Page 203 of 1463
1B2-14 M161 ENGINE MECHANICAL
20. Disconnect following sensors connector.
lHFM sensor.
lCoolant temperature sensor.
l2 knock sensors.
lCamshaft and crankshaft sensors.
21. After removing the ignition coil cover, disconnect the ignition
coil connector.
22. Remove the harness cover and disconnect the 6 injection
valve connectors. Disconnect the main harness.
23. Separate the hose toward engine from canister purge
solenoid valve.
24. Remove the automatic transmission oil cooler line.
Page 253 of 1463
1B2-64 M161 ENGINE MECHANICAL
7. Unscrew the bolt (3) from the armature (4) and remove
the roll pin, and remove the armature.
Installation Notice
Tightening Torque 35 Nm
8. Unscrew the nut (6) and remove the seal cover (7).
Installation Notice
Tightening Torque 60 - 70 Nm
Notice
Put the locking slot of nut toward armarture.
9. Take off the timing chain from intake camshaft sprocket.
10. Remove the cover (7), adjuster piston (9) and conical
spring (10) from intake camshaft sprocket.
11. Unscrew the bolt (11) and remove the flange shaft.
Installation Notice
Tightening Torque1st step 20 Nm
2nd step + 95°
Notice
The flange bolt is designed to be used only once, so always
replace with new one.
12. Installation should follow the removal procedure in the
reverse order.
13. Check and adjust the camshaft timing.
Page 469 of 1463
OM600 ENGINE MECHANICAL 1B3-167
6. Coat the cylinder bore, connecting rod bearing journal,
connecting rod bearing shell and piston with oil.
7. Compress the piston rings with a tensioning strap (7).
Tensioning Strap 000 589 04 14 00
8. Insert the piston assembly into the cylinder with a wooden
stick (18).
Notice
The arrow on the piston crown must point toward the front
of vehicle.
9. Insert the connecting rod bearing shells (9, 10).
Notice
Be careful of the difference in upper and lower bearing
shells and not to be changed.
10. Position the connecting rod bearings caps.
Notice
Position so that the retaining lugs are on the same side of
the connecting rod bearing(arrow).
11. Measure stretch shaft diameter (C) of the connecting rod
bolts.
Limit ‘C’ 7.1mm
Page 757 of 1463
1F3-28 OM600 ENGINE CONTROLS
Tools Required
001 589 65 09 00 Socket Wrench Insert
000 589 00 68 00 Cleaning Set
Repair Procedure
1. Clamp the nozzle holder (1) in a vice and remove the nozzle
tensioning nut (8).
Notice
Use protective jaws for clamping.
2. Disassemble the fuel injection nozzle.
Socket Wrench Insert 001 589 65 09 00
3. Clean the nozzle needle (6) and nozzle body (7) with an
abradant.
4. Clean the nozzle seat with cleaning cutter.
Cleaning Set 000 589 00 68 00
5. Immerse nozzle needle (6) and nozzle body (7) in filtered
diesel fuel. When the nozzle body is held vertical, the weight
of the nozzle needle must cause it to slide down toward the
nozzle needle seat.
6. Assemble the injection nozzle so that the tip of the thrust
(4) pin is facing toward the nozzle holder.
Tightening Torque 80 Nm
Notice
Nozzle needle (6) and nozzle body (7) should always be
replaced as a pair.
Page 788 of 1463
1G1-8 M162 ENGINE INTAKE & EXHAUST
Function Description
A pneumatically actuated resonance flap (5) is located on the
intake manifold, and will be opened and closed by load, which
operates resonance flap according to engine and controlled
by ECU and rpm.
1. Resonance flap closed (at idle/partial load : less than
3,800/rpm)
The switch valve (7) will be adjusted by ECU and resonance
falp will be colosed. By increasing air flow passage through
dividing intaking air flow toward both air collection housing
(8). This leads to a signficant increase in the torque in the
lower speed range.
2. Resonance flap open (at full load : over 3,800/rpm)
The switch valve (7) will not be adjusted by ECU and
resonance falp (5) will be open. The colllected air in the air
collection housing (8) will not be divided and intaking air
passage will be shorten.
Page 837 of 1463
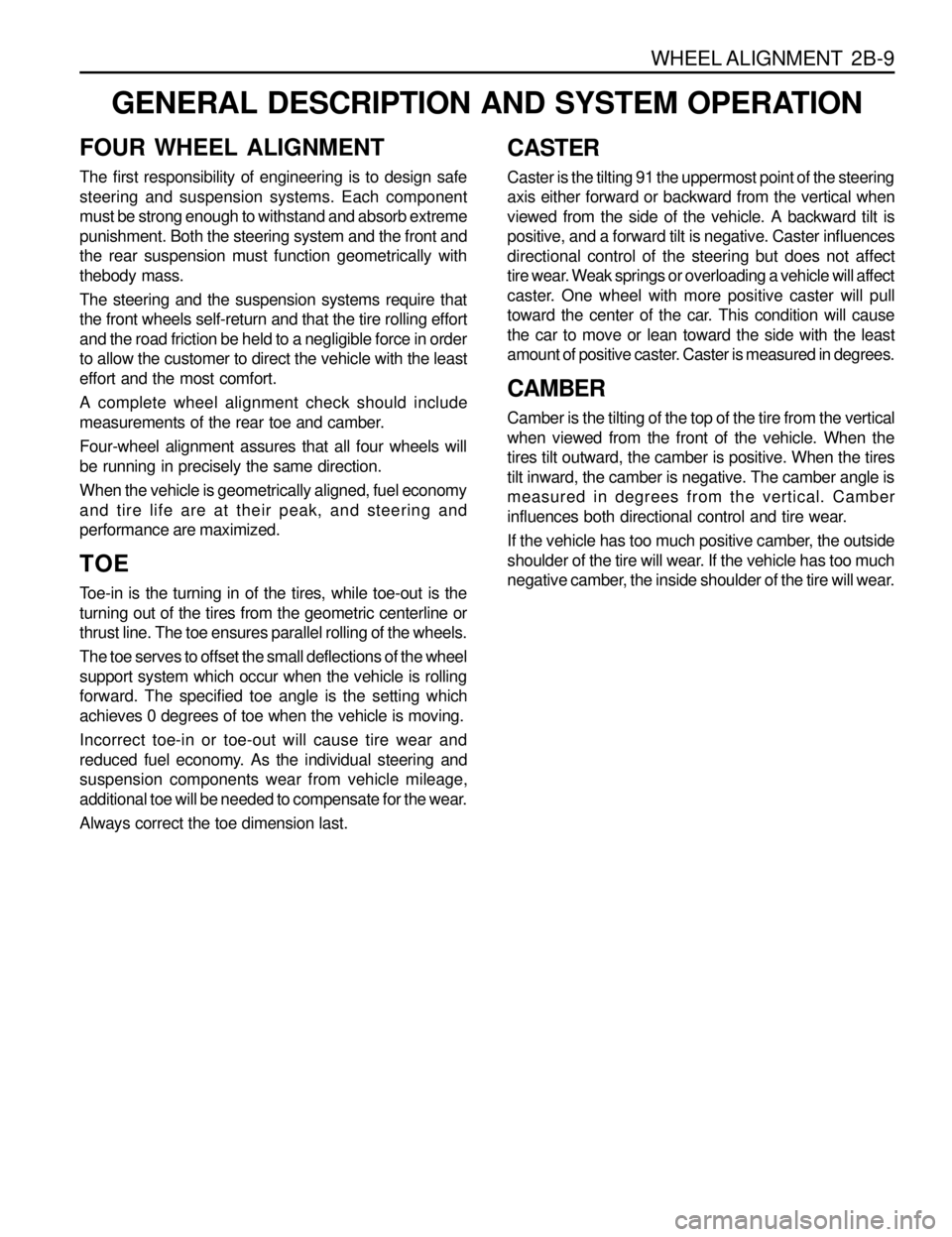
WHEEL ALIGNMENT 2B-9
GENERAL DESCRIPTION AND SYSTEM OPERATION
FOUR WHEEL ALIGNMENT
CASTER
Caster is the tilting 91 the uppermost point of the steering
axis either forward or backward from the vertical when
viewed from the side of the vehicle. A backward tilt is
positive, and a forward tilt is negative. Caster influences
directional control of the steering but does not affect
tire wear. Weak springs or overloading a vehicle will affect
caster. One wheel with more positive caster will pull
toward the center of the car. This condition will cause
the car to move or lean toward the side with the least
amount of positive caster. Caster is measured in degrees.
CAMBER
Camber is the tilting of the top of the tire from the vertical
when viewed from the front of the vehicle. When the
tires tilt outward, the camber is positive. When the tires
tilt inward, the camber is negative. The camber angle is
measured in degrees from the vertical. Camber
influences both directional control and tire wear.
If the vehicle has too much positive camber, the outside
shoulder of the tire will wear. If the vehicle has too much
negative camber, the inside shoulder of the tire will wear. The first responsibility of engineering is to design safe
steering and suspension systems. Each component
must be strong enough to withstand and absorb extreme
punishment. Both the steering system and the front and
the rear suspension must function geometrically with
thebody mass.
The steering and the suspension systems require that
the front wheels self-return and that the tire rolling effort
and the road friction be held to a negligible force in order
to allow the customer to direct the vehicle with the least
effort and the most comfort.
A complete wheel alignment check should include
measurements of the rear toe and camber.
Four-wheel alignment assures that all four wheels will
be running in precisely the same direction.
When the vehicle is geometrically aligned, fuel economy
and tire life are at their peak, and steering and
performance are maximized.
TOE
Toe-in is the turning in of the tires, while toe-out is the
turning out of the tires from the geometric centerline or
thrust line. The toe ensures parallel rolling of the wheels.
The toe serves to offset the small deflections of the wheel
support system which occur when the vehicle is rolling
forward. The specified toe angle is the setting which
achieves 0 degrees of toe when the vehicle is moving.
Incorrect toe-in or toe-out will cause tire wear and
reduced fuel economy. As the individual steering and
suspension components wear from vehicle mileage,
additional toe will be needed to compensate for the wear.
Always correct the toe dimension last.
Page 890 of 1463
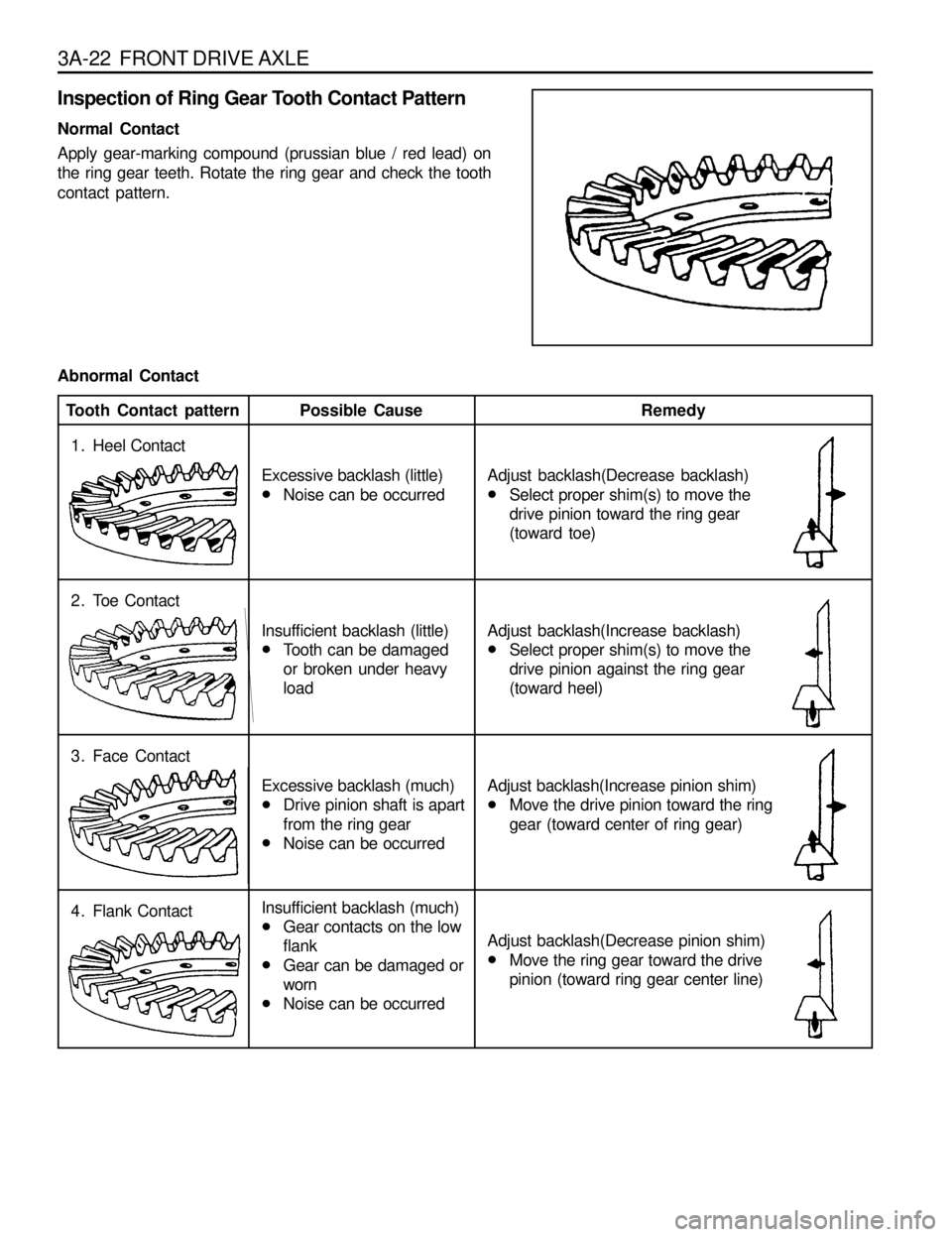
3A-22 FRONT DRIVE AXLE
Inspection of Ring Gear Tooth Contact Pattern
Normal Contact
Apply gear-marking compound (prussian blue / red lead) on
the ring gear teeth. Rotate the ring gear and check the tooth
contact pattern.
Abnormal Contact
Tooth Contact patternPossible CauseRemedy
1. Heel Contact
2. Toe Contact
3. Face Contact
4. Flank ContactInsufficient backlash (little)
lTooth can be damaged
or broken under heavy
load
Excessive backlash (much)
lDrive pinion shaft is apart
from the ring gear
lNoise can be occurred
Insufficient backlash (much)
lGear contacts on the low
flank
lGear can be damaged or
worn
lNoise can be occurredAdjust backlash(Decrease backlash)
lSelect proper shim(s) to move the
drive pinion toward the ring gear
(toward toe)
Adjust backlash(Increase backlash)
lSelect proper shim(s) to move the
drive pinion against the ring gear
(toward heel)
Adjust backlash(Increase pinion shim)
lMove the drive pinion toward the ring
gear (toward center of ring gear)
Adjust backlash(Decrease pinion shim)
lMove the ring gear toward the drive
pinion (toward ring gear center line) Excessive backlash (little)
lNoise can be occurred
Page 913 of 1463
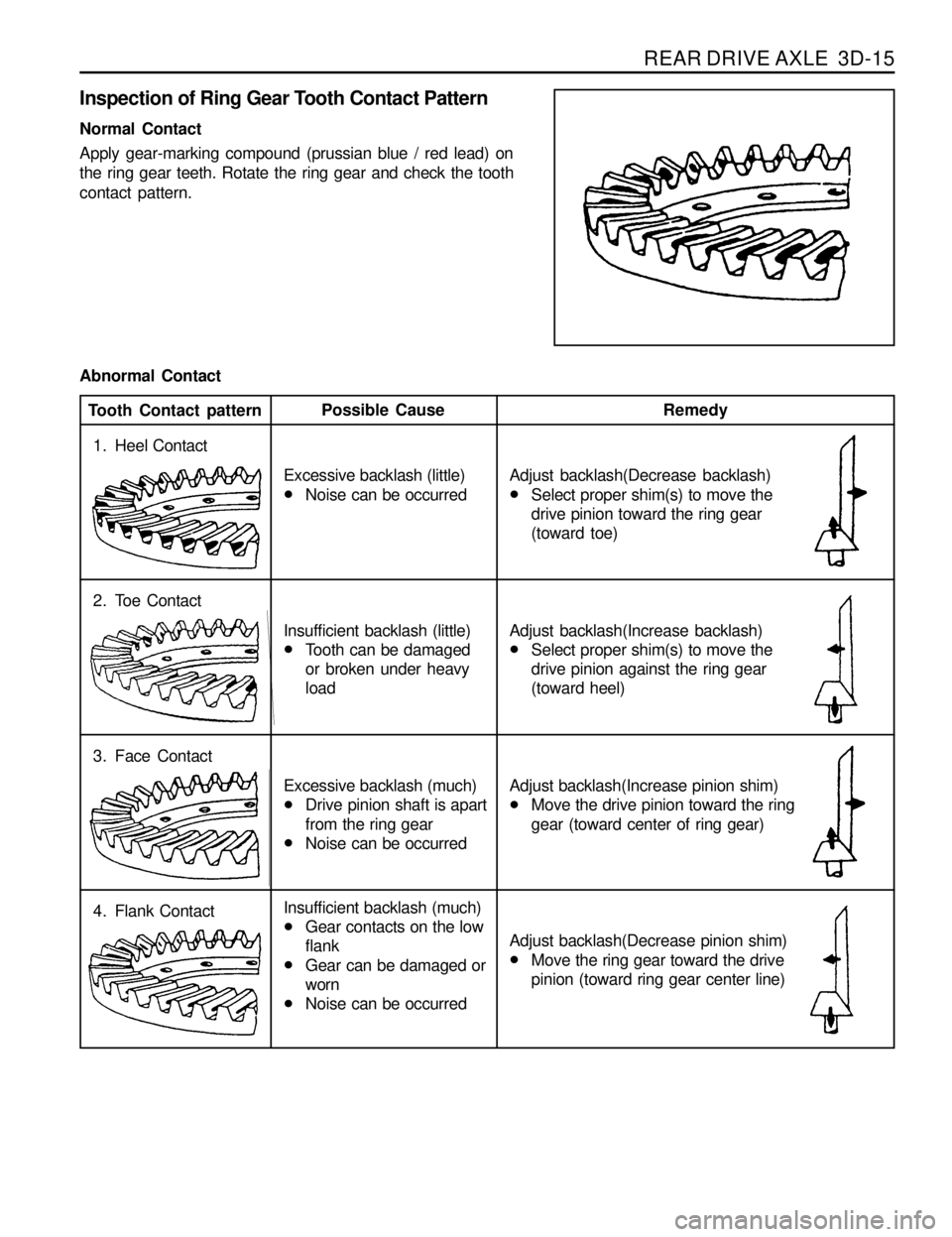
REAR DRIVE AXLE 3D-15
Inspection of Ring Gear Tooth Contact Pattern
Normal Contact
Apply gear-marking compound (prussian blue / red lead) on
the ring gear teeth. Rotate the ring gear and check the tooth
contact pattern.
Abnormal Contact
Tooth Contact patternPossible CauseRemedy
1. Heel Contact
2. Toe Contact
3. Face Contact
4. Flank ContactInsufficient backlash (little)
lTooth can be damaged
or broken under heavy
load
Excessive backlash (much)
lDrive pinion shaft is apart
from the ring gear
lNoise can be occurred
Insufficient backlash (much)
lGear contacts on the low
flank
lGear can be damaged or
worn
lNoise can be occurredAdjust backlash(Decrease backlash)
lSelect proper shim(s) to move the
drive pinion toward the ring gear
(toward toe)
Adjust backlash(Increase backlash)
lSelect proper shim(s) to move the
drive pinion against the ring gear
(toward heel)
Adjust backlash(Increase pinion shim)
lMove the drive pinion toward the ring
gear (toward center of ring gear)
Adjust backlash(Decrease pinion shim)
lMove the ring gear toward the drive
pinion (toward ring gear center line) Excessive backlash (little)
lNoise can be occurred