs With Poor Blowing
Checks
Excessive clearance between
Clutch plate and clutch coilAction
Adjust clutch clearance (0.2-0.6mm).
Magnetic Clutch Plays By Hand Only
Page 1323 of 1463
SUPPLEMENTAL RESTRAINT SYSTEM(SRS) 8B-19
Air Bag
Horn (Relay)
Remote Control (Electronic Circuit)
CLOCK SPRING
General Specification
Voltage
Rating Operating Voltage
Current Rating
Air Bag Circuit Resistance
Isolating Resistance
Rotating RangeDC 12V
DC 6 - 18V
10 - 30mA(6A,0.1second)
200 - 220mA
15mA
0.16 - 0.38W(-40°C - 85°C)
5MW
2.7 - 3.1 Rotation from neutral
Position to Both Sides
Notice
lClock spring can not be repaired.
lDo not disassemble or modify.
lTo adjust to the center position, rotate clockwise until it
stops and then rotate it counterclockwise 2.3 ± 0.2
revolutions and align marks. If not, airbag system can
not work normally and driver can be injured seriously.