Page 61 of 396
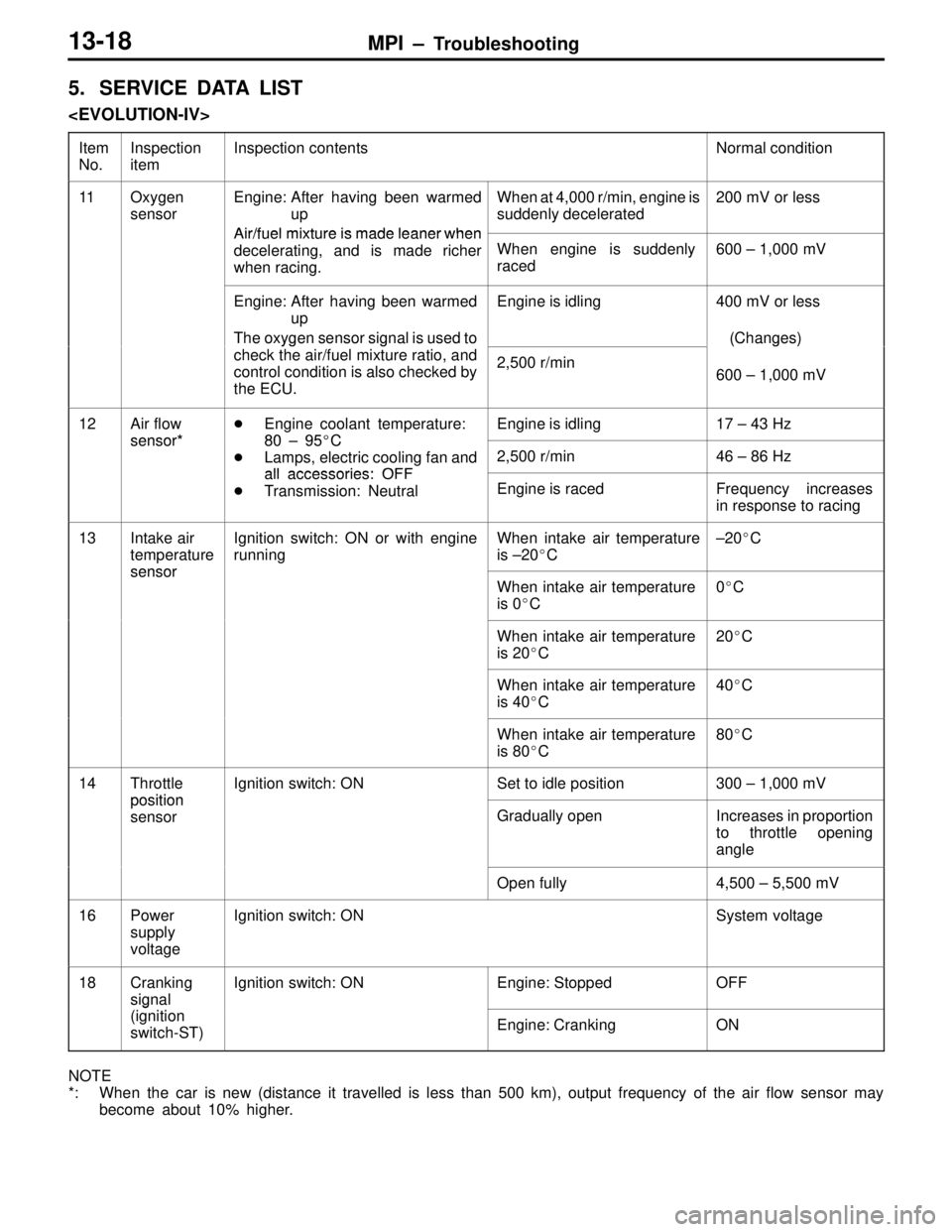
MPI – Troubleshooting13-18
5. SERVICE DATA LIST
Item
No.Inspection
itemInspection contentsNormal condition
11Oxygen
sensorEngine: After having been warmed
up
Air/fuel mixture is made leaner when
When at 4,000 r/min, engine is
suddenly decelerated200 mV or less
Air/fuel mixture is made leaner when
decelerating, and is made richer
when racing.
When engine is suddenly
raced600 – 1,000 mV
Engine: After having been warmed
up
The ox
ygen sensor signal is used to
Engine is idling400 mV or less
(Chan
ges)The oxygen sensor signal is used to
check the air/fuel mixture ratio, and
control condition is also checked by
the ECU.2,500 r/min
(Changes)
600 – 1,000 mV
12Air flow
sensor*
Engine coolant temperature:
8095C
Engine is idling17 – 43 Hz
sensor*80 – 95C
Lamps, electric cooling fan and
all accessories: OFF
2,500 r/min46 – 86 Hz
all accessories: OFF
Transmission: NeutralEngine is racedFrequency increases
in response to racing
13Intake air
temperature
sensor
Ignition switch: ON or with engine
runningWhen intake air temperature
is –20C–20C
sensorWhen intake air temperature
is 0C0C
When intake air temperature
is 20C20C
When intake air temperature
is 40C40C
When intake air temperature
is 80C80C
14Throttle
position
Ignition switch: ONSet to idle position300 – 1,000 mV
position
sensor
Gradually openIncreases in proportion
to throttle opening
angle
Open fully4,500 – 5,500 mV
16Power
supply
voltageIgnition switch: ONSystem voltage
18Cranking
signal Ignition switch: ONEngine: StoppedOFF
g
(ignition
switch-ST)Engine: CrankingON
NOTE
*: When the car is new (distance it travelled is less than 500 km), output frequency of the air flow sensor may
become about 10% higher.
Page 64 of 396
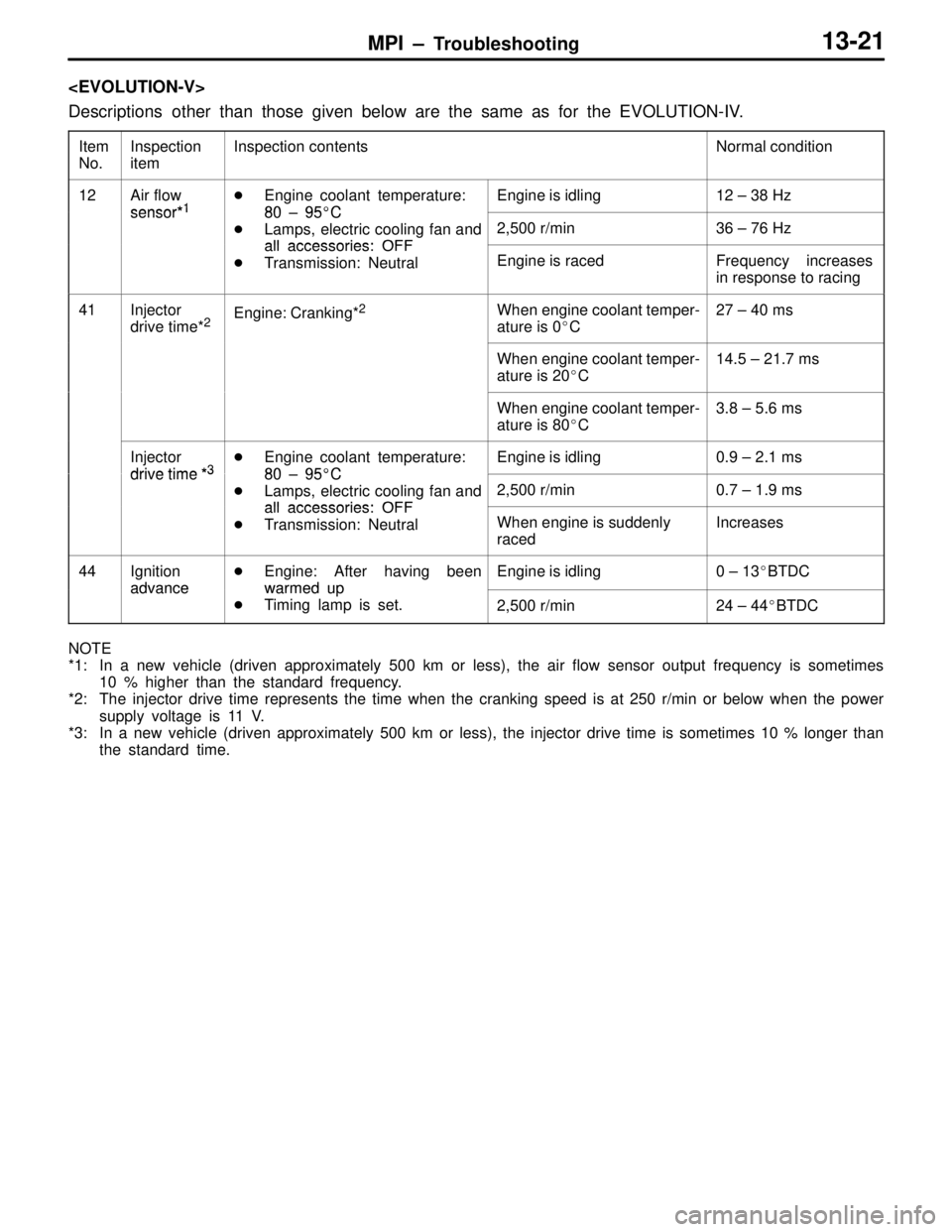
MPI – Troubleshooting13-21
Descriptions other than those given below are the same as for the EVOLUTION-IV.
Item
No.Inspection
itemInspection contentsNormal condition
12Air flow
sensor*1Engine coolant temperature:
80–95C
Engine is idling12 – 38 Hz
sensor*180 – 95C
Lamps, electric cooling fan and
all accessories: OFF
2,500 r/min36 – 76 Hz
all accessories: OFF
Transmission: NeutralEngine is racedFrequency increases
in response to racing
41Injector
drive time*2Engine: Cranking*2When engine coolant temper-
ature is 0C27 – 40 ms
When engine coolant temper-
ature is 20C14.5 – 21.7 ms
When engine coolant temper-
ature is 80C3.8 – 5.6 ms
Injector
drive time*3Engine coolant temperature:
8095C
Engine is idling0.9 – 2.1 ms
drive time *380 – 95C
Lamps, electric cooling fan and
all accessories: OFF
2,500 r/min0.7 – 1.9 ms
all accessories: OFF
Transmission: NeutralWhen engine is suddenly
racedIncreases
44Ignition
advance
Engine: After having been
warmed up
Engine is idling0 – 13BTDC
advancewarmed up
Timing lamp is set.2,500 r/min24 – 44BTDC
NOTE
*1: In a new vehicle (driven approximately 500 km or less), the air flow sensor output frequency is sometimes
10 % higher than the standard frequency.
*2: The injector drive time represents the time when the cranking speed is at 250 r/min or below when the power
supply voltage is 11 V.
*3: In a new vehicle (driven approximately 500 km or less), the injector drive time is sometimes 10 % longer than
the standard time.
Page 70 of 396
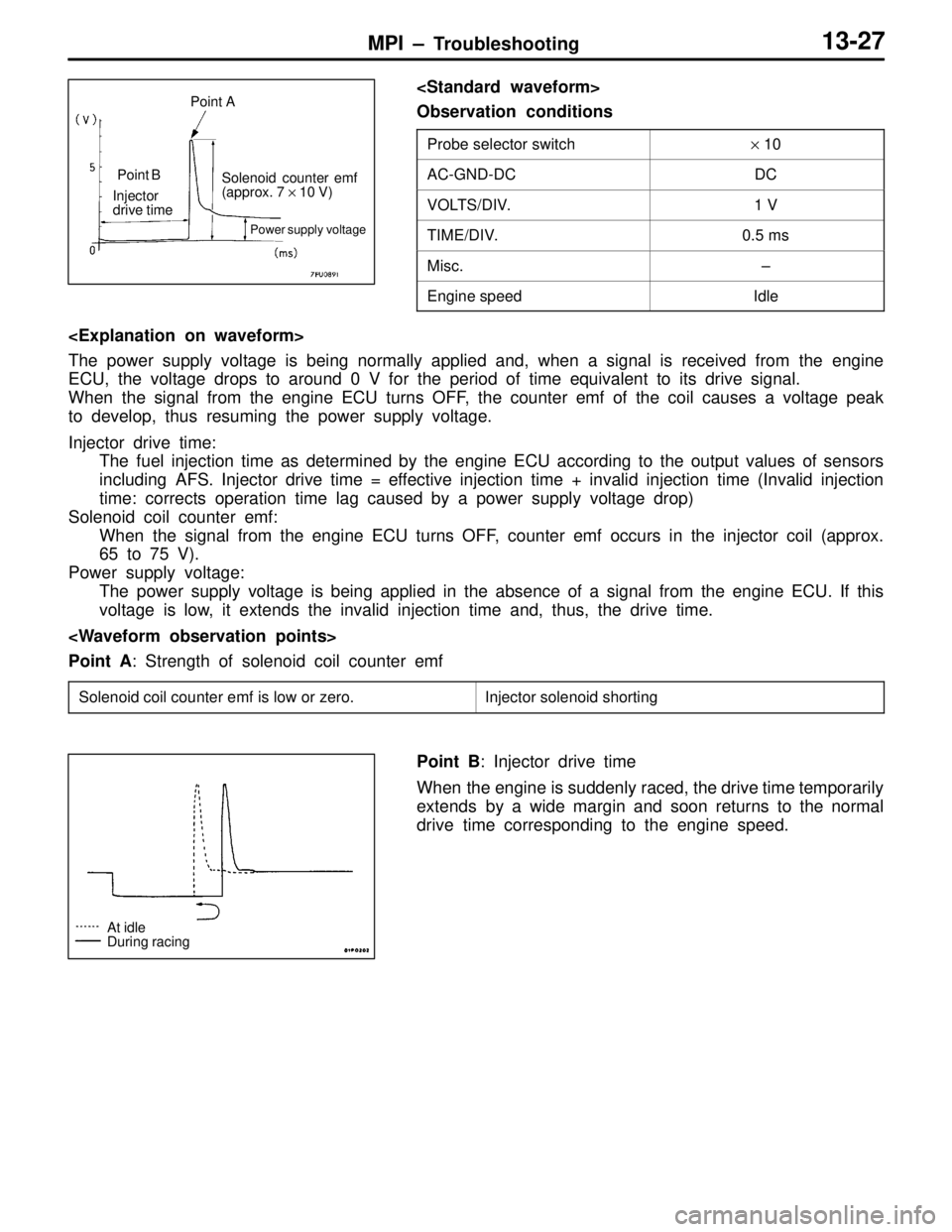
MPI – Troubleshooting13-27
Observation conditions
Probe selector switch× 10
AC-GND-DCDC
VOLTS/DIV.1 V
TIME/DIV.0.5 ms
Misc.–
Engine speedIdle
The power supply voltage is being normally applied and, when a signal is received from the engine
ECU, the voltage drops to around 0 V for the period of time equivalent to its drive signal.
When the signal from the engine ECU turns OFF, the counter emf of the coil causes a voltage peak
to develop, thus resuming the power supply voltage.
Injector drive time:
The fuel injection time as determined by the engine ECU according to the output values of sensors
including AFS. Injector drive time = effective injection time + invalid injection time (Invalid injection
time: corrects operation time lag caused by a power supply voltage drop)
Solenoid coil counter emf:
When the signal from the engine ECU turns OFF, counter emf occurs in the injector coil (approx.
65 to 75 V).
Power supply voltage:
The power supply voltage is being applied in the absence of a signal from the engine ECU. If this
voltage is low, it extends the invalid injection time and, thus, the drive time.
Point A: Strength of solenoid coil counter emf
Solenoid coil counter emf is low or zero.Injector solenoid shorting
Point B: Injector drive time
When the engine is suddenly raced, the drive time temporarily
extends by a wide margin and soon returns to the normal
drive time corresponding to the engine speed.
Point A
Point B
Injector
drive timeSolenoid counter emf
(approx. 7 × 10 V)
Power supply voltage
At idle
During racing
Page 76 of 396
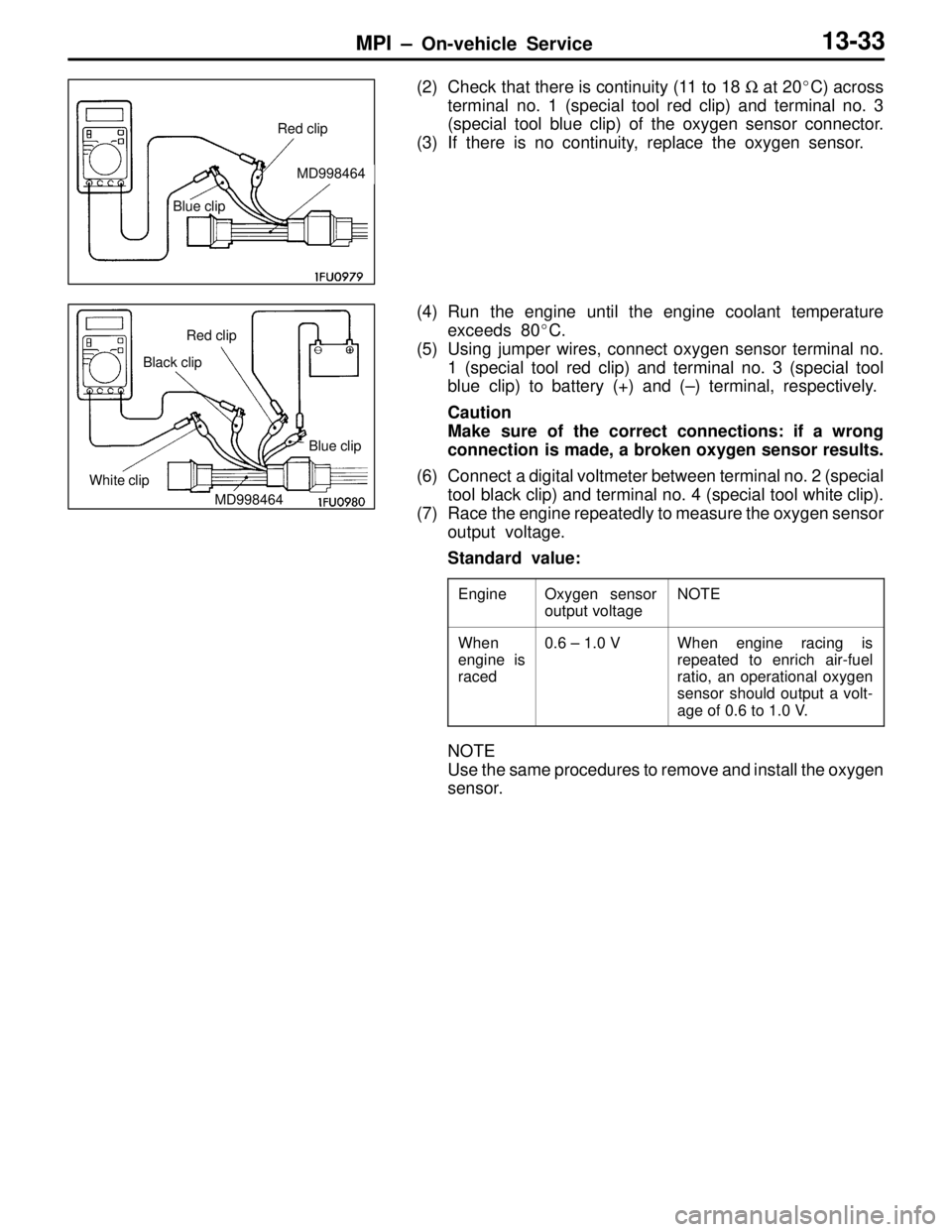
MPI – On-vehicle Service13-33
(2) Check that there is continuity (11 to 18 Ω at 20C) across
terminal no. 1 (special tool red clip) and terminal no. 3
(special tool blue clip) of the oxygen sensor connector.
(3) If there is no continuity, replace the oxygen sensor.
(4) Run the engine until the engine coolant temperature
exceeds 80C.
(5) Using jumper wires, connect oxygen sensor terminal no.
1 (special tool red clip) and terminal no. 3 (special tool
blue clip) to battery (+) and (–) terminal, respectively.
Caution
Make sure of the correct connections: if a wrong
connection is made, a broken oxygen sensor results.
(6) Connect a digital voltmeter between terminal no. 2 (special
tool black clip) and terminal no. 4 (special tool white clip).
(7) Race the engine repeatedly to measure the oxygen sensor
output voltage.
Standard value:
EngineOxygen sensor
output voltageNOTE
When
engine is
raced0.6 – 1.0 VWhen engine racing is
repeated to enrich air-fuel
ratio, an operational oxygen
sensor should output a volt-
age of 0.6 to 1.0 V.
NOTE
Use the same procedures to remove and install the oxygen
sensor.
Red clip
Blue clip
MD998464
Red clip
Blue clip
MD998464 Black clip
White clip
Page 78 of 396
MPI – On-vehicle Service13-35
11. FUEL PUMP RELAY NO.2 CHECK
(1) Remove fuel pump relay No.2.
(2) Using jumper wires, connect fuel pump relay No.2 terminal
(3) to battery (+) terminal, and terminal (1) to battery
(–) terminal, respectively.
(3) Connecting and disconnecting the jumper wire on the
battery (–) terminal end, check for continuity across
terminal (2) and terminal (5), and across terminal (4) and
terminal (5), of fuel pump relay No.2.
Jumper wireContinuity across
terminals (2) and (5)Continuity across
terminals (4) and (5)
ConnectedNoYe s
DisconnectedYe sNo
(4) If the continuity is checked abnormally, replace fuel pump
relay No.2.
12. FUEL PUMP RESISTOR CHECK
(1) Disconnect the fuel pump resistor connector.
(2) Measure resistance across the terminals.
Standard value: 0.6 – 0.9 Ω
(3) If the measurement falls outside the specified range,
replace the fuel pump resistor.
Fuel pump relay No.2
Fuel pump resistor
Page 106 of 396
ENGINE ELECTRICAL – Charging System16-3
REMOVAL SERVICE POINTS
APOWER STEERING, A/C COMPRESSOR, AND
ALTERNATOR DRIVE BELT REMOVAL
(1) Align the hole in the auto tensioner bracket with that
in the arm and insert a screwdriver into the holes.
(2) Remove the drive belt.
BDELIVERY PIPE, INJECTOR, AND PRESSURE
REGULATOR ASSEMBLY REMOVAL
After the mounting points have been loosened, slightly move
the corresponding part to allow for a space for removal of
the alternator.
CALTERNATOR REMOVAL
Push the engine all the way up with a garage jack and remove
the alternator upward the engine compartment.
Phillips
screwdriver
Hole in arm
Auto tensioner
Hole in bracket
Page 121 of 396
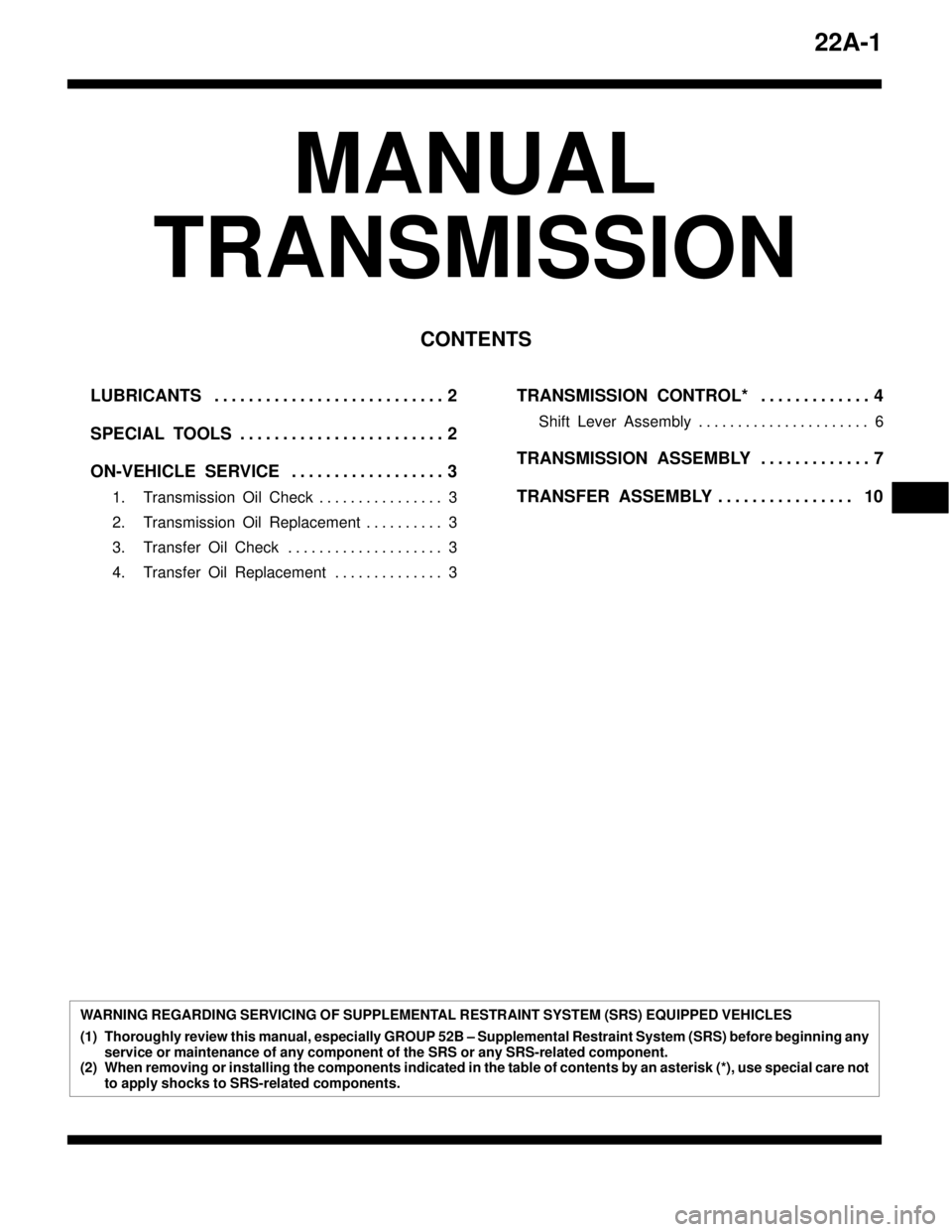
22A-1
MANUAL
TRANSMISSION
CONTENTS
LUBRICANTS 2. . . . . . . . . . . . . . . . . . . . . . . . . . .
SPECIAL TOOLS 2. . . . . . . . . . . . . . . . . . . . . . . .
ON-VEHICLE SERVICE 3. . . . . . . . . . . . . . . . . .
1. Transmission Oil Check 3. . . . . . . . . . . . . . . .
2. Transmission Oil Replacement 3. . . . . . . . . .
3. Transfer Oil Check 3. . . . . . . . . . . . . . . . . . . .
4. Transfer Oil Replacement 3. . . . . . . . . . . . . .
TRANSMISSION CONTROL* 4. . . . . . . . . . . . .
Shift Lever Assembly 6. . . . . . . . . . . . . . . . . . . . . .
TRANSMISSION ASSEMBLY 7. . . . . . . . . . . . .
TRANSFER ASSEMBLY 10. . . . . . . . . . . . . . . .
WARNING REGARDING SERVICING OF SUPPLEMENTAL RESTRAINT SYSTEM (SRS) EQUIPPED VEHICLES
(1) Thoroughly review this manual, especially GROUP 52B – Supplemental Restraint System (SRS) before beginning any
service or maintenance of any component of the SRS or any SRS-related component.
(2) When removing or installing the components indicated in the table of contents by an asterisk (*), use special care not
to apply shocks to SRS-related components.
Page 193 of 396
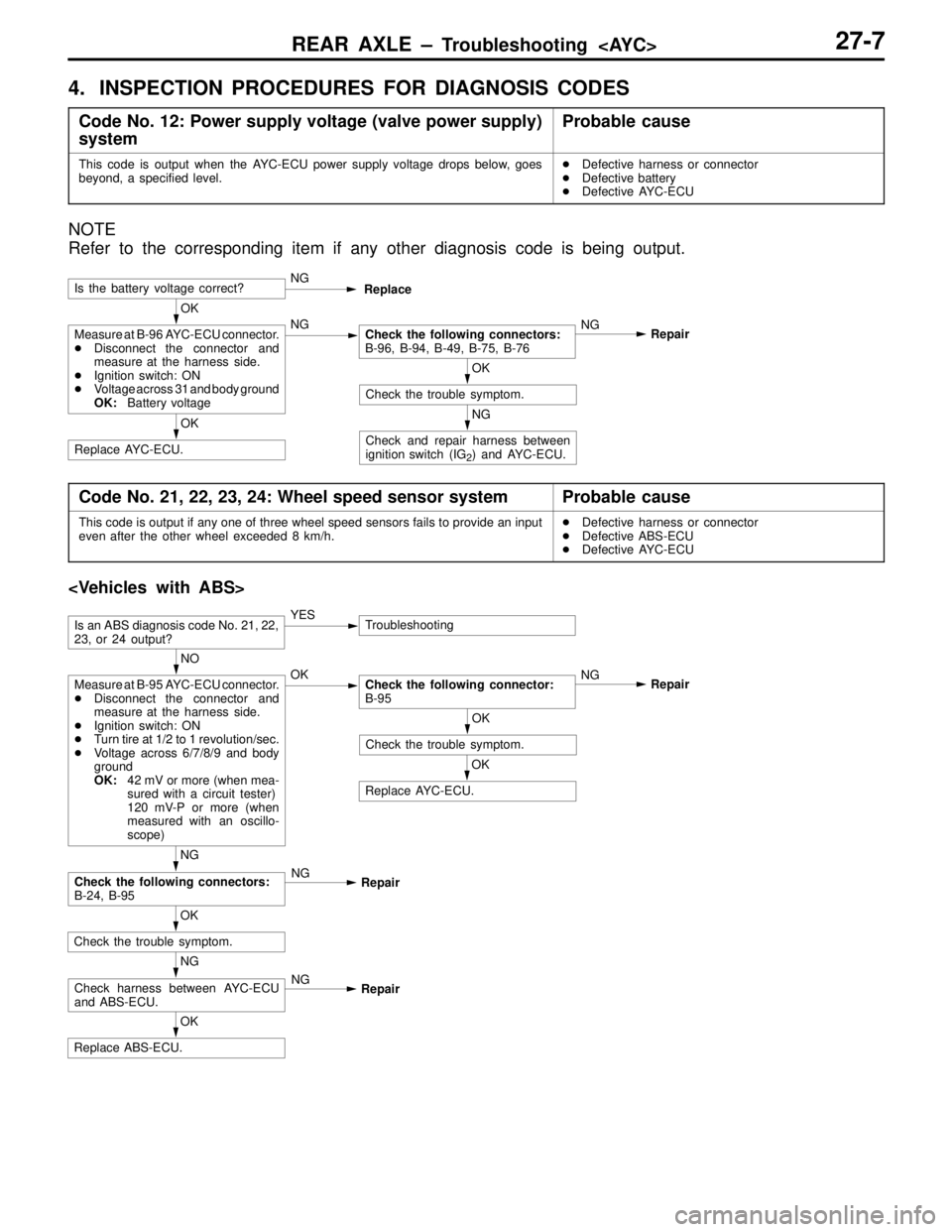
REAR AXLE – Troubleshooting 27-7
4. INSPECTION PROCEDURES FOR DIAGNOSIS CODES
Code No. 12: Power supply voltage (valve power supply)
systemProbable cause
This code is output when the AYC-ECU power supply voltage drops below, goes
beyond, a specified level.Defective harness or connector
Defective battery
Defective AYC-ECU
NOTE
Refer to the corresponding item if any other diagnosis code is being output.
Is the battery voltage correct?NG
Replace
OK
Measure at B-96 AYC-ECU connector.
Disconnect the connector and
measure at the harness side.
Ignition switch: ON
Voltage across 31 and body ground
OK:Battery voltageNGCheck the following connectors:
B-96, B-94, B-49, B-75, B-76
OK
Check the trouble symptom.
NG
Check and repair harness between
ignition switch (IG
2) and AYC-ECU. OKReplace AYC-ECU.NG
Repair
Code No. 21, 22, 23, 24: Wheel speed sensor systemProbable cause
This code is output if any one of three wheel speed sensors fails to provide an input
even after the other wheel exceeded 8 km/h.Defective harness or connector
Defective ABS-ECU
Defective AYC-ECU
OK
Replace AYC-ECU.
OK
Replace ABS-ECU.
NG
Check harness between AYC-ECU
and ABS-ECU.NG
Repair
OK
Check the trouble symptom.
Is an ABS diagnosis code No. 21, 22,
23, or 24 output?YESTroubleshooting
NO
Measure at B-95 AYC-ECU connector.
Disconnect the connector and
measure at the harness side.
Ignition switch: ON
Turn tire at 1/2 to 1 revolution/sec.
Voltage across 6/7/8/9 and body
ground
OK:42 mV or more (when mea-
sured with a circuit tester)
120 mV-P or more (when
measured with an oscillo-
scope)OKCheck the following connector:
B-95
OK
Check the trouble symptom.
NG
Check the following connectors:
B-24, B-95NG
RepairNG
Repair